Abstract
Ultrapure Water (UPW), Water for Injection (WFI), High-purity Water and Deionized (DI) are all terms describing basically the same property. They refer to water which has been purified to the highest standards by removing all contaminants such as organic and inorganic compounds; dissolved and particulate matter; volatile and non-volatile, reactive and inert; hydrophilic and hydrophobic; and dissolved gases. The purified water has very low conductivity which means it is high in resistance because all the conductive components have been removed. Combined with susceptibility to contamination and temperature effects, low-conductive solutions make accurate pH measurement very difficult to achieve. Achieving accurate and reliable readings using a traditional pH analyzer is challenging. However, by understanding what causes the difficulties in pH measurements and having the proper equipment, stable and accurate pure water pH measurement can be accomplished.
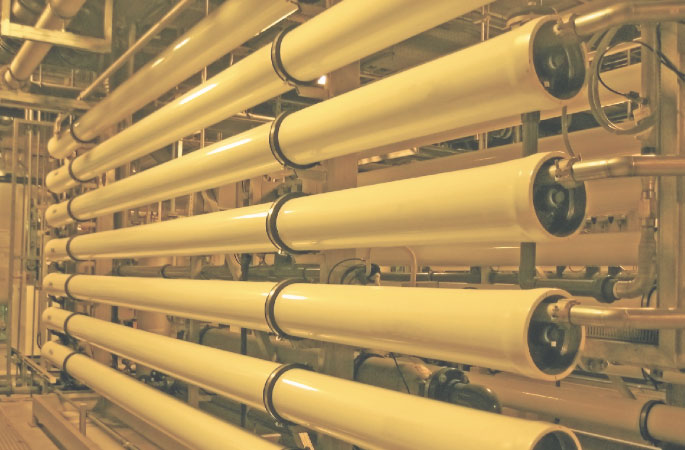
Introduction
What is Pure Water?
Over the years, organizations such as the American Society for Testing and Materials (ASTM), Electric Power Research Institute (EPRI), the Food and Drug Administration (FDA) and the Environmental Protection Agency (EPA) have all developed water quality guidelines and standards. The extent of purification needed depends on its use and the quality of raw water. Ultrapure Water (UPW), Water for Injection (WFI), High-purity Water and Deionized (DI) are all terms describing basically the same property. They refer to water which has been purified to the highest standards by removing all contaminants such as organic and i norganic compounds; dissolved and particulate matter; volatile and non-volatile, reactive and inert; hydrophilic and hydrophobic; and dissolved gases. The purified water has very low conductivity which means it is high in resistance because all the conductive components have been removed. Combined with susceptibility to contamination and temperature effects, low-conductive solutions make accurate pH measurement very difficult to achieve.
How is Pure Water Made?
Processes requiring pure water must continually replace the water being consumed. Sources of replacement water are usually local supplies from a river or lake and therefore require pre-treatment and purification before it can be used in the process. The most commonly seen treatment stages within a water purifying process are water clarifiers, filters (depth/carbon), membrane separation (reverse osmosis), primary demineralizer (ion exchanger), storage tanks, polishing demineralizer (polisher), ultraviolet sterilizer and submicron filter. No matter the location a step may reside within a water purifying process, it performs that same function.
The schematic below is an example of pure water production within a power plant. Typically after preliminary purification, which may include filtration, clarification and softening further downstream, a two-pass reverse osmosis system and demineralization operations are employed to further purify the water.
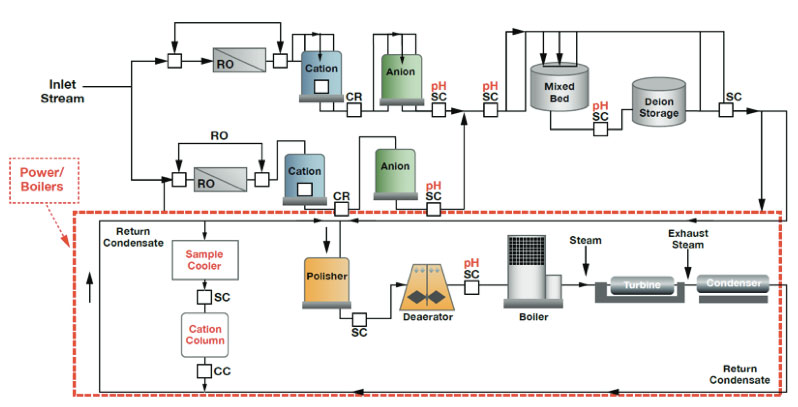
Figure 1: Power Plant
Stages in Water Purification
1. Clarifier - There are different types of clarifiers (i.e. circular, horizontal, and vertical) available on the market. The primary function is the same: clarifiers remove solid particulates or suspended solids. Depending on the raw water condition, there could be a single clarifier or multiple clarifiers. Raw water is pre-screened to remove large objects and grit before entering the primary clarifier. The primary clarifier tank is responsible for producing a homogeneous liquid that is capable of being treated biologically and allows for sludge removal that can be treated or processed separately. Coagulation and flocculation reagents are added to the water to remove suspended solids before the effluent is processed through a secondary clarifier.
