Create a roadmap for AI implementation or continue to build upon existing strategies with a range of industry-proven solutions.
What Are the Benefits of AI Solutions?
Abnormal Sign Detection
Predict equipment failures and plant shutdowns. By enabling users to perform maintenance before an abnormality occurs, countermeasures can be taken in advance, improving uptime.
Root Cause Analysis
Identify sources of reduced quality and changes in consumed power. By identifying focus areas when implementing quality measures, product consistency improves.
Quality Estimation
Assign quality indexes, predicting quality before testing. By avoiding destructive testing and other time-consuming processes, costs are redued and quality is increased.
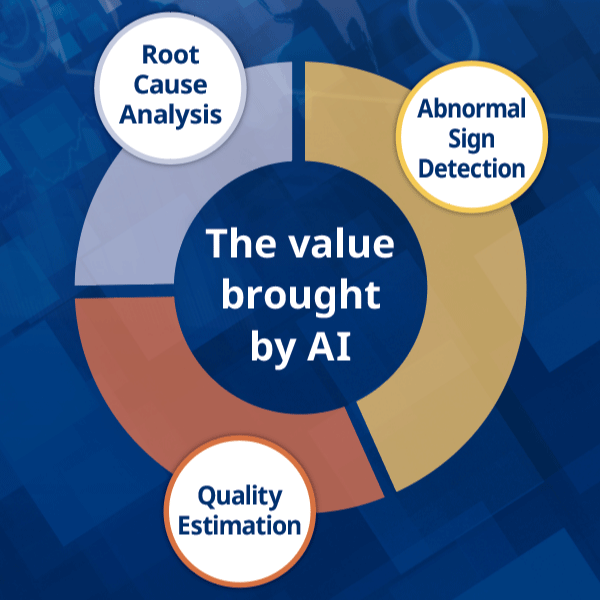
→ AI Product Solution Book download
Details
AI Solutions
A shaft breakage occurred in a reducer that monitored trends with a wireless vibration sensor (Sushi Sensor). The graph below shows acceleration, speed, and surface temperature data, and the results of AI analysis based on those data. The moving average of health index calculated by AI moved from the normal to abnormal range three weeks before a failure. It captured the “anomality” that were signs of abnormality earlier than the sensor data trend changes. By combining the Sushi Sensor with the AI, undesired states can be notified based on the equipment's vibration and surface temperature data, which enables users to predictively detect equipment abnormality and take prior actions for equipment maintenance.
Results from YOKOGAWA AI solutions
Industry | Category | Overview | |
---|---|---|---|
Abnormal Sign Detection | |||
Chemical | pH Sensor | Predict deterioration of sensors installed in a waste water pipeline | |
Oil | Furnace | Predict operating conditions of a furnace by using process data | |
Power | Pump | Predict cavitation in pipes by using pressure-related data | |
Root Cause Analysis | |||
Oil | Compressor | Identify the causes of reduced efficiency of cooling compressors in area A of a plant by using process data | |
Hot spring | Hot spring control | Identify the causes of changes in hot water distribution by using operating data | |
Paper & Pulp | Beating machine | Identify the relationship between a beating machine’s power and product quality | |
Quality Estimation | |||
Electronic parts | Electronic parts manufacturing equipment | Identify damaged parts in an assembly process by using sensor data | |
Chemical | Industrial material continuous production equipment | Predict indicators between quality measurement indicators by using 18 types of data | |
Oil | Product quality values | Estimate product quality values by using production data | |
Food & drug |
Medical product manufacturing equipment | Predict the quality of completed product by using 10 types of manufacturing data |
See the AI Product Solution Book for other achievements.
→ AI Product Solution Book download
Utilizing decades of analysis experience and elemental technologies, Yokogawa can offer a lineup of easy-to-use AI products.
- Draw the past to the present, and on to the future
Now with the Future Pen SMARTDAC+ GX/GP Series paperless recorders - AI on a stand-alone computer detects predictive abnormality sign of equipment
with anomaly detection, AI analysis data logging software GA10 + Sushi Sensor - With a wealth of I/O for high scalability and fan-less high environmental worthiness
Supports Python Industrial AI Platform e-RT3 Plus
For additional examples of optimal plant control using AI reinforcement learning, please see below.
→ Plant control by AI
Future Pen SMARTDAC+ GX/GP Series Paperless Recorders
AI is installed as standard while maintaining the reliability and functions of the SMARTDAC+ GX/GP Series Paperless Recorders. With no complicated settings, users easily register the channels that need to be monitored as future pens and draw the near future as waveforms.
