Crear juntos un futuro sostenible para la química fina y especializada mediante la fabricación inteligente
Las especialidades químicas y los productos químicos finos de alto valor añadido son esenciales en todos los sectores, desde los materiales semiconductores hasta los componentes de automoción. Los fabricantes se enfrentan a retos de lanzamiento de la producción, estabilidad de la calidad y cumplimiento de la sostenibilidad que no pueden resolverse únicamente mediante la optimización individual.
Yokogawa aborda estos retos combinando mediciones centenarias Experiencia con modernas tecnologías de IA para promover la fabricación inteligente. A través de nuestra red de apoyo global, colaboramos con todo el ecosistema para crear soluciones sostenibles para el sector de la química fina y especializada.
Colabore con Yokogawa para lograr una fabricación sostenible que vaya más allá de los enfoques convencionales.
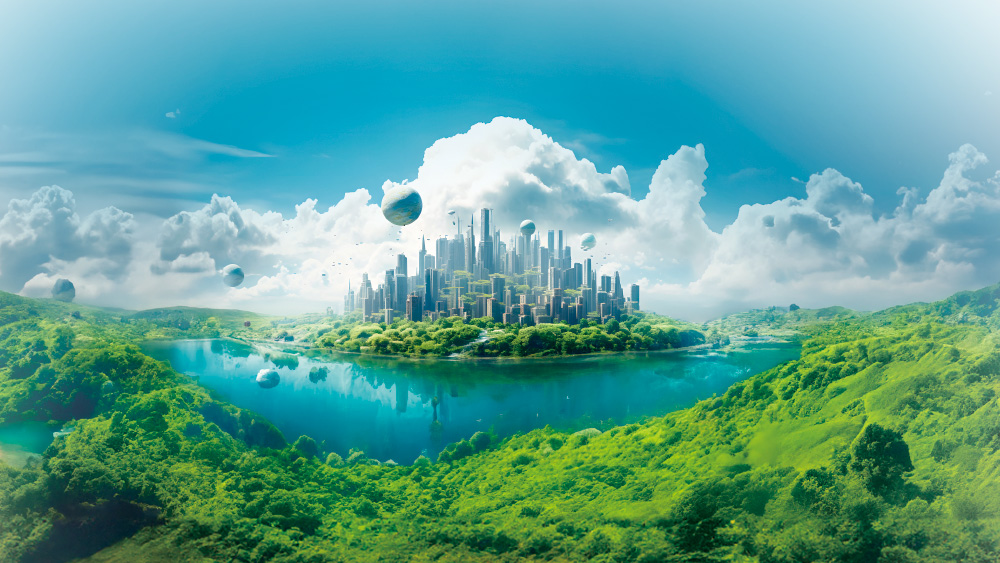
Fabricación inteligente
