Chlor-Alkali Industrial Production Plant
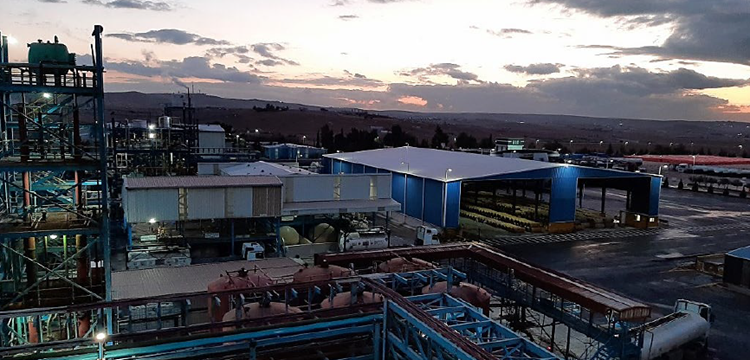
A specialized company in Caustic Soda and Chlorine manufacturing and considered
as one of the largest companies in the Chlor-Alkali industry.
About
Quality is never an accident; it is always the result of intelligent effort. This chlor-alkali industry client is considered one of the largest and most advanced chemical companies in the development and manufacturing of advanced chlor-alkali products, such as caustic soda, hydrochloric acid, sodium hypochlorite, and chlorine.
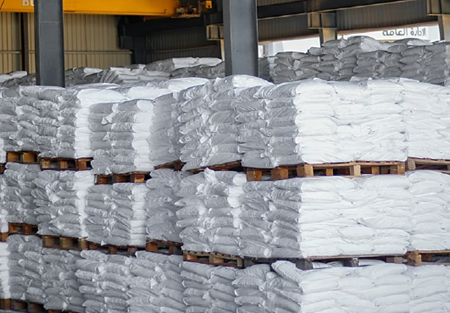
Example of one of the production stages for caustic soda, playing a critical role
in ensuring global demand is met today and in the future.
The operating capacity of this client is 93 tons of caustic soda per day, according to the highest/international quality standards. Using the Bichlor electrolysis system, one of the modern technologies that are environmentally friendly and preserve the health and safety of workers and community members, this client desired to continue to improve and optimize production.
Executive Summary
To ensure the quality of their products, this chlor-alkali producer is investing annually to continuously keep their production and operational machinery up to date with the latest technologies provided in the chemical industry. Moreover, this client applies many modern operating systems to cope with ongoing industrial developments that secure higher efficiency in operation and lower variable costs.
Application Background
A Chlor-Alkali process can shortly be defined as a process where treated Brine Water (NaCl) is subjected to an Electrolysis process, which yields Chlorine Gas, Hydrogen Gas, and Caustic (NaOH).
2NaCl + 2H2O → Cl2 + H2 + 2NaOH

The Electrolyzer operates at a power of 575 volts DC and 17.4 KA. This means there is a huge current flow in the NaOH and Liquids circulating in the Electrolyzer cells, which necessitates the use of GRP or Plastic (Non-conductive) process piping for the process.
The overall efficiency of a membrane-type chlor-alkali cell, measured by the number of kilowatt hours required per unit of caustic produced, is a complex result of the interaction of several factors.
These include, among other things, the Concentration, pH, Temperature, and Flow Rate, or residence time, of the anolyte brine and catholyte caustic solutions within the cell and the cell current and voltage.
Challenges
Prior to using Yokogawa's AXG Magnetic flowmeter, the client used several other reputed brand magnetic flowmeters, and even Variable Area flowmeters on Brine Water line and Caustic line.
These competition's flowmeters were highly inaccurate and highly fluctuating, due to the following reasons:
- The presence of huge DC stray current in process liquid
- Magnetic field around the Electrolyzer cell
- Unavailability of Expert Advice and support from Flowmeter vendors
As a result, the client was facing flow control problems, i.e., the mismatch between the Brine input rate, Electrolyzer, and the Caustic generation rate. This further led to the suspicion of Electrolyzer cell efficiency and increased power consumption.
The competition’s flowmeter was suffering from a high noise problem as it was a low-frequency pulsed DC magmeter. PTFE-lined magmeters were used, which also resulted in leakage and failure of the meter due to poor electrode liner sealing.