The GX/GP series is a panel mount or portable paperless recorders that provide intuitive touch panel operations. Its highly flexible modular I/O architecture enables you to acquire, display, and record data such as temperature, voltage, current, flow, and pressure in various industrial production and development sites.
Please refer to the details of SMARTDAC+ SMARTDAC+ GX/GP Series Paperless Recorders
> Panel mount type GX10/GX20 > Portable type GP10/GP20
GX/GP AI functions
Future pen
Use acquired data to predict future data and draw predicted future waveforms along with real-time data on the trend monitor. The future waveforms allow users to identify and deal with likely problems.
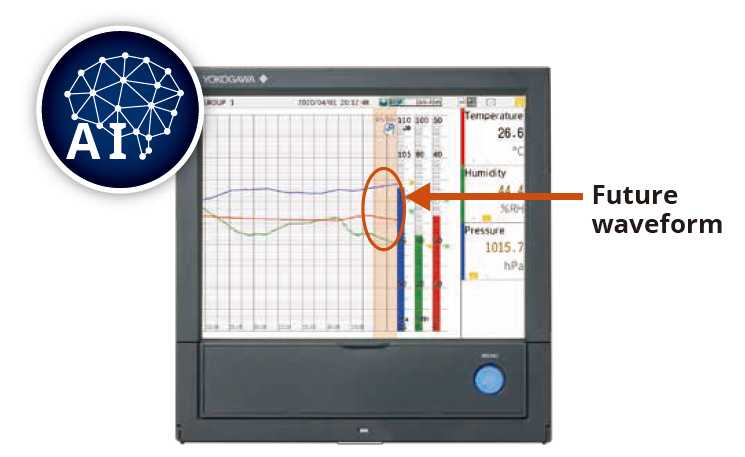
Future alarm
Set future alarms against future measured data from the future pen. Future alarm information is shown in a future alarm summary. When a future alarm is generated, external output or email alert users.
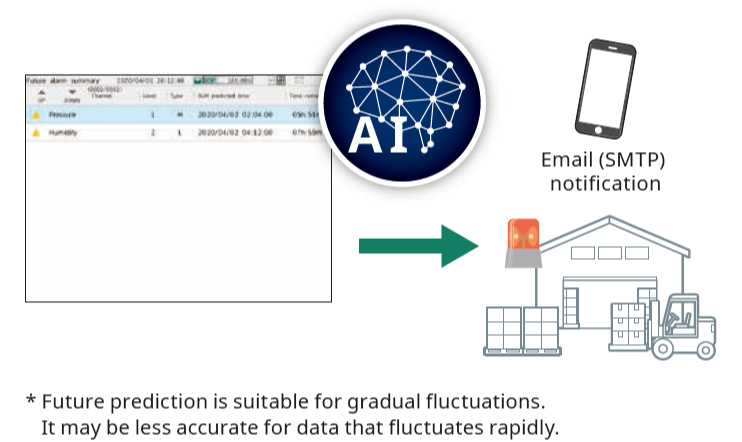
Recorder-centric AI solutions
Easily add AI to a recorder (GX/GP future pen, future alarm)
Temperature and voltage process signals can be displayed from past to present, and future waveforms by AI function. (GX/GP)
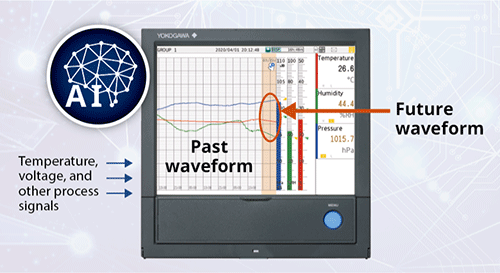
Accurate AI analysis in real time on a PC, displaying determination results on site. (GX/GP + GA10)
GX/GP collects the process signal and displays the measured values.
Send real-time data to PC, the AI analysis function of the software GA10 displays the result of AI judgment such as uncomfortable feeling detection on the GX/GP on the site side.
Ask us about the highly accurate AI consultant service.
Analyze via an embedded device with accurate AI and display determination results (GX/GP + e-RT3 Plus)
GX/GP collects the process signal and displays the measured values.
Collect process signals with GX/GP, display measured values, transmit data in real time to the Python-compatible AI platform e-RT3 Plus, and deploy the judgment results by the AI algorithm developed by the customer on the GX/GP screen can do.