Within the secondary clarifier, the newly formed clumps of suspended solids are called flocs. The flocs then settle and can be easily removed. Overfeeding or underfeeding the coagulation/flocculation injects can have downstream RO membrane and particulate fouling. Sometimes there is a clarifier that combines the functions of chemical treatment, mixing, flocculation, and sedimentation. This type of clarifier may be used for lime softening as well. Lime softening is used to remove the total hardness of the water that is associated with alkalinity. Incorrect lime addition can result in a higher scaling potential in the downstream RO units.
2-3. Filters - After the effluent passes through the clarifiers, it enters a filtration media. The most common are sand filters or a dual media filter. These filters remove the majority of particulates. Proper care and maintenance has to be taken with the flow to ensure removal of the particulates from the filter.
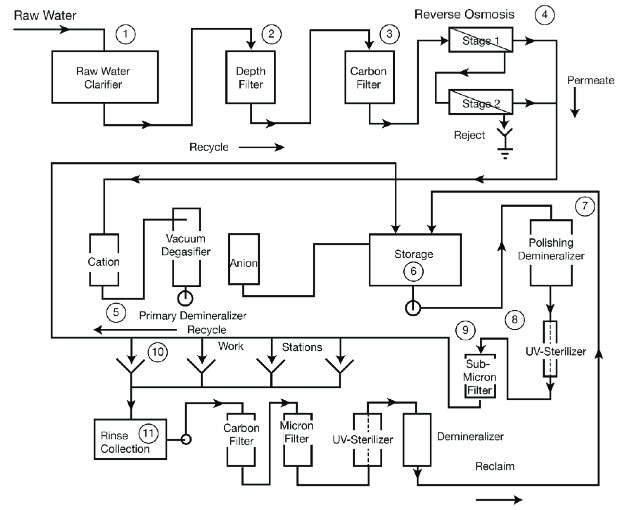
Figure 2
Figure 3: Examples of Common Filters
4. Reverse Osmosis - Osmosis is the natural tendency of a fluid, usually water, to pass through a semipermeable membrane from a less concentrated solution into a more concentrated one, thus equalizing the concentrations on each side of the membrane. Reverse osmosis is often used in commercial and residential water filtration. It is also one of the methods used to desalinate seawater. Sometimes reverse osmosis is used to purify liquids in which water is an undesirable impurity (e.g., ethanol).
![]() |
Figure 4 |
Reverse osmosis (RO), also known as hyper-filtration, is a separation process that uses pressure to force a solution through a membrane that retains the solute on one side and allows the pure solvent to pass to the other side. In reverse osmosis (RO), pressure must be exerted on the side with the concentrated solution to force the water molecules across the semi-permeable membrane to the fresh (pure) water side. To illustrate, imagine a semipermeable membrane with fresh water on one side and a concentrated aqueous solution on the other side. If normal osmosis takes place, the fresh water will cross the membrane to dilute the concentrated solution. In reverse osmosis, pressure is exerted on the side with the concentrated solution to force the water molecules across the membrane to the fresh water side.
This semi-permeable membrane inhibits the majority of dissolved impurities from passing through to the pure water side. The amount of impurities carried over depends on the type and condition of the membrane (i.e. age, cleanliness) and the amount of pressure (energy) applied to the process.
Not all the feedwater passes through the membrane. Some is diverted to flow over the membrane to cleanse away the rejected impurities in a cross-flow filtration mode.
The RO system produces one purified water stream called permeate and a second stream called concentrate, brine, or reject. Feedwater enters the machine at fairly low pressure and flows through pre-filters to remove suspended particles, such as silt. Pre-filters are typically a replaceable cartridge type which provides a cost effective method for keeping the membrane clean. Typical life expectancy for these membranes is approximately three years.
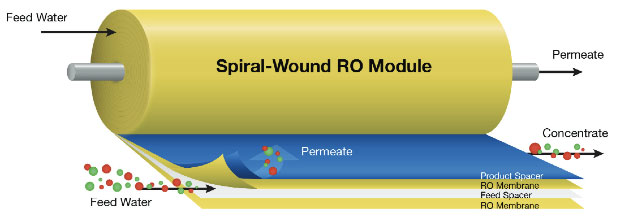
Figure 5
RO systems are designed for automatic operation and require routine preventative and corrective maintenance. Common problems include membrane fouling and the use of improper flow rates. The result is reduced throughput capacity and shortened runs.
Membranes can fail altogether, resulting in excessive demand on downstream purification systems and poor quality product water.
Both pH and conductivity measurements are used to safeguard the successful operation of an RO system.
Some types of RO membranes are sensitive to feed water pH and can become damaged if the pH is outside the recommended range of 5 to 8 pH. A pH sensor upstream of the membrane can provide a feedback signal to control dosing of acidic or basic reagent to maintain the pH within acceptable limits.
