ProSafe-RS Lite conforms to the international safety standard for up to SIL2(*1) application. You can select the ProSafe series from SIL2 (ProSafe-RS Lite), SIL3 (ProSafe-RS) and SIL4 (ProSafe-SLS). Continued functional enhancements to ProSafe series help you run your plants safely.
*1 Established by the International Electrotechnical Commission (IEC), a safety integrity level (SIL) indicates the relative level of risk provided by a safety function. SILs 1 through 4 are defined by IEC 61508. Compared to a plant where safety measures are not in place, at SIL2 the risk factor is reduced to between 1/100 and 1/1,000. At SIL3, the risk factor is in a range between 1/1,000 and 1/10,000. At SIL4, the risk factor is in a range between 1/10,000 and 1/100,000.
Latest release information of R4.11 (March 2025)
Enhancement of the Bypass Monitoring Package
- Display Override information
The list of override information (*1) is displayed on Bypass Monitor in addition to forced I/O information (*2). It makes it easier for user to understand the overall bypass operation. - Export Bypass information as a csv file
A command is provided to export the information displayed on Bypass Monitor as a csv file. The collected information can be used for user applications, such as creating operational reports on bypass operations automatically in customer’s format.
*1: Information such as variables temporarily overwritten on operation monitoring screens to suppress alarms, etc.
*2: Information such as variables locked on the engineering function for verification or maintenance/p>
ProSafe-RS Lite Safety Instrumented System
ProSafe-RS Lite inherits the highly reliable technology of ProSafe-RS, and by combining with CENTUM VP/ProSafe-RS, enables integrated operation that includes process and safety control. It greatly contributes to your plant’s safety and reliability. As comprehensive SIS vendor, Yokogawa will support your functional safety management entirely throughout the plant lifecycle.
Single-module architecture achieves SIL2
The many SIL2 compliant safety instrumented systems available in the market achieve SIL2 by redundant modules, on the other hand, ProSafe-RS Lite achieves SIL2 with a single module configuration. Building a simpler system means keeping down installation, maintenance, and other running costs. Redundant module configuration of ProSafe-RS Lite enables to maintain SIL2 compliance even if one module fails that achieves high availability.
Integration with control systems
ProSafe-RS Lite can be fully integrated with CENTUM VP Control System and ProSafe-RS. The familiar CENTUM VP monitoring and operation terminal (HMI) allows operators to monitor and control processes, as well as centrally monitor safety instrumented systems installed for emergency shut down, fire and gas, burner management purpose. During plant abnormal condition, you can quickly ascertain the situation by alarms from the safety instrumented systems and take appropriate action.
Easily add SIL2 to existing systems
ProSafe-RS Lite supports the same control bus Vnet/IP(*2) as CENTUM VP and ProSafe-RS. You can easily add ProSafe-RS Lite to existing systems built on the Vnet/IP. The engineering tool for ProSafe-RS also can be commonly used so there is no need to install or learn any new tools.
*2 Vnet/IP is a control network developed by Yokogawa that delivers high reliability and responsiveness, and conforms to the IEC61784-2 international communication standard for the process industry.
About OpreX
OpreX is the comprehensive brand for Yokogawa’s industrial automation (IA) and control business and stands for excellence in the related technology and solutions. It consists of categories and families under each category. This product belongs to the OpreX Control and Safety System family that is aligned under the OpreX Control category.
Details
Engineering
ProSafe-RS Lite is composed of the Safety Engineering PC (SENG) equipped with engineering and maintenance functions, the Safety Control Station (SCS) for safety control and Vnet/IP for control network to communicate with each of those equipment.
ProSafe-RS Lite can be integrated with the CENTUM VP. The SCS can be operated and monitored by the HIS (Human Interface Station) of the CENTUM VP. It is also possible to connect to other DCSs and PLCs via subsystem communication (Modbus communication).
HART communication on ProSafe-RS Lite allows Plant Resource Manager (PRM) to manage the HART communication devices connected to I/O modules on SCS. Also, the AO signal allows PRM client to conduct Partial Stroke Test (PST) on HART-supported valve positioner equipped with the PST function.
One architecture
Seamless architecture achieves true integration of DCS and SIS, contributing to plant optimization.
