Crear juntos un futuro sostenible mediante la minería inteligente
La sociedad moderna depende de los recursos minerales para todo, desde los automóviles hasta las infraestructuras. La industria minera se enfrenta a retos complejos, como las normas ASG, el agotamiento de los recursos, los riesgos geopolíticos y los problemas de seguridad, que no pueden resolverse únicamente mediante la optimización individual.
Yokogawa impulsa la planta minera Transformación combinando mediciones centenarias Experiencia del sector del petróleo y el gas con tecnologías IoT, AI y Digital Twin. A través de nuestra red mundial de asistencia, nos asociamos con todo el ecosistema para abordar estos complejos problemas.
Colaborar con Yokogawa para lograr una minería sostenible que vaya más allá de los planteamientos convencionales.
Industria Destacados
NOTICIAS
¿Por qué es fundamental la optimización integral para una minería sostenible? Naohisa Endo, Vicepresidente de Yokogawa, comparte sus ideas en Mining.com.
Read the full article
FOLLETO
Minería inteligente: El futuro de las plantas mineras evoluciona gracias a la tecnología digital
REFERENCIA
CENTUM La migración de VP mejora la eficiencia en una mina de oro australiana
Claves Industria Desafíos y cómo responde Yokogawa
Seguridad de los trabajadores y de las instalaciones
- Introducción de la tecnología de automatización
- Medidas de ciberseguridad
Mejora de la productividad
- Mejorar la eficiencia mediante la utilización de datos
- Integración de IoT, IA y Digital Twin
Planta óptima Operación
- Refuerce la fiabilidad con un mantenimiento inteligente
- Minimizar el tiempo de inactividad
Soluciones de Yokogawa
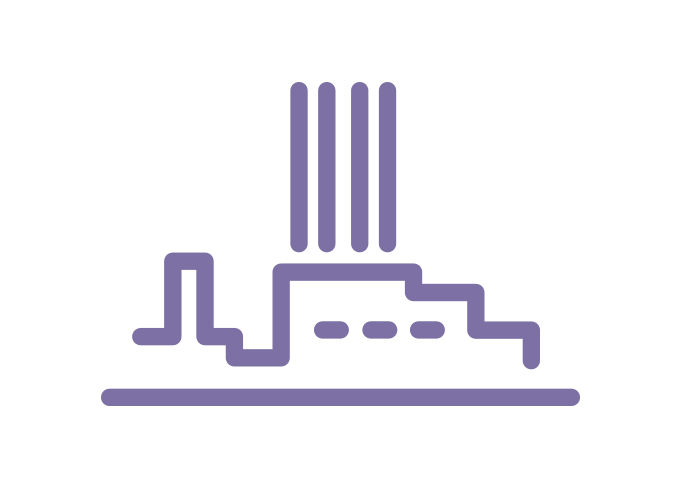
Apoyo al trabajo de campo
Permita operaciones seguras compartiendo y digitalizando vídeo y audio en tiempo real
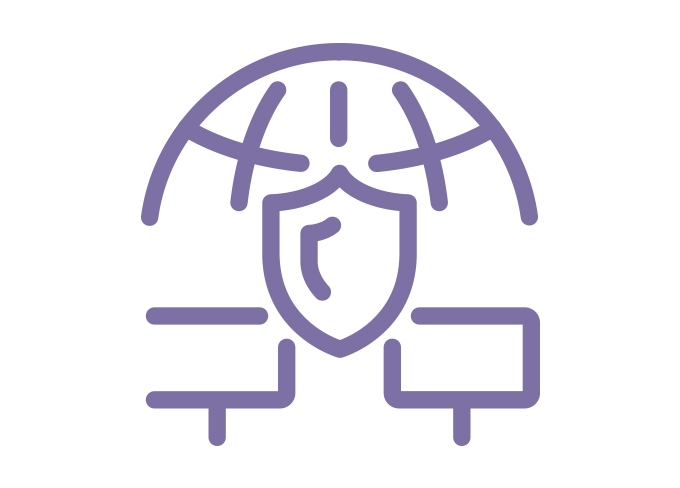
Minimización del riesgo de ciberataque
Garantizar una gestión de la seguridad adecuada a las situaciones de los clientes y proteger eficazmente la planta de los ciberataques.
