Tanto si produce productos petroquímicos, inorgánicos o intermedios, está sometido a una presión constante de costes y márgenes para suministrar productos a sus clientes de forma puntual y eficiente, manteniendo al mismo tiempo unas operaciones seguras y conformes con la normativa. Además, tiene que ajustarse a los precios constantes de las materias primas y la energía y ser capaz de ofrecer al mercado la combinación de productos más rentable.
Yokogawa ha estado sirviendo al mercado de productos químicos a granel en todo el mundo y es el líder reconocido en este mercado. Con productos, soluciones y la industria Experiencia, Yokogawa entiende su mercado y las necesidades de producción y trabajará con usted para proporcionar una solución fiable y rentable a través del ciclo de vida de su planta.
Desafíos
Desafío del cliente
La industria química está altamente especializada, con plantas que producen productos intermedios, a partir de materias primas, que, a su vez, son utilizados por otras plantas como insumos en su producción de productos más avanzados. Cada empresa química debe considerar cuidadosamente su posicionamiento en un mercado altamente competitivo.
Nuestras soluciones
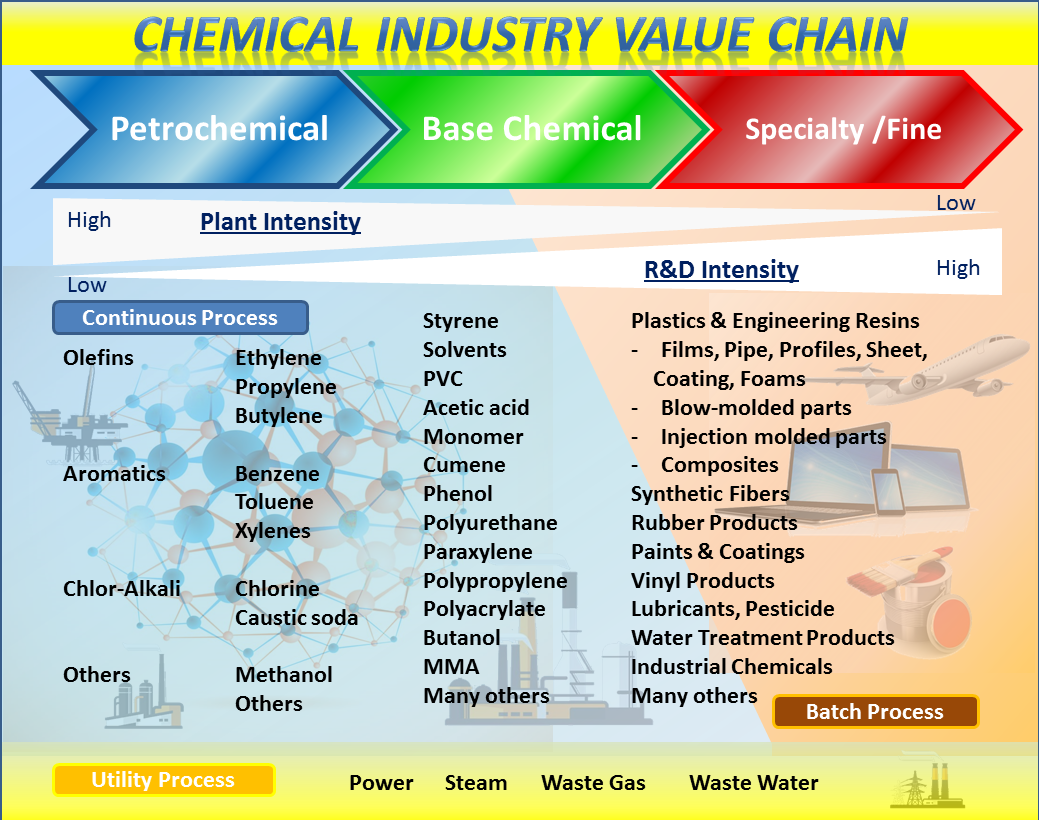
Los productos químicos básicos suelen producirse en un proceso continuo que requiere un sistema de control altamente fiable y robusto. También en este caso, el sistema de control de producción integrado CENTUM VP es la solución ideal, ya que permite un entorno de funcionamiento cómodo en respuesta a los requisitos del proceso y proporciona un entorno de conducción confortable con un control estable del proceso. La herramienta de navegación en línea Exapilot proporciona a los operarios un sólido apoyo para la ejecución fiable de operaciones no rutinarias, como el apagado y la puesta en marcha.
