Las plantas químicas dependen de procesos de producción continuos y discontinuos, cada uno de los cuales plantea requisitos diferentes para un sistema de control. Un proceso continuo exige un sistema de control robusto y estable que no falle y provoque la parada de una línea de producción, mientras que en un proceso por lotes se hace hincapié en disponer de un sistema de control que permita una gran flexibilidad a la hora de realizar ajustes en fórmulas, procedimientos y similares. Ambos tipos de sistemas necesitan disponer de un historial de calidad del producto y poder ejecutar operaciones no rutinarias. Con su amplia cartera de productos, sus experimentados ingenieros de sistemas y su red mundial de ventas y servicios, Yokogawa tiene una solución para cada proceso de planta.
-
Base Química
Yokogawa ha estado sirviendo al mercado de productos químicos a granel en todo el mundo y es el líder reconocido en este mercado. Con productos, soluciones y la industria Experiencia, Yokogawa entiende su mercado y las necesidades de producción y trabajará con usted para proporcionar una solución fiable y rentable a través del ciclo de vida de su planta.
-
Química fina y especializada
Esta página presenta los mensajes y soluciones de Yokogawa para la industria de la química fina y especializada, mostrando nuestras ofertas especializadas y Experiencia.
-
Biocarburante
Para combatir el calentamiento global, la producción y el consumo de biocombustibles están aumentando en todo el mundo. Como proveedor líder de soluciones de medición y control para las industrias química y petrolera, entre otras, Yokogawa ha desarrollado tecnologías que pueden utilizarse para garantizar la producción fiable y eficiente de bioetanol y otros tipos de combustibles renovables.
-
Granel y petroquímica
Tanto si producen productos petroquímicos como inorgánicos o intermedios, las empresas químicas están sometidas a presiones de costes y márgenes para suministrar productos de forma puntual y eficiente, manteniendo al mismo tiempo unas operaciones seguras y conformes con la normativa. Además, las empresas químicas tienen que adaptarse a las fluctuaciones de los precios de las materias primas y la energía y ofrecer al mercado la combinación de productos más rentable.
Yokogawa ha estado atendiendo las necesidades de automatización del mercado de productos químicos a granel en todo el mundo y es el líder reconocido en este mercado. Con productos, soluciones y la industria Experiencia, Yokogawa entiende su mercado y las necesidades de producción y trabajará con usted para proporcionar una solución fiable y rentable a través del ciclo de vida de su planta.