El futuro de la química fina y especializada evoluciona a través de Transformación Digital
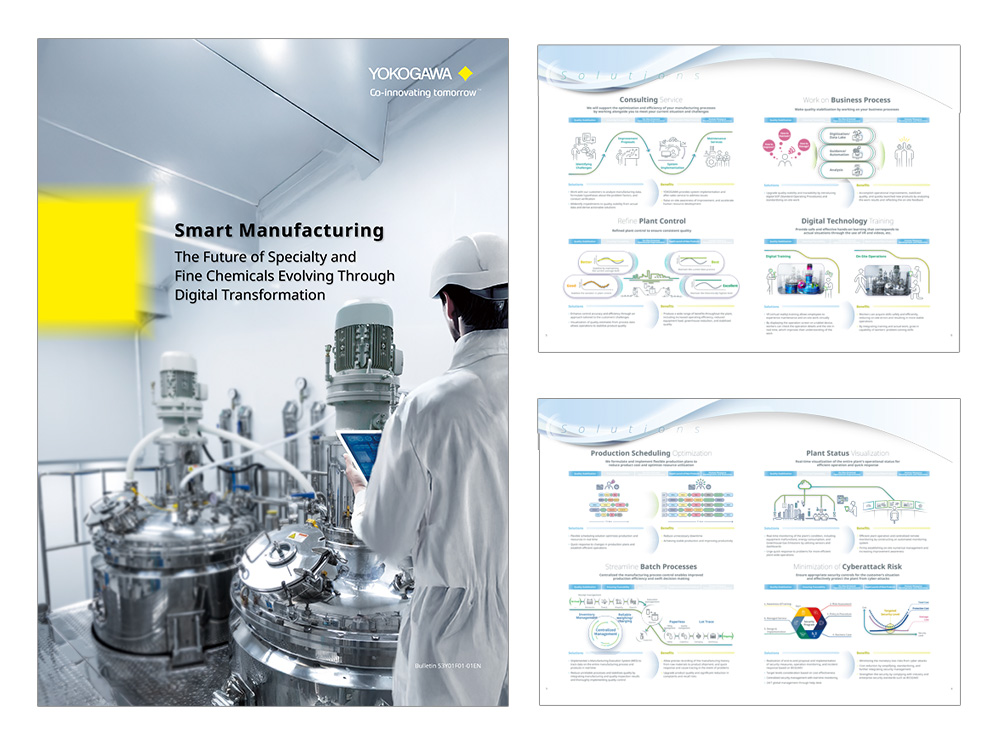
Industria Desafíos y el enfoque de Yokogawa
Eficiencia de los recursos
- Mejora de la productividad mediante el uso integrado de IA e IoT
- Optimización de la eficiencia mediante la utilización de datos
Responsabilidad medioambiental
- Reducción de las emisiones de dióxido de carbono
- Introducción a la energía limpia
Operaciones integradas
- Reforzar la colaboración en la cadena de suministro mediante Transformación Digital
Yokogawa Soluciones
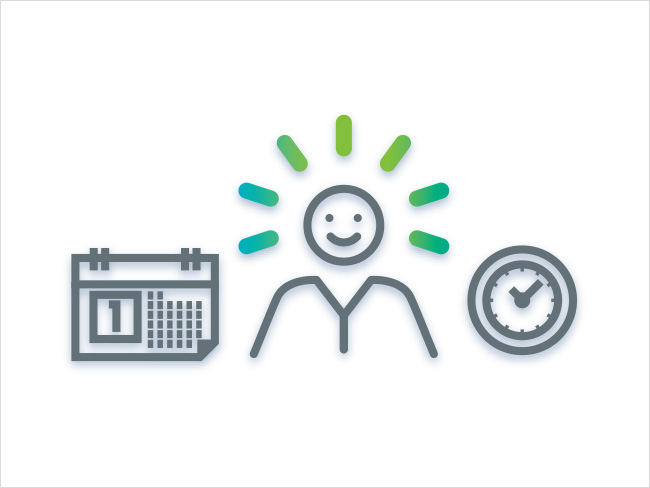
Optimización de la programación de la producción
Formulamos y aplicamos planes de producción flexibles para reducir el coste de los productos y optimizar la utilización de los recursos.
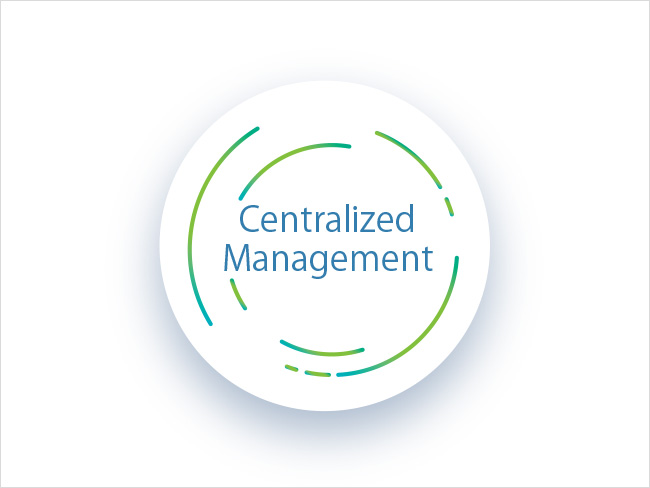
Racionalizar los procesos por lotes
La centralización del control del proceso de fabricación mejora la eficacia de la producción y agiliza la toma de decisiones.
