The DTSX is a unique and innovative temperature monitoring system that uses a fiber optic cable as a temperature sensors.
Current Issues
Impacts of Nonuniformity in Temperature for Resins and Other Materials inside Reactors on Productivity, Quality, and Management
In some cases, temperature nonuniformity inside operating reactors affect the productivity and quality of products.
In general, a reactor is only equipped with several thermometers, which hardly help you check temperature nonuniformity inside the reactor.
When increased efficiency has promoted plant integration and upsizing, resulting in decreased productivity and deteriorated quality, it not only leads to late deliveries but also impacts the supply chain, which will have direct impacts on the society and management.
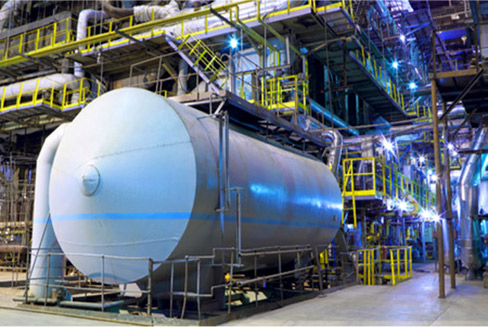
Solutions and Benefits
Fiber Optic Cables Allow You to Recognize Variations in Temperature inside Reactors from Outside
Reactors are equipped with point sensors, which are capable of measuring temperatures inside reactors; these sensors are several in number, which are unevenly distributed in a certain direction at intervals of several meters, often indicating uniform temperature.
When you manufacture a resin or the like from the same material and with the same parameters, you may not always achieve the same-level productivity and / or quality. If this is the case, it is required not only to secure the same level productivity and / or quality, but also to spend time and effort in determining the cause (s) and taking countermeasures.
It is considered that cause analysis requires temperature nonuniformity inside the reactor to be checked as one the factors; however, in realty, there is no way to check the nonuniformity.
DTSX distributed temperature sensor allows you to relatively recognize temperature nonuniformity inside the reactor from outside, using a fiber optic cable installed on the surface of the reactor to totally measure reactor surface temperatures.
The DTSX is used to improve productivity and quality by checking temperature nonuniformity inside reactors and feeding back that information to be reflected as an operational indicator.
Supposing that a facility with annual production of 300,000 tons has improved its productivity by 0.3 % , it increases its production amount 900 tons, resulting in a yield improvement of 900 million yen a year (with an assumption that the yield is 100,000 yen / ton).
Features of Optical Fiber Sensing in DTSX System
Temperature distribution monitored every 1 m
- Monitoring distance: to 50 km
- Monitoring temperature: -200 to 300 °C
- Shortest monitoring cycle: Approx. 5 seconds
- Temperature resolution: 0.03°C
* Each specification dependent on conditions
Main Features
- 24 hours a day, 365 days a year monitoring even in wide areas and ordinarily non-manned areas
- Power supply not required, explosion-proof, not affected by electromagnetic noise
- Flexible installation
- High compatibility with DCS and other host systems (Modbus / TCP)
Related Applications
-
Monitoring of Soundness of Power Supply Bus Bar
The joints of the power supply bus bar are monitored. Abnormalities are not overlooked as fiber optic cable is built into the bus duct and bus bars extending over long distances in blind areas such as roof space are comprehensively monitored.
(For details, refer to "Monitoring of Soundness of Power Supply Bus Bar -In-vehicle Lithium-ion Battery Applications-".)
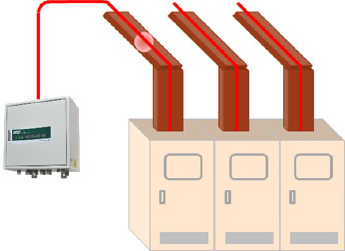
-
Monitoring the Soundness of High-Temperature Reactor Bodies
DTSX monitors the soundness of the refractory bricks inside high-temperature reactor bodies. It detects any abnormality that may lead to a shell breakage at an early stage by checking for hot spots on the reactor body surface to determine whether refractory bricks inside are damaged.
(For details, refer to "Furnace Monitoring for Safety and CBM".)
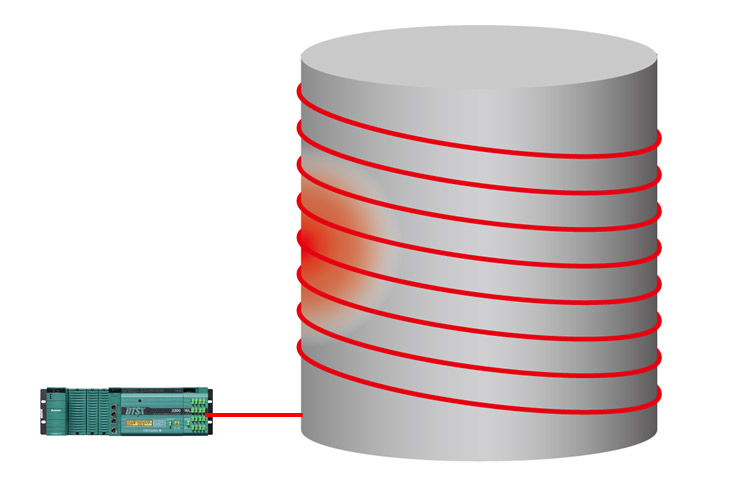
-
Checking of Separator / Electrode Coating Drying Furnace Temperature Distribution
The temperature distribution inside the drying furnace of the coating drying process for the separators / electrodes that make up a lithium-ion battery is visualized. Optimizing the temperature profile improves productivity.
(For details, refer to "Fiber Optic Cable Visualizes In-furnace Temperature Distribution".)
Looking for more information on our people, technology and solutions?
Contact UsIndustrias
-
Chemical
Chemical plants rely on continuous and batch production processes, each posing different requirements for a control system. A continuous process calls for a robust and stable control system that will not fail and cause the shutdown of a production line, whereas the emphasis with a batch process is on having a control system that allows great flexibility in making adjustments to formulas, procedures, and the like. Both kinds of systems need to be managed in available quality history of product, and to be able to execute non-routine operations. With its extensive product portfolio, experienced systems engineers, and global sales and service network, Yokogawa has a solution for every plant process.
Productos y Soluciones Relacionadas
-
DTSX1 Fiber Optic Heat Detector
DTSX1 stores the functions required for heat detection in one box. DTSX1 analyzes the temperature data with high accuracy by measuring with fiber optic sensor cable and perform high temperature heat detection.
-
DTSX200 Distributed Temperature Sensor
The DTSX200 is a standard version that is ideal for temperature measurement, for medium-sized areas, and for areas where the distance of fiber optic sensor cables is short. It has excellent environmental resistance because it consumes less power and is less dependent on the temperature measurement environment.
-
DTSX3000 Distributed Temperature Sensor
The DTSX3000 is a distributed temperature sensor developed in response to the demand that “one unit be used to monitor temperature distribution a longer distance and a wider area”. A flagship model that meets the expectations for long-distance temperature measurement and high temperature resolution.
-
Fiber Optic Temperature Sensor DTSX
The DTSX fiber optic temperature sensor, which uses optical fiber for the temperature sensor, quickly detects and locates abnormalities in equipment by monitoring temperatures at production facilities located far away and across wide areas 24 hours a day, without omission. Highly accurate predictive maintenance avoids downtime and ensures stable plant operation.