Tecnología instrumental
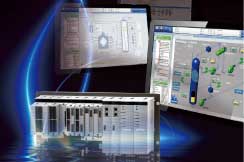
Producción Sistema de control: CENTUM VP
La base de datos única del Sistema Integrado de Control y Seguridad (ICSS) simplifica la ingeniería: los gráficos, las ventanas de alarma y las pantallas de estado del sistema tienen el mismo aspecto, lo que facilita el manejo.
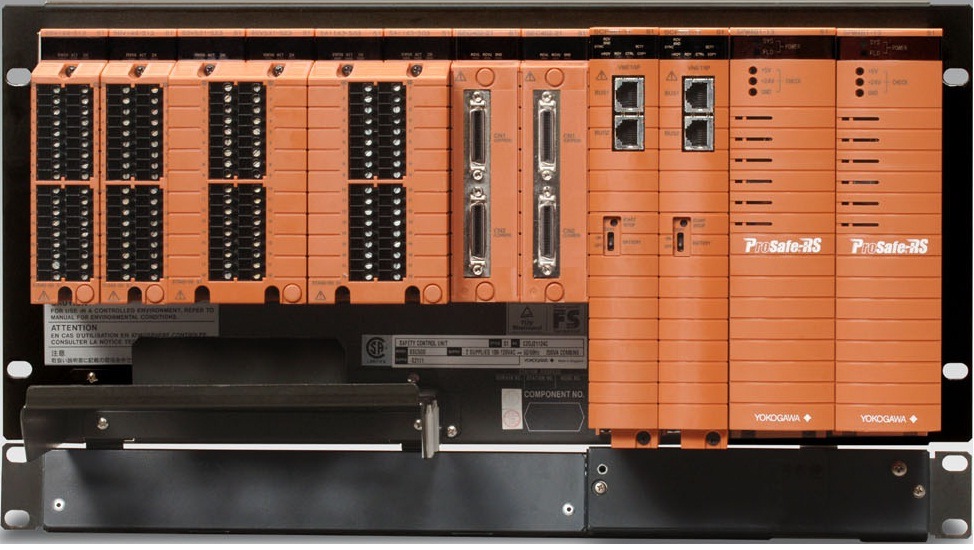
Sistema instrumentado de seguridad: Prosafe-RS
Yokogawa ofrece una gama completa de sistemas instrumentados de seguridad, desde los de estado sólido y cableados hasta los totalmente integrados DCS-SIS, que cubren todos los niveles de integridad de la seguridad (SIL 1 a 4) para la industria química.
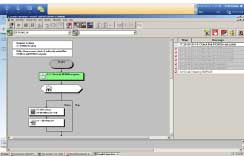
Operación Mejora de la eficiencia: Exapilot
Exapilot es una herramienta de navegación en línea que guía a los operarios paso a paso a través de los procedimientos operativos de la planta.
Utilizando Exapilot, se crean Procedimientos Operativos Estándar (o PNT) de forma estandarizada. Los PNT mejoran la eficiencia y reducen el coste total de propiedad al reducir o eliminar los errores humanos.
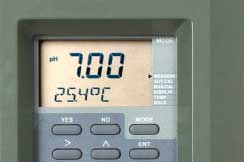
Analizador
Los sistemas analíticos de alta capacidad de respuesta contribuyen a la medición precisa de las propiedades de los productos/intermedios, ayudando a las empresas químicas a cumplir las normativas medioambientales y de control de calidad más estrictas.
