Executive Summary
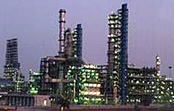
High Uptime and Maintainability Secured
by Full-fledged Automation Platform
at Indian Refinery
HPCL-Mittal Energy Limited (HMEL) is a joint venture between Hindustan Petroleum Corporation Limited and Mittal Energy Investment Pte Ltd, a Lakshmi N Mittal company that is based in Singapore. HMEL has built and currently operates the Guru Gobind Singh refinery, which is located near Bathinda in India's Punjab region. This new refinery has a production capacity of 9 million tons per annum (the equivalent of 180,000 bpd) and complies with the Euro IV emission norms. This is a zero bottom plant, with a very high Nelson Complexity Index. The refinery facilities include a polypropylene unit (PPU) that utilizes the Novolen® gas-phase polypropylene (PP) process and is capable of producing 440,000 tons per year of homo-polymer PP.
HMEL produces an entire range of PP homo-polymers. The refinery's state-of-the art delayed coker unit (DCU) produces a high sulfur petroleum coke (pet coke) derivative. The sulfur recovery unit produces very high quality sulfur in powder and lump form. The other notable deliverable is a high yield of environmentally friendly liquid petroleum gas (LPG) for household and commercial customers in the northern region of the country.
For the monitoring and control of the entire Guru Gobind Singh refinery, HMEL selected an integrated solution from Yokogawa consisting of the CENTUM VP state-of-the-art distributed control system, the ProSafe-RS safety instrumented system, the Plant Resource Manager (PRM) asset management system, the Exasmoc, Exarqe, and fitOMS advanced process control (APC) packages, FOUNDATION™ fieldbus instruments, and an operator training simulator (OTS). Yokogawa India oversaw and implemented their engineering, installation, and commissioning, and the refinery has performed flawlessly since coming online in early 2012.
The central control room
The Challenges and the Solutions
1. Maintenance
This full scale refinery has a total of nearly 12,000 field instruments. To ensure the efficient utilization and maintenance of these assets, HMEL decided to use the FOUNDATION fieldbus technology in tandem with the PRM asset management package. With this solution, personnel in the central control room can monitor the performance of these field assets and diagnose their condition. PRM also has a control valve signature analysis function. With these capabilities, the HMEL maintenance team is able to adopt a proactive maintenance approach whereby problems are spotted before a field device or control valve fails and maintenance can be scheduled to be performed at an opportune time. In addition to improving plant uptime, this eliminates the need for many manual checks of devices in the field, reducing field operator workload.
2. Safety
Safety is always a paramount concern at an oil refinery. ProSafe-RS is SIL-3 certified by TUV for the management of the emergency shutdown (ESD) system and the fire & gas system (FGS), and is fully integrated with the DCS. In addition to the many benefits of an integrated human machine interface (HMI) for DCS and ESD, the integration of DCS and ESD also allows the seamless exchange of signals between the DCS interlocks and the ESD logic, especially in the Poly Propylene units which requires many signals and status of ESD logics in the DCS controllers.
3. Efficiency and product quality
HMEL utilizes APC packages together with the DCS to improve efficiency and ensure the highest levels of product quality. The Exasmoc multivariable optimization controller and the Exarqe robust quality estimator are used to reduce the amount of steam consumed by the continuous distillation unit (CDU), DCU, and fluidized catalytic cracking unit (FCCU) and to help ensure the steady operation of the entire refinery.
Blending is the last step in the process of producing finished products from crude oil. Quality control for the finished products is one of the most important steps in the refining process. At the HMEL refinery, Yokogawa's fitOMS (future integration technology for oil movement system) APC solution works in conjunction with near infrared analyzers (NIR) to optimize mid sulfur (MS) oil blending and high speed diesel (HSD) blending. This ensures that the finished products are kept within the targeted blend ranges and that this is done in the most cost-effective way.
