Thermal power using coal, oil or gas as fuel accounts for the majority of electric generation throughout the world. With a record of installing over 1000 control systems in thermal power plants, Yokogawa helps customers to ensure safe, optimized operation.
Zorluklar
Customer Challenge
Improving power plant efficiency
Solution
Yokogawa helps power plants operate more efficiently by improving the control of fuel, steam, and feed water.
Enabling Technologies
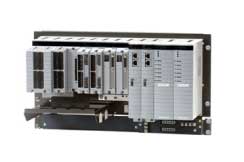
CENTUM VP Integrated Production Control System
The CENTUM VP integrated control system secures interruption-free “uptime only” plant performance for optimal productivity and profitability in the power generation field.
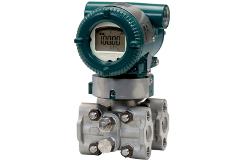
Transmitter
The DPharp series of digital pressure transmitters use a differential pressure high accuracy resonance pressure (DPharp) sensor that represents one of the most revolutionary advances in transmitter technology.
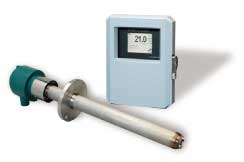
Zirconia Oxygen Analyzers
Yokogawa’s zirconia oxygen analyzers are used for combustion monitoring and control applications and are relied on by a wide range of industries to optimize combustion and reduce NOX emissions.
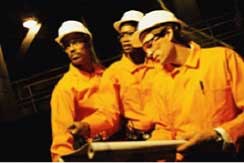
Plant Service (FS)
Commissioning, Operator Training, Operation, Maintenance, and Simulation Services
Customer Challenge
Safely and efficiently starting up boilers, a complicated process that requires considerable skill
Solution
Yokogawa systems make startups safer and more efficient by automating processes such as heating with fuel oil and switching over to biomass fuel. Graphic displays give operators a real-time window into the status of each process.
Enabling Technologies
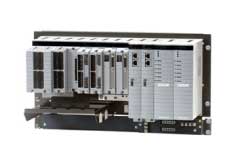
CENTUM VP Integrated Production Control System
The CENTUM VP integrated control system secures interruption-free “uptime only” plant performance for optimal productivity and profitability in the power generation field.
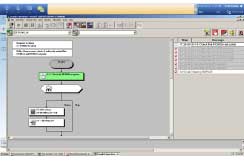
Exapilot Operation Efficiency Improvement Package
Exapilot is an online navigation tool that guides operators step by step through plant operating procedures. Exapilot automates standard operating procedures (SOPs) and provides early detection of process and device abnormalities.
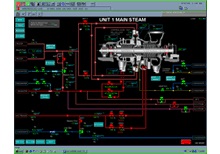
Simulator
High Fidelity, Full-replica Training Simulators
Customer Challenge
Improving combustion efficiency and reducing/eliminating harmful stack emissions
Solution
Yokogawa oxygen analyzers measure the oxygen (O2) concentration in flue gas. With this information, the air-fuel ratio can be adjusted to optimize combustion. Likewise, our stack gas analyzers can be used to reduce harmful emissions by measuring the concentrations of nitrogen oxide (NOX) and sulfur oxide (SOX) in stack gas.
Enabling Technologies
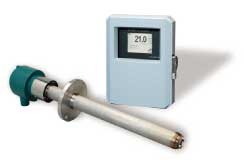
ZR Series Zirconia Oxygen Analyzers
Yokogawa’s zirconia oxygen analyzers are used for combustion monitoring and control applications and are relied on by a wide range of industries to optimize combustion and reduce NOX emissions.
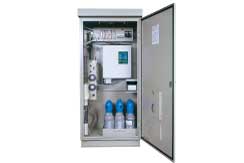
SG Stack Gas Analyzer
The SG stack gas analyzer consists of an infrared gas analyzer unit, a zirconia oxygen analyzer unit, and a sampling unit, and can simultaneously measure up to five components: NOX, SO2, CO2, CO, and O2.
Customer Challenge
Reducing the emission of CO, NOX, dioxins, and other substances into the atmosphere by burning off residual gas components in the stack gas
Solution
Yokogawa gas analyzers measure the oxygen concentration in the stack gas so that adjustments can be made in the O2 supply that will improve combustion efficiency and burn off more residual gas components.
