The ADMAG AXG Magnetic Flowmeter, used for brine and caustic flow measurement in electrolyzer cells at chloro-alkali plants, optimizes production throughput and reduces energy consumption by providing stable, repeatable, and accurate flow measurement.
Introduction
Considered one of the largest companies in Chlor-Alkali industries, specializing in the manufacturing of Caustic Soda, Chlorine, Hydrochloric Acid and Sodium Hypochlorite. The operating capacity is over 9 tons of Caustic Soda per day, Prized for using modern technologies that are environmentally friendly and preserve the health and safety of workers and community members, beyond coping with ongoing industrial developments that secure higher efficiency in operation and lower variable cost, the effort and need to ensure future sustainability is high.
Example: Flow area inside chemical processing facility
Application
In a Chloro-Alkali process, treated brine (NaCl) undergoes electrolysis, producing chlorine gas, hydrogen gas, and caustic soda (NaOH). A one liner introduction of a Chloro-Alkali process is, treated Brine Water (NaCl) is subjected to Electrolysis process, which yields, Chlorine Gas, Hydrogen Gas and Caustic(NaOH).
2NaCl + 2H2O → Cl2 + H2 + 2NaOH
The electrolyzer operates at 575 volts DC and 17.4 KA, resulting in high current flow in the process liquids, requiring non-conductive materials like GRP or plastic for piping. The overall efficiency of the electrolyzer depends on various factors, including the concentration, pH, temperature, and flow rate of the brine and caustic solutions, as well as the current and voltage applied.
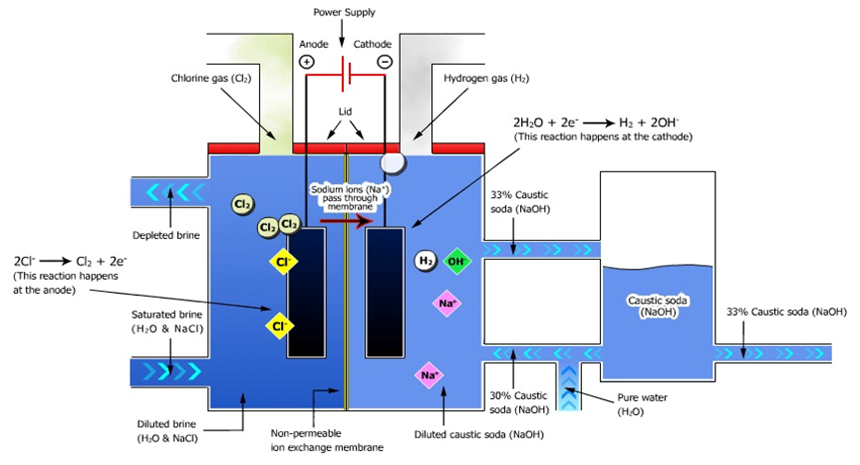
Challenges
Before adopting the ADMAG AXG, the plant used several magnetic and variable area flowmeters from other manufacturers, which resulted in unstable and inaccurate readings due to:
- High DC stray currents in the process liquid
- Magnetic interference from the electrolyzer cell
- Lack of expert support from the flowmeter suppliers
These issues caused mismatches between brine input and caustic production, raising concerns about electrolyzer efficiency and energy consumption. Low-frequency pulsed DC magmeters were particularly susceptible to noise and instability, while PTFE-lined models experienced leakage and electrode failures.
Solution
Yokogawa’s ADMAG AXG Magnetic Flowmeter was recommended to address the brine and caustic flow measurement challenges. The initial reluctance to use magnetic flowmeters was overcome through a detailed process study, leading to the installation of a pilot flowmeter. The study revealed high stray DC currents and magnetic field interference from the electrolyzer, which were mitigated by using ferromagnetic enclosures around the flowmeters.
After, The study of the process concluded that high DC Stray current was present in the NaOH line. There was a strong magnetic field radiating from the Electrolyzer cell interfering with the flowmeter electronics and generating additional noise. The necessary corrective action was suggested to the client and the AXG Magnetic flowmeters were installed on the Caustic and the Brine lines.