Detalles
Cadena de valor de la química Industria
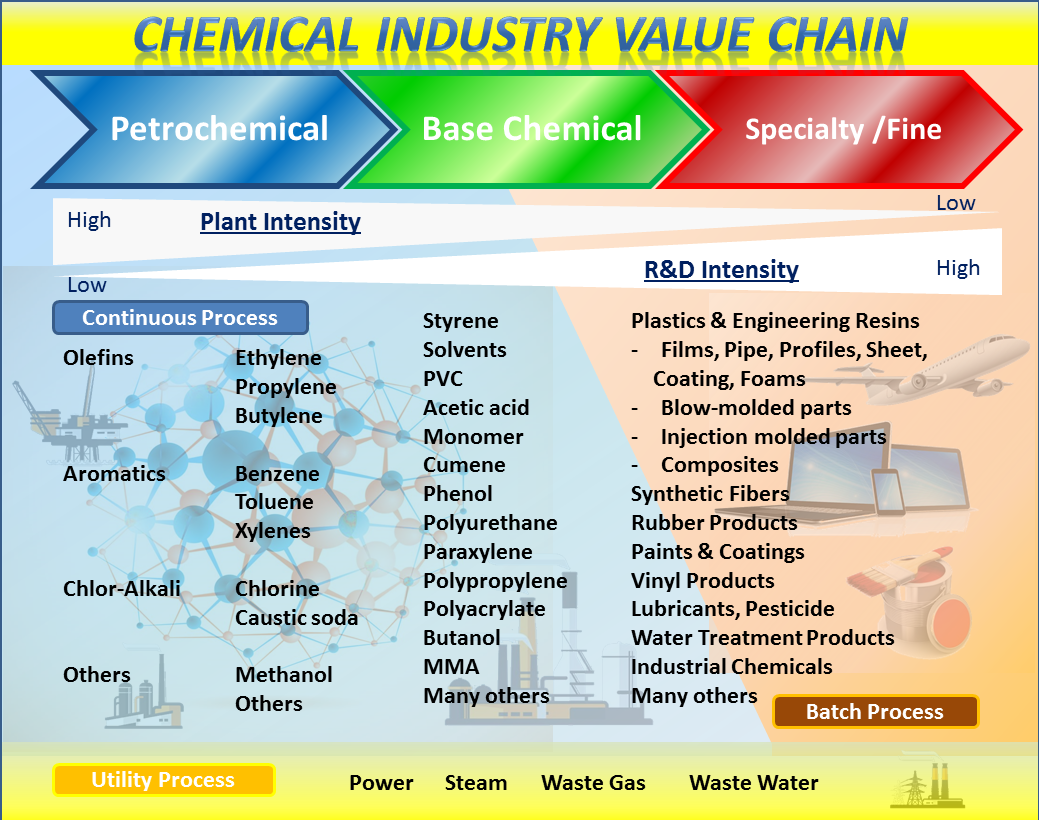
Yokogawa Electric Corporation / Corporación Eléctrica Yokogawa lanzó el primer DCS del mundo en 1975, que rápidamente se hizo popular entre muchos clientes de la industria química de todo el mundo. Yokogawa ha contribuido así al funcionamiento seguro y estable de las plantas de los usuarios como proveedor líder de soluciones de control de procesos en esta industria.
Dado que los procesos, productos y Cadena de Valor de la industria química son cada vez más complejos y sofisticados, también lo son los requisitos de los clientes. Yokogawa sigue ofreciendo soluciones y servicios industriales para satisfacer esas necesidades aprovechando su gran experiencia y Experiencia en este campo. También hemos lanzado varias soluciones nuevas, como la gestión de la energía, para optimizar el funcionamiento de las plantas.
Yokogawa seguirá respondiendo a las expectativas de los clientes de la industria química proporcionando soluciones de automatización de vanguardia como proveedor integral.
Excelencia en la producción
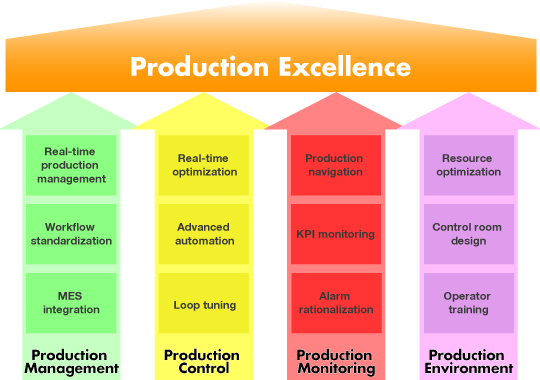
Gestión de la Producción
- MES Integración
En el ámbito de los sistemas de ejecución de la fabricación (MES) se incluyen diversos sistemas individuales que realizan funciones de programación y de otro tipo. La conectividad entre sistemas es un factor clave fundamental para una gestión ágil de la producción. - Normalización del flujo de trabajo
Los flujos de trabajo de producción deben definirse y supervisarse para una gestión fiable de la producción. La estandarización de los flujos de trabajo es especialmente eficaz en empresas con múltiples centros de producción. - Gestión de la producción en tiempo real
La gestión global de la producción en tiempo real es necesaria para acelerar el ciclo de producción planificar-hacer-comprobar-actuar (PDCA).
Control de producción
- Ajuste del bucle
El control de identificación de procesos (PID) desempeña un papel fundamental en el control de procesos. Una sintonización adecuada es necesaria para un control estable del proceso y es un requisito previo para el control de nivel avanzado. - Automatización avanzada
El control avanzado de los procesos y los sistemas de navegación basados en el conocimiento son elementos clave de una operación bien automatizada. - Optimización en tiempo real
La optimización de toda la planta puede lograrse con un optimizador en tiempo real que utilice cálculos rigurosos de modelos.
