PRM contributes to improving the quality of maintenance plans and optimizing maintenance costs throughout the plant life cycle.
The PRM plant manager software centrally manages large amounts of status and maintenance information from automation and production assets. PRM has various maintenance support functions, including online functions for monitoring and diagnosing devices and equipment.
Introductory Video
In this video we show you how PRM plant manager software can be useful in preventing sudden equipment failures that can affect production at a plant.
PRM Overview
Why it is important to have a proper asset management regime in place for reliable, efficient, and profitable plant operations
Damage to or failure of plant equipment can have a significant impact on operation of the plant as a whole. Yokogawa’s Plant Resource Manager (PRM) helps improve your equipment maintenance plans and optimize equipment maintenance costs.
Plant equipment maintenance challenges
- Complexity of a vast fleet of equipment
- Lack of maintenance resources
- Depletion of institutional knowledge
Yokogawa’s approach to efficient facility maintenance
- Centrally manage and visualize plant equipment data
- Achieve cost savings through improved maintenance efficiency
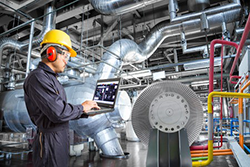
Yokogawa offers equipment maintenance solutions that provide both reliability and efficiency
Yokogawa is a trusted provider of systems that keep the plant online, as well as maintenance solutions that allow operations to stay online while achieving reliability and efficiency gains.
Yokogawa streamlines plant management across three levels!
Select which tier to start with based on plant needs
Plant equipment and device malfunctions cause abnormalities and instability to manufacturing workflows, which in turn add to the time it takes to identify the cause of the malfunctions and restore the system. As a result, overall production efficiency goes down. Anticipating equipment malfunctions before they occur and monitoring plant processes for prevention of failures lets you hot-swap equipment with limited impact to operations.
Yokogawa provides solutions across three tiers:
- Visualize and remotely configure equipment status
- Device templating allows for efficiently propagating shared parameters across multiple devices
- Device Type Manager (DTM) and other specialized calibrating tools enable equipment to be brought online quickly
- More efficient equipment replacement by tracking and comparing parameter logs
- Reduce man-hours by checking and configuring device parameters remotely
- Monitor equipment and device performance
- Device patrolling ensures periodic polling of status data for efficient assessment of equipment conditions
- Versatile diagnostic algorithms allow for measuring valves from multiple vendors
- Periodic and automatic equipment status reports (field asset KPI reports) visualize conditions and comprehensively assess the health of the plant
- Provide data to enhance maintenance and operations
- Critical equipment information can be checked immediately not only through DCS but also through comprehensive ICSS (*1) integration for rapid response to problems
- Loop diagnostics allow for improving control valve performance and maintaining high productivity
- Work order efficiency is achieved by integrating with higher level systems (ERP/CMMS (*2), etc.)
*1) ICSS : Integrated Control and Safety System (incl. DCS, SIS, and other subsystems)
*2) ERP : Enterprise Resource Planning, CMMS: Computerized Maintenance Management System
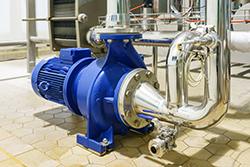
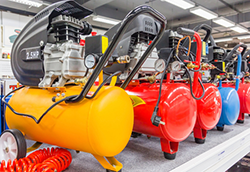

PRM system configuration
Details
Asset diagnostics
- Diagnosis functions
- Predictive Maintenance of pump cavitation (Cavitation detection system)
- PST scheduler
- Fieldbus diagnosis
1. Diagnosis functions
Prevent trouble through control valve diagnosis
The control valve is one of the most important devices in a plant. Sudden trouble may lead to a drop in production quality or a plant shutdown. The plant has an enormous number of field devices, and many customers struggle with planning and implementing inspection and maintenance plans to maintain the normal functioning of valves.. Control valve diagnostics are useful to help solve this problem. Five diagnosis logic expressions based on field digital technology are included to help detect deterioration of the valve. The diagnosis supports multiple vendors, and can diagnose all valves in the entire plant using in the same diagnosis logic. Inspection and maintenance plans can be drawn up and prioritized according to the diagnosis results.
- Easily make inspection and maintenance plans according to deterioration state and importance
- Multi-vendor support enables evaluation of the entire plant
- Simple engineering: Just choose a file to enter settings
Monitoring parameters to leverage device information
The spread of field devices with digital communication functions such as HART, PROFIBUS, FOUNDATION™ Fieldbus and wireless advances. These functions enable remote setup of the field devices and detailed monitoring, and contributed to work efficiency. Furthermore, the field devices’ self-diagnosis functions allowed abnormal detection in real time. However, field devices have parameter information that is not being well utilized. Monitoring this information is an effective way to grasp device abnormality trends and respond with preventive maintenance.