The AXG Magnetic flowmeter were shielded by means of iron (Ferromagnetic material) enclosures to isolate it from cells magnetic field effect generated by the Electrolyzer cells. Ferromagnetic material has good magnetic field permeability and are good magnetic field shielding material.
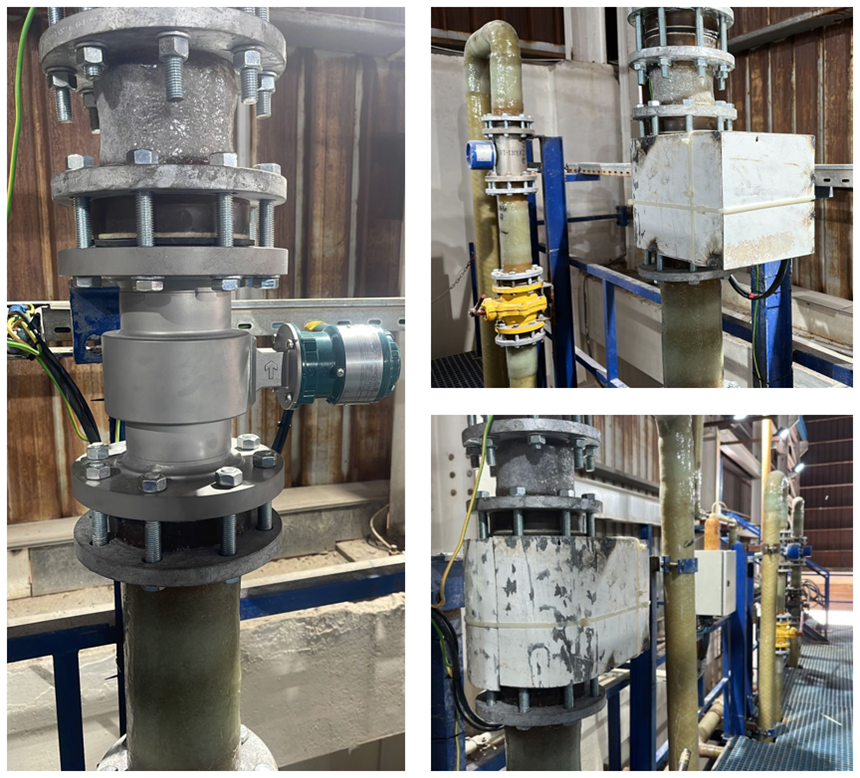
Initially the AXG showed some fluctuations, but not to the extent of competition magnetic flowmeters fluctuation. Thanks to the AXG’s unique Noise Level detection feature. We were getting Noise Level 3 (20 cm/s). It was instantly identified the grounding was done to the incorrect pit, having rectified the grounding to the correct pit, the Noise level dropped to Level 1 (5 cm/s).
The AXG with unique /ELC option to cut off DC noise present in the process fluid, worked phenomenally well with highly stable and accurate flow reading. The /ELC option cuts off the stray DC current noise present in the process fluid. This is achieved by a specialized capacitance circuit between the Detector and the Converter.
The Frequency of the Excitation signal fed to Electromagnet plays a key role in Magnetic Flowmeter’s measurement stability (noise rejection / cancellation).
Example: Online Parameter, focus on Flow noise result
Competitions magnetic flowmeters only operate on single excitation frequency, it will be either Low Frequency Pulsed DC (around 6 to 12Hz) or High Frequency Pulsed DC (around 30 to 50Hz).
Low Frequency Excited (6 Hz to 12 Hz) Magmeters suffer from Noise (electrode potential noise) caused by Slurry, Bubbles, Conductivity Fluctuations. Especially in Electrolyzer application for Brine and Caustic flow measurement, the effect of this unstable electrode potential noise is very pronounced which leads to high flow measurement fluctuations. This means a Low Frequency excitation magmeter will not be able to deliver stable and accurate flow measurement in such applications. On the other hand, High Frequency Excited (30 to 50Hz) Magmeters suffer from Poor Zero Stability.
