Path to Prosperity
The increasing demand for petrochemical goods, coupled with the quest for cleaner energy sources, contributes to the surge in methanol demand. Yokogawa experts co-innovate with methanol producers come to market well positioned with our deep understanding of what profitable methanol production entails – low cost of feedstock, high energy requirements for steam reforming, high pressure for cooling, compression for catalytic reaction, and distillation for purification of methanol to allow best conditions for optimum production outcomes.
We provide solutions that enhance safety, ensure accurate and reliable operation, and increase plant efficiency across every facet of your production activities. As a key element of this crucial industrial process, water retention/discharge, and the smart management of it, can influence both process efficiency and sustainability results.
Discover how Yokogawa devices are used.
Yokogawa stands ready to meet the exponential rise in demand for methanol across various industries. Our advanced automation solutions provide seamless integration and lifecycle optimization for manufacturers of methanol products, from traditional chemicals to energy-related applications and gasoline blending. By leveraging our expertise, you can enhance operational efficiency, ensure safety, and optimize production to stay competitive in a rapidly growing market.
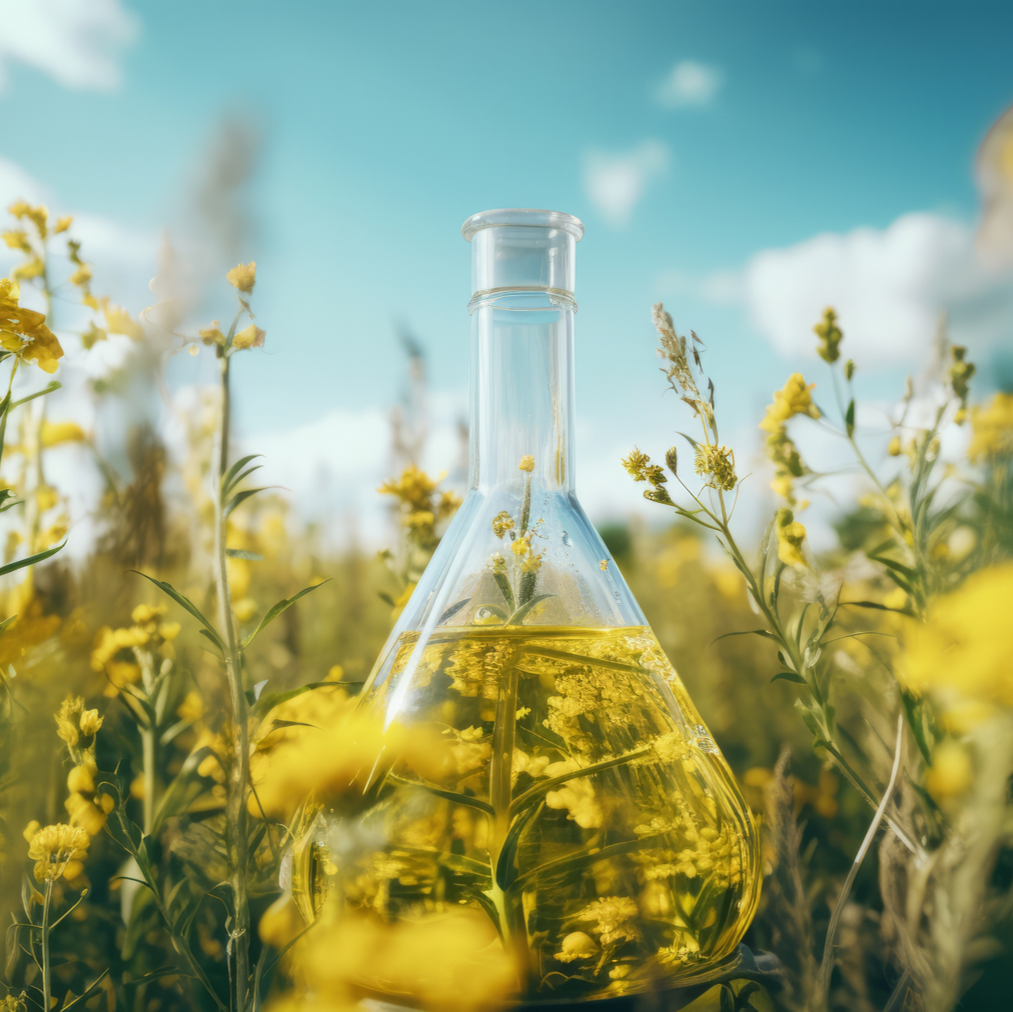
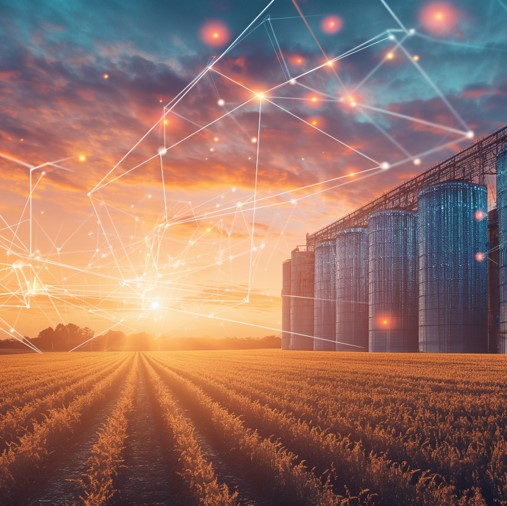
As a global commodity chemical, methanol plays a crucial role in the housing, automotive, and energy industries. Yokogawa’s automation solutions are designed to support methanol manufacturers facing the challenges of high energy costs, inflation, and geopolitical uncertainty. Our technology enables plant-wide integration, helping you streamline operations, improve safety, and reduce environmental impact, ensuring your production remains resilient and future-ready.
Industry Issues. Yokogawa Works.
Market Demand and Predictability Uncertainty The demand for methanol is influenced by various sectors, including chemicals, fuels, and materials. Market dynamics, competition, and shifts in demand patterns impact the industry’s growth and stability. Working to improve leak detection, enhance process management to decrease energy usage and minimize or capture carbon emissions, upgrade equipment and technology to optimize methanol production will solve these issues. |
Feedstock Availability and Shipping Disruptions The availability and cost of feedstocks (such as natural gas, coal, or biomass) directly impact methanol production. Fluctuations in feedstock prices can affect profitability. Shipping disruptions and delays are impacting many commodities, including methanol. These disruptions include delayed shipping times, increasing freight rates, and low vessel availability. Each region is navigating unique circumstances based on trade flows and preferred shipping routes. |