Control de la producción
- Racionalización de las alarmas
Ingeniería Se recomienda un enfoque de Gestión de alarma basado en la conocida directriz nº 191 de la asociación de usuarios de equipos y materiales (EEMUA). El análisis de la causa raíz de las alarmas también es un método eficaz para racionalizarlas con éxito. - Seguimiento de los KPI
Cada persona debe supervisar una amplia variedad de indicadores clave de rendimiento (KPI). El seguimiento de los KPI requiere compararlos con los objetivos y obtener información detallada. - Navegación de la producción
Las tareas de producción deben ser gestionadas correctamente por el sistema. La supervisión del progreso de las tareas es un valioso puente entre la planificación y la fabricación que facilita la cooperación en la gestión de la producción.
Entorno de producción
- Formación de operadores
Los sistemas de formación de operarios les permiten adquirir experiencia en el manejo de diversas situaciones, como el mal funcionamiento de los equipos y la realización de puestas en marcha y otras operaciones rutinarias. Ayuda a los operarios a mejorar sus conocimientos. - Diseño de salas de control
El diseño de la sala de control debe tener en cuenta todos los aspectos del entorno de trabajo, como la ergonomía, la seguridad, la facilidad de comunicación, la funcionalidad, la automatización de los sistemas y la política empresarial. - Optimización de recursos
Para que el entorno de producción sea eficaz, es conveniente disponer de una dirección central Sala de control. Todas las unidades relacionadas con la producción deben estar situadas cerca para garantizar una buena comunicación. Además de centralizar la Sala de control, se puede considerar la optimización de los recursos humanos y otras actividades para alcanzar la excelencia en la producción.
Recursos
Implementación de CENTUM VP a gran escala para ayudar al control de una planta sucroenergética
- La introducción de CENTUM CS 3000 maximiza la productividad y mejora la calidad del producto en la fábrica de polímeros especiales.
- Una de las grandes satisfacciones de este proyecto es el enorme aumento de la eficacia de la recuperación del monómero de butadieno.
- La PRM permite un enfoque de mantenimiento preventivo en el que el mantenimiento puede programarse y realizarse antes de que falle un Dispositivo de campo.
- Exaquantum recoge los datos de la planta en CENTUM VP para generar diversos informes sobre el proceso de polimerización.
Syngenta se propuso promover la agricultura sostenible como responsabilidad social a través de Transformación digital. Syngenta seleccionó Yokogawa para iniciar el viaje de la fabricación inteligente Transformación.
Kuraray Engineering proporciona la solución IoT big Análisis de datos en colaboración con Yokogawa.
El proceso colaborativo Análisis de datos logró un alto nivel de estabilización de la calidad en las instalaciones de un cliente.
Osaka Gas Chemicals eligió Yokogawa para resolver un antiguo problema en el proceso de fabricación de fibra de carbono.
Osaka Gas Chemicals estableció un método único de resolución de problemas utilizando la solución analítica Datos de proceso de Yokogawa.
Nippon Sanso Vietnam JSC (NSVN) equipó un sistema digitalizado de gestión de la cadena de suministro para optimizar la eficiencia del suministro de gases industriales.
El ODMS (sistema de gestión de entrega de pedidos) se desarrolló rápidamente utilizando el enfoque ágil de DevOps en colaboración con NSVN y Yokogawa.
- Sumitomo Seika logró la estabilización de la calidad mediante un proyecto interdepartamental.
- La fusión del conocimiento de los procesos y la tecnología de Análisis de datos fue la clave del éxito.
- A partir de una revisión minuciosa de todos los procedimientos operativos y las funciones de los operarios, se han configurado nuevos procedimientos operativos normalizados en Exapilot.
- Como resultado, SFC ha podido reducir la carga de trabajo de los operarios, mejorar la calidad del producto y reducir las pérdidas de producción.
La introducción de eServ ha dado lugar a un sistema centralizado de información sobre las instalaciones. El motivo de la pérdida de oportunidades de producción ha quedado claro, y todos los miembros han podido hacer un seguimiento de la marcha de las medidas.
El simulador de formación de operadores ayuda a mejorar la fiabilidad humana en una joven planta de PetroVietnam Ca Mau Fertilizer.