Example: Noise Cut filter
Thanks to the Dual Frequency excitation of AXG to deliver stable zero and noise immunity. Yokogawa AXG’s patented Dual Frequency Excitation (6.25 and 75Hz simultaneously) is has the best Process Noise rejection and Zero Stability.
The inbuilt Meter Verification of AXG proved to be a very important feature to check the meter health in this harsh application. The inbuilt meter verification checks the following and inform the user a definitive Pass / Fail result.
- Magnetic Circuit
- Excitation Circuit
- Calculation Circuit
- Device Status
- Communication Status
Additionally, the meters Accuracy performance can be verified with the extended Meter Verification which can be performed using FieldMate and Yokogawa Magnetic flowmeter calibration kit, where a report is generated.
Example: Online Parameter, focus on Maintenance Root Metrics
After using and evaluating the AXG magmeter thoroughly the client was extremely impressed with the performance, stability and repeatability. This plant was able to optimize production throughput by running the Electrolyzer cell at optimum power and stable load.
The client placed order for 3 additional AXG magmeters and will standardize all flow measurement points in the plant with Yokogawa Flowmeters. Most importantly the client appreciated Yokogawa's advice and expertise provided to solve their problem.
Yokogawa’s ADMAG AXG Magnetic Flowmeter has been many customer’s preferred choice globally, in Chloro-Alkali plants. Thousands of ADMAG flowmeters installed in chloro-alkali application are working exceptionally well delivering great measurement confidence to users.
Key Benefits
- Dual Frequency Excitation: The AXG's patented dual frequency excitation (6.25 Hz and 75 Hz) provides excellent noise rejection and zero stability, outperforming competitors' single-frequency models.
- Noise Reduction: The /ELC option cuts off stray DC current noise, resulting in highly stable flow readings.
- Superior Performance in Challenging Environments: The AXG flowmeter offers robust performance in applications like electrolyzer processes where low-frequency excitation magmeters struggle.
- Inbuilt Meter Verification: The AXG’s inbuilt verification checks the health of critical components, including the magnetic circuit, excitation circuit, and communication status, providing a clear Pass/Fail result.
- Extended Verification: For more comprehensive accuracy checks, FieldMate and Yokogawa’s calibration kit can perform an extended verification and generate performance reports.
ADMAG AXG Magnetic Flow Meters
Yokogawa’s line of ADMAG AXG Magnetic Flow Meters are a high-quality and highly reliable magnetic flowmeter, enhanced by Yokogawa's proprietary dual frequency excitation method. Our electromagnetic flow meters feature enhanced settings for customized setups, pre-defined trend views, and multiple configuration sets for fast changeover through micro-SD card and comes standard with built-in verification, reducing total cost of ownership.
Related Industries
-
Chemical
Chemical plants rely on continuous and batch production processes, each posing different requirements for a control system. A continuous process calls for a robust and stable control system that will not fail and cause the shutdown of a production line, whereas the emphasis with a batch process is on having a control system that allows great flexibility in making adjustments to formulas, procedures, and the like. Both kinds of systems need to be managed in available quality history of product, and to be able to execute non-routine operations. With its extensive product portfolio, experienced systems engineers, and global sales and service network, Yokogawa has a solution for every plant process.
-
Base Chemical
Yokogawa has been serving the bulk chemical market globally and is the recognized leader in this market. With products, solutions, and industry expertise, Yokogawa understands your market and production needs and will work with you to provide a reliable, and cost-effective solution through the lifecycle of your plant.
-
Chlor-Alkali
The rigorous demands of Chlor-alkali production require accurate, reliable instrumentation that provides all required measurements.
Related Products & Solutions
-
ADMAG AXG
Magnetic flowmeters for oil & gas, chemical, pulp & paper, food & beverage, and metal & mining applications
-
Flow Meters
Achieve precision flow measurement with field-proven sensor technology.
-
Magnetic Flow Meters
Achieve stable measurement and quick response times.
Have Questions?
Contact a Yokogawa Expert to learn how we can help you solve your challenges.