In some lines, VA meters were used where the magnetostrictive pickups were affected by the DC current field also leading to high fluctuation and improper flow reading.
Solutions
Yokogawa approached the client to solve the Brine and Caustic flow-measurement challenge by recommending the use of an AXG magnetic flowmeter. The client was initially reluctant to accept a magnetic flowmeter solution due to the past experiences using competitor's magnetic flowmeters. Yokogawa assured the client that a detailed study of the process would be provided, and install a pilot magnetic flowmeter and analyze the outcome.
The study of the process concluded that a high DC Stray current was present in the NaOH line. There was a strong magnetic field radiating from the Electrolyzer cell interfering with the flowmeter electronics and generating additional noise. The necessary corrective action was suggested to the client and the AXG Magnetic flowmeters were installed on the Caustic and the Brine lines.
The AXG Magnetic flowmeter was shielded by means of iron (Ferromagnetic material) enclosures to isolate it from the cell’s magnetic field effect generated by the Electrolyzer cells.
Ferromagnetic material has good magnetic field permeability and are good magnetic field shielding material.
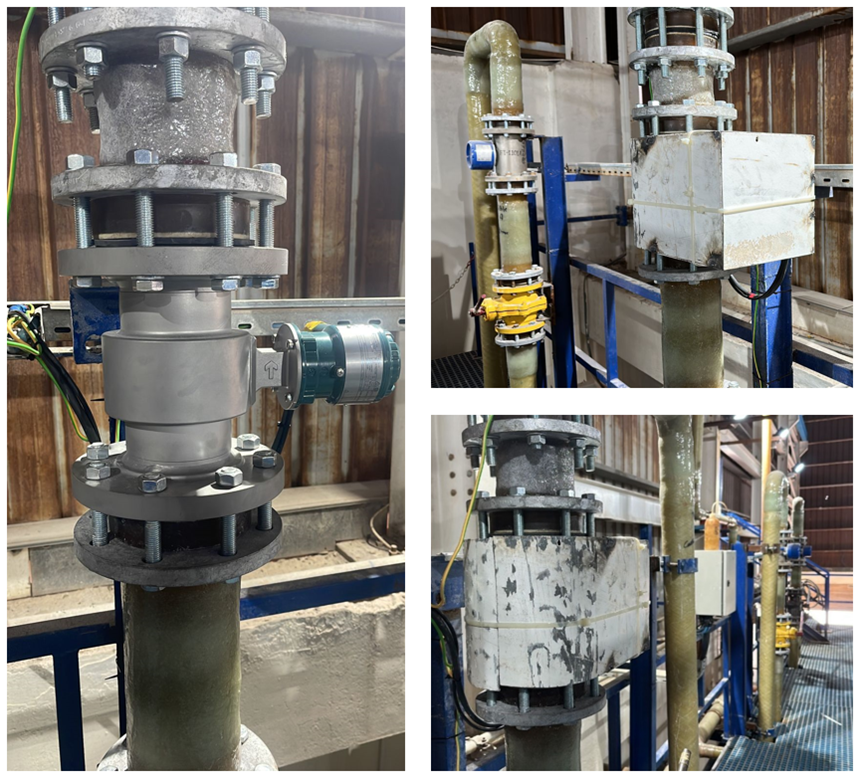
Initially, the AXG showed some fluctuations, but not to the extent of the competition's magnetic flowmeter fluctuation, thanks to the AXG’s unique Noise Level detection feature. We were getting Noise Level 3 (20 cm/s). It was instantly identified the grounding was done to the incorrect pit, having rectified the grounding to the correct pit, the Noise level dropped to Level 1 (5 cm/s).