The package includes an OTS for a total of 10 process units. Built by Omega Simulation Co., Ltd., this is a DCS direct connect type OTS used in operator training that also can function as a DCS-programmable logic controller (PLC) to check out control strategies. The early delivery of the OTS ensured that the operators could familiarize themselves with the systems before the plant commissioning. The specific process units covered by the OTS are:
- CDU, vacuum distillation unit (VDU)
- Naphtha hydrotreater (NHT)
- Isomerization (ISOM) unit
- Catalytic reformer
- Diesel hydrotreater (DHDT)
- Vacuum gas oil – hydrotreater) (VGO-HDT)
- Fluidized catalytic cracking – propylene recovery unit (FCC-PRU)
- Polypropylene
- Hydrogen generation unit (HGU)
- DCU & sulfur recovery unit (SRU)
Client satisfaction parameters:
- Robust best-in-class DCS/PLC solution
- Robust, fast Vnet/IP network
- Control of field instruments on FOUNDATION fieldbus closed loops
- Integrated DCS/ESD PLC network
- Robust HMI used as direct node on DCS network
- Remote PLC I/O for hardwired console in CCR
- Able to perform PRM control valve signature analysis and partial stroke testing of shutdown valves from CCR
- Redundant ProSafe-RS architecture for both ESD and FGS, from I/O level to CPU
- ProSafe-RS sequence of events (SOE) functionality with 1-msec event resolution for trip analysis and troubleshooting
Project details:
Total system tags: | 41,000 |
---|---|
Total DCS closed loops (conventional): | 2,350 |
Total devices on FOUNDATION fieldbus: | 12,000 |
Total FOUNDATION fieldbus segments: | 2,240 |
Maximum number of devices per segment: | 9 |
Total FOUNDATION fieldbus closed loops: | 1,210 |
Total HMIs: | 82 |
Total ESD and FGS PLC I/Os (ProSafe-RS): | 16,240 |
Video wall size in main control room: | 48,854 mm (W) x 2,200 mm (H) (80 x 60" displays) |
Customer Satisfaction
P.S. Prasad, General Manager, Maintenance – Control & Instrumentation at HMEL, commented, "The CENTUM VP system supplied by Yokogawa forms a complete integrated network connecting all the process units and the central control room. Since its commissioning in 2012, the system has been very robust and has withstood all plant disturbances. PRM has proven to be an extremely effective maintenance tool as the majority of the closed loops are based on FOUNDATION fieldbus. The ESD and FGS systems designed to work with ProSafe-RS have performed as specified. Yokogawa has been very forthcoming with its support and maintenance of the integrated automation system, ensuring high uptime."
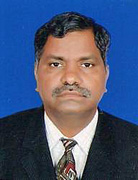
Odvetvia
-
Oil & Gas Downstream
The oil & gas downstream industry has been facing an increasing number of challenges in recent years. These include the changing characteristics of the feedstock to be processed, aging of process facilities and equipment, rising cost of energy, lack of skilled plant operators who can run a refinery safely and efficiently, and the ever-changing requirements from both the market and the customer.
Over the years, Yokogawa has partnered with many downstream companies to provide industrial solutions focused on solving these challenges and problems. Yokogawa's VigilantPlant solutions have helped plant owners to achieve maximum profitability and sustainable safety within their plants.
-
Refining
In the ever changing marketplace, refineries are seen not only as crude processing units but also as profit centers. At the same time, there is a keen awareness of the need for safety at such facilities. A total production solution that encompasses planning, scheduling, management, and control is required to achieve long-term goals for profitability, efficiency, and environmental protection. With years of expertise in the automation field, Yokogawa can bring you affordable total solutions for improved operability and a cleaner world.
Súvisiace produkty a riešenia
-
Plant Resource Manager (PRM)
Have the facility managed properly for high-reliable and stable plant operation? PRM contributes to improving the quality of maintenance plans and optimizing maintenance costs throughout the plant life cycle.
-
Platform for Advanced Control and Estimation (Advanced Process Control)
The all inclusive Platform for Advanced Control and Estimation brings multi-variable control, quality estimation, complex custom calculations, and operator user interface design all into one application; in doing so, dramatically reducing deployment time and simplifying maintenance for robust performance.
-
SIS (Up to SIL 3) ProSafe-RS
The ProSafe-RS is a Safety Instrumented System that is certified by the German certification organization (TÜV) to meet Safety Integrity Level (SIL) 3 specified in IEC 61508.
-
Distributed Control System (DCS)
Our distributed control system (DCS) enables automation and control of industrial processes and enhanced business performance. Over 30,000 systems entrust Yokogawa DCS to deliver their production goals.
-
Safety Instrumented System (SIS)
Yokogawa’s SIS and relevant safety solutions are widely used in applications of Emergency ShutDown systems, Fire & Gas systems, Burner Management Systems and HIPPS systems.