- Easily make inspection and maintenance plans according to deterioration state and importance
- Prevent sudden equipment failure and reliable operation
- Simple engineering: Just choose a file to enter settings
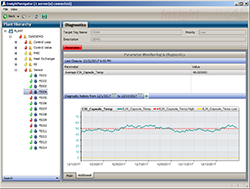
2. Predictive Maintenance of Pump Cavitation (Cavitation Detection System)
Providing data that will optimize maintenance and operations
Early detection of equipment abnormalities allows for efficient plant maintenance
Yokogawa’s cavitation detection system does not rely on detection by vibration or pings, which is the traditional technique used to detect cavitation after it has already progressed. Instead, our solution detects fluid pressure differentials caused by early cavitation, allowing for quantitatively determining the extent of possible cavitation. Early detection of cavitation provides plant operators time to take proper countermeasures to prevent damage to pipes.

3. PST Scheduler
PRM and PST Scheduler
It is known that partial stroke tests (PST) extend the interval between full stroke tests (FST) for emergency shutdown valves and help to reduce maintenance costs. PST Scheduler brings precision, efficiency, and integration to the PST process. PST Scheduler can schedule an automatic, semi-automatic, or manual PST and automatically record test results for safety valves connected either to a Yokogawa ProSafe-RS or another safety instrumented system. PST Scheduler works with safety valves from the four leading vendors.
Perform automatic and semi-automatic PST’s of multiple valves per preconfigured settings and log the results. A PST allows larger lengths of time between each FST, which normally requires taking a plant offline.
Operating under PRM, PST Scheduler remotely executes the PST provided by the safety valve vendor, and records the results. Testing is efficient and well-planned, and results are shown on a single screen without any additional hardware or software. Only Yokogawa's PRM and PST Scheduler support safety valves from multiple vendors.
Features of PST Scheduler
- Schedule: Week, Month, Year, On demand
- Mode: Manual, Semi-automatic, Automatic
- Execution: Serial, Parallel
- Operation: Execute, Pause, Resume, Skip
- Recording: PST Results
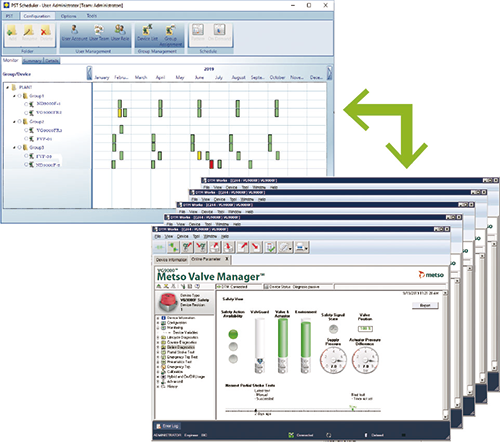
Maximize safety system performance
Yokogawa's ProSafe-RS safety instrumented system is SIL3 certified even in a single modular configuration. Execution of PSTs on a fixed schedule is key to ensuring that a safety system will function correctly in an emergency. The combination of ProSafe-RS and PRM with PST Scheduler not only simplifies the management of safety devices, it maximizes safety system performance. In addition, no additional wiring or hardware such as a multiplexer is needed to manage safety devices.
Optimal flexibility in valve selection
The Vigilant Integration Partners (VIP) program is an open, non-exclusive, standard-based, and interoperability-driven initiative that enables users of Yokogawa's ProSafe-RS safety instrumented system (SIS) and PRM asset management system to use best-in-class field devices from Dresser Masoneilan, Flowserve Corporation, Metso, and SAMSON AG.
What is a partial stroke test (PST)?
A partial stroke test (PST) partially opens and closes emergency shutdown (ESD) valves while the plant is running. Safety standards, such as IEC61508, IEC61511, or ANSI/ISA-84.00.01, require full stroke tests (FST) for those ESD valves to be conducted at certain intervals depending on the safety integrity levels (SIL) to make certain that they are functional in case of emergency. FST requires those shutdown valves to fully open and close, and it can only be done while the plant is shut down for maintenance. However, by conducting PSTs, it is possible to extend the intervals of the FSTs, thus maximizing the plant operation time and reducing the OPEX and TCO.
4. Fieldbus diagnosis
FieldConnex® Advanced Diagnostic Module (ADM)
In addition to supporting the use of powerful tools such as oscilloscopes and data historians, ADM has a unique commissioning wizard that can reduce the amount of time required for the critical plant start-up phase by up to 80%.
ADM's online monitoring capabilities provide actionable information through PRM's user interface, indicating changes in the fieldbus physical layer before they become critical.
The integration of the FieldConnex ADM interface widens the scope of PRM's asset management capabilities to include the communication status of FOUNDATION™ Fieldbus segments.
Benefits
End Users and Plant Operators:
- Minimizes installation time
- Speeds up commissioning
- Increases plant uptime
- Simplifies verification of explosion protection
Engineering Companies:
- Simplifies planning
- Eliminates unnecessary engineering
- Documents the complete segment for plant handover
Maintenance Teams:
- Enables a proactive maintenance approach
- Reduces frequency of outages
- Increases plant uptime
CMMS* Interface
PRM has a CMMS interface for Maximo, an enterprise asset management (EAM) system from IBM Software, Inc. Through this interface, Maximo can provide better maintenance operation by acquiring real-time device information from PRM when both systems are connected.
