About Thai Acrylic Fibre Co., Ltd.
Remarkable Reduction in CAPEX and Faster
Commissioning by FOUNDATION™ Fieldbus
Thai Acrylic Fibre Co., Ltd. (TAF) was established in 1987 and is currently a leading acrylic fiber manufacturer in the ASEAN region with 450 employees. It produces a wide range of acrylic fiber productions with varied deniers and the annual production recorded 77,000 megatons in 2004 which is five times the production rate at the time of establishment. TAF is a flagship company of the Aditya Birla Group which is one of the biggest business entities in India, having 72,000 employees in 18 countries. TAF is proud of improving the efficiency and quality of their products and has won international awards including the famous *Deming Prize in 2001.
*Deming Prize: The Deming Prize is an award and given to companies which have exerted an immeasurable influence on the development of quality control and management. The Deming Prize committee examines the execution condition of the quality control.
Background of This Project
Over 60% of TAF's production is being exported directly to all over the world and TAF is aiming to be one of the big three in the global textile market by 2010. In order to survive in the competitive market, TAF required a leaner production management system, accompanied with an optimal and minimum capital investment on plant and equipment, and improvements of productivity and operating profit ratio. This project was obliged to achieve not only capital expenditure (CAPEX) saving but also future operation cost (OPEX) reduction.
The Reasons for Selecting Yokogawa
TAF had already introduced Yokogawa's products and solutions as analog instruments to its 1st to 3rd fields. The customer has relied on our technologies and capabilities, which prompted TAF to adopt Yokogawa's state-of-the-art technology, FOUNDATION™ fieldbus for this 4th field.
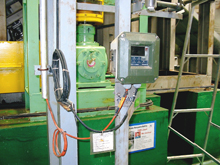
TAF had already introduced Yokogawa's products and solutions as analog instruments to its 1st to 3rd fields. The customer has relied on our technologies and capabilities, which prompted TAF to adopt Yokogawa's state-of-the-art technology, FOUNDATION™ fieldbus for this 4th field.
The Challenges
TAF did not have any experience with FOUNDATION fieldbus and there was no actual data which showed its introduction merits for a plant of almost the same size as the 4th field. Furthermore, the customer faced the following challenges.
- Faster commissioning
TAF's most demanding requirement was to reduce commissioning time. "Time to market" is the key issue and TAF thought that FOUNDATION fieldbus would bring huge benefit directly if its commissioning was completed within one year. Commissioning time for this project means a period from placing the order including a CENTUM CS 3000 distributed control system to starting normal operation of the installed system. - Asset performance optimization
Generally speaking, the latest FOUNDATION fieldbus technology reduces CAPEX cost by up to 10%, including field wiring, marshalling racks and devices. TAF was aiming to achieve more than 10% savings which could be invested to build the 5th field. - Innovation in operation and maintenance by digital plant control system
The customer wanted a digital plant control system based on FOUNDATION fieldbus, which achieved an innovation of the plant operation and maintenance.
The Results
- 10-month commissioning realization
The project completed in only 10 months supported by collaboration between Yokogawa and TAF engineers, which was much shorter than the original schedule. Two-month reduction in commissioning period enabled cost saving. - About 20% reduction in CAPEX
The faster commissioning led to a remarkable CAPEX reduction at about 20%. This cost saving could be invested in enhancement of the 5th field in the future and TAF is also expecting to greatly reduce OPEX-an ongoing, long-term cost associated with on-site maintenance. - Plant efficiency and process capability improvements
To enhance the FOUNDATION fieldbus system, TAF introduced the latest distribution control system, CENTUM CS 3000 R3, and solution-based packages such as plant resource manager (PRM) and plant information management system (PIMS). They contributed to increasing efficiency in operation and maintenance work by utilization of information from field devices, as well as enabled status monitoring, self-diagnosis of field devices and remote control. As a result, plant operation and maintenance trouble was reduced and the plant efficiency and process capability were improved.
Customer's Satisfaction
To survive in the competitive global market, the paradigm shift from traditional analog control systems to digital fieldbus systems is essential. This success has also encouraged TAF to work with Yokogawa in starting up the 5th field.
System Details
System: | Fieldbus Control System |
---|---|
CENTUM CS 3000 R3 | |
Plant Resource Manager | |
Exaquantum / Exaplog | |
Control Configuration: | HIS x 1, ICS x 8, FFCS x 3 |
Conventional type I/O: 1104 (HART I/O:368) | |
80 segments of FOUNDATION fieldbus |
Súvisiace produkty a riešenia
-
Alarm Analysis (Exaplog)
The new Exaplog event analysis package facilitates the quantitative analysis of problems in the DCS event log. By alternating analysis with alarm setting adjustment and operation sequence tuning, you can continuously improve operational efficiency.
-
Plant Resource Manager (PRM)
Have the facility managed properly for high-reliable and stable plant operation? PRM contributes to improving the quality of maintenance plans and optimizing maintenance costs throughout the plant life cycle.