Conductivity measurements are used at both the inlet and outlet of the RO unit to determine whether the total dissolved solids are being filtered effectively.
In pure water applications, a two-pass RO system is typically installed upstream of the demineralizer. Its performance is pH dependent with the second-pass section most dramatically affected. While these changes are not significant in the majority of applications, variations become crucial to the success of high-purity water processing.
In addition, the effect of minor feedwater constituents, such as alkalinity and ammonia, also play a role in achieving high-purity permeate.
The overall efficiency of dissolved solids removal is usually determined utilizing a pair of conductivity measurements, one at the inlet (cell 1) and one at the outlet (cell 2). This is referred to as % rejection and calculated by the formula:
% rejection = [1-(cell2)/(cell 1)] x 100
For example, if the inlet water had 200 ppm of dissolved solids and the outlet water had 10 ppm, the efficiency would be 95% rejection rate. A typical range for this type of application is 80% - 100% rejection.
A final conductivity measurement after the second stage is often used to determine the absolute quality of the outlet water.
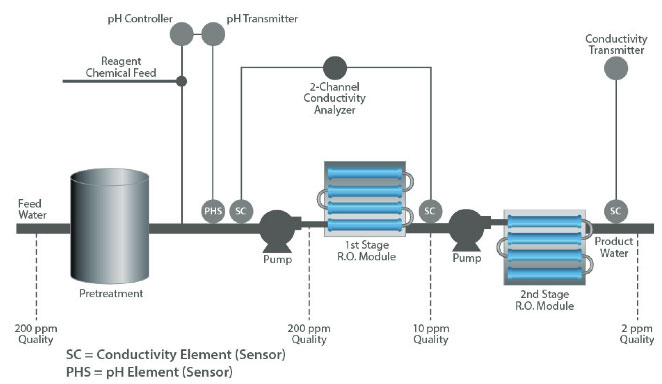
Figure 6
Ammonia also affects the production of high purity water and may be present due to municipal chlorination of feedwater or from organic contamination. Ammonia (NH3) will pass through the membrane system in either the molecular or ionic (NH4+) form. Ammonium hydroxide is less conductive than ammonium carbonate [(NH4)2CO3] so it is not uncommon to find off-line samples or storage tank water with conductivity higher than that of on-line readings. The pH values will be lower. This shift in pH is due to absorption of CO2 from the air and the formation of carbonic acid in the water. Without the presence of ammonia, this type of contamination of high-purity water with CO2 would generate higher conductivity as well as the reduced pH.
![]() |
Figure 7 |
5. Demineralizer - Typically after the water passes through the RO system it will also pass through a demineralizer or ion exchanger. Deionization is a process that removes dissolved ionic material from water for purification. Deionization takes place in an ion exchange unit, which usually consists of a cation bed, an anion bed and a mixed bed in series. The mixed bed, also referred to as a polisher, contains both cation and anion resins and provides the highest ion removal efficiency.
The cation bed is used to remove positively charged ions such as calcium, magnesium and sodium, while the anion bed removes negative ions such as sulfate and chloride. Specific resins are chosen to optimize bed performance, depending upon the water composition to be purified.
Ion exchange resins come from a wide variety of organic and synthetic materials containing positively or negatively charged sites which attract ions of opposite charge from the surrounding solution. The resins commonly consist of a styrene-divinylbenzene copolymer. The electrically charged groups are commonly sulfonic or carboxylic acid salts or quaternary ammonium salts. Polymers containing acid groups are classified as anion or cation exchangers because they exchange positively charged ions, such as hydrogen ions and metal ions.
Ion exchange resins are light and porous solids usually prepared in the form of granules, beads, or sheets. When immersed in solution, the resins absorb the solution and swell. In industrial and domestic applications, ion exchange resins are used for the removal of calcium, magnesium, iron and manganese salts from water (water softening), for the purification of sugar, as well as for concentrations of valuable elements such as, gold, silver, and uranium.
![]() |
Figure 8 |
Anion exchange materials are classified as either weak base or strong base depending on the type of exchange group. The weak base resins act as acid absorbers, efficiently removing strong acids such as sulfuric and hydrochloric. They are used in systems where strong acids predominate, where silica reduction is not required, and where carbon dioxide is removed in degasifiers. Preceding strong base units in demineralizing processes, weak base resins give a more economical removal of sulfates and chlorides.
Cation exchanger materials consist of inorganic zeolites, natural (greensand) or synthetics. Sulfonated coal, styrene-base resins, phenolic resins and acrylic resins are some that have been developed. Weakly acidic cation exchange resins contain carboxylic and phenolic groups. They remove alkalinity by exchanging their hydrogen ions for the cations associated with the bicarbonate ion (calcium, magnesium, and sodium bicarbonates). Being weakly acidic, they will not affect the cations associated with the anions of strong acids.
![]() |
Figure 9: Mixed |
7. Polisher - A polisher mixed-bed ion exchanger, but could be an RO unit or an evaporator. It is used as the final stage.