PVCFC y Yokogawa implantaron en equipo el sistema OTS de control y seguridad para terceros.
- En una nueva planta química de carbón de China se logró un funcionamiento estable y un mantenimiento proactivo.
- Yokogawa garantizaron el éxito y la eficacia de la puesta en marcha.
- Nan Ya había estado utilizando Yokogawa Micro-XL DCS desde que la planta abrió sus puertas en la década de 1990.
- La migración paso a paso de Micro-XL a CENTUM VP reduce al mínimo el tiempo de inactividad.
Ube Corporation Europe y Yokogawa han creado conjuntamente la solución móvil Field Assistant.
Field Assistant innova la patrulla de inspección, la gestión de supervisión y la eficiencia de O&M en la planta.
- Sistema heredado sustituido por Yokogawa CENTUM VP y ProSafe-RS en la planta de PTA de Indonesia.
- Parámetros PID importados a CENTUM VP sin cálculos complejos.
- Excelencia operativa mediante la maximización de activos, utilizando DCS, SIS, analizadores y Instrumentos de campo de Yokogawa.
- CENTUM VP PCS y ProSafe-RS SIS se integraron utilizando el mismo entorno Ingeniería.
- Cerca de 60 cromatógrafos de gases y un gran número de otros tipos de analizadores en varias casas de analizadores.
El proyecto AFCO es una muestra de la buena coordinación entre Yokogawa Oriente Medio, Yokogawa Tailandia, Yokogawa Singapur y Yokogawa Electric Corporation / Corporación Eléctrica Yokogawa. Yokogawa Las sedes de Oriente Medio y Yokogawa participaron en la ejecución del proyecto.
- Yokogawa proporciona soluciones CENTUM CS 3000, Exaquantum y PMR para el mayor complejo refino-petroquímico de China.
- La gestión de los datos de proceso por Exaquantum es una cuestión clave en el complejo petroquímico.
- Con el sistema CENTUM CS 3000, se calculan y analizan muchos tipos de índices de rendimiento clave de la planta para producir nuevas mejoras.
- Durante la puesta en marcha de la planta, PRM ayuda a los ingenieros del cliente a realizar todas las comprobaciones del bucle.
- En este proyecto se aplicó el concepto de proveedor principal de instrumentos (MIV) para reducir el coste total del proyecto Ingeniería.
- Constaba de DCS, SIS, todos los instrumentos, válvulas de control y sistema de medición de tanques en colaboración con el consultor de gestión de proyectos (PMC) y EPC.
- La integración de CENTUM CS 3000 con ProSafe-RS mejora la seguridad y fiabilidad de la planta.
- Yokogawa gestiona más de 500 dispositivos de campo HART, incluidas válvulas de control.
- CENTUM CS 3000 El sistema de control de la producción contribuye a una producción fluida de HDPE.
- El reto de este proyecto de sustitución consistía en terminar las obras y poner en marcha el nuevo sistema CS 3000 lo antes posible, reduciendo al mínimo el tiempo de inactividad.
- CS 3000 controla y supervisa eficazmente el proceso de gasificación del carbón.
- Una vez que el operador selecciona "Arrancar", se envían las instrucciones necesarias a todos los equipos de la planta a través del control de secuencia.
- Rápida implantación de CENTUM CS 3000 integrado y ProSafe-RS.
- El sistema CENTUM CS 3000, de gran fiabilidad, también ha ayudado a TOL a mantener una alta productividad en esta planta.
- La migración de Micro-XL y CENTUM CS 1000 a CENTUM CS 3000 mejora la fiabilidad.
- Las operaciones de esta planta, que funciona más de 330 días al año, se gestionan cuidadosamente mediante el DCS CENTUM CS 3000 y el paquete CS Batch.
- Un sistema certificado Parada de emergencia
- Reducción sustancial de los trabajos de mantenimiento
- Configuración del sistema que ocupa menos espacio
- Escalabilidad del sistema
- CS Batch se utiliza para automatizar una amplia gama de procesos por lotes y procesos multiproducto/multirruta de Reichhold.