Transition to Low-Carbon Methanol Stricter environmental regulations and emissions standards are influencing methanol production and consumption. Companies are adapting to reduce pollutants and greenhouse gas emissions. The methanol industry is witnessing a wave of announcements related to low-carbon, ultra-low carbon, bio, and e-methanol production. Efforts are being made to reduce carbon intensity and explore alternative feedstocks for methanol production |
Technological Advancements Innovations in methanol synthesis, catalysts, and process efficiency play a crucial role. Research and development efforts focus on improving production methods and reducing energy consumption. |
Details
Optimum outcomes for methanol
Total Insight instrumentation solutions for methanol plant applications from start to finish
![]() |
Methanol: Stabilization of Process and Improvement of Operation through Process Data AnalysisDiscover how a process data analytics will improve operator awareness from simply being mechanically conscious of process conditions, but to adopt a more analytical approach in understanding the sequence of steps in a process and what happens over time with that process.. The impact on safety and productivity this methanol and ammonia producer experienced in control operations throughout this facility has helped to reduce operator workload and stabilize processes. Discovering root causes, performing difficult calculations, spotting potential issues and taking preemptive actions before something goes wrong has become invaluable. Their future is predictable, adaptable and sustainable! < Explore how Yokogawa uses analysis to find and solve process fluctuation factors |
![]() |
![]() |
![]() |
![]() |
MAC Approach Speeds Automation Revamp at Mothballed Methanol/Ammonia Plant |
Production Management and Optimization Solutions for Methane Chloride Plant |
Methanol Applications
Yokogawa helps manufacturers of methanol products such as traditional chemicals and fuels use automation solutions that enable plant-wide integration and lifecycle optimization. Here is a quick list of applications for which Yokogawa has a global network of experts at your service, providing comprehensive automation solutions for the methanol process to produce hundreds of everyday products, including plastics, paints, car parts and construction materials and clean energy resource used to fuel cars, trucks, buses, ships, fuel cells, boilers and cook stoves. This list is just a few of the thousands of products and fuels made with methanol.