8. Ultraviolet Sterilizer - UV Irradiation destroys microbes that may have entered the water supply and survived earlier treatment stages. UV radiation oxidizes organic matter producing carbon dioxide.
9. Submicron Filter - A submicron filter removes the microbes destroyed by the UV light.
Why Do We Measure pH in Pure Water?
Pure water is used in a variety of industrial processes. Understanding why pH is being measured and its level of importance in the overall process is key.
- A primary purpose of measuring pH is its quick response to the ingress process contamination during production and distribution of pure water. Gaseous contaminants like air or carbon di-oxide, or the exhaustion of resin beds are the main sources of the contamination. The measurement of pure water can help to ensure that the water being used remains as pure as possible for the application.
- For demineralization applications, the resin beds can be either cationic or anionic. An increase in pH results from cationic bed exhaustion, whereas anionic bed exhaustion leads to a decrease in pH value.
- Reverse osmosis systems' overall performance is pH sensitive.
- Most industrial plants use high pressure boilers to generate steam from pure water. Impurities in the water will increase scaling of boiler tubes and carryover of impurities in steam, which will further reduce the boiler efficiency and damage the equipment. Corrosion can occur when pH exceeds recommended limits at ranges that are dependent on metallurgies with the steam cycle.
- Pure water is an essential factor in the pharmaceutical industry as well. It is necessary for the production of a variety of products such as those in the semiconductor industry.
Where Do We Normally Find Pure Water Measurements?
In the production and use of pure water, pH must be measured at various points. Examples of some of the measurement points are as follows:
- Preparation point - pH measurement at this beginning point validates that the desired purity has been produced and with sufficient quantity.
- RO systems - RO systems' performance is pH sensitive. pH determines the performance of the RO membranes. Membrane separation efficiency is affected by feedwater chemistry. Chemistry takes the dominant role when the desired product is high-purity water and the benchmark is conductivity. Dissolved gases, such as carbon dioxide (CO2), can dramatically affect permeate conductivity and RO systems cannot effectively deal with these gases by themselves. In the specific case of CO2, it is possible to force a conversion to bicarbonate (HCO3) and carbonate (CO3-2) ions by raising the feedwater pH. These ions are well rejected by PA (RO) membranes whereas CO2 (and carbonic acid) are not rejected at all.
By controlling the pH of the feed solution, a portion of the CO2 present can be shifted to HCO3 and/or CO3-2 depending on the pH level reached. These pH adjustments permit up to 98% of bicarbonate and arbonate being removed in the first pass of a two-pass system. Sometimes it is not possible to elevate the pH of the feedwater. The same objective (removal of some of the feedwater alkalinity and CO2) can be reached by the use of a degasifier. The degasifier can be located ahead of the first RO machine or between the two passes. Should some alkalinity pass into the RO permeate, it will re-equilibrate, forming H2CO3, HCO3 and/or CO3-2 in proportion to the pH.
- Demineralizers - pH measurement after the demineralizer is necessary to ensure that the chemical treatment is working effectively. At this point, the water has almost no electrolytic conductivity, making the measurement of pH difficult.
- Distribution system - This confirms no impurities have been injected by the distribution system which could hamper the process.
- Usage Point - pH measurement here further confirms the water is of the required purity.
- Apart from these points, wherever steam is generated, other pH measurement points include; after water treatment, condensate pump discharge, after condensate polishing units, boiler feedwater, etc.
What Are Some of the Difficulties with Pure Water pH Measurements?
The low conductivity and limited buffering capacity of low ionic strength pure water causes pH electrodes to drift, producing non-reproducible and inaccurate results. The common problems are large drift, unacceptable flow sensitivity and poor temperature compensation. Electrical noise and interference complicate matters further. Certain properties of pure water adversely affect the ability to obtain a reliable pH measurement. For many years it was believed that these properties could not be satisfactorily overcome in order to achieve the desired measurement accuracy and reliability. The areas most affected by the pure water properties include:
- Reference Electrode Stability
- Glass Electrode Response
- Electrical Noise
- Special T.C. Requirements
Process Contamination and Reference Junction Potential
A potential is developed at the reference junction when two different solutions come in contact with each other. This is called diffusion gradient. The reason for this unwanted gradient is transfer of ions at different rates because of flow variations. This may cause unstable reference potential and anomalous pH measurement. Process contamination can also generate these errors in pH measurement.
The liquid junction of the reference electrode tends to develop an appreciable diffusion potential as a result of the extremely large differences in concentration of ions between the process and the fill solution of the reference electrode.
The resulting junction potential can be as high as 20-40 millivolts (approximately 0.5 pH). Any change in this potential will show up as an erratic, drifting pH value.
It will appear that there is a change in the process pH, but this change is false since it is caused by the junction potential. Depletion or dilution of the reference fill solution occurs much more rapidly in high purity water, causing the reference potential to become unstable and the measurement unreliable.