Ask about the highly accurate AI consultant service.
AI Analysis Data Logging Software GA10 + Sushi Sensor
The need for maintenance grows as equipment ages. Equipment conditions are mainly ascertained by human workers through inspections such as operator rounds inspection. However, many industries face the problems of labor shortages and the retirement of skilled workers. Additionally, the measured results obtained through operator inspections are not quantified, and often cannot be utilized effectively. More efficient equipment maintenance mechanisms are urgently needed.
Automatically detects anomalies that are signs of abnormalities
GA10 + Sushi Sensor are a equipment predictive maintenance solution that operates like an AI operator, detecting the anomalies that are signs of abnormality, and automatically notifying the user.
This allows workers to be dispatched to equipment that needs maintenance at just the right time, reducing equipment inspection man-hours, quickly discovering abnormal signs, and preventing unanticipated equipment shutdowns. Users realize more efficient equipment maintenance and increase plant availability.
What Is a GA10?
GA10 is PC-based data logging software that connects various devices installed in factories and premises (such as Sushi Sensor, recorders, and data loggers) through an Ethernet network, and performs monitoring and recording.
What Is a Sushi Sensor?
The Sushi Sensor* is a wireless solution for IIoT that includes sensors for detecting equipment conditions. It supports low power, wide-area LoRaWAN communication standard for wireless network.
*Sushi Sensor is to be released to other countries in order. For details, please click “more information”
GA10 AI Functions
Anomaly Detection
AI can learn what normal operating data “looks like” by aggregating data on GA10 from sensors implemented to the production equipment. This enables it to identify anomalies and notify users. By implementing the Sushi Sensor, the AI can also notify users of anomalies based on the equipment’s vibration and surface temperature data, predictively detecting equipment failure.
The AI detects anomaly data in large data sets and notifies users by highlighting display.
Realize Predictive Maintenance with Trend Monitoring
- Monitoring of large amounts of data
- Digitizing on-site know-how
Efficient Equipment Maintenance
- Digitize equipment health conditions and monitor trends
- Reduce the cost of operator rounds inspections
- Share and transfer field operators' knowledge and experience of equipment maintenance
- Prevent sudden unexpected equipment failures
Quickly Capture Signs of Equipment Abnormalities
- Capture signs, even with equipment for which it is difficult to apply threshold-based abnormality determination
- Based on a variety of data, determine signs of equipment abnormalities
Access Signs of Equipment Abnormalities with Intuitive Settings
- Simple system: Sushi Sensor, LoRaWAN gateway, and GA10
- Easily specify a data period of normal conditions and start automated analysis
- Notifies users when anomalies are detected
The e-RT3 Plus
With a wealth of I/O for high scalability and fan-less high environmental worthiness, the e-RT3 Plus supports Python Industrial AI Platform, making it indispensable for machine learning development and other AI branches. In addition, it can be scaled to add many AI open source libraries, quickly ramping up a plant's AI development.
Able to withstand the tough environments, the e-RT3 is ideal for industrial AI platforms, leveraging easy access to I/O.
> Please refer to the details of e-RT3 Plus
I/O Modules for Easy Access
With a wide selection of I/O modules, users can easily incorporate applications into the data acquisition and control level. The CPU and I/O modules are both from Yokogawa, making them easy to connect. And in the rare case of hardware trouble, isolation is simpler than ever.
Ubuntu Supported
Includes the freely available and open-source Linux Ubuntu, ensuring compatibility with a wide range of open-source software. Additionally, it facilitates seamless integration with applications like network file sharing and PC-less SCADA, simplifying your experience.
Multi-CPU Supported
Place the e-RT3 Plus CPU next to an existing sequence CPU and divide their roles: a high speed ladder for control and the e-RT3 Plus for communication and AI determination.
Environmental Worthiness
Holds up in hot, harsh environments. The e-RT3 has a fan-less design, modules that can withstand temperatures from 0°C to 55°C, and installs in factories, plants, or inside a box outdoors.
Stable Supply
Long-term stable supply made possible by Yokogawa, the PLC maker. Yokogawa maintains a long and steady supply of the same products and parts.
Highly Accurate AI Using Python for Harsh Environmental Industrial Applications
Reduce Development Time
Existing AI applications stay as-is while maintaining fewer tedious I/O settings.