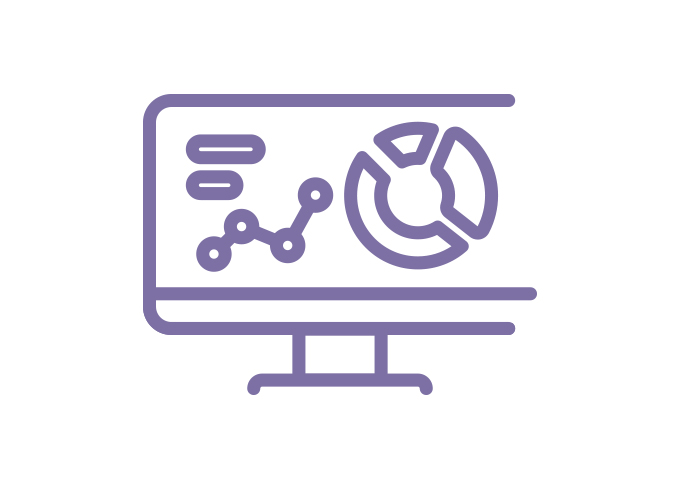
Transformación en operaciones basadas en datos
Organizar los flujos de trabajo para favorecer una utilización óptima de los datos in situ.
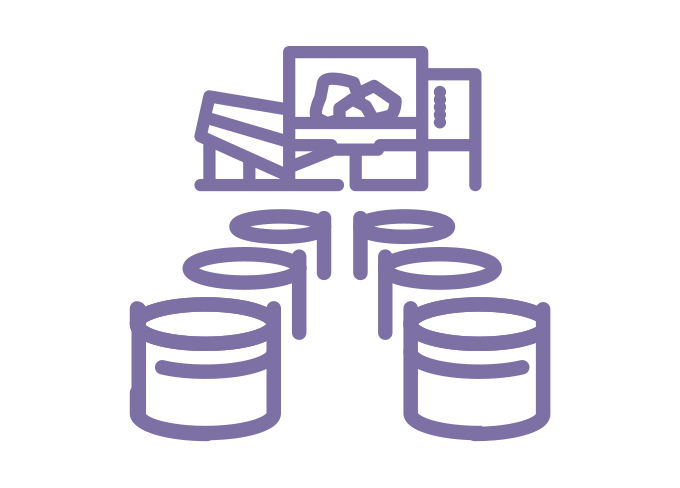
Visualización del estado de los equipos
La visualización en tiempo real del estado de toda la planta y los equipos permite un funcionamiento eficaz y una respuesta rápida a las anomalías.
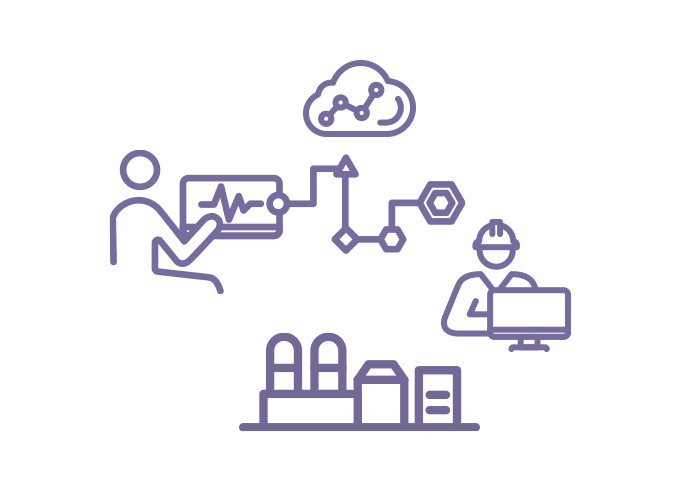
Planta Operación Plataforma de optimización
Utilizando Digital Twin para el procesamiento de datos en tiempo real y agentes autónomos de IA para la resolución de problemas, maximizar el uso de activos como equipos y apoyar a los responsables de la toma de decisiones en las operaciones de la planta, optimizando así las operaciones de la planta.