Since there are no conductive ions to speak of in high purity water, a physical path of conductive reference solution from the reference electrode to the glass electrode must be established in order for the measurement circuit to be complete. If there are no ions provided from the reference electrode (they have been depleted), there will be no stable reference from which to make the measurement.
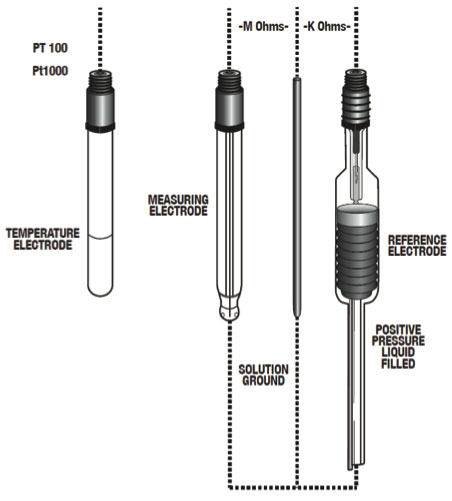
Figure 10: Typical Electrode Configuration for High Purity Water Applications
Counter Measure
These anomalies can be minimized or removed by maintaining a steady flow across a "positive pressure" reference sensor such as the unique bellow system in the reference electrode. The build-in bellow ensures immediate interior pressure equalization to the outside pressure making the sensor virtually insensitive to external pressure/flow variations. A slight overpressure caused by the bellow tension, prevents fluid ingress and maintains a positive ion flow out of the sensor. This feature is of particular interest in pure water applications.
Static Charges
Since pure water is a poor electrical conductor because the conductivity is very low, it creates a static charge when flowing past non-conducting materials that affect the pH reference sensor. This static charge will create stray currents resulting in erratic pH readings.
Pure water has a conductivity value of 0.055 μS (18.2 Mohm) at 25oC. This liquid resistance can lead to the ormation of surface static charges. This can generate "streaming potentials" (stray currents that can mimic pH) in the solution which may cause large errors, or at least excessive noise in the readings. A low impedance, well- shielded and grounded electrode can lower these errors to a minimal value, usually less than ±0.05 pH units. Because the electrical resistance of a typical measuring cell is so high, the electronics used to measure the cell potential are very susceptible to additional interfering factors - extraneous electrical noise pickup and hand capacitance effects. These static charges, called streaming or friction potentials, are comparable to rubbing a glass rod (glass electrode) with a wool cloth (the water). This high resistance also increases the measurement loop's sensitivity to surrounding electrical noise sources. (Figure 11)
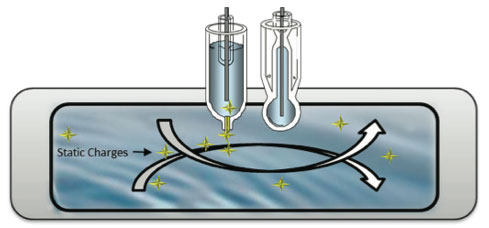
Other electrical source such as ground loop faults and
electro-treatment process will cause the same troubles
Figure 11: Streaming Potentials in a Pure Water Sample
Counter Measure
Using a pH sensor with a liquid earth electrode combined with dual amplifier pH transmitter is recommended. This configuration ensures the measuring and reference electrode signals are amplified separately against the liquid earth contact. This provides the best immunity to noise and stray currents and thus reliable, stable pH readings.
Temperature Compensation
![]() |
Figure 12: Effects of Temperature |
Another problem involves the buffering capacity of pure water, which is very low. When pure water is exposed to air, the absorption of carbon dioxide (CO2) occurs causing a decrease in the pH reading. Depending on temperature and pressure, the pH of pure water may drop to as low as 6.2. Taking grab samples to a lab meter should be avoided because atmospheric CO2 will contaminate the sample. Also, pure water temperature compensation must be taken into account.
There are two major temperature effects that must be addressed in order to establish a truly accurate representation of pH in high purity water. The standard automatic temperature compensator only corrects for one of these, often referred to as the Nernstian or electrode correction.
Its magnitude is determined directly, using the Nernst Equation, which describes that glass electrode operation is independent of the nature of the process fluid. Simply stated, the Nernst Equation states that as a glass electrode increases in temperature, its output voltage increases, even though the actual pH of the measured solution may remain the same. The effect is minimal at or near a pH of 7 and increases linearly above and below a pH of 7.
The second effect is known as the equilibrium or dissociation constant correction. While this effect is usually much smaller in magnitude, it can become significant.
All solutions respond to changes in temperature in a specific way (dissociation constant). Depending on the solution, this response may be related to changes in pH or conductivity. The dissociation constant of pure water is 0.172 pH/10°C. This means that at 50 °C, pure water has a pH of 6.61, while at 0 °C it will have a value of 7.47 pH. The amount of temperature change involved and the critical nature of the measurement dictate if this effect must be compensated for or not. (Figure 12)
Many of the problems associated with high purity pH can be reduced or eliminated through careful consideration of these critical aspects of the pH measuring loop.