Environmental Worthiness
The device used for development goes right into the harsh environment. Runs in environments where single-board computers couldn’t until now.
Plant Control with AI and Reinforcement Learning
Reinforcement learning is a machine learning type where AI learns from trial and error. Yokogawa's reinforcement learning technology is remarkably practical, gaining insights from minimal trials.
Issues with a Complex Process
- Indicated values are destabilized due to disturbances, resulting in loss of raw materials
- Skilled workers have difficulty passing on control adjustment technology, requiring time and labor
- Destabilization of process and decrease in quality due to unfamiliar control methods
Features of Yokogawa Electric’s Reinforcement Learning:
- Learns with a small number of trials.
- Optimized with reinforcement learning technology specialized for the control field
AI Control Test Equipment by a Three Tank Level Control System
Real-world sites often require complex control mechanisms.
Below is an example of reinforcement learning technology applied to control a Three Tank Level Control System. [Soundless video]
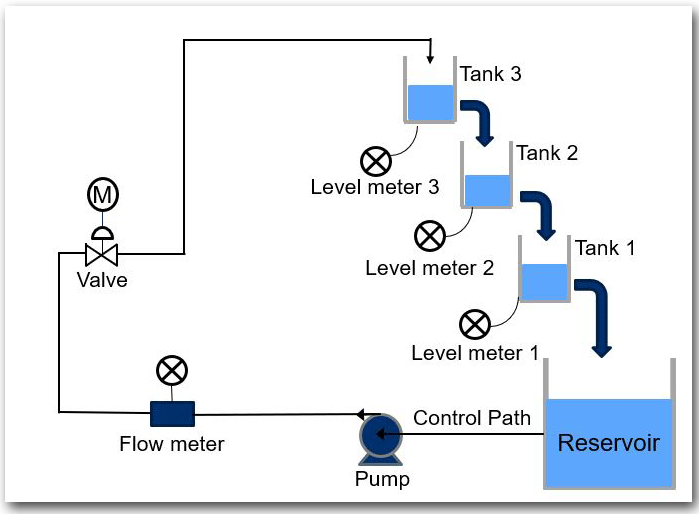
Result
In under 4 hours of learning, it found the ideal control method to eliminate the overshoots that occurred previously.
Resources
ENEOS Materials successfully achieved the world's first long-term autonomous operation of a plant using Yokogawa's AI. FDKPP saves energy and reduces operator workload while maintaining manufacturing quality.
The plant still has legacy OT systems that pose significant challenges in a modern ammonia manufacturing environment due to their limited functionality, which can prevent the adoption of advanced technologies and tools needed to keep up with current production demands. These systems often require costly and hard-to-find maintenance and support as they age, and they lack robust cybersecurity measures, making them vulnerable to cyber threats.
Wireless sensors and the network can reduce expenses
Industrial artificial intelligence/machine learning (AI/ML) software and long-range sensors predict maintenance requirements across entire enterprises, increasing productivity and profits.
Videos
GA10 is PC-based data logging software for monitoring and recording data by connecting to devices distributed in a factory. Now with an AI-based Anomaly Detection function, the AI notifies you of anomalies before equipment abnormalities occur.
AI development is not that difficult! This tutorial video shows you how to develop AI application on e-RT3 F3RP70 by running AI sample program available on Partner Portal.
News
-
Press Release Mar 30, 2023 In a World First, Yokogawa’s Autonomous Control AI Is Officially Adopted for Use at an ENEOS Materials Chemical Plant
– One year of stable operation demonstrates this next-generation control technology can decrease environmental impact, achieve stable quality, and transform operations –
-
Press Release Feb 26, 2023 Yokogawa Launches Autonomous Control AI Service for Use with Edge Controllers
- Optimizes control to improve productivity and save energy -
-
Press Release May 29, 2022 Yokogawa and DOCOMO Successfully Conduct Test of Remote Control Technology Using 5G, Cloud, and AI
- Targeting remote, autonomous operations for the process industries
-
Press Release Mar 21, 2022 In a World First, Yokogawa and JSR Use AI to Autonomously Control a Chemical Plant for 35 Consecutive Days
- Putting into practical use a next-generation control technology that takes into account quality, yield, energy saving, and sudden disturbances -
-
Press Release Apr 13, 2021 Yokogawa to Undertake Proof of Concept Test of 5G, Cloud, and AI for Remote Control of Plant Systems with NTT DOCOMO
Looking for more information on our people, technology and solutions?
Contact Us