- Con PRM, los ingenieros de procesos pueden conocer inmediatamente el estado de cada Dispositivo de campo sin tener que realizar una inspección in situ.
- Cumplen las normas de seguridad funcional IEC 61508/JIS C 0508
- Introducir proactivamente tecnologías punteras
- Cumplir los requisitos de seguridad, fiabilidad y facilidad de mantenimiento del licenciante de la planta.
- Mejorar las funciones de supervisión y explotación del sistema Parada de emergencia
Samsung Petrochemical Co. Ltd. (SPCL) (SPCL), una importante empresa petroquímica coreana, produce 700.000 toneladas anuales de ácido tereftálico purificado (PTA) en su planta de Daesan. El PTA, una sustancia en polvo blanco que se produce oxidando y refinando paraxileno, es un precursor del tereftalato de polietileno (PET), un material de poliéster que tiene una excelente resistencia térmica y al desgaste y se utiliza ampliamente como sustituto de las fibras de algodón natural y en envases de película, botellas de bebidas, cuerdas de neumáticos, pinturas, adhesivos y otras aplicaciones.
- La instalación del paquete Exaquantum PIMS mejora la eficacia de la gestión de Datos de proceso.
- Mejorar la calidad y el rendimiento mediante el mantenimiento proactivo de los activos de la planta.
- CENTUM CS 3000 Sistema de control distribuido para controlar la planta de etanol y sus calderas de servicios públicos
- Procesos por lotes que requieren un cuidadoso control automatizado para obtener la máxima eficacia y calidad del producto
- CENTUM VP Batch sustituye al sistema anterior y mejora la eficacia de la producción en la planta de acrílico.
- CENTUM La capacidad VP Batch puede manejar la gestión Receta a la gestión de informes Batch y la gestión de unidades.
- CENTUM El paquete VP Batch mejora la productividad.
- Reducción de la carga de trabajo del operario y funcionamiento seguro.
- Migración del sistema de la planta de polietileno de PetroChina Dushanzi Petrochemicals.
- La renovación incluyó la difícil creación de especificaciones de diseño de funciones (FDS), así como de FAT y SAT.
- CENTUM CS 3000, de gran fiabilidad, sustituye al sistema anterior y automatiza el funcionamiento de la planta de procesamiento por lotes.
- Trabajando juntos, el personal del proyecto de Hanwha Chemical y Yokogawa Korea completó este trabajo a tiempo y según lo previsto.
- Yokogawa proporciona STARDOM y FAST/TOOLS para la planta piloto de biomasa.
- FAST/TOOLS es una solución SCADA "todo en uno" que funciona como historiador de datos.
- Implementación de controladores optimizadores multivariables y estimadores de calidad robustos en un plazo récord
- Se espera un aumento del 3% en el importe de los piensos para RCC
- Introducción de la tecnología de bus de campo para realizar un mantenimiento predictivo y preventivo.
- ISAE para mejorar la fiabilidad del diagnóstico y la parametrización, utilizando los datos recogidos por la PMR.
- Como principal contratista de automatización (MAC) para este proyecto de construcción de la planta, Yokogawa Brasil diseñó, instaló y encargó una solución integrada de control e instrumentación.
- A Yokogawa Brasil concluiu o comissionamento desses sistemas antes do previsto e a produção do polímero verde foi iniciada apenas uma semana depois
- Kaneka Corporation ha necesitado urgentemente aplicar contramedidas que reduzcan los costes energéticos de esta instalación.
- La optimización de la estrategia de control ayuda a la planta BTG a ahorrar energía y funcionar con mayor eficiencia.
- Yokogawa 's CENTUM VP y PRM mejoran la eficiencia de la nueva planta de nailon de Tailandia.
- En la fase de puesta en marcha de la planta, se utilizó PRM junto con FieldMate para comprobar a fondo todos los bucles.
- En la planta de resina de la empresa en Ulsan, seis servidores Exaquantum estaban conectados a CENTUM CS 3000 y a los sistemas de otros proveedores.
- KKPC necesitaba ampliar sus capacidades de SBC y mejorar la eficiencia de la producción en sus plantas.