Essentials for Optimizing Your pH Measurement
Achieving accurate and reliable readings using a traditional pH analyzer is challenging, however with the right equipment and proper maintenance, stable and accurate pure water pH measurements can be accomplished.
Choosing the Right Materials
Materials of construction of the storage tanks, sample lines, and measurement housings may contaminate the water due to corrosion of leaching of plastics. Table 1 shows a brief list of known acceptable materials of construction for use in ultrapure water systems.
To prevent the increase of static potentials, a stainless steel flow chamber is recommended. Since most plastics are not completely gas tight, such a chamber will also prevent the absorption of CO2 from the air.
Choosing the Right Equipment
Measuring electrode - To counter the low response speed and the effect of the alkali components on the glass electrode, a low-impedance glass is recommended.
Reference electrode - The reference electrode is the most important piece in the measurement setup besides a liquid earth/ solution ground element. The purpose of the reference electrode is to provide a constant reference voltage as well as complete the pH measuring circuit. Because of the low conductive properties of high purity water, a flowing reference is needed. The purpose of the flowing reference is to release just enough ions to carry the measurement signal and to complete the measurement circuit.
Liquid earth/solution ground - To counter the effects of noise (static charge) it is essential that the equipment setup include a liquid earth/solution ground.
Temperature electrode - To ensure accurate temperature compensation, it is recommended that the pH system include a built-in temperature electrode. Recommended Conditions For accurate pH measurement, it is recommended to maintain the following sample conditions:
- The sample temperature should preferably be in the 20 to 30°C range and remain constant.
- The sample must not be stagnant since errors will result.
- Constant flow rates between 50 ml and 150 ml give the best results.
- Air must not be allowed into the sample stream.
- Temperature compensation for both the Nernst potentials and the dissociation constant of pure water are required.
- It is also beneficial to measure pH in the smallest sample volume possible. Direct pH measurement in large volume samples such as drums or tanks and other samples with flowing or moving water tend to fluctuate and will require excessive stabilization time.
Yokogawa Solutions
Depending on installation requirements, there are a couple of different options that can be considered.
Transmitter/Analyzer
Noise problems resulting from ground loop potentials are addressed by the design of the pH transmitter. Many pH transmitters utilize a single-ended amplifier design. This design allows leakage current to pass through the reference electrode, giving an offset in addition to shortening the useful life of the reference electrode. With the differential amplifier design, this leakage current will flow through the solution ground, not the reference. Therefore, no offset occurs and the reference electrode is not adversely affected.
Yokogawa offers two kinds of pH/ORP analyzers:
- FLXA21 2-wire 24VDC pH/ORP Transmitter
- PH450G 4-wire 110 VAC pH/ORP Analyzer
Introduction to the Bellomatic Sensor
Through years of experience and innovative design, Yokogawa has developed solutions for the problems previously discussed. The high diffusion potentials of the reference electrode can be overcome by using a positive pressure style electrode. One such electrode, called the Bellomatic, was developed (Figure 13).
Utilizing a large refillable reservoir, the electrode provides a constant flow rate of reference electrolyte. This provides for a longer, more economical service life than fixed reference electrodes can provide. In addition, the electrode is independent of the effects of process pressure. Therefore, the use of independent air pressure as is used with a salt bridge is not required. The positive pressure that the self-adjusting bellows creates prevents plugging and fouling. It compensates for process pressure spikes, and prevents process ingress.
Introduction to the All-in-One FU24 pH/ORP Sensor
![]() |
Figure 13: SR20-AC32 Bellomatic Reference Electrode |
An alternative to a separate glass and reference electrode is a combination electrode with pressurized reference portion. In addition to the benefits already stated, the close proximity of the two measuring elements helps ensure electrode circuit continuity. The FU24, which incorporates the successful patented bellow system in an all-in-one body, is the ideal solution.
The FU24 was originally developed for harsh chemical temperature/pressure variations resulted in early depletion of the sensors reference chamber, subsequent signal drift and finally loss of functionality.
Designed with an internal bellow, large reference chamber and long-life reference probe, the expected sensor lifetime was calculated to be about 20 years at 20°C in demineralized water.
Further lab tests (D&E 2010-015 & D&E 2011-020) and field tests (D&E 2012-022) indicate that the FU24 also performs very well in pure water applications. Results have been combined into one document TNA1502, however a summary of the results is mentioned below.
Proven Successful Results
Lab tests and field tests were set up to compare the Bellomatic (SR20-AC32) with the FU24 in pure water applications. The following tests were reported:
- 2 hrs test in demineralized water (~1 μS/cm)
- 5 hrs test with demineralized water (~1 μS/cm) and ultra-pure water ((~0.1-0.4 μS/cm)
- 5 wks test with ultrapure water (~50-200 nS/cm)
All tests were at ambient temperature (about 20°C), and a flow rate of about 100 ml/min.
- The main conclusion is that in the reported tests, the FU24 performed as good as the reference system using a separate Bellomatic + glass electrode system.