Expected operational benefits:
- faster project implementation at a lower cost - using just one process network saves engineering design time
- greater operational efficiency - integrated information displays are clearer and more usable
- lower cost of ownership - common control and network architecture standards cut maintenance overhead
Eliminating SIS selection complexities
ProSafe-RS Lite is SIL2 certified in a single module configuration. Redundancy is already built-in to each ultra-compact input, output, and processor card. This intrinsically simple modularity makes it possible to design systems with ease. If additional system availability is required, users can add redundancy on a function by function basis by simply plugging in the appropriate module.
Automation Design Suite (AD Suite)
ProSafe-RS Lite features AD Suite, the same engineering environment used with the CENTUM VP integrated control system, allowing the integrated management of CENTUM VP and ProSafe-RS Lite data.
With this feature, ProSafe-RS Lite engineers can use AD Suite to design the I/O.
AD Suite also has functions for managing the change history and recording changes that save time when renovating systems.
Better Operations, easier Engineering and Hardware Reduction
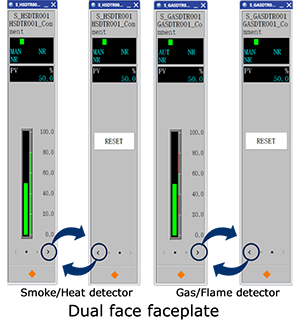
FGS (Fire & Gas System)
- Standard FGS HMI parts for gas, flame, smoke and heat detectors are added for better operations.
- Standard function blocks for FGS detectors are added for easier engineering.
- ProSafe-RS Lite analog module can reset smoke and heat detectors alarms without additional hardware such as relays and DO modules.
The logical solution for perfect control
One network
ProSafe-RS Lite plugs directly onto the same network used by Yokogawa's field-proven CENTUM VP. No gateway or interface hardware is required for data exchange between SIS and DCS functions. Safety communication between SIS controllers is realized and certified in a mixed DCS - SIS configuration.
Expected benefits:
- simple and quick route to system realization
- reduced engineering complexity and cost for connecting SIS and DCS
- lower maintenance costs for large process plants
Safe, reliable and available control without compromise
One architecture
Seamless architecture achieves true integration of DCS and SIS, contributing to plant optimization.
Expected operational benefits:
- faster project implementation at a lower cost - using just one process network saves engineering design time
- greater operational efficiency - integrated information displays are clearer and more usable
- lower cost of ownership - common control and network architecture standards cut maintenance overhead
Eliminating SIS selection complexities
ProSafe-RS Lite is SIL2 certified in a single module configuration. Redundancy is already built-in to each ultra-compact input, output, and processor card. This intrinsically sim Liteple modularity makes it possible to design systems with ease. If additional system availability is required, users can add redundancy on a function by function basis by simply plugging in the appropriate module.
Significant gains in the capabilities of plant displays
- Common human-machine interface (HMI)
No more separate monitoring of SIS and DCS. While continuing to use the interface that they are most familiar with, operators can more rapidly predict which process conditions are likely to reach emergency levels. - Unified event data
Sample screens such as "faceplate" style instrument and alarm displays are provided that enable easy data comparison and decision making. - Back-tracking analysis
A further benefit of data integration is the ability to analyze events preceding an alarm - a powerful tool for effective process safety management.
It's now easy to create displays that integrate DCS and SIS data.
Virtualization Platform
Yokogawa's virtualization separates system software operations from physical hardware dependencies, allows software reusability to optimally commission system hardware.
Virtualization platform enables a single server to perform the work of multiple virtual computers, thus reducing the number of computers required to configure a control system. With this platform, both the hardware and software required to build a virtual environment are provided.
By means of this virtualized server environment, it is possible to separately update and make modifications to hardware and software as required.
This translates to customer's business centric benefits like smooth migration to new physical hardware with reduced downtime, shorter migration process and system tests time.
From maintenance point of view, segregation of hardware and software maintainability are also the significant advantages.
FIO (Field network I/O)
Features
- A variety of I/O modules (AI/AO/DI/DO/Communication function) are available.
- Modbus TCP/RTU communication (Master/Slave) is available by using communication modules.
- Remote installation up to 50 km is available by using optical cables.
- SIL2 can be achieved with single configuration. Redundant configuration is also selectable.
- Dedicated terminal boards, terminal blocks, and cables for FIO are supported.