*CMMS: computerized maintenance management system
Online monitoring
- Navigation functions
- Remote adjustment
- Efficient setting of device parameters
- Asset information management
- Maintenance alarm
- Best-in-class collaboration
1. Navigation functions
A single window for managing plant-wide assets
The device navigator displays the status of plant-wide assets with a Windows Explorer–like interface. Flexible navigation mechanisms enable maintenance personnel to quickly identify areas of the plant that require online diagnosis. Intuitive status icons for the field devices change color depending on diagnostic conditions. Maintenance personnel can easily focus on specific plant areas and assets that require attention.
The right information to the right people at the right time
Maintenance information is immediately transmitted to the right people (operators and/or maintenance personnel) depending on the type and criticality of the diagnostic data analysis. Necessary actions can be taken at the right time, maximizing productivity.
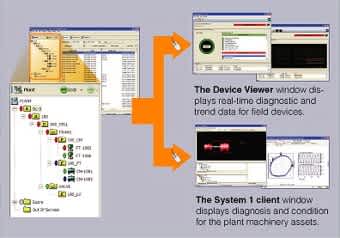
Device Viewer
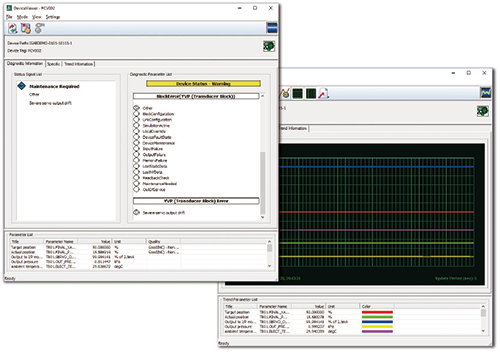
Equipment diagnostic data is shown online in an intuitive format. Equipment data trends can be monitored at a glance.
Plant equipment conditions can be integrally viewed in a list or explorer format. A variety of display formats are available to suit plant needs. Monitor field equipment status online, with icons that facilitate at-a-glance review.
DeviceViewer displays real-time diagnostic and trend data for FOUNDATION™ Fieldbus and HART devices from Yokogawa and other vendors. It features a color-highlighted display of device status and parameters that helps operators grasp the device status at a glance without having to go into the field. DeviceViewer can also run on a CENTUM VP operator station, allowing operators to identify whether a process or a field device is responsible for a failure.
2. Remote adjustment
You can set and adjust equipment parameters remotely from the PRM screen. By using the DTM (Device Type Manager) device setting and adjustment tool provided by the vendor, you can adjust devices intuitively and visually using easy-to-understand graphical screens for each model. Also, for devices such as valve positioners that are complicated to adjust, you can make valve adjustments efficiently by calling a dedicated PRM plug-in application. Using these tools reduces device recovery times, and improves your equipment maintenance efficiency.
3. Efficient setting of device parameters
A template function for the setting of device parameters has been added to R4.01. Once parameters are set using this function, the template can be downloaded to multiple devices. By making it easy to reset parameters, this function allows the immediate start up and use of the new device(s).
4. Asset information management
Assess past alarm history to craft inspection plans. Saved parameters, as well as those for other equipment, can be reused during inspections and calibration. They can also be sorted by specific equipment, alarms, or other parameters; overlooking alarms or forgetting to change modes after inspection will no longer be an issue.
Synchronization with FieldMate™
FieldMate™ is a versatile device management wizard used to set, adjust, and troubleshoot parameters of field devices. All adjustments and settings made with FieldMate™ can be monitored and managed from a PRM window.

5. Maintenance alarm
Maintenance alarm functionality takes warnings from equipment and advance diagnostics, adds relevant information, and notifies maintenance personnel. Alarms intended for operators are conveyed via guidance messages from CENTUM HIS (Human Interface Station).
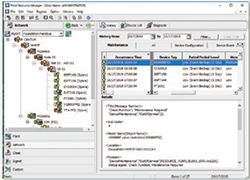
For operators
The operator guide message generated by a predictive maintenance alarm gives operators enough time to manage process changes when an asset fails. Operators can check the device diagnostics information by clicking the Operator Guide Message to launch DeviceViewer.
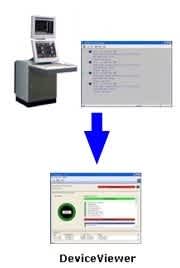
For maintenance personnel
PRM action guidance messages help maintenance personnel determine what actions are needed based on alarm details and probable causes. This allows field maintenance personnel to make the most efficient and effective use of their time. The DeviceViewer window displays real-time diagnostic parameters and trend data for field devices.

