近海的勘探和生產需要在惡劣的條件下最大限度地保障正常運行時間。載人和無人駕駛設施需要可靠的綜合控制和安全系統(ICSS),並且需要具有先進的遠程監控能力。橫河電機擁有先進技術和豐富經驗,可以執行各種規模及自動化程度複雜的離岸項目。
挑戰
客戶面臨的挑戰
靈活的模組化系統整合
我們的解決方案
橫河的ICSS架構和FLNG解決方案採用了靈活的模組化技術。我們在設計全整合模組化系統時使用分佈式ICSS體系結構,盡量減少設計過程中的風險。直到“firstLNG”,利用專用的網絡段和控制器,以及每個自治系統的分佈式I / O模塊,保證了不同製程模組的自主控制,安全/消防和燃氣系統。
在大型模組中,支援分段的專用操作站安裝在本地機房(LER)中。
在模組化設計中,我們在FLNG設施上實施ICSS解決方案的概念。節省成本和節省時間的執行在多個地點實施,並按計劃交付給每個模組。每個模組都可以在本地進行測試,然後再運到組裝現場進行最終集成。
船體ICSS可以與幹舷工業模組分開實現,並在安裝幹舷設備之前在適當的時間投入運行。這也適用於海下ICSS,橫河能夠以同樣的方式整合海下主控制。
客戶獲得的收益
在設計,安裝和調試過程中盡量減少風險。
技術實現
橫河的ICSS與N-IO(網路I/O),下一代智能可配定I / O,允許靈活的綁定I / O分配。通過與橫河電機的調試工具FieldMate驗證器結合使用,顯著加快了項目完成的速度,並在不影響質量的前提下降低了成本。
Details
浮式生產,儲存和卸載(FPSO)
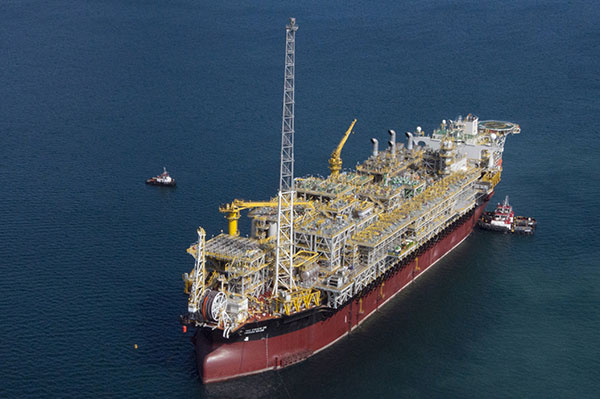
照片由 MODEC公司提供
浮式生產,儲存和卸載(FPSO)裝定是一種浮動的海上生產設施,既儲存加工設備,又儲存生產的烴類。碳氫化合物是由平台或海底模板生產的,然後傳遞到FPSO設施。FPSO設施處理石油並儲存,直到石油可以通過管道或油輪運輸。浮動生產儲油和卸載(FPSO)裝定被石油公司用在偏遠地區和深水石油生產具有經濟可行性。
浮動存儲和再氣化裝定(FSRU)
多年研究表明,大型浮式生產、儲存和卸載(FPSO)船是LNG項目日益可行的解決方案。儘管近海和陸上天然氣液化和再氣化工廠有不同的要求,但兩者都必須依靠已證實的液化和再氣化製程。在LNG運輸船上,壓載和貨物裝卸控制也非常相似。基於豐富的液化天然氣液化、再氣化及載體方面的項目執行經驗,以及實施各種浮式生產系統的專業知識,橫河有信心為浮動LNG(FLNG)和浮動存儲及再氣化裝定(FSRU)項目提供生產管理、資產管理、安全管理、電源管理和壓縮機控制等全方位的解決方案。
浮式液化天然氣(FLNG)
橫河擁有三十多年的LNG項目執行經驗,並通製整個產業鏈獲得了重要的工程知識。橫河結合液化、再氣化和液化天然氣運輸方面的知識,以及海上生產設施的豐富經驗,提供了獨特的知識和能力,可以在設備全生命周期執行全球的FLNG項目。

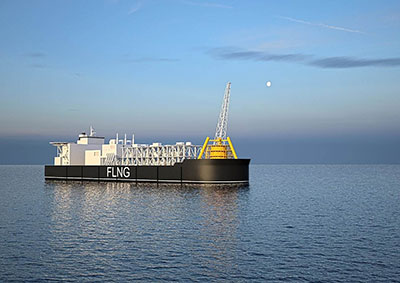
參考
- Yokogawa's integrated solution contributed to reliable and efficient operation.
- All the instrument information is fully integrated with the instrument management system.
STARDOM field control node (FCN) autonomous controllers allow both Modbus master and slave functions to run simultaneously.
Operators must receive diagnostic information before a line block leads to a malfunction. Yokogawa provides predictive diagnostics based on trend analysis of the blocking factor, which improves maintenance efficiency and reduces maintenance costs.
One of the most common applications for differential pressure transmitters is flow measurement. DPharp differential pressure transmitters have some unique signal conditioning features to eliminate instability at low flow rates.
The major methods of improved oil recovery are water flooding and steam injection. "These technologies make a tremendous contribution to recovering additional oil from old wells as well as improve primary recovery of operating oil fields."
