To combat global warming, the production and consumption of biofuels is on the rise around the world. As a leading provider of measurement and control solutions to the chemical, oil, and other industries, Yokogawa has developed technologies that can be used to ensure the reliable and efficient production of bioethanol and other types of renewable fuels.
Challenges
Customer Challenge
Yokogawa has the tools and experience to build control and instrumentation solutions that provide tangible benefits to companies seeking to make use of renewable energy.
Fermentation management
The challenge
The temperature control settings must be adjusted for each kind of raw material.
Our solution
For fermentation management, Yokogawa makes it possible to select the optimal temperature control settings for a raw material from various presets.
Integrated management of batch and continuous processes
The challenge
To improve the efficiency of production operations that rely on both batch and continuous processes, consistency must be maintained in operating procedures.
Our solution
With Yokogawa’s integrated production control system, the operating method is the same for both batch and continuous processes. An intuitive human machine interface also helps operators work more efficiently.
Efficient loading
The challenge
Tank farm and truck loading operations must be carried out efficiently, and the quality of all products must be thoroughly checked before loading.
Our solution
Yokogawa enables integrated management by making it possible to link tank gauge and truck loading systems with the CENTUM integrated production control system. Furthermore, an online gas-chromatography measurement solution ensures thorough quality control.
Enabling Technology
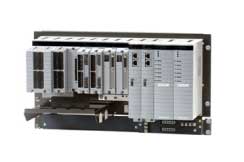
CENTUM VP Integrated Production Control System
The CENTUM VP integrated control system secures interruption-free “uptime only” plant performance for optimal productivity and profitability in the renewable energy field.
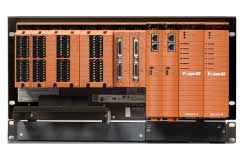
ProSafe-RS Safety Instrumented System
Yokogawa offers a full-lineup of safety instrumented systems, from solid-state and hard-wired types to fully integrated DCS-SIS types, covering all safety integrity levels (SIL 1 to 4).

STARDOM Network-based Control System
Dual redundant and low-power configurations are available for the STARDOM hybrid PLC/intelligent RTU. STARDOM supports HART, Modbus, FOUNDATION™ fieldbus, and other network protocols.
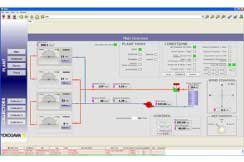
FAST/TOOLS SCADA
The FAST/TOOLS package optimizes performance for renewable energy applications. It ensures high availability and performance and supports online configuration.
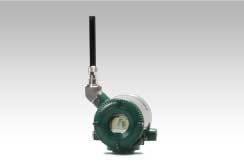
YTA Series Temperature Transmitters
YTA series temperature transmitters convert sensor inputs to a 4 to 20 mA, HART, or FOUNDATION™ fieldbus signal; this eliminates the drawbacks of wire resistance and signal noise that are often experienced with conventional temperature instruments.
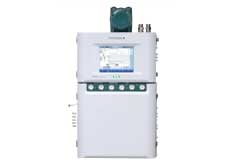
GC8000 Process Gas Chromatograph
The GC8000 sets a new standard for process gas chromatographs. It has multiple ovens, greatly expanding its capabilities. The GC8000 also brings a number of other important innovations, from an innovative 12-inch color touch screen HMI to powerful predictive diagnostics.
Details
Bioethanol Process
The production of bioethanol from agricultural feedstocks (raw materials) is roughly divided into the following steps: cultivation, fermentation, distillation, dehydration, storage, and loading. First, a raw material is transferred to a preparation tank, where it is diluted with warm water. Then, it is put into fermentation tanks, where molasses and yeast are mixed in to ferment the sugars present in the raw material. The fermented mash is moved to a mash column to increase the ethanol concentration, then moved to a distillation column where the alcohol content is increased to 95 volume percent. In the dehydration process, water is removed to bring the alcohol content to at least 99.5 volume percent so that the ethanol can be used as a fuel additive.
Processes:
Cultivation and Fermentation
- Yeast tank/fermentation tank temperature control
- Fermentation management
- Cleaning-in-place management
- Fermentation liquor sugar content measurement
Distillation and Dehydration
Distillation
- Feed flow control
- Discharge flow control
- Reflux flow control
- Drum level control
- Bottom liquid level control
- Column temperature control
Dehydrator
- Dehydrator operation management
Storage and Loading
- Truck loading control
- Tank inventory management
- Moisture content measurement
- Impurity measurement (e.g. methanol)
Control and Measurement Technologies
Information
- Operation support
- Operation training
- Plant asset management
Control
- Integrated monitoring and control
- Safety instrumentation
Measurement
- Flow rate
- Pressure
- Liquid level
- Temperature
- pH
- Conductivity
Resources
- CENTUM CS 3000 distributed control system to control the ethanol plant and it's utility boilers
- Batch processes that require careful automated control for maximum efficiency and product quality
- CENTUM VP Batch package improves productivity.
- Reduction of operator workload and safe operation.
- Yokogawa provides STARDOM and FAST/TOOLS for biomass pilot plant.
- FAST/TOOLS is an "all in one" SCADA solution that functionsa a data historian.
- As the main automation contractor (MAC) for this plant construction project, Yokogawa Brazil engineered, installed, and commissioned an integrated control and instrumentation solution
- Yokogawa Brazil completed the commissioning of these systems ahead of schedule and the production of green polymer was started just one week later
This introduces a system that uses Ethernet communications to acquire measured values, target values, and control output values from a controller installed on site into a PLC at high speed (ten units' worth within one second).
The worlds of process automation and production management have been converging for some time. What once used to be islands of automation and production management functionality connected through highly proprietary integration schemes that were costly to maintain have developed into integrated platforms that provide seamless data exchange between the world of automation and the plant floor, the functions of production and operations management, and integration with business level systems.
The automation suppliers that will be successful in the long term will be those that effectively address application or industry specific problems for end users with a value proposition that cannot be ignored. These problems exist throughout the process industries today, and they won't be solved by simply offering a product, but through a combination of hardware, software, services, application expertise, and knowledge.
In ARC's view, customers need a compelling business value proposition to justify investment in any kind of automation. Vigilance and VigilantPlant were created with this in mind. Yokogawa's vision with VigilantPlant is to create an environment where plant personnel and operators are well informed, alert, and ready to take action.
Yokogawa has come a long way in making its message clear to the world of process automation. Last year, the company embarked on a full-scale global marketing campaign to make customers aware of the company's focus on system reliability, security, dependability, and robustness. Dubbed "Vigilance", the campaign created a unified message for the company and greatly helped expand awareness of the Yokogawa brand and corporate philosophy.
Process automation end users are under more pressure than ever to do more with less. The current economic climate means that many automation capital projects are on hold. With capital budgets tighter than ever, users instead focus on operational budgets (where cost cutting is also a key concern), or on automation investments with a very rapid return on investment.
In today's dynamic industrial marketplace, the only constant is change. Raw material costs, energy costs, market demands, environmental and safety regulations, technology, and even the nature of the labor force itself are constantly changing, and not always in predictable directions.
Downloads
Videos
How much do you know about pressure transmitters? Are you accurately, quickly and reliably measuring pressure? Ultimately, the drive of any good pressure transmitter is to get an accurate, reliable pressure measurement to the data user quickly. This video gives you the answers to your basic questions about pressure and pressure transmitters.
Sample systems are a crucial component of and have a significant impact on the performance of a process gas chromatograph analyzer. When working on sample systems, you must have a constant awareness of time delays. This fundamentals webinar will take the mystery out of lag times.
Looking for more information on our people, technology and solutions?
Contact Us