- CENTUM CS 3000 y Exaquantum PIMS mejoran la eficacia de la producción en una planta china de caucho sintético.
- Exaquantum proporciona datos sobre las tendencias a largo plazo necesarios para introducir mejoras en los procesos de la planta.
- Hasta el 90% de las tareas manuales pueden realizarse ahora automáticamente.
- Aumento de la productividad mediante procedimientos de puesta en marcha y cambio de carga parcialmente automatizados.
- 16.000 dispositivos FOUNDATION Fieldbus
- Contratista principal de automatización (MAC)
- Concepto DCS anywhere Integración con el sistema SAP del centro
- Contrato de mantenimiento a largo plazo
- Desarrollo sostenible
- El proyecto de reinstrumentación de la planta de HDPE sustituyó los instrumentos neumáticos y PLC heredados por CENTUM CS 3000 PCS y ProSafe-RS SIS integrados.
- Los dispositivos de campo HART pueden supervisarse desde la central Sala de control con el paquete de gestión de recursos de planta (PRM), lo que permite un enfoque de mantenimiento más predictivo y proactivo que reduce el coste total de propiedad.
- Interfaz de usuario única para el DCS y el NCS
- Ciclo rápido y controlable Integración
- Solución de control de compresores híbridos de alta velocidad
- Reducción de los gastos operativos para el funcionamiento del compresor mediante la sustitución de PLC antiguos y obsoletos por una moderna plataforma de control híbrida.
- Toda la logística de materias primas, productos intermedios y productos finales está controlada y gestionada por MAS.
- MAS permite la excelencia operativa gracias a su interfaz perfecta con el sistema de planificación de recursos empresariales.
- Implantación del paquete AOA para mejorar los cambios de rasante
- Reducción drástica de la carga de trabajo de los operarios y de los productos transitorios, así como de los conocimientos operativos compartidos.
- El trabajo se basó en una hoja de ruta previamente formulada con listas de comprobación detalladas para cada armario de control, estación de proceso y componente de red.
- El uso sin fisuras de la misma HMI para PCS y SIS, y la mejora de la seguridad y la integridad.
- Exapilot automatiza el proceso de descoordinación comlex y no rutinario de las NCU.
- La carga de trabajo de los operadores se ha reducido drásticamente.
- Exapilot se construyó como un sistema e-SOP basado en los procedimientos operativos estándar y en los conocimientos técnicos de operadores experimentados.
- El sistema e-SOP mejoró la calidad y la productividad en la planta de productos químicos de alto rendimiento de China.
A medida que aumenta la demanda de alimentos en todo el mundo, los fertilizantes desempeñan un papel esencial en la mejora de la productividad agrícola. OCI Nitrogen (en adelante OCI) es uno de los principales productores de fertilizantes minerales y el mayor productor mundial de melamina, que se utiliza para fabricar adhesivos y resinas para una amplia gama de aplicaciones, como paneles para muebles, suelos laminados, revestimientos, pinturas y plásticos.
Tsurumi Soda Corporation,Yokohama,Prefectura de Kanagawa, Japón
- IFCo eligió el sistema de formación de operarios de Omegaland para prepararse para una puesta en marcha impecable y segura de la planta.
- Omegaland contribuye a la formación de los operarios antes de la finalización de la planta de fertilizantes.
Yokogawa CENTUM VP y SIS fueron seleccionados para el proyecto de ampliación de las instalaciones BTX de Evonik Oxeno.
CENTUM proporciona la transparencia operativa y un diagnóstico más eficaz de los compresores, que son el corazón de la instalación.
Yokogawa ayudó al cliente a identificar lo que necesitaba para protegerse de los ciberataques.
Al "visualizar" el tráfico de red en el sistema de control, el cliente pudo detectar comunicaciones no autorizadas en su sistema.
- Una planta petroquímica japonesa aprovecha los dispositivos de campo inteligentes compatibles con FDT/DTM y el sistema de gestión de activos PRM de Yokogawa para mejorar la eficiencia del mantenimiento.
- El cliente pretende mejorar aún más la eficiencia del mantenimiento introduciendo el mantenimiento basado en la condición (CBM).