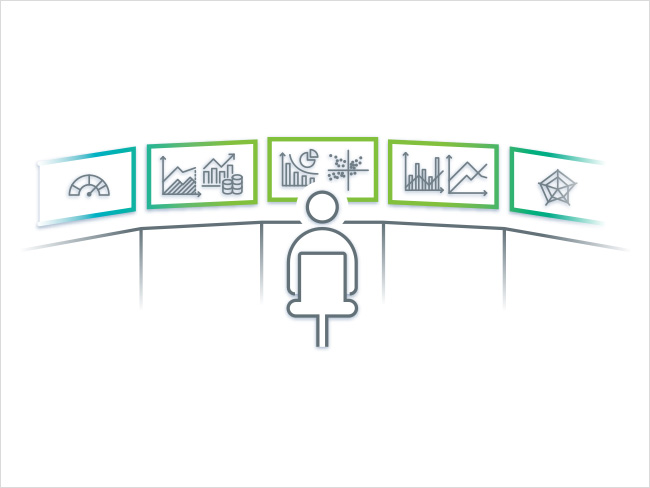
Visualización del estado de la planta
Visualización en tiempo real del estado operativo de toda la planta para un funcionamiento eficaz y una respuesta rápida
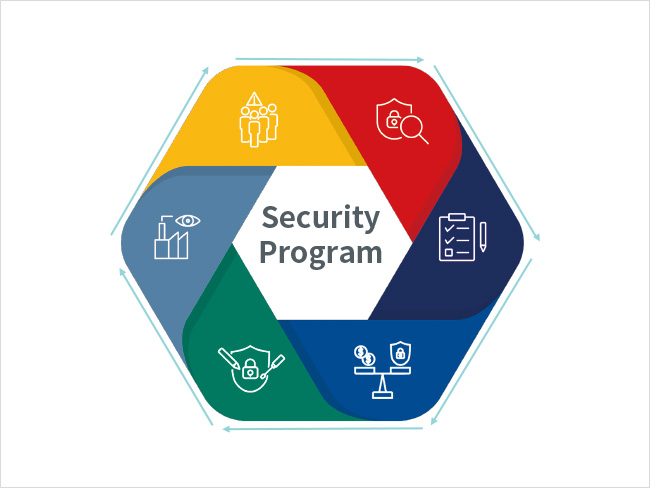
Minimización del riesgo de ciberataque
Garantizar controles de seguridad adecuados a la situación del cliente y proteger eficazmente la planta de ciberataques.
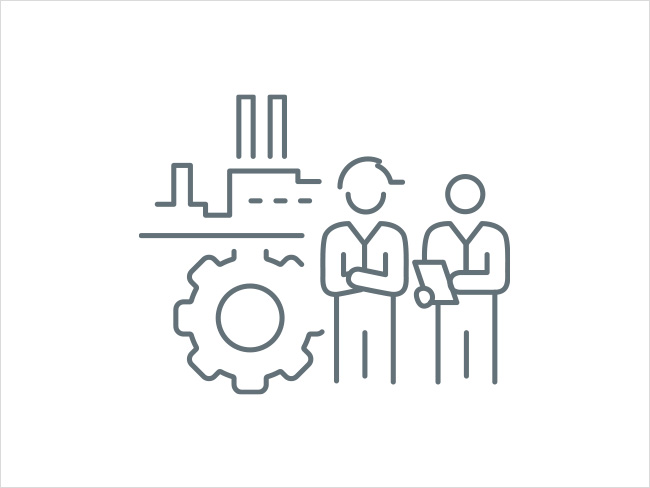
Consultar Servicio
Apoyaremos la optimización y eficiencia de sus procesos de fabricación trabajando junto a usted para responder a su situación y retos actuales
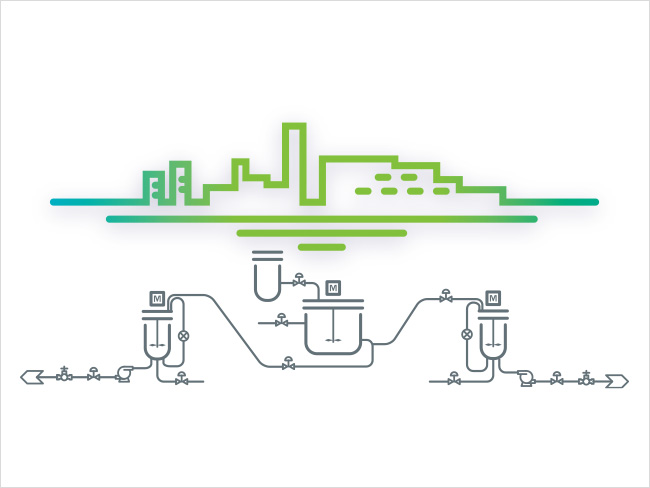
Refinar el control de las plantas
Control perfeccionado de la planta para garantizar una calidad constante
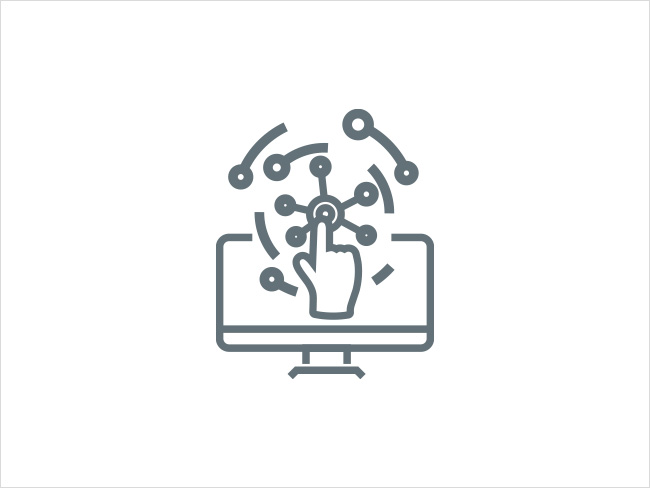
Trabajar en el proceso empresarial
Estabilice la calidad trabajando en sus procesos empresariales
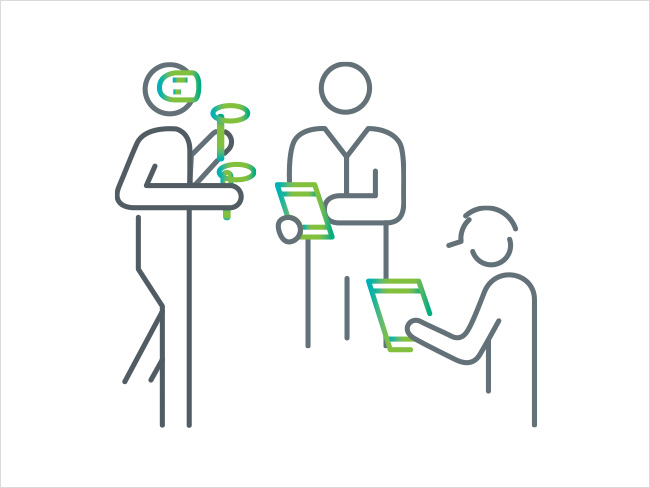
Formación en tecnología digital
Proporcionar un aprendizaje práctico seguro y eficaz que corresponda a situaciones reales mediante el uso de RV y vídeos, etc.
Optimización de la programación de la producción
Formulamos y aplicamos planes de producción flexibles para reducir el coste de los productos y optimizar la utilización de los recursos.
Soluciones
- Una solución de programación flexible optimiza la producción y los recursos en tiempo real