Maintenance Marks
Maintenance marks are used by maintenance engineers to identify the status of a device. You can assign a maintenance mark to each device. Using these marks, maintenance engineers can set and check the work status of devices. Maintenance marks can also be linked with CENTUM's operation marks so that maintenance engineers and operators can share the same information and coordinate their work.
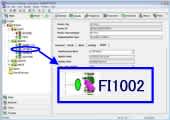
6. Best-in-class collaboration
Collaboration with other companies
PRM has an open integration tool for connecting with valve management and device maintenance software from other vendors. This plug-in application (PIA) interface enables these programs to run as PRM clients and communicate with related devices through Yokogawa host systems. Yokogawa provides a PIA interface development kit to software suppliers with a contract. After developing a program with this interface, a supplier sends it to Yokogawa for integration testing.
ValVue for Dresser valve positioners
ValveLink for Fisher DVC5000f/DVC5000, DVC6000f/DVC6000 valve positioners
Integration with GE Energy's System 1®
Field devices and machinery account for 51% of plant maintenance costs.
GE Energy's System 1 is a proven software platform for real-time optimization of equipment and selected processes, condition monitoring, and even diagnostics.
Through integration with System 1, PRM is able to provide a single monitoring window for the diagnosis of turbines, rotating equipment, and reciprocating equipment, in addition to field instrumentation such as pressure transmitters and flowmeters.
Benefits
- Maintenance strategies are optimized for maximum effectiveness.
- Risk to operations is reduced through improved capabilities, safety, and business performance.
- Costs are controlled though more effective planning and the avoidance of unexpected shutdowns and catastrophic failures.
- Cost savings are achieved by reducing the need for manual data collection.
- Equipment damage is prevented by ensuring operation within design parameters.
KPI report
Data collected from field equipment is used to generate a field asset KPI report, visualizing possible abnormal trends in equipment and peripheral processes. These reports allow for efficient maintenance tailored to the current and future conditions of equipment.
Display of quantitative status information on all the devices in a plant. A function for the reporting of key performance indicators (Field Asset KPI Report) on field assets has been added to R4.01. These KPIs can also be referred to when planning a maintenance schedule.
Device report function
Subscribers to Yokogawa's InsightSuiteAE services can use PRM to generate daily, weekly, monthly, and annual field asset KPI reports from the alarm and event messages that are saved for FOUNDATION Fieldbus and HART devices. A KPI report provides an overview of device conditions and helps users prioritize their maintenance activities.
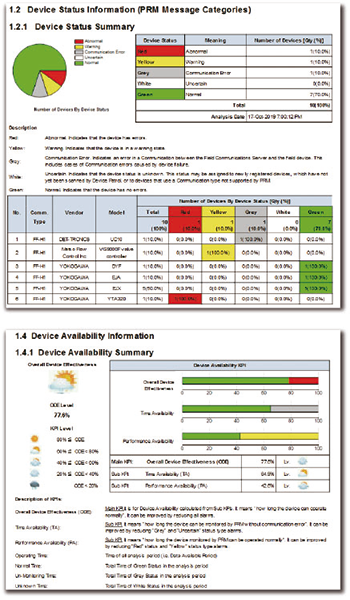
Commissioning support
1. Overview
This is a solution that automatically checks connections, performs loop checks, generates reports, and performs other functions for field devices that support FOUNDATION fieldbus, HART, and other communication protocols. It reduces labor and increases operating quality in plant startup and maintenance.
2. Details
More efficient equipment connection checks
Many field devices can be found in plants, and commissioning the plant requires checking whether the devices were installed in the correct location. Checking the location means opening each piece of equipment one by one―a labor-intensive process. But with the PRM commissioning support package(PRM CSP), rather than having to open the equipment, you simply send a command to a device from the PRM CSP and view it on the device’s display. This greatly reduces the time it takes to perform connection checks.
To check whether the device is installed in the right place, you remove the device’s wiring at the site, and then check whether a connection error occurred on the corresponding device on HIS. This requires connecting and disconnecting wiring.
To check the connection, send a command from PRM CSP to the target device to display a specific pattern on the device’s LCD. This lets you confirm whether the device is connected without connecting or disconnecting any wires. You can also check the configured device tag name.
More efficient I/O loop checks
A loop check confirms proper wiring from the field device to the control system, and the quality of signals. I/O loop checks must be performed for reliable plant startup. However, because they involve checking the device status and changing device configurations, the checks need to be performed on site, which requires a lot of man-hours. The PRM CSP can perform I/O loop checks automatically so you don’t have to be on site. This reduces labor and increases operating quality.
Connect a handy terminal to the device and other stuff, change the device’s output value, and check the value change on HIS. Requires configuring the value for the device on site.
Send a command from PRM CSP to change the device’s output value. Next, read the output value from the device on PRM SCP via Exaopc, and confirm its accuracy. This means less on-site work.
Change the device’s output value on HIS, then check the change in the valve’s opening and other properties on the actual instrument on site. Requires checking the actual device on site.