A single, simple, SIL2 solution
Yokogawa designers have employed state-of-the-art electronic design techniques and component packaging to miniaturize the safety controller circuitry. Every ProSafe-RS Lite processor, input module, and output module features a dual architecture, providing users with SIL2-level protection on a single card. This architecture is simplicity itself to understand, design, install and maintain. Complete safeguarding now comes in one box.
Plug-in availability
If even higher system availability and fault tolerance is required, ProSafe-RS Lite can be configured for dual redundancy while maintaining SIL2 by simply plugging in the appropriate additional card. Because the I/O or processing functions of ProSafe-RS Lite have a modularity that extends down to the function level, redundancy can be applied exactly where it is needed - to input, output, or processor modules - providing a combination of safety and economy that is unprecedented in the SIS market. This flexibility allows any mix of dual redundancy to be configured such as a single input and redundant output or a redundant input and single output.
Versatile Modular Redundancy (VMR)
With its flexible selection of redundant CPU and I/O modules, ProSafe-RS Lite delivers the high availability required by even SIL2 applications. Rather than making selections at the system or rack level, you can apply redundancy exactly where it is needed - in specific input, output or processor modules - depending on such factors as the required SIL for a loop or the reliability of field devices. This is possible because the I/O and processing functions of ProSafe-RS Lite have a modularity that extends down to the function level.
Even when an internal failure occurs, safety functionality is maintained, reducing the likelihood of a false trip in a process.
We call this flexible plug-in availability “VMR / Versatile Modular Redundancy™".
Partial Stroke Test (PST)
Under normal conditions, valves that are integrated with a safety instrumented system (SIS) are not activated. (They are only actuated when the SIS initiates a process shutdown after an abnormality is detected in a process.) It is therefore necessary to periodically test valves to ensure that they are in good working order and will respond properly when needed.
This periodic check is called a “proof test,” and generally it involves a full stroke test (completely closing the valves). When a plant is up and running, the costly installation of a bypass is necessary to conduct a proof test. If this is not possible, the only other option for conducting this test is to shut down the plant. As a consequence, proof tests of the valves are usually conducted only once every several years.
An alternative to the full stroke test is the partial stroke test (PST), which involves slightly closing a valve to diagnose problems. A PST can be conducted without stopping a process, and it can be performed remotely from locations such as a control room.
By conducting a PST, plant owners can significantly reduce their maintenance costs. And by checking the valves more frequently than is possible with the full stroke test, they can anticipate great benefits such as increased reliability .
Note: although the PST does not eliminate the need for a full stroke test, it makes it possible to extend the proof test interval without sacrificing the required safety level.
Complied Certificate
- TÜV SIL2
- ISASecure CSA 1.0.0 Level 1 *1
*1: It complies with IEC 62443-4-2 and IEC 62443-4-1 international standards for security in control devices.
Click here for ISASecure Certification details
Complied Standards
ProSafe-RS system hardware conforms to the standards listed below. Please use the ProSafe-RS system in the industrial environment only.
PLC (Programmable Logic Controller)
- IEC 61131-2
Functional safety
- IEC 61508, IEC 61511-1, IEC 62061
Application
- EN 54-2, EN 298, EN 50156-1, NFPA85, NFPA86, NFPA72
Safety
- CSA
- CE Marking
- EAC Marking
- Morocco Compliance Marking
- UKCA Marking
EMC Standards
- CE Marking EMC Directive
- RCM
- KC Marking
- EAC Marking
- Functional Safety
- Morocco Compliance Marking
- UKCA Marking
Hazardous location equipment
- FM Non-Incendive
- ATEX Ex “ec”
- IECEx Ex “ec”
- ECAS-Ex “ec”
- UKEX-Ex “ec”
Marine Standards
- American Bureau of Shipping (ABS)
- Bureau Veritas (BV)
- Lloyd’s Register
- DNV
Resources
- Reinstrumentation project at HDPE plant replaced legacy pneumatic instruments and PLCs with integrated CENTUM CS 3000 PCS and ProSafe-RS SIS.
- HART field devices can be monitored from the central control room with the plant resource manager (PRM) package, enabling a more predictive and proactive maintenance approach that reduces total cost of ownership.
Downloads
Looking for more information on our people, technology and solutions?
Contact Us