- Respuesta rápida a los cambios en los planes de producción y establecimiento de operaciones eficientes
Beneficios
- Reduzca los tiempos de inactividad innecesarios
- Lograr una producción estable y mejorar la productividad
Racionalizar los procesos por lotes
La centralización del control del proceso de fabricación mejora la eficacia de la producción y agiliza la toma de decisiones.
Soluciones
- Implantación de un sistema de ejecución de la fabricación (MES) para realizar un seguimiento en tiempo real de los datos de todo el proceso de fabricación y de los productos.
- Reduce los procesos poco fiables y estabiliza la calidad mediante la integración de los resultados de las inspecciones de fabricación y calidad y la aplicación exhaustiva del control de calidad.
Beneficios
- Permitir un registro preciso del historial de fabricación, desde las materias primas hasta el envío del producto, y una rápida respuesta y rastreo de causas en caso de problemas.
- Mejora de la calidad de los productos y reducción significativa de las reclamaciones y los riesgos de retirada.
Visualización del estado de la planta
Visualización en tiempo real del estado operativo de toda la planta para un funcionamiento eficaz y una respuesta rápida
Soluciones
- Supervisión en tiempo real del estado de la planta, incluidas las averías de los equipos, el consumo de energía y las emisiones de gases de efecto invernadero mediante sensores y cuadros de mando.