Derivative Chemicals
- Acetic Acid
- Fleece
- Adhesives
- Paints
- Vinegar
- Textiles
- Pharmaceuticals (Vitamins, streptomycin, hormones, cholesterol drugs)
- Methyl Methacrylate (MMA)
- PMMA-LCD Screens
- Automotive Manufacturing (clean fuels, paints, polyester carpet, polyester fabric, thermoset bumper and energy absorber, light lens, tire core adhesives, body panels, MDF/MDI door panels, safety glass laminate, polyurethane dashboard foam, acetyl thermoplastics: gears, pumps, moldings, compounds, distributer caps, fuses)
- Silicone
- Sealants
- Lubricants
- Medical Equipment (gloves, masks, medical gowns, caps, aprons, pharmaceutical drugs, disinfectants)
Insulation
- Olefins
Caustic soda
- Marine fuel
- Camping and boating stove fuel
- Gasoline blending/substitute
- Diesel blending/substitute
- Bio-diesel production
- Methyl tert-butyl ether (MTBE)
- Dimethyl-ether (Displacing LPG)
Aerosols
- Disinfectants
- Fragrances (air fresheners)
Solvents
- Paint Varnishes
- Shellac
- Brake parts cleaner
- Antifreeze
- Windshield washer fluid
- Adhesives
- Resins
- Inks
Resources
Optimizing the maintenance cycle is not always straightforward. In some cases, cleaning once a week is sufficient and other processes may require every 8 hours.
Select the correct pH glass and reference type to improve your pH sensor lifetime and you can limit or even eliminate the effects of temperature and pressure on especially the reference sensor.
Kind of. Calibration itself will not extend the life of a sensor, however, a sensor that is not calibrated properly can cause unreliable measurements - that are often misdiagnosed leading to unnecessary replacements.
Learning these four lessons will help you improve your engineering skills and most importantly extend the life of your pH sensors.
The lifetime of a pH sensor has a significant impact on the overall annual costs of a pH measuring loop. Optimizing four key factors will decrease these costs and optimize process control and overall plant efficiency.
Downloads
Brochures
- Chemical Industry Solutions (986 KB)
- Success Story Collection Chemical (Base Chemical, Fertilizer, Petrochemical) (7.6 MB)
- Electrolysis Solutions: Instrumentation Solutions for Electrolysis Plant Applications (841 KB)
- TDLS8220 LOC (Limiting Oxygen Concentration) Infographic
- Extractive Tunable Diode Laser Spectrometer TDLS8220 (5.6 MB)
- CENTUM VP DCS Top 10 Features Infographic (231 KB)
- Pre-Engineered Solutions for Moisture in Chlorine (650 KB)
- Yokogawa Corporation of America Corporate Overview - Products & Solutions (3.5 MB)
- Solutions for the Chemical Operations Executive (1.2 MB)
- Improved Combustion Efficiency and Safety with TDLS Measurements (526 KB)
- Overcome Temperature Effects for DP Level (778 KB)
Instruction Manuals
Videos
ROTAMASS is the integral and remote type Coriolis Mass Flow Meter. Both types have highly refined digital signal processing electronics, so that accurate and stable mass flow measurement is achieved.
It is the most technologically advanced mass flow meter yet. By combining the superior design of the application specific flow sensor and transmitters with the Total Insight philosophy and functionality, the flexibility of the ROTAMASS to adapt to changing requirements guarantees performance throughout the lifecycle of the process measurement.
Watch the film by KBC who are supporting their clients in their efforts to address climate change and sustainability.
Looking for more information on our people, technology and solutions?
Contact Us