- Based on the KCl diffusion rate at 20°C, a lifetime of the FU24 reference chamber of about 20 years is calculated.
Test #1
In one test, the vessels were filled with tap water and flushed with demineralized water. The water sources used in the short term tests had the following conductivities:
Tap Water: | about 250 μS/cm |
Demineralized Water: | about 1 μS/cm |
Ultrapure Water: | about 0.1 μS/cm |
The conductivity was recorded at various time intervals. After about 40 minutes, the conductivity in the test vessel with FU24 sensors was stabilized at about 1 μS/cm. The test vessel with the reference SR20-AC32 + SM21-AG2 sensors took a little longer because of the larger volume (less and smaller sensors). The FU24 sensors demonstrated a steady regular signal pattern comparable to the reference sensor system.
The pH-sensors used in the reported tests were not calibrated. The absolute values therefore cannot be compared. However, the main focus is on the stability of the signal, not the absolute mV and/or pH readings.
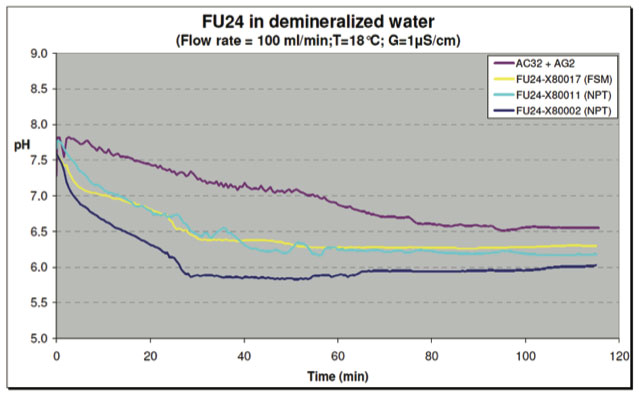
Figure 15: Test with Demineralized Water - pH
Test #2
In another test, the vessels were filled with demineralized water. After about two hours, a switch was made to flush with ultrapure water (see Figure 16) for another three hours. Both the SR20-AC32 + SM21-AG2 reference sensor system and the FU24 sensors showed a more fluctuating signal in ultrapure water as in demineralized water. These fluctuations are in the order of about 10 mV or 0.2 pH units (min-max).
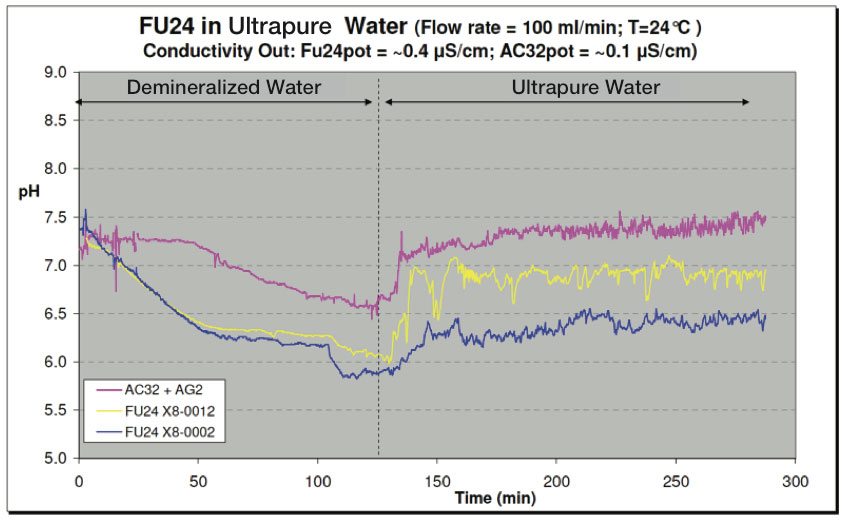
Figure 16: Test with Ultrapure Water - pH
Test #3
In order to confirm a possible application of the FU24 in pure water applications, a longer term test was performed. A Behropur B5 demineralization unit was used to purify the tap water supply to the test pot. The conductivity of the inlet water was reduced to 40-50 nS/cm. A Bellomatic sensor setup was placed in the test pot together with two FU24 sensors. A flow rate of 100 ml/min was maintained for about five weeks while the conductivity, temperature and mV/pH values were continuously monitored. The conductivity and pH data are shown in Figure 17.
The mixed bed ion exchanger in the demineralization unit had to be replaced about every 4-5 days. As the full ion exchange capacity of the bed was reached, not only did the conductivity of the water increase, but the pH also changed. The decrease in pH is most likely caused by an imbalance in the ratio of anionic/cationic resin of the mixed bed ion exchanger. This turned out to be a good control feature, because it helped to observe the response of the sensors to pH changes in low conductive water.
The conductivity of the water coming out of the test pot was in the range of 100 – 200 nS/cm. The temperature varied between 16 – 21°C. The pH data plotted in Figure 6 was corrected to a constant temperature of 20°C. The graph shows 10 points moving average trend lines. Part of the variations in the conductivity is caused by the non-steady flow rate of the tap water supply. The actual flow rate was 100 ± 20 ml/min.