The paperless recorder DX series instruments allow you to determine temperature and humidity, and manage the results as manufacturing and quality data at a reasonable cost with a simple configuration.
Yokogawa provides controller embedded flow calculation library based on AGA (American Gas Association) reports.
Reverse osmosis (RO) is a separation process that uses pressure to force a solution through a membrane that retains the solute on one side and allows the pure solvent to pass to the other side. More formally, it is the process of forcing a solvent from a region of high solute concentration through a membrane to a region of low solute concentration by applying a pressure in excess of the osmotic pressure.
Floating-point format calculations have enabled physical quantities (in engineering units) to be used in calculations.
- Effeciently controls the inlet valve and blow-off valve when the compressor starts and stops.
- During steady operation, controls the inlet valve so that the amount of discharged compressed air becomes constant (flow control)
- Surging: Load decreases, the amount of discharge flow and pressure drop, and a limit is exceeded, possibly destroying the compressor.
Industrial Combustion sources such as thermal cracking furnaces and, process heaters play a critical role in the process industry.
Recently, several ARC Advisory Group analysts and management team members had a chance to sit down with the new Yokogawa President and COO, Mr. Takashi Nishijima, and several other top Yokogawa executives to discuss the company's burgeoning presence in the worldwide upstream and midstream oil & gas industry.
Alarm management is not just a project that has a start and end date; it's a continuous cycle. Once the alarm system has been reviewed and improvements have been identified, we must check that controls are in place to ensure the alarm system remains functional. The key is to ensure that the system is continuously monitored and any changes are fully documented. There are seven key steps for alarm management. Rationalization is one of those critical steps.
Tuning PID controllers can seem a mystery. Parameters that provide effective control over a process one day fail to do so the next. The stability and responsiveness of a process seem to be at complete odds with each other. And controller equations include subtle differences that can baffle even the most experienced practitioners.
The worlds of process automation and production management have been converging for some time. What once used to be islands of automation and production management functionality connected through highly proprietary integration schemes that were costly to maintain have developed into integrated platforms that provide seamless data exchange between the world of automation and the plant floor, the functions of production and operations management, and integration with business level systems.
The world of process automation is governed by procedures. While we like to refer to the process industries as being largely "continuous", this could not be further from the truth. Process manufacturing is constantly in flux.
The automation suppliers that will be successful in the long term will be those that effectively address application or industry specific problems for end users with a value proposition that cannot be ignored. These problems exist throughout the process industries today, and they won't be solved by simply offering a product, but through a combination of hardware, software, services, application expertise, and knowledge.
In ARC's view, customers need a compelling business value proposition to justify investment in any kind of automation. Vigilance and VigilantPlant were created with this in mind. Yokogawa's vision with VigilantPlant is to create an environment where plant personnel and operators are well informed, alert, and ready to take action.
Yokogawa has come a long way in making its message clear to the world of process automation. Last year, the company embarked on a full-scale global marketing campaign to make customers aware of the company's focus on system reliability, security, dependability, and robustness. Dubbed "Vigilance", the campaign created a unified message for the company and greatly helped expand awareness of the Yokogawa brand and corporate philosophy.
Process automation end users are under more pressure than ever to do more with less. The current economic climate means that many automation capital projects are on hold. With capital budgets tighter than ever, users instead focus on operational budgets (where cost cutting is also a key concern), or on automation investments with a very rapid return on investment.
In today's dynamic industrial marketplace, the only constant is change. Raw material costs, energy costs, market demands, environmental and safety regulations, technology, and even the nature of the labor force itself are constantly changing, and not always in predictable directions.
Migration of a refinery's DCS provided an opportunity to reconfigure and consolidate the control rooms and operational management system.
July 2011
Process plants are run according to operational procedures. These procedures consist of a set of tasks that are executed in a consistent manner to achieve a specific objective, such as starting up, shutting down or transitioning a unit as part of making a product.
July 2010
Martin te Lintelo, Yokogawa Europe B.V., The Netherlands, discusses high level control system design for LNG receiving terminals. As demand for LNG increases worldwide, players face seemingly conflicting challenges. On one hand, they must expand capacity in different regions, make the business and production as agile and adaptive as possible, and improve operational efficiency.
The LNG sector presents challenges for the automation supplier, particularly in the implementation of automation systems for regasification terminals. Yokogawa Europe's business development manager, upstream oil and gas Martin te Lintelo looks at the handling of the potential automation-related problem areas and opportunities.
August 2006
Many published papers discuss the benefits of subsea HIPPS and many studies show the potential cost-benefit analysis of this technology in deepwater applications. An internet search for subsea HIPPS is informative; however, little appears that discusses the systems already delivered and operating successfully.
Chevron turns to deeper relationships with fewer suppliers to increase project execution consistency
Offshore, February 2013
Offshore and deep-water production has been a significant factor in the sustained growth of the oil and gas industries over the past decade and this trend is expected to continue beyond 2013.
Pipeline & Gas Journal, February 2014
The line of functionality between supervisory control and data acquisition and distributed control system is blurring. These two traditionally disparate technologies are now seen as competitors in similar application environments.
下載
產品型錄
- Subsea Master Control Station (831 KB)
影片
Chet Mroz, President & CEO Yokogawa North America, discusses the benefits of IoT at the 2015 ARC Industry Forum in Orlando.
想了解更多技術&解決方案嗎?
聯絡我們