Enabling Technologies
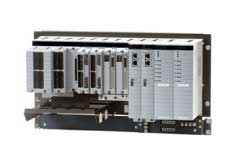
CENTUM VP Integrated Production Control System
The CENTUM VP integrated control system secures interruption-free “uptime only” plant performance for optimal productivity and profitability in the power generation field.
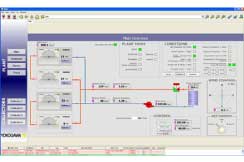
FAST/TOOLS SCADA
The FAST/TOOLS package optimizes performance for renewable energy applications. It ensures high availability and performance and supports online configuration.

ZR Series Zirconia Oxygen Analyzers
Yokogawa’s zirconia oxygen analyzers are used for combustion monitoring and control applications and are relied on by a wide range of industries to optimize combustion and reduce NOX emissions.
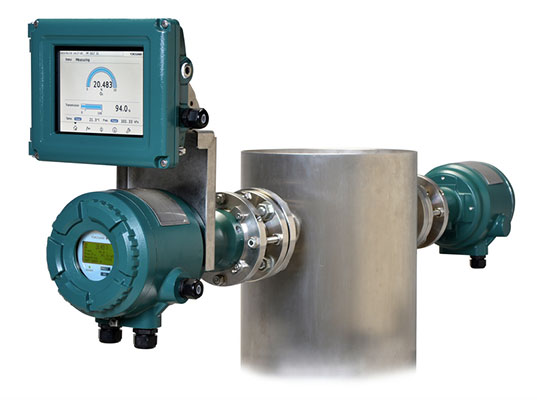
TDLS Laser Gas Analyzer
The TruePeak TDLS gas analyzer relies on a proprietary peak area integration method and is ideal for in-situ analysis in harsh process environments. It significantly improves the efficiency of boiler operations.
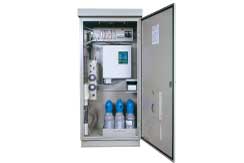
SG Stack Gas Analyzer
The SG stack gas analyzer consists of an infrared gas analyzer unit, a zirconia oxygen analyzer unit, and a sampling unit, and can simultaneously measure up to five components: NOX, SO2, CO2, CO, and O2.
Customer Challenge
Prevent fire accident in coal yard, transmission, and any other facilities.
Solution
Distributed Temperature Sensor (DTS) provided by Yokogawa contributes to fire detection, leak/plugging detection, hot (cold) spot monitoring, and facilities preventive maintenance.
Enabling Technologies
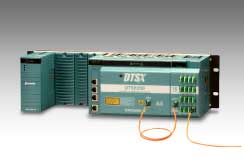
Distributed Temperature Sensor (DTS)
Yokogawa DTSX200/3000 makes possible gapless detection and monitoring.
Details
Coal/Oil/Gas fired Power Generation Process
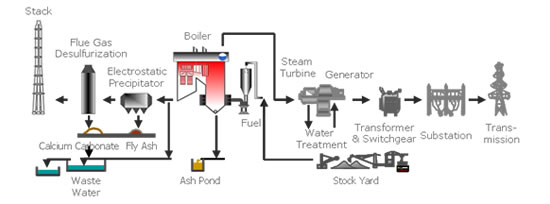
Coal/ Oil/ Gas fired power generation requires the following control and optimization.
Unit control: boiler/ burner management/ turbine/ balance of plant/ flue gas desulfurization/ emergency shutdown
Plant optimization: plant information management/ operation efficiency improvement support/ alarm management
Kaynaklar
- 2009 PACE Zenith joint winner project
- Reduced operating and maintenance costs
- Increased power generation
- Improved plant operating flexibility
- Modernized, screen-based operations
- Reduced emissions
- Steady power supply and safe operation thanks to reliable Yokogawa CENTUM CS 3000 and transmitters
- Environmentally optimized operation by fine-tuned boiler combustion control and strict monitoring and control of CO, NOx and SOx in flue gas and pH of water from cooling towers
- Full replica plant simulator for effective plant operation and engineering staff training
- Annual maintenance contract
- Modernized controls, assured stable power supply to Ulaanbaatar by a highly reliable, expandable distributed control system
- Fully automated boiler, burner, balance-of-plant operations
- Power plant simulator for efficient DCS operator training
- Yokogawa's integrated solutions control FGD processes at Romania's largest power plant
- SO2 and dust emissions are controlled within the EU environmental standards
"Installing the Yokogawa TDL improved our capability to optimize urea injection for the SNCR. The monitors provided more reliability and accuracy, in a harsh environment, than the previous monitors."