- Yokogawa colaboró en la ejecución del proyecto mediante la revisión del diseño, las modificaciones de los cálculos, la puesta en servicio previa, la formación de operarios e ingenieros, la puesta en servicio y la revisión posterior a la ejecución.
- Shell Global Solutions y Shell Deer Park Management quedaron plenamente satisfechos con la forma en que se llevó a cabo el proyecto y con los resultados obtenidos.
- TOK decidió iniciar la producción local de fotorresistencias de alta calidad para la fabricación de semiconductores cerca de sus clientes en Taiwán.
- El MES con trazabilidad comparable a la fabricación farmacéutica es uno de los factores para ganarse la confianza de sus clientes.
- Yokogawa mejoró el rendimiento de la automatización de la planta química.
- El estrés de los operarios se redujo drásticamente al identificar las causas de las excesivas intervenciones manuales.
- Yokogawa unió fuerzas con Air Liquide para co-innovar el plan de renovación paso a paso basado en los requisitos específicos de Air Liquide.
- El cliente se mostró satisfecho de que Yokogawa fuera capaz de entregar sus soluciones a tiempo y dentro del presupuesto.
- FieldMate, compatible con FDT, gestiona una amplia variedad de instrumentos de proceso digitales de múltiples proveedores.
- Los ingenieros del SNF pueden gestionar el ciclo de vida completo de los activos y configurar los dispositivos mediante FieldMate.
- La aplicación de control avanzado de procesos implantada en la unidad de MEG de Scotford ayudó a controlar la planta con menos variaciones, lo que permitió maximizar la producción de TEG y reducir el consumo total de vapor.
- Los aumentos de producción de TEG fueron superiores a los estimados inicialmente y los precios del vapor y el TEG utilizados en el estudio posterior a la aplicación se redujeron considerablemente.
- Kuraray EVAL y Yokogawa se prepararon cuidadosamente para la ampliación y modernización del sistema CENTUM.
- La gestión de más de 400 instrumentos de bus de campo por parte de Yokogawa 's PRM plant resource manage también contribuyó a que el proyecto se desarrollara sin contratiempos.
La serie TC de controladores de temperatura es perfecta para controlar la temperatura de calentamiento de las piezas de sellado y la temperatura de los rodillos de sellado (precalentamiento) en una gran variedad de maquinaria de envoltura.
La supervisión remota de las condiciones de la bomba de suministro en el proceso de agitación reduce las vueltas del operario y contribuye a estabilizar la calidad del producto.
Mejora de la productividad mediante la visualización de las variaciones de temperatura en el interior del reactor
Control de la distribución de la temperatura del horno de secado del separador/electrodo (aplicaciones de baterías de iones de litio para vehículos)
En las plantas de los fabricantes de alimentos y bebidas, hay ocasiones en las que es necesario supervisar y registrar los equipos de producción dentro de las salas blancas. Esta es una introducción a la supervisión y el registro en salas blancas mediante registradores sin papel.
La configuración del transmisor de nivel DP puede llevar mucho tiempo. Yokogawa Los transmisores de presión DPharp EJA/EJX reducen las horas de trabajo gracias a la función de configuración de nivel inteligente.
Los operarios deben recibir información de diagnóstico antes de que un bloqueo de línea provoque una avería. Yokogawa proporciona diagnósticos predictivos basados en el análisis de tendencias del factor de bloqueo, lo que mejora la eficacia del mantenimiento y reduce sus costes.
Presenta un sistema que utiliza comunicaciones Ethernet para adquirir valores medidos, valores objetivo y valores de salida de control desde un controlador instalado in situ a un PLC a gran velocidad (diez unidades en un segundo).
Control del estado de la pared del reactor/horno con un sensor de temperatura de fibra óptica
Si un sensor no funciona, el fabricante no puede detectar la humedad en el cloro y debe detener el proceso. Por desgracia, los sensores pueden deteriorarse y ofrecer mediciones inexactas debido al contacto con el proceso.