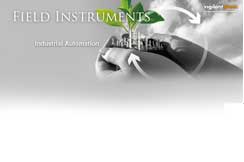
Instrumentos de campo
Los instrumentos digitales de campo "Instale y olvídese" ofrecen mediciones de procesos estables y precisas con un bajo coste de instalación, mantenimiento casi nulo e inteligencia de autodiagnóstico. Como auténtico líder en el sector de la automatización de procesos y sus tecnologías relacionadas, Yokogawa lanzó al mercado el primer dispositivo del mundo compatible con FOUNDATION fieldbus™ y, desde entonces, ha desarrollado una gama completa de instrumentación con los protocolos FOUNDATION fieldbus™, HART y Profibus, además de productos de comunicación inalámbrica compatibles con ISA100.11a.
Recursos
ENEOS Materials ha logrado con éxito el primer funcionamiento autónomo a largo plazo de una planta utilizando la IA de Yokogawa. FDKPP ahorra energía y reduce la carga de trabajo de los operarios, al tiempo que mantiene la calidad de fabricación.
- La introducción de CENTUM CS 3000 maximiza la productividad y mejora la calidad del producto en la fábrica de polímeros especiales.
- Una de las grandes satisfacciones de este proyecto es el enorme aumento de la eficacia de la recuperación del monómero de butadieno.
La sosa cáustica y el ácido clorhídrico, producidos en plantas electrolizadoras, son materiales fundamentales utilizados en diversas industrias: química, farmacéutica, petroquímica, papelera, etc. El beneficio es el resultado de una producción eficaz con un coste de funcionamiento/mantenimiento minimizado. Un control adecuado del proceso permite estabilizar la calidad de los productos y obtener grandes beneficios operativos.
Si un sensor no funciona, el fabricante no puede detectar la humedad en el cloro y debe detener el proceso. Por desgracia, los sensores pueden deteriorarse y ofrecer mediciones inexactas debido al contacto con el proceso.
Se consumen muchos tipos de gases en industrias tan variadas como la química, la alimentaria y de bebidas y la médica. Estos gases se suministran normalmente en forma líquida en camiones y se dispensan en las instalaciones del cliente. Aunque el caudal de gas licuado criogénico se utiliza con fines de facturación, no es fácil medirlo con precisión porque el gas está siempre a temperaturas de saturación.
Los tanques de almacenamiento se utilizan en una variedad de industrias que van desde el almacenamiento de petróleo crudo hasta el almacenamiento de materias primas para el monómero de cloruro de vinilo (VCM).
El gas amoniaco (NH3) se inyecta para eliminar los NOx y reducir así la concentración de NOx en los gases de combustión de la chimenea. Con los analizadores de NH3 convencionales que realizan mediciones de forma indirecta, las concentraciones de NH3 se obtienen a través de un sistema de muestreo. Por lo tanto, existen problemas con el mantenimiento y los costes de funcionamiento del sistema de muestreo, así como retrasos en la medición. El analizador láser TDLS8000 es la solución a todos estos problemas.
En este artículo se analizan ejemplos industriales reales en los que el sistema de servicios públicos de una refinería o planta petroquímica se optimiza con un software en tiempo real, en línea y de eficacia probada en la industria. Se comentan las experiencias adquiridas durante más de 20 años de proyectos industriales desplegados en todo el mundo (las referencias 1 a 10 se refieren a algunos proyectos recientes). Se explican los principales pasos del proyecto y se presentan los detalles críticos que hay que tener en cuenta para garantizar un uso satisfactorio y una transferencia de tecnología adecuada. En la ponencia se analizarán casos prácticos concretos.
Las grandes y complejas instalaciones industriales, como las refinerías y petroquímicas, son cada vez más conscientes de que los sistemas de energía deben gestionarse de forma óptima, ya que cualquier reducción de energía que las operaciones logren en las unidades de producción podría acabar desperdiciándose si el coste global del sistema de energía no se gestiona adecuadamente. Sin embargo, los ingenieros de procesos siempre han intentado desarrollar algún tipo de herramienta, muchas veces basada en hojas de cálculo, para mejorar la forma en que se gestionaban los sistemas de utilidades. El principal inconveniente de los intentos anteriores era la falta de datos: los ingenieros pasaban todo el día al teléfono o visitando las salas de control para recopilar información del historiador de datos del Sistema de Control Distribuido (DCS), procesarla en la hoja de cálculo y producir recomendaciones que, cuando estaban listas para ser aplicadas, estaban obsoletas y ya no eran aplicables.