At the age of approximately 30 years the plant underwent $A 72 million technology upgrade in 2001, to improve operating reliability and performance. Macquarie Generation, Yokogawa Australia and Ralph M Lee concluded an alliance agreement to supply and install the replacement control system at Liddell.
Eraring Power Station, located just north of Sydney, is one of the largest power stations in Australia, comprising four 660MW coal-fired units. The power station has operated reliably since 1981. To ensure continued reliability for the next few decades, Eraring Energy, the owner of the power plant, decided to replace the original hard-wired control equipment with a modern integrated control and monitoring system (ICMS).
The customer has successfully brought online a greenfield 800 MW supercritical power plant, using a Yokogawa full-replica plant simulator to ensure a fast and smooth plant commissioning process.
The CENTUM CS 3000 / UOI was selected for this project. The control platform in the UOI is the GE Fanuc CIMPLICITY Human Machine Interface (HMI) system, which fully integrates the controls for the turbine and BOP auxiliaries and uses the same screens/formats at both the turbine and BOP HMI displays. The CIMPLICITY HMI used in the UOI is a SCADA based design that fully supports the customer's requirement for remote operation capability.
The construction of Tuas Power Station started in the mid 1990s. The plant has steadily grown to be a significant player in the competitive Singaporean electricity market. Stage One of Tuas Power Station is equipped with the country's largest steam generators which are capable of producing 600 MW each.
Since entering commercial operation in 2000, the environmental control facilities at the Tachibanawan Thermal Power Station have been managed effectively by the CENTUM control system, achieving a stable electricity supply with minimal impact on the environment.
The Bahia de Bizkaia Plant is one of the most significant power projects to be carried out in this region. The project has been led and financed by Ente Vasco de la Energia, Repsol-YPF, British Petroleum, and Iberdrole S.A., with the total investment coming to approximately 600 million euros.
Unified operator interface solution enables remote operation
The Itoigawa Power Plant was constructed adjacent to a cement plant in Itoigawa City, Niigata Prefecture, and is operated by an IPP that supplies electricity to Tohoku Electric Power, one of Japan's major power companies. The use of a 149 MW coal-fired CFB boiler in this power plant is a first for an IPP in Japan, and this effectively reduces NOx emissions.
- Yokogawa’s CENTUM VP and full-replica simulator contribute to the stable operation of this supercritical coal-fired plant.
- The two units have been operating successfully since start-up.
- Yokogawa supplied an integrated boiler and turbine control, monitoring and protection system for each of the four generating units in a coal-fired power plant in Australia.
- Yokogawa also delivered two high fidelity operator training simulators for this plant.
Measures temperature and vibration of the turbine for rapid identification of abnormalities.
One of the most common applications for differential pressure transmitters is flow measurement. DPharp differential pressure transmitters have some unique signal conditioning features to eliminate instability at low flow rates.
Recently, air pollution legislations such as the Clean Air Act to reduce the amount of air pollution are increasing worldwide. The Clean Air Act address numerous air quality problems. One of these problems is acid rain caused by sulfur dioxide and nitrogen oxide emissions from fossil-fueled power plants and other industrial and transportation sources.
In flue gas desulfurization systems that use magnesium hydroxide (Mg(OH)2) slurry, the consumption of the desulfurization agent (Mg(OH)2) is controlled by using online pH analyzers. A great concern in the pH measurement is heavy staining of the pH electrodes by the Mg(OH)2 slurry. To ensure accurate measurement, frequent cleaning of the electrodes with an acid is required, adding to both maintenance workload and cost.
Industry:Chemical, Power
Seawater leak detection is the post-condensation water quality management processes. Damage to the ion exchange resin, which deionizes the supplied water, is also monitored during this process, and both of these applications are executed by a conductivity analyzer. (AN10D01P01-01E)
A package boiler operates more efficiently if the oxygen concentration in the flue gas is reduced. Optimizing air intake for boiler operation requires continuous measurement of the oxygen concentration in the flue gas.
Yokogawa ensures a reliable heat and CO2 transfer system by using the standard GPRS protocol. The exclusive use of webbased technology enables the market gardeners to go online to order heat and CO2 and view information.