The data proves that the Bellomatic sensor system and both FU24 sensors follow the system pH-changes in similar response. This is even more noteworthy, since the pH-probe glass surface area of the FU24 is about 60% of the surface area of the pH measuring glass sensor in the Bellomatic setup. The main factor in pure water applications is the low conductivity resulting in a large resistance between the reference and the glass electrode. In the FU24 sensor, the diaphragm of the reference electrode is in near proximity of the glass electrode compared to separate reference and glass electrodes in the Bellomatic system. The fact that the resistance is reverse proportional to the distance is in favor for the FU24. The internal overpressure of the FU24 caused by the bellow might also favorably help diffusion out of the sensor compared to other combined sensors.
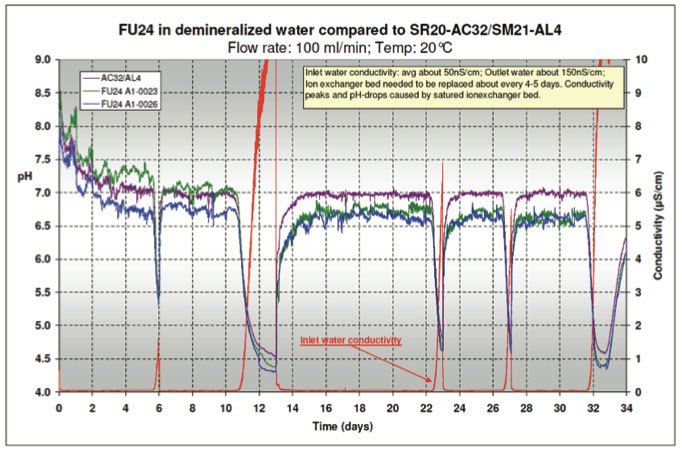
Figure 17: Test with Ultrapure Water -
pH & Conductivity measurements during 5 weeks
Summary
Purified water has very low conductivity, which means it is high in resistance because all the conductive components have been removed. In low conductive solutions combined with its susceptibility to contamination and temperature effects makes accurate pH measurement very difficult. Achieving accurate and reliable readings using a traditional pH analyzer is challenging. However, with the right equipment, stable and accurate pure water pH measurements can be accomplished. Selecting the proper electrodes and holder will eliminate problems with reference junction potentials, slow glass electrode response and surface static charges. Selecting the proper transmitter or analyzer will eliminate ground loop problems and allow for accurate temperature compensation for both the Nernst potentials and the dissociation constant of pure water. In addition, sensor diagnostics gives the operator the ability to assure the measurement loop is functioning properly.
References
Pictures and Figures
Title Page
http://www.shutterstock.com/pic-203101846/stock-photo-pressure-vessels-of-an-industrial-reverse-osmosis-plant. html?src=csl_recent_image-4
Figure 2
Nalco Chemical Company. The NALCO Water Handbook. 2nd ed. Ed. Frank N. Kemmer New York: McGraw-Hill Book Company.1988. Print.
Figure 4
http://www.shutterstock.com/pic-171500693/stock-vector-osmosis-diffusion-of-fluid-through-a-semipermeable-mem- brane-from-a-solution-with-a-low-solute.html?src=pp-photo-209784118-6&ws=1
Table 1
Nalco Chemical Company. The NALCO Water Handbook. 2nd ed. Ed. Frank N. Kemmer New York: McGraw-Hill Book Company.1988. Print.
Information
Nalco Chemical Company. The NALCO Water Handbook. 2nd ed. Ed. Frank N. Kemmer New York: McGraw-Hill Book Company. 1988. Print.
Endüstriler
-
Desalination
The demand for seawater desalination as a stable water resource has been increasing. Yokogawa has a wealth of experience in controlling various types of desalination plant such as reverse osmosis (RO), multi-stage flash (MSF) and multi-effect distillation (MED). Yokogawa provides advanced solutions such as operator training simulators for stable plant operation.
-
Industrial Water
Industrial water is used in all industrial plants such as power generation stations, refineries and petrochemical plants. Yokogawa’s single control platform handles all water and wastewater control processing integrated with the main process.
-
Water & Wastewater
Water resources are finite, and therefore contributing to a sustainable water cycle is one of the Sustainable Development Goals (SDGs). Yokogawa has been providing advanced digital control solutions for the stable supply of clean and safe water, wastewater treatment for protecting the water environment, water loss management and optimization of plant operation for reducing CO2 emissions and running costs. With our leading-edge technologies, dependable products and extensive expertise and experience of diverse water projects around the world, we work with you to provide sustainable water solutions that boost your business and add value throughout the plant lifecycle.
Yokogawa supports a wide range of water control applications in both the municipal and industrial water markets.
ilgili Ürünler & Çözümler
-
Industrial pH/ORP Electrodes
The heart of a pH measuring loop is the electrode system. Yokogawa has designed a wide range of electrodes to ensure this heart keeps beating under the most severe conditions.