En este artículo se describen los sistemas energéticos, los pasos para la implantación de Visual MESA y varias características del modelo, centrándose en el uso del software para el cálculo de los KPI relacionados con la energía. Se analiza el proyecto de implantación del EMS y se presentan también las principales conclusiones relativas a la reducción de los costes de explotación.
Se comentan las experiencias adquiridas durante más de 20 años de proyectos industriales desplegados en todo el mundo. Se explican los principales pasos del proyecto y se presentan los detalles críticos que hay que tener en cuenta para garantizar el éxito de su uso y la correcta transferencia de tecnología. En la ponencia se analizan casos prácticos concretos. También se presenta la aplicación en bucle abierto frente a la de bucle cerrado.
Rohm and Haas Company es uno de los mayores fabricantes mundiales de materiales especiales, como adhesivos, sellantes, revestimientos, monómeros, materiales electrónicos, soluciones inorgánicas y especiales y resinas de intercambio iónico. Fundada en 1909 por dos empresarios alemanes, Rohm and Haas ha crecido hasta alcanzar unos ingresos anuales de aproximadamente 6.000 millones de dólares.
Este artículo muestra cómo mejorar las operaciones de destilación centrándose en la automatización de los procedimientos. Se revisará la importancia de utilizar procedimientos en las operaciones de destilación y se destaca el trabajo de colaboración en curso entre Fractionation Research Inc. (FRI) y Yokogawa Corporation para mejorar las operaciones de procedimiento.
Los mundos de la automatización de procesos y la gestión de la producción llevan algún tiempo convergiendo. Lo que antes eran islas de funcionalidades de automatización y gestión de la producción conectadas a través de esquemas altamente propietarios Integración cuyo mantenimiento resultaba costoso, se han convertido en plataformas integradas que proporcionan un intercambio de datos sin fisuras entre el mundo de la automatización y la planta de producción, las funciones de gestión de la producción y las operaciones, y Integración con sistemas de nivel empresarial.
La migración del DCS de una refinería brindó la oportunidad de reconfigurar y consolidar las salas de control y el sistema de gestión operativa.
Julio de 2011
Las plantas de proceso funcionan de acuerdo con procedimientos operativos. Estos procedimientos consisten en un conjunto de tareas que se ejecutan de forma coherente para lograr un objetivo específico, como la puesta en marcha, el apagado o la transición de una unidad como parte de la fabricación de un producto.
Septiembre de 2008
Yokogawa ayuda a una gran planta química china a gestionar el transporte de productos por carretera, barco y tubería.
La actualización de la mina de mineral y refinería de Wyoming Trona de Yokogawa Centum CS3000 a CENTUM VP-R5 implicó dos dominios, 21 estaciones de control de campo RIO y FIO, 17 estaciones de operador, 6 estaciones Ingeniería y 8 servidores de planta diferentes.
CONTROL, enero de 2013
La metodología de automatización estándar mejora las operaciones y evita incidentes al permitir compartir las mejores prácticas entre los operadores.
ARC cree que mediante la implementación de la automatización de procedimientos, muchas plantas de proceso pueden minimizar la variabilidad para ayudar a garantizar transiciones de estado suaves, eficientes y seguras.
Descargas
Folletos
- Deliver Excellence and Create Success - To be the Leader in the Chemical Industry - (4.9 MB)
- Success Story Collection Chemical (Base Chemical, Fertilizer, Petrochemical) (7.6 MB)
- Electrolyzer Solution Instruments and Solution for Ion-Membrane Electrolyzer Plant Application (3.4 MB)
- Solutions for the Chemical Operations Executive (2.0 MB)
- Differential Pressure Level Solutions (8.0 MB)
¿En busca de información adicional sobre Yokogawa Iberia, tecnología y soluciones?
Contáctenos