In a pulverized coal-fired boiler of a large power plant, an oxygen analyzer is essential for combustion control. A pulverized coal-fired boiler is an industrial or utility boiler that generates thermal energy by burning pulverized coal (also known as powdered coal or coal dust).
The discharge of improperly treated industrial chemicals and fuel gas can have a major impact on the environment, posing a serious threat to public health. Concurrent with the global growth of manufacturing operations to keep pace with market trends, many countries are taking measures to deal with environmental problems.
Floating-point format calculations have enabled physical quantities (in engineering units) to be used in calculations.
Best Solution for Automatic Boiler Control
Sensors and controllers for the efficiency and environmental performance
The SMARTDAC+ GM is best suited for applications where the voltage of each cell in fuel cells, secondary batteries and electrolyzers is measured.
In limestone-gypsum flue gas desulfurization systems, the consumption of a desulfurization agent (lime) is controlled using online pH analyzers.
This paper introduces the ADMAG AXR 2-wire magnetic flomwmeter solution for chilled water application in air conditioning unit.
The ammonia (NH3) gas is injected to remove the NOx and thus reduce the NOx concentration in the stack flue gas. With conventional NH3 analyzers that perform measurements indirectly, NH3 concentrations are obtained through a sampling system. Therefore, there are problems with the maintenance and running costs of the sampling system, and time delays in measurement. The TDLS8000 Laser Analyzer is the solution to all these problems.
Industrial Combustion sources such as thermal cracking furnaces and, process heaters play a critical role in the process industry.
Current trend for increasing mercury awareness throughout the public sector has caused the government to take action. Recently, the Environmental Protection Agency (EPA) has focused their efforts on controlling mercury levels produced in various coal fired power plants. Based on information from several case studies, the EPA developed the Mercury and Air Toxics Standards to cut back mercury emissions. The most popular technology utilized by coal plants to meet the new standards is a scrubber which cleans the off gas from the combustion process. ORP sensors can further monitor the effluent from these scrubbers to ensure optimal mercury emission levels are achieved. By closely monitoring the mercury concentrations in the effluent, plant managers will be able to easily confirm their plants are meeting the EPA's standards.
The worlds of process automation and production management have been converging for some time. What once used to be islands of automation and production management functionality connected through highly proprietary integration schemes that were costly to maintain have developed into integrated platforms that provide seamless data exchange between the world of automation and the plant floor, the functions of production and operations management, and integration with business level systems.
Power plants concerned with lowering NOx emissions are making tremendous changes to accommodate EPA regulatory requirements. A substantial number of these changes include the expansion and upgrade of the plant combustion oxygen measurement equipment. There is a striking relationship between the number of NOx reductions projects and the sales quantity of insitu oxygen detectors.
From engineering to installation, commissioning, operations, and maintenance, FOUNDATION fieldbus offer significant cost reductions of 30 percent or more versus conventional analog systems. Many of these cost reductions come from the advanced functions that fieldbus offers versus analog technology.
The automation suppliers that will be successful in the long term will be those that effectively address application or industry specific problems for end users with a value proposition that cannot be ignored. These problems exist throughout the process industries today, and they won't be solved by simply offering a product, but through a combination of hardware, software, services, application expertise, and knowledge.
In ARC's view, customers need a compelling business value proposition to justify investment in any kind of automation. Vigilance and VigilantPlant were created with this in mind. Yokogawa's vision with VigilantPlant is to create an environment where plant personnel and operators are well informed, alert, and ready to take action.
Yokogawa has come a long way in making its message clear to the world of process automation. Last year, the company embarked on a full-scale global marketing campaign to make customers aware of the company's focus on system reliability, security, dependability, and robustness. Dubbed "Vigilance", the campaign created a unified message for the company and greatly helped expand awareness of the Yokogawa brand and corporate philosophy.
Process automation end users are under more pressure than ever to do more with less. The current economic climate means that many automation capital projects are on hold. With capital budgets tighter than ever, users instead focus on operational budgets (where cost cutting is also a key concern), or on automation investments with a very rapid return on investment.
In today's dynamic industrial marketplace, the only constant is change. Raw material costs, energy costs, market demands, environmental and safety regulations, technology, and even the nature of the labor force itself are constantly changing, and not always in predictable directions.
İnsanlarımız, teknolojimiz ve çözümlerimiz hakkında daha fazla bilgi mi arıyorsunuz?
Bizimle İletişime Geçin