After changing the output value for the device on PRM CSP through HIS, use a PRM CSP command to read the valve’s readback value from the device, and confirm that the value changed to the desired value. This means you don't have to work on site.
Automatic generation of operations reports means reduced labor and improved quality
- Reduce man hours
Manually organizing descriptions of work performed and formatting it into reports is very labor-intensive. With PRM CSP, you can load test data from range checks and comprehensive loop checks, and automatically create operations reports. This greatly reduces reporting man hours.
- Improve report quality
Assembling all work contents and data by hand invites errors. The PRM CSP loads data and automatically generates reports in a standard format, which cuts down on reporting errors. Plus, users can flexibly customize the format to create high quality reports that fit the customer’s circumstances.
Interoperability
- DeviceFiles (Partner Potal)
- Supported devices
- The list of devices included in the Device Files Media (Partner Portal)
- List of HIST completed devices (Yokogawa website)
- List of FIST completed devices (Yokogawa website)
- PRM integration
- PRM plug-in application integration (Yokogawa website)
- PST Scheduler integration (Yokogawa website)
- Accessories
- A list of accessories interoperable with PRM (Partner Portal)
To view information on Partner Portal, please register as a member.
1. Table of Device Files
The table of Device Files is for members of Partner Portal. To access the table, please use the links above to register as a member.
- Device Files (Partner Portal)
2. Supported devices
A list of devices that the latest PRM version supports can be accessed by members of Partner Portal. Please register to access this information.
- The list of devices included in the Device Files Media (Partner Portal)
Yokogawa confirms the interoperability of Yokogawa FOUNDATION™ Fieldbus devices and non-Yokogawa FOUNDATION™ Fieldbus devices with Yokogawa's host system using the HIST (Host Interoperability Support Test) scheme which has been certified by the FOUNDATION™ Fieldbus. The FOUNDATION™ Fieldbus device list shows the devices which have passed the Yokogawa HIST.
- List of HIST Completed Devices (Link to Yokogawa Global Website)
FDT/DTM Interoperability Support Test, where FDT stands for Field Device Tool and DTM stands for Device Type Manager, is a test activity to reinforce the interoperability between Yokogawa FDT Frame application and the DTM's of third party field device vendors. DTM and Frame application are being developed independently of one another, with the only prerequisite to comply with given FDT interfaces. The interaction can only work, when compliance with these interfaces can be ensured. Even though the FDT Group itself validates the DTM by a certification process, Yokogawa additionally established an "Interoperability Test Lab" to verify the interoperability of the DTM's with our Frame applications, namely PRM and FieldMate.
- List of FIST Completed Devices (Link to Yokogawa Global Website)
3. PRM integration
PRM has an open integration tool to connect with external applications such as valve management and device maintenance software. This scheme is called the plug-in application (PIA) interface. It enables this software to run on PRM as a client and enables it to communicate with related devices through Yokogawa host systems. Yokogawa provides a PIA development kit for software suppliers with a contract. The suppliers are requested to develop interfacing software and to send it to Yokogawa for integration testing.
- PRM Plug-in Application Integration (Link to Yokogawa Global Website) (Link to Yokogawa Global Website)
Operating under PRM, PST Scheduler remotely executes the PST (partial stroke test) for the emergency shutdown valve. The following list shows the positioners and DTMs which have passed the integration test with PST Scheduler.
- PST Scheduler Integration (Link to Yokogawa Global Website)
4. Accessory
PRM supports the following models as HART communication interfaces and has the ability to access parameters and diagnostics information of HART devices via a multiplexer.
- A list of accessories interoperable with PRM (Partner Portal)
Resources
- Highlyadvanced biopharmaceutical plant uses CENTUM, VP Batch, Exaquantum and PRM.
- Total system integration for large-scale biotech production facility.
- Operational Excellence by Asset Maximization, Utilizing Yokogawa's DCS, SIS, Analyzers, and Field Instruments.
- The CENTUM VP PCS and ProSafe-RS SIS were integrated using the same engineering environment.
- Nearly 60 gas chromatographs and a large number of other types of analyzers in several analyzer houses.
- Stable operation and proactive maintenance were realized at new coal-chemical plant in China.
- Yokogawa engineers ensured a successful and efficient commissioning and startup.
- Italian waste to energy plant turns to CENTUM, PRM and FOUNDATION fieldbus solution
- Nearly 1500 FOUNDATION fieldbus devices are monitored and managed using the PRM
- As the main automation contractor (MAC) for this plant construction project, Yokogawa Brazil engineered, installed, and commissioned an integrated control and instrumentation solution
- Yokogawa Brazil completed the commissioning of these systems ahead of schedule and the production of green polymer was started just one week later
- Reinstrumentation project at HDPE plant replaced legacy pneumatic instruments and PLCs with integrated CENTUM DCS PCS and ProSafe-RS SIS.
- HART field devices can be monitored from the central control room with the plant resource manager (PRM) package, enabling a more predictive and proactive maintenance approach that reduces total cost of ownership.
