Executive Summary
Qatar Petroleum, Qatar
Qatar Petroleum (QP), a government-owned company responsible for all oil and gas industry activities in Qatar, initiated this project to upgrade and enhance the control systems on the PS-2 and PS-3 offshore production platforms in the Maydan Mahzam and Bul Hanine fields. The scope of work encompassed the upgrade and replacement of existing instruments and systems with a FOUNDATION™ fieldbus-enabled distributed control system (DCS). The existing control system was partly electronic (Honeywell DCS and GE Fanuc PLC) and partly pneumatic (single loop controllers from various vendors).
All of the subsystems such as the emergency shutdown (ESD) and fire & gas safety systems (FGS) (Triconex and Wonderware), well head monitoring system (DATAC), and power management system (ABB) had independent human machine interfaces (HMI).
Amidst stiff competition from engineering companies, Yokogawa Middle East was awarded the engineering, procurement, installation, and commissioning (EPIC) contract for the control system upgrade at the PS-2 & PS-3 offshore platforms. It is believed that QP is the first company in the Gulf region to adapt the FOUNDATION fieldbus technology on its offshore platforms.
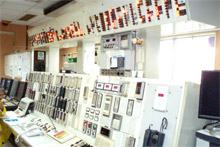
Central control room
(before upgrade)
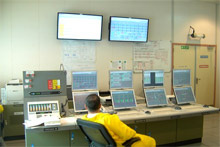
Central control room
(after upgrade)
The Challenges and the Solutions
Yokogawa Middle East faced a wide scope of challenging tasks in this EPIC project, conducting extensive site surveys, carrying out detailed engineering of field instruments and control systems, preparing design specifications, interfacing with existing third party systems, and eliminating barriers for QP's documentation practices. The Yokogawa Middle East engineering team and their project partners made full use of the best engineering practices and their experience to realize QP's project vision for utilizing all the features of the latest technology. Regular team meetings, knowledge sharing sessions, and methodical validation of output data during the engineering process paved way for the delivery of quality products. One hundred percent FAT checks of the hardware and application software as well as tests verifying communications with sub-systems ensured that the plant could start up and be fully operational in a minimum amount of time.
Yokogawa worked very closely with QP Project Execution Team consisting of Sathar Vadooth, Sathesh Kamath, Subbiah Shivaji, Abdullah Al-Marri and Shahed Halim from project commencement to project handover guiding Yokogawa Team-This was a major contribution factor in the success of the project.
Much to the appreciation of the client, the entire cutover to the new systems was achieved well within the 30 day shutdown timeframe, and this was accomplished in spite of the typical offshore operational hurdles of weather, logistics, and limited accommodations. The QP, Yokogawa Middle East, and project business partners worked as one team to bring this project to a successful completion.
Applying the new FOUNDATION fieldbus technology was one of the challenges in this project. Nearly 1,000 FOUNDATION fieldbus-enabled devices were connected to the CENTUM CS 3000 DCS and this configuration brought the following major benefits to QP's operations:
- Space is very limited on offshore platforms and must be put to optimum use. The FOUNDATION fieldbus-based design enabled drastic reductions in the size and number of marshalling cabinets and in the amount of trunk cable that had to be laid.
- With Yokogawa's Plant Resource Manager (PRM) asset management system, commissioning tasks such as valve tuning, loop checking, device configuration, and troubleshooting could all be done online from a central location, yielding a drastic improvement in efficiency.
- For those valves that had been retrofitted with new positioners, valve signatures could be derived using the PRM ValveNavi plug-in application.
- PRM also provides a single window interface to all FOUNDATION fieldbus and HART devices on the platform and this gives maintenance personnel quick access to all related device documents such as loop drawings, manuals, and hook-up drawings that have been registered with the system.
Customer Satisfaction
"We are now very comfortable with our current operations and we very much appreciate Yokogawa's support. The PS-2 & PS-3 offshore platforms are equipped with Yokogawa's VigilantPlant product solutions that clearly deliver value at each stage of our processes. These include the Tharp multivariable transmitter, YTA temperature transmitter, CENTUM CS 3000, Exaquantum/SER, PRM, and the FIELDEYE CCTV system.", said by Mr. Ahmed Abbad Nasser Hussain Al-Aji, Manager Production (Offshore Fields), Mr. Mohd Ali Mohd Humaid, Asst. Manager, Operations-PS2, Mr. Darwish Ghloom Hussein Bahzad, Asst. Manager, Operations-PS3.
A Great Achievement
Yokogawa Middle East announces with pride the successful start-up of the PS-2 & PS-3 offshore platforms after a seamless upgrade from existing Honeywell DCS, GE FANUC ICS, and pneumatic systems to a FOUNDATION fieldbus-based CS 3000 DCS. The system has interfaces with the ESD/FGS, power monitoring, wellhead monitoring, and heating/ventilation/air conditioning systems, thereby achieving the project objective of having a single HMI window for monitoring and control of an entire platform.
"Talent wins games, but teamwork and intelligence win championships"
– Yokogawa Middle East project team
Odvetvia
-
Upstream
The upstream industry includes offshore and onshore activities including wellhead automation, fractionation, completion, and separation to recover and prepare underground or underwater crude oil and natural gas.
As petroleum is brought to the surface, it must be separated prior to transport. Primary and secondary separation stages commonly distribute gas flow, water flow, and oil flow in three phase separation. Gas movement requires pipeline and can include a fractionation process in the upstream stage prior to movement. Liquids can be placed into a tanks or pipelines and sent for processing, requiring accurate level measurements.