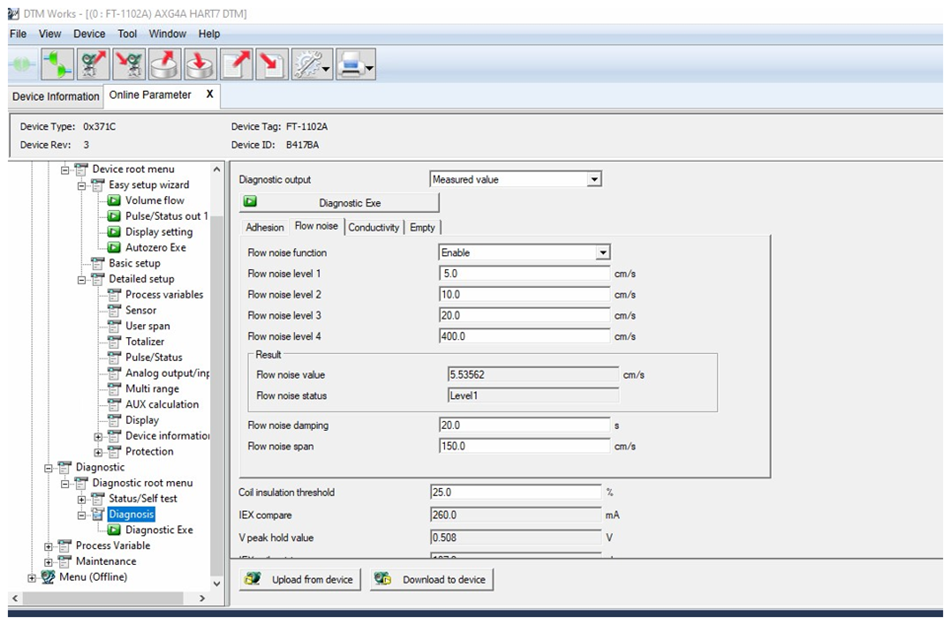
The AXG with a unique /ELC option to cut off DC noise present in the process fluid worked phenomenally well with highly stable and accurate flow readings.
The /ELC option cuts off the stray DC current noise present in the process fluid. This is achieved by a specialized capacitance circuit between the Detector and the Converter.
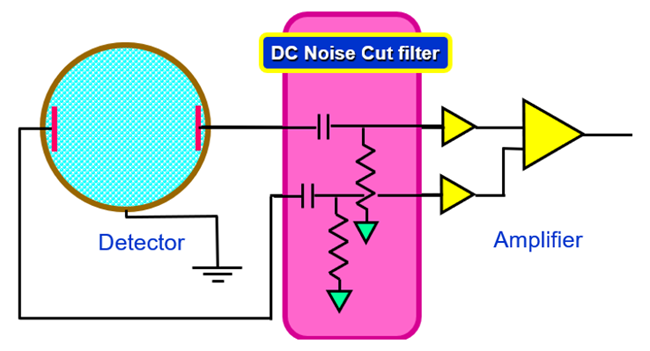
The Frequency of the Excitation signal fed to the Electromagnet plays a key role in the Magnetic Flowmeter’s measurement stability (Noise rejection/cancellation).
Competitions magnetic flowmeters only operate on single excitation frequency, it will be either Low-Frequency Pulsed DC (around 6 to 12Hz) or High-Frequency Pulsed DC (around 30 to 50Hz.)
Low Frequency Excited (6 Hz to 12 Hz) Magmeters suffer from Noise (electrode potential noise) caused by Slurry, Bubbles, and Conductivity Fluctuations. Especially in Electrolyzer applications for Brine and Caustic flow measurement, the effect of this unstable electrode potential noise is very pronounced which leads to high flow measurement fluctuations. This means a Low-Frequency excitation magmeter will not be able to deliver stable and accurate flow measurements in such applications. On the other hand, High-Frequency Excited (30 to 50Hz) Magmeters suffer from Poor Zero Stability.
Thanks to the Dual Frequency excitation of AXG it delivers stable zero and noise immunity. Yokogawa AXG’s patented Dual Frequency Excitation (6.25 and 75Hz simultaneously) has the best Process Noise rejection and Zero Stability.
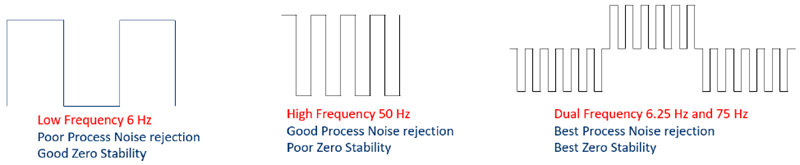
The Built-In Meter Verification of AXG proved to be a very important feature to check the meter's health in this harsh application. The built-in meter verification checks the following and informs the user of a definitive Pass/Fail result.