- Steady boiler control by CENTUM CS 3000 with dual redundant CPUs and seven 9s availability
- Total plant information integrated into supervisory information system via OPC interface
- Reduced water, coal and other resource consumption
- CENTUM CS3000 seamlessly integrates with multivendor control systems through OPC interface.
- Challenging predictive maintenance to monitor many transmitter data through PRM.
CENTUM VP was selected for the BOP in a concentrated solar power plant of the Xina Solar One Project.
Yokogawa provided a complete control system solution that integrates the subsystems in the plant as a system of systems.
- DCS, SIS, PRM with FOUNDATION fieldbus and OTS Installed in Thailand First LNG Terminal.
- Alarms are issued before any device fails completely, enabling predictive maintenance that reduces maintenance costs throughout the facility lifecycle.
- Xstrata designed and supplied a plant wide process control system for the project based on a Yokogawa CENTUM CS 3000 system.
- Xstrata has used Yokogawa extensively in the past and trusted the reliability of the CS 3000 system.
- Computerized Maintenance Management System by PRM and SAP Schedules Field Instrumentation Maintenance.
- The frame applications and DTMs support the preventive maintenance strategy with self-diagnostic and condition monitoring.
Yokogawa's integrated asset management system that combines FDT technology with a device management tool is being used to achieve real productivity advantages and savings in maintenance and service operations.
- Fieldbus technology introduced to realize predictive and preventive maintenance.
- ISAE to improve the reliability of diagnosis and parameter setting, utilizing data collected by PRM.
- 16,000 FOUNDATION Fieldbus devices
- Main Automation Contractor (MAC)
- DCS anywhere concept integration with site SAP system
- Long term maintenance contract
- Sustainable development
- CS Batch is used to automate a wide range of Reichhold's batch processes and multi-product/multi-path processes.
- Using PRM, process engineers can immediately find out the status of every field device without having to do an onsite inspection.
- HMEL selected an integrated solution from Yokogawa
- Yokogawa India oversaw and implemented the engineering, installation, and commissioning of the refinery
- Integration of CENTUM CS 3000 with ProSafe-RS improves plant safety and reliability.
- Yokogawa's PRM package manages more than 500 HART field devices including control valves.
Thai Acrylic Fibre Co., Ltd. (TAF) was established in 1987 and is currently a leading acrylic fiber manufacturer in the ASEAN region with 450 employees. It produces a wide range of acrylic fiber productions with varied deniers and the annual production recorded 77,000 megatons in 2004 which is five times the production rate at the time of establishment.
- PRM allows a preventive maintenance approach where maintenance can be scheduled and performed before a field device fails.
- Exaquantum gathers plant data from the CENTUM VP to generate a variety of reports on the polymerization process.
Eraring Power Station, located just north of Sydney, is one of the largest power stations in Australia, comprising four 660MW coal-fired units. The power station has operated reliably since 1981. To ensure continued reliability for the next few decades, Eraring Energy, the owner of the power plant, decided to replace the original hard-wired control equipment with a modern integrated control and monitoring system (ICMS).
- Smooth and safe switchover to the new system
- Easy-to-use, easy-to-engineer system, plus various post-installation enhancements
- Tuned controllers for smooth plant operation and better traceability of process upsets
- Various other improvements thanks to advanced process control and MVC implementation
Saudi Aramco's operations span the globe and the energy industry. The world leader in crude oil production, Saudi Aramco also owns and operates an extensive network of refining and distribution facilities, and is responsible for gas processing and transportation installations that fuel Saudi Arabia's industrial sector. An array of international subsidiaries and joint ventures deliver crude oil and refined products to customers worldwide.
PetroChina Guangxi Petrochemical Company has completed construction of a combined refinery and petrochemical production complex in Qinzhou, a port city in China's Guangxi Autonomous Region. With a 10 million ton per year capacity, the refinery is one of China's largest, and is truly world class, using a highly advanced hydrogenation process, with the main process technologies coming from the USA and France.
- State-of-the-art FOUNDATION fieldbus technology
- Plant Resource Manager (PRM) field device management system
- Remote data monitoring via WAN
- Using the CENTUM CS 3000 system, many kinds of plant key performance indexes are calculated and analyzed to produce further improvements.
- During plant start-up, PRM helps the customer's engineers perform all the loop checks.
- Yokogawa's CENTUM VP and PRM improve efficiency at new nylon plant in Thailand.
- At the plant startup stage, PRM was used together with FieldMate to thoroughly check all loops.
- Yokogawa's integrated solution contributed to reliable and efficient operation.
- All the instrument information is fully integrated with the instrument management system.
- The visualization of data using the Exaquantum PIMS plays an important role in efforts to improve operations at this power station.
- To reduce operator workload and eliminate unplanned shutdowns, HERA decided on the use of field digital technology at this power station.
- Yokogawa provides CENTUM CS 3000, Exaquantum and PRM solutions for China's largest refinery/petrochemical complex.
- Process data management by Exaquantum is a key issue in the petrochemical complex.
