Executive Summary
Integrated CENTUM VP and ProSafe-RS
Systems Ensure Nonstop Operation of
ADU/DKU Processes
Integrated Refinery & Petrochemical Complex Public Co., Ltd. (IRPC) is an integrated producer of petrochemical products. Its complex consists of an upstream oil refinery and a downstream petrochemical plant. The oil refinery has a total capacity of 215,000 barrels per day, accounting for 21% of the country's total refining capacity.
Without the products from the refinery's atmospheric distillation unit (ADU) and diesel kerosene unit (DKU), operations at IRPC's downstream petrochemical plant would come to a halt. It is therefore absolutely essential for these units to operate nonstop, 24/7/365, with no unscheduled shutdowns.
The ADU and DKU each had a legacy production control system (PCS), with the former relying on a system from ABB and the latter using a Rosemount RS3 PCS. Both of these control systems could be operated from the same control room. The safety system was an A&B PLC.
Due to part supply difficulties and the discontinuance of vendor support, IRPC decided to replace these legacy systems with the latest systems technology. For this revamping project, Yokogawa Thailand successfully integrated the CENTUM VP PCS with the ProSafe-RS safety instrumented system (SIS), Plant Resource Manager (PRM) asset management package, and Exaplog event analysis package. In the control room, two large screens now display the status of processes throughout the plants and key process control trend data. The central control room is quiet and well managed.
Somnuk Boonprasert, IRPC's instrument supervisor, in the central
The Challenges and the Solutions
Challenge 1: Application of new technology to improve efficiency
There were two different production control systems side by side in one control room. Procedures for operating them were different, they did not use the same reporting format, and the engineering was also different. With CENTUM VP's new ergonomically designed human machine interface (HMI), information access became quicker and more intuitive, with operators being able to see lots of different process information at a glance and handle any situation seamlessly. By improving operator efficiency, it became possible to reduce the number of control room personnel.
Challenge 2: Nonstop and safe operationThe nonstop supply of products from the ADU and DKU processes to the downstream plant was essential, so unscheduled shutdowns needed to be eliminated. As the CENTUM VP and ProSafe-RS systems each have processor cards with dual redundant CPUs, they achieve high availability and are highly reliable. Since the installation of these integrated control systems, operations have been able to continue nonstop with no major failures to the present day.
The integration of ProSafe-RS with CENTUM VP makes it possible to monitor all instrument blocks from the CENTUM VP HMI. The operation procedures for ADU and DKU are all the same now, eliminating operator confusion and bringing a higher level of safety.
If a problem occurs with the ProSafe-RS system, a sequence of event recorder (SOER) function that captures and stores time-stamped event data makes it possible to analyze what happened and make improvements to the plant operations.
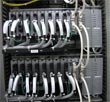
CENTUM
field control station (FCS)
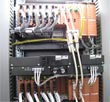
ProSafe-RS
safety controller
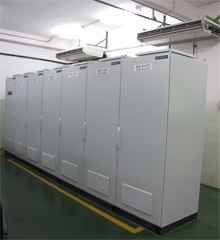
Rack room: clean and neat
Customer Satisfaction
Mr. Somnuk said, "We are happy using Yokogawa's systems because we have not had any major problems with them. The plant is easier to operate with the new CENTUM VP HMI." He continued by saying, "This is a real VigilantPlant! We will continue to improve our production efficiency"
產業別
-
石油和天然氣下游
近年來,石油和天然氣下游產業面臨著越來越多的挑戰。這些挑戰包括待加工原料的特性變化、工業設施及設備的老化、能源成本的上升、缺乏能夠使煉油廠安全有效運行的熟練技術工人,以及市場和客戶的需求不斷變化。
多年來,橫河與許多下游公司合作,致力於提供應對這些挑戰和問題的工業解決方案。橫河的解決方案幫助工廠投資者盡可能實現最大的盈利能力和工廠內可持續的安全。 -
精煉
在不斷變化的市場中,煉油廠不僅是原油加工單位,而且是利潤中心。同時,人們強烈意識到煉油廠設施安全性的重要。為了實現盈利,效率及環境保護的長期目標,需要包括計劃,調度,管理和控制的總體生產解決方案。憑藉在自動化領域多年積累的專業知識,橫河可以為您提供經濟實惠的完善的整體解決方案,改善操作並使世界更清潔。
相關產品&解決方案
-
CENTUM VP
CENTUM VP具有簡單而通用的架構,由人機界面、現場控制站和控制網絡構成。
-
分散式控制系統(DCS)
我們的分散式控制系統 (DCS) 可自動化和控制製程,提高績效。 已經超過 10,000 家工廠利用Yokogawa DCS 實現生產目標。