- Urge una respuesta rápida a los problemas para un funcionamiento más eficiente de toda la planta
Beneficios
- Funcionamiento eficiente de la planta y supervisión centralizada a distancia mediante la construcción de un sistema de supervisión automatizado.
- Establecer firmemente la gestión numérica in situ y aumentar la conciencia de mejora
Minimización del riesgo de ciberataque
Garantizar controles de seguridad adecuados a la situación del cliente y proteger eficazmente la planta de ciberataques.
Soluciones
- Realización de una propuesta de extremo a extremo y aplicación de medidas de seguridad, supervisión de operaciones y respuesta a incidentes basadas en la norma IEC62443.
- Consideración de los niveles objetivo en función de la rentabilidad
- Gestión centralizada de la seguridad con supervisión en tiempo real
- Gestión global 24/7 a través del servicio de asistencia
Beneficios
- Minimizar los riesgos de pérdidas monetarias por ciberataques
- Reducción de costes mediante la simplificación, normalización e integración de la gestión de la seguridad
- Refuerce la seguridad cumpliendo las normas de seguridad del sector y de las empresas, como la IEC62443.
Consultar Servicio
Apoyaremos la optimización y eficiencia de sus procesos de fabricación trabajando junto a usted para responder a su situación y retos actuales
Soluciones
- Trabajar con nuestros clientes para analizar los datos de fabricación, formular hipótesis sobre los factores problemáticos y llevar a cabo la verificación.
- Identificar los obstáculos a la estabilidad de la calidad a partir de datos reales y encontrar soluciones prácticas.
Beneficios
- Yokogawa proporciona servicios de implantación de sistemas y posventa para resolver problemas
- Aumentar la conciencia de mejora in situ y acelerar el desarrollo de los recursos humanos.
Refinar el control de las plantas
Control perfeccionado de la planta para garantizar una calidad constante
Soluciones
- Mejorar la precisión y la eficacia del control mediante un enfoque adaptado a los retos de los clientes.
- La visualización de las estimaciones de calidad en Datos de proceso permite estabilizar la calidad de los productos.
Beneficios
- Producen una amplia gama de beneficios en toda la planta, como una mayor eficacia operativa, una menor carga de los equipos, la reducción de los invernaderos y la estabilización de la calidad.
Trabajar en el proceso empresarial
Estabilice la calidad trabajando en sus procesos empresariales
Soluciones
- Mejorar la estabilidad de la calidad y la trazabilidad mediante la introducción de procedimientos normalizados de trabajo (PNT) digitales y la normalización del trabajo in situ.
Beneficios
- Lograr mejoras operativas, estabilizar la calidad y lanzar rápidamente nuevos productos analizando los resultados del trabajo y reflejando los comentarios in situ.
Formación en tecnología digital
Proporcionar un aprendizaje práctico seguro y eficaz que corresponda a situaciones reales mediante el uso de RV y vídeos, etc.
Soluciones
- La formación en RV (realidad virtual) permite a los empleados experimentar virtualmente el mantenimiento y el trabajo in situ
- Al visualizar la pantalla de operaciones en una tableta, los trabajadores pueden comprobar los detalles de la operación y el lugar en tiempo real, lo que mejora su comprensión del trabajo.
Beneficios
- Los trabajadores pueden adquirir habilidades de forma segura y eficiente, lo que reduce los errores in situ y da lugar a operaciones más estables.
- Integrando la formación y el trabajo real, aumentar la capacidad de los trabajadores para resolver problemas
Recursos
DIC Corporation ha desarrollado conjuntamente con Yokogawa la Plataforma de Utilización de Datos. La solución reduce drásticamente el trabajo de preparación de datos para Análisis de datos.
BASF Schwarzheide GmbH eligió el sistema de detección de cavitación de Yokogawa para detectar la cavitación de las bombas en una fase temprana.
El sistema de detección de cavitación detecta las fluctuaciones de presión mínimas generadas por la cavitación baja; los problemas se detectan antes de que se produzcan vibraciones.
Ube Corporation Europe y Yokogawa han creado conjuntamente la solución móvil Field Assistant.
Field Assistant innova la patrulla de inspección, la gestión de supervisión y la eficiencia de O&M en la planta.
¿En busca de información adicional sobre Yokogawa Iberia, tecnología y soluciones?
Contáctenos