- A Japanese petrochemical plant leverages FDT/DTM-compliant intelligent field devices and Yokogawa's PRM asset management system for maintenance efficiency.
- The customer aims to improve maintenance efficiency further by introducing condition-based maintenance (CBM).
To enable central control of the entire plant, all of its subsystems are integrated with Yokogawa's CENTUM VP DCS.
- Kuraray EVAL and Yokogawa prepared carefully for the expansion and modernization of the CENTUM system.
- Management of 400+ fieldbus instruments by Yokogawa's PRM plant resource manage also helped the project to proceed smoothly.
Process automation end users are under more pressure than ever to do more with less. The current economic climate means that many automation capital projects are on hold. With capital budgets tighter than ever, users instead focus on operational budgets (where cost cutting is also a key concern), or on automation investments with a very rapid return on investment.
- Biofuel
- Biomass Power
- Chemical
- Drinking Water Treatment
- Energy Transition
- Geothermal Power
- Iron & Steel
- Mining & Metal
- Offshore (FPSO FLNG & FSRU)
- Oil & Gas
- Oil & Gas Downstream
- Petrochemical
- Pharmaceutical
- Power
- Pulp & Paper
- Refining
- Specialty & Fine Chemical
- Thermal
- Upstream
- Waste to Energy
- Water & Wastewater
In today's dynamic industrial marketplace, the only constant is change. Raw material costs, energy costs, market demands, environmental and safety regulations, technology, and even the nature of the labor force itself are constantly changing, and not always in predictable directions.
- Biofuel
- Biomass Power
- Chemical
- Drinking Water Treatment
- Energy Transition
- Geothermal Power
- Iron & Steel
- Mining & Metal
- Offshore (FPSO FLNG & FSRU)
- Oil & Gas
- Oil & Gas Downstream
- Petrochemical
- Pharmaceutical
- Power
- Pulp & Paper
- Refining
- Specialty & Fine Chemical
- Thermal
- Upstream
- Waste to Energy
- Water & Wastewater
Yokogawa Electric Corporation promotes the standardization of FOUNDATION™ fieldbus as the communication foundation supporting Asset Excellence for VigilantPlant, which is an approach aimed at the advancement of plant instruments and equipment. With the recent dramatic advancement of fieldbus technologies, information processing technologies, and network speed, it has become possible to process various kinds of information inside the field sensors and transmit the results to the distributed control system (DCS) and host computer.
In 2005, Yokogawa announced "VigilantPlant" as a concept to ward the realization of a type of plant operation that is considered ideal by our customers.
Intelligent field instruments and process analyzers accumulate diverse field information including process values and diagnostic results. This data needs to be sent to upper systems such as distributed control systems (DCS) via digital communications such as FOUNDATION Fieldbus and analyzer buses, or hybrid communications such as HART and Brain, and visualized to enable the customer to utilize them for plant operations and maintenance.
More than ten years have passed since the first digitized field devices were introduced. These support either a hybrid communication protocol such as HART or a full digital communication protocol such as FOUNDATION Fieldbus.
As field instrumentation devices become increasingly digitized and computerized, interactive and remote access to a large quantity of field information becomes possible. This will increase the efficiency of plant equipment maintenance by reducing labor requirements in field patrol work for example.
There has been increasing demand for cost reductions and lower-priced products in the manufacturing industry, and maintaining cost competitiveness and achieving optimum costs have become necessary for the survival of manufacturers. This calls for minimizing TCO (Total Cost of Ownership) over the whole life cycle of plants and maximizing TVO (Total Value of Ownership).
Process automation involves both operation and maintenance. Plant operation and monitoring are mainly conducted by a control system such as CENTUM, while equipment maintenance is handled by Plant Asset Management (PAM) such as Plant Resource Manager (PRM).
As compared to Distributed Control Systems (DCS) such as CENTUM VP that monitors the operations of the overall plant, PRM is a type of Plant Asset Management (PAM) software package that primarily focuses on the maintenance of devices and instruments.
Environment and safety are major topics on a global scale in recent times. As symbolized by the effectuation of the Kyoto Protocol, an interest in preserving the environment is growing worldwide, and there is also a tendency to criticize more severely, occurrences of industrial accidents that are accompanied by environmental contamination or which may cause damage, etc., to residents in the surrounding areas.
The FieldMate versatile device management wizard is PC software mainly used for configuring and adjusting field devices. Under the concept of "one tool for all," Yokogawa has been enhancing this software to support a wide range of field devices and field communication protocols.
Asset Excellence (AE) provides a set of solutions for maintaining a plant in good condition at reasonable cost to ensure that it works as a production infrastructure. To reduce maintenance costs without causing a risk to production, it is necessary to change from breakdown maintenance to predictive or preventive maintenance.
Latest field devices have not only various self-diagnosis functions but also process-interface-diagnosis functions such as valve diagnosis of valve positioners and impulse line blockage detection of differential pressure transmitters. The YVP valve positioner can easily perform initial tuning, parameter adjustment, trend monitoring, and valve diagnosis, by using the ValveNavi YVP management software.