- Magnetic Circuit
- Excitation Circuit
- Calculation Circuit
- Device Status
- Communication Status
Additionally, the meter's accuracy performance can be verified with the extended Meter Verification which can be performed using FieldMate and Yokogawa Magnetic flowmeter calibration kit, where a report is generated.
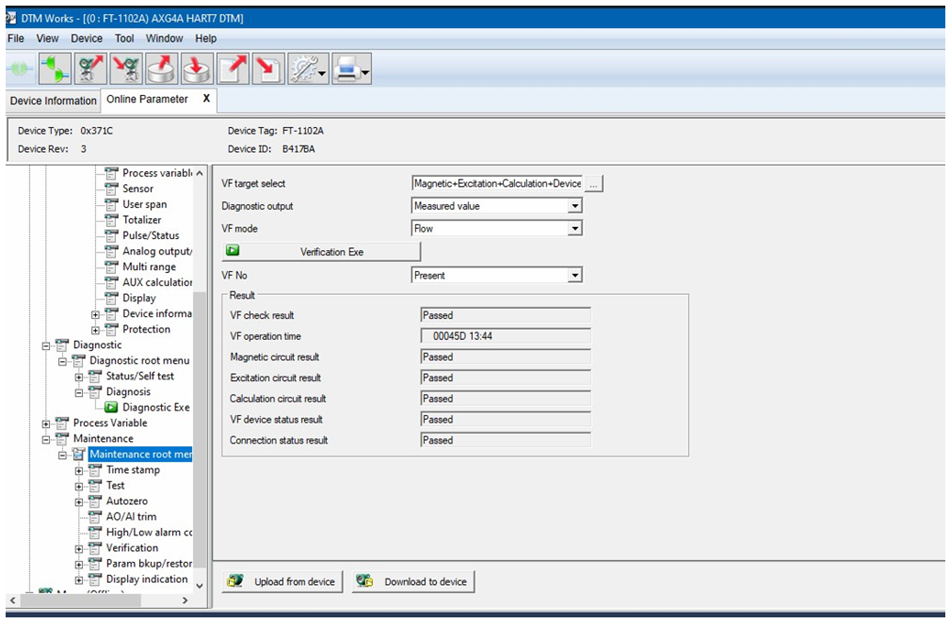
After using and evaluating the AXG magmeter thoroughly the client was extremely impressed with the performance, stability, and repeatability. The client was able to Optimize production throughput by running the Electrolyzer cell at optimum power and stable load.
The client placed an order for 3 additional AXG magmeters and will standardize all flow measurement points in the plant with Yokogawa Flowmeters. Most importantly the client appreciated Yokogawa's advice and expertise provided to solve their problem.
Yokogawa’s ADMAG AXG Magnetic Flowmeter has been many customer’s preferred choice globally, in Chloro-Alkali plants. Thousands of ADMAG flowmeters installed in chlor-alkali application are working exceptionally well delivering great measurement confidence to users.
Industries
-
Base Chemical
Yokogawa has been serving the bulk chemical market globally and is the recognized leader in this market. With products, solutions, and industry expertise, Yokogawa understands your market and production needs and will work with you to provide a reliable, and cost-effective solution through the lifecycle of your plant.
-
Chemical
Chemical plants rely on continuous and batch production processes, each posing different requirements for a control system. A continuous process calls for a robust and stable control system that will not fail and cause the shutdown of a production line, whereas the emphasis with a batch process is on having a control system that allows great flexibility in making adjustments to formulas, procedures, and the like. Both kinds of systems need to be managed in available quality history of product, and to be able to execute non-routine operations. With its extensive product portfolio, experienced systems engineers, and global sales and service network, Yokogawa has a solution for every plant process.
-
Chlor-Alkali
The rigorous demands of Chlor-alkali production require accurate, reliable instrumentation that provides all required measurements.
Related Products & Solutions
-
ADMAG AXG
Magnetic flowmeters for oil & gas, chemical, pulp & paper, food & beverage, and metal & mining applications
-
Flow Meters
Achieve precision flow measurement with field-proven sensor technology.
-
Magnetic Flow Meters
Achieve stable measurement and quick response times.