Apoyo al trabajo de campo
Permita operaciones seguras compartiendo y digitalizando vídeo y audio en tiempo real
En el sitio Desafíos
- Lleva tiempo llegar al lugar del problema
- Un apoyo insuficiente provoca fallos en los equipos y lesiones a los trabajadores
Soluciones
- Compruebe la situación in situ utilizando llamadas de voz y vídeo nítidas desde ubicaciones remotas
- Escriba instrucciones desde ubicaciones remotas en documentos e imágenes mostrados en dispositivos móviles en tiempo real.
- Graba los detalles del trabajo junto con el vídeo, y comparte la información y crea un manual más adelante
Beneficios
- Si surge algún problema, la situación in situ puede compartirse con antelación, y puede prestarse apoyo al centro desde ubicaciones remotas.
- Reducción del tiempo de trabajo in situ y del tiempo de recuperación del sistema
Minimización del riesgo de ciberataque
Garantizar una gestión de la seguridad adecuada a las situaciones de los clientes y proteger eficazmente la planta de los ciberataques.
En el sitio Desafíos
- No existen medidas para hacer frente a los incidentes de seguridad
- No sabe por dónde empezar con las medidas de seguridad
Soluciones
- Realización de una propuesta de extremo a extremo y aplicación de medidas de seguridad, supervisión de operaciones y respuesta a incidentes basadas en la norma IEC62443.
- Consideración de los niveles objetivo en función de la rentabilidad
- Gestión centralizada de la seguridad con supervisión en tiempo real
- Gestión global 24/7 a través del servicio de asistencia
Beneficios
- Minimizar los riesgos de pérdidas monetarias por ciberataques
- Reducción de costes mediante la simplificación, normalización e integración de la gestión de la seguridad
- Refuerce la seguridad cumpliendo las normas de seguridad del sector y de las empresas, como la IEC62443.
Transformación en operaciones basadas en datos
Organizar los flujos de trabajo para favorecer una utilización óptima de los datos in situ.
En el sitio Desafíos
- Poco uso de las imágenes de la cámara y Datos de proceso
- Procedimientos de trabajo poco claros
Soluciones
- Organizar los datos recopilados y el uso para crear prioridades y hojas de ruta para la utilización de los datos.
- Organizar talleres para aclarar los procedimientos de trabajo
- Introducir procedimientos normalizados de trabajo (PNT) digitales para lograr la automatización mediante sistemas
Beneficios
- Transformación operativa adaptada a los contenidos y datos reales del trabajo
- El PNT facilita la transferencia de conocimientos y reduce la carga de los operarios
Caso práctico de flotación
Paso1: Organizar el uso de los datos y los procedimientos de trabajo.
Proponer mejoras del flujo de trabajo utilizando datos no utilizados
Antes : Con frecuencia permanece en estado anormal
La espuma de la superficie de la celda de flotación se capta con una cámara, pero no es supervisada por el operador. Las condiciones anormales de la espuma no se controlan, lo que afecta negativamente a los índices de recuperación de mineral.
Después : Detección y respuesta rápidas ante condiciones anómalas
Detección y respuesta rápidas ante condiciones anómalas Detecta automáticamente las condiciones anómalas de la espuma mediante el reconocimiento de la imagen de la cámara. Notifica al operador y le pide que responda rápidamente.
Paso2: Normalización y automatización del trabajo
Lograr la estabilización operativa y la pronta recuperación mediante la introducción de PNT
Antes : El trabajo varía en función de los operarios
Los procedimientos de trabajo de los operarios para pasar de condiciones anormales a normales son incoherentes y varían.