Due to emerging competitors from the rapidly growing countries such as India and China and the global economic downturn triggered by the Lehman shock, many companies in the process industries are struggling to survive the severe global competition.
March 2006
The new CSPC (CNOOC and Shell Petrochemicals Company Limited) petrochemical complex at Daya Bay in southern China is one of the world's largest process industry projects (see box, Figure 1 and Table). It has a control system to match. Process Worldwide spoke to Johan Veerman, principal instrument and process control engineer at CSPC, about the challenges of managing such a huge job.
May 2006
Predictive maintenance allows to schedule plant maintenance before a failure occurs only when it is necessary, greatly reducing unnecessary inspection and improving productivity. Yokogawa's Asset Excellence initiative helps its customers make their plant asset condition predictable and performance sustainable.
The global market for Process Information Management Systems (PIMS) is well established. Companies using these systems have collected data for many years, and the advent of open systems architecture now means data from many different systems can be shared around the plant or business and used in many different ways, including providing environmental monitoring capabilities.
2011
Decades of operation, modernization and expansion have left many chemical plants with a somewhat haphazard automation mix of different controls, process control systems, remote I/Os and field devices. The various components may use different communication protocols such as HART, PROFIBUS or FOUNDATION Fieldbus, and are often based on different device integration technologies.
Combining smart instruments, analyzers and valves with a modern asset management system can provide faster response to incidents, enable proactive maintenance, and reduce downtime.
September 2007
Yokogawa's web-based DCS Anywhere has simplified commissioning at the Nanhai petrochemicals complex. With a total investment of 4.2 billion US dollars, the Nanhai petrochemicals complex at Daya Bay in Huizhou, China, has attracted a lot of attention because of its sheer scale.
Offshore, February 2013
Offshore and deep-water production has been a significant factor in the sustained growth of the oil and gas industries over the past decade and this trend is expected to continue beyond 2013.
October 2008
Yokogawa's Raju Seshadri reveals the latest trends in predictive maintenance solutions. We all dream of being able to see into the future, of being able to predict what will happen before it has, and taking decisive action before something negative occurs later.
September 2006
Asset management systems need to be able to handle more data and present information in better formats if plant managers are to move towards proactive maintenance, says John van der Geer, industrial automation marketing manager at Yokogawa Europe.
July 2010
Martin te Lintelo, Yokogawa Europe B.V., The Netherlands, discusses high level control system design for LNG receiving terminals. As demand for LNG increases worldwide, players face seemingly conflicting challenges. On one hand, they must expand capacity in different regions, make the business and production as agile and adaptive as possible, and improve operational efficiency.
LNG Industry, Summer 2012
Martin te Lintelo, Yokogawa, The Netherlands, discusses the need for better automation, measurement and control instruments to cope with the rising popularity of LNG.
Downloads
Videos
What's the proper plant asset management (PAM) to prevent sudden equipment failures? Have the facility managed properly for high-reliable and stable plant operation? Yokogawa's PRM leads to the revolving of PAM issues throughout the plant life cycle.
By prompt trouble shooting realizes to improves Plant Productivity. Yokogawa’s Plant Resource Manager, PRM enables you to check remotely the status of equipment without head on-site. PRM contributes to Increased Plant Productivity.
"Remote plant maintenance is absolutely impossible!" ...Don't you think so?
In order to minimize travel and contact with people, it's becoming commonplace to work remotely. That’s why we’d like to propose the Field Asset KPI Reports provided by Yokogawa PRM.
Yokogawa's Control Valve Diagnostics leads to the revolving of the valve issues throughout the plant life cycle.
Yokogawa's parameter monitoring is effective in understanding the trend of device abnormalities in field devices, and can be used for preventive maintenance of devices.
Yokogawa's InsightSuiteAE leads to the revolving of the plant assets issues throughout the plant life cycle.
Plant Healthcare Service for field assets is a service that Yokogawa quantitatively grasps the status and risks of customer’s plant assets, and provides useful information for asset maintenance optimization.
News
-
Press Release Jan 11, 2022 Yokogawa Enhances Cybersecurity and Safety for the OpreX Control and Safety System Lineup
-
Press Release Nov 13, 2019 Yokogawa Releases Plant Resource Manager (PRM) R4.03, a Software Package in the OpreX Asset Management and Integrity Family
- Enhanced device diagnostics for predictive plant maintenance -
-
Press Release Apr 11, 2018 Yokogawa Releases Plant Resource Manager (PRM) R4.01
- New maintenance and operations support function for the display of statistical information on the status of all plant devices -
-
Press Release Sep 6, 2016 Yokogawa Releases Plant Resource Manager (PRM) R3.31
- Improving maintenance efficiency -
-
Press Release Jul 14, 2016 Yokogawa Wins Major Refinery Control Systems Order from S-Oil Corporation
Looking for more information on our people, technology and solutions?
Contact Us