Después : El trabajo está normalizado y parcialmente automatizado
Identificar y mejorar los procedimientos de trabajo del operario, e incorporarlos al PNT.
Minimizar las horas-persona necesarias para la recuperación automatizando los trabajos que puedan sistematizarse.
Visualización del estado de los equipos
La visualización en tiempo real del estado de toda la planta y los equipos permite un funcionamiento eficaz y una respuesta rápida a las anomalías.
En el sitio Desafíos
- Control irregular de los equipos y dependencia de la mano de obra
- Inspección lenta debido a la gran extensión del emplazamiento
Soluciones
- Recopile automáticamente datos sobre el estado de los equipos en todo momento utilizando los sensores inalámbricos de fácil instalación
- Supervise el estado de los equipos en un cuadro de mandos y detecte señales anómalas con IA
Beneficios
- Reducir las horas-persona de inspección humana
- Estabilizar la calidad de la inspección mediante la cuantificación y visualización del trabajo de inspección
- Evitar fallos repentinos e inesperados de los equipos
Caso práctico de equipos rotativos
Supervisión de los datos de vibración en el salpicadero y detección de señales anómalas mediante IA.
Permiten supervisar las condiciones de los equipos mediante valores numéricos sin depender de la intuición y la experiencia de los profesionales.
Además, al utilizar el entorno de la nube, realizar el mantenimiento predictivo y la supervisión remota impulsados por IA. Tras detectar una anomalía, realice un diagnóstico preciso y tome las medidas adecuadas.
Instalación de sensores inalámbricos
Los datos de vibración de los equipos giratorios se recopilan automáticamente en todo momento, lo que elimina la necesidad de inspeccionar los equipos in situ en ubicaciones remotas.
1. Pasarela LoRaWAN
Recogida y transferencia de datos al servidor
2. Sensor Sushi
Medición de la temperatura y la vibración de la superficie
Planta Operación Plataforma de optimización
Utilizando Digital Twin para el procesamiento de datos en tiempo real y agentes autónomos de IA para la resolución de problemas, maximizar el uso de activos como equipos y apoyar a los responsables de la toma de decisiones en las operaciones de la planta, optimizando así las operaciones de la planta.
Marco propuesto por Yokogawa
AOM (Asset Gestión de Operaciones) se basa en tres pilares tecnológicos: Composability, AI/ML y Digital Twin. Unifica las operaciones, el mantenimiento, la fiabilidad y Ingeniería para alcanzar la excelencia operativa.
- Operaciones
Las operaciones garantizan el uso eficiente y eficaz de los activos - Fiabilidad
Mejorar la fiabilidad de los activos garantizando el cumplimiento de los parámetros de rendimiento previstos sin fallos durante un periodo determinado y en condiciones específicas. - Mantenimiento
El mantenimiento de los activos minimiza eficazmente el tiempo de inactividad y los costes asociados. - Ingeniería
Desarrollar y optimizar los diseños y procesos de los activos para garantizar la eficacia de las operaciones y el cumplimiento de las normas, así como para satisfacer las demandas operativas y las modificaciones futuras.
La IA pasa de asistir a los humanos a colaborar con ellos
Los agentes de IA no sólo realizan tareas especializadas para alcanzar objetivos empresariales, sino que también se comunican y coordinan con otros agentes de IA para mejorar la capacidad de resolución de problemas. Esto significa que los agentes de IA se comportan del mismo modo que lo han hecho hasta ahora los operadores y los ingenieros.
Pasos para lograr una minería inteligente
Optimizar el funcionamiento de la planta por etapas, empezando por el sistema Integración, para lograr seguridad, mejores índices de funcionamiento, mayor productividad, costes minimizados y gestión ESG.
¿En busca de información adicional sobre Yokogawa Iberia, tecnología y soluciones?
Contáctenos