Últimamente están aumentando en todo el mundo las legislaciones sobre contaminación atmosférica, como la Ley de Aire Limpio (Clean Air Act), para reducir la cantidad de contaminación atmosférica. La Ley de Aire Limpio aborda numerosos problemas de calidad del aire. Uno de estos problemas es la lluvia ácida causada por las emisiones de dióxido de azufre y óxido de nitrógeno procedentes de centrales eléctricas alimentadas con combustibles fósiles y otras fuentes industriales y de transporte.
Cómo el mapa de ruido automatizado en tiempo real puede contribuir a la eficiencia de la producción
Los GX20 y GX90UT ofrecen una función de cálculo del valor medio que los hace ideales para controlar la temperatura y otros fenómenos fluctuantes. El estado de funcionamiento puede controlarse en tiempo real, lo que permite reducir los costes de explotación.
En los sistemas de desulfuración de gases de combustión que utilizan lodos de hidróxido de magnesio (Mg(OH) 2), el consumo del agente de desulfuración (Mg(OH)2) se controla utilizando analizadores de pH en línea. Una gran preocupación en la medición del pH es la fuerte tinción de los electrodos de pH por la lechada de Mg(OH) 2 . Para garantizar una medición precisa, es necesario limpiar frecuentemente los electrodos con un ácido, lo que aumenta tanto la carga de trabajo de mantenimiento como el coste.
Industria:Química, Energía
La medición de O2 en vapores de hidrocarburos se utiliza para el control de seguridad en columnas de destilación al vacío en el refinado de petróleo. Con los analizadores paramagnéticos de oxígeno convencionales, las concentraciones de O2 se obtienen mediante un sistema de muestreo extractivo, que acondiciona la muestra antes de ser analizada.
Fluidcom puede optimizar los sistemas de inyección de productos químicos para lograr una elevada integridad de los activos y minimizar los gastos operativos.
El AXR de ADMAG es el primer medidor magnético de 2 hilos del mundo medidor de caudal / caudalímetro que emplea el exclusivo "Método de excitación de doble frecuencia", con el que se consigue una precisión del 0,5%, la mejor de su clase, y una excelente estabilidad para la medición de procesos. Además, las tecnologías clave del AXR, recientemente desarrolladas", alcanzan el mismo nivel de inmunidad al ruido que el tipo de 4 hilos bajo el cambio estado de los fluidos y ofrece un rendimiento suficiente para cumplir el requisito de aplicarse en el Circuito de control.
El control de la concentración de cloruro sódico (NaCl) en un disolvedor de sal, donde la sal sólida se disuelve en agua, es muy importante debido a la eficacia de la electrólisis. Una forma convencional de medir la concentración de la solución de NaCl sobresaturada se había realizado mediante el uso de sensores de tipo sin contacto (por ejemplo, densímetro de rayos γ), ya que el NaCl, las impurezas y los precipitados se encuentran en la solución.
Existen varios métodos para la tintura continua de tejidos, así como para la fijación del tinte. Cuando el tinte se aplica directamente, es necesario vaporizar (tratamiento térmico). En la actualidad, el método de vaporización por tampones es el más utilizado para la tintura continua. Para garantizar una calidad estable del producto, la humedad en el vaporizador se mantiene a un nivel constante.
La sosa cáustica es un material básico importante en la industria química y se produce principalmente mediante la electrólisis de la sosa. En el proceso de electrólisis para fabricar sosa cáustica concentrada, el densímetro de líquidos DM8 garantiza una alta calidad del producto mediante la medición precisa de la densidad del líquido.
Por qué FluidCom es adecuado para la inyección química en plataformas de cabeza de pozo no tripuladas (UWHP)
Los analizadores de líquidos de proceso, como pH-metros, conductivímetros, redox-metros y densímetros, desempeñan un papel importante en las plantas de electrólisis en el control de las concentraciones de diversas soluciones de proceso. Esto requiere tanto precisión como estabilidad en condiciones adversas que incluyen sustancias altamente corrosivas, altas temperaturas y muchas impurezas.
Para un funcionamiento seguro y eficaz, la calidad del agua de alimentación, el vapor y el condensado en las plantas de calderas debe controlarse y mantenerse en las condiciones más favorables.
- Controla eficazmente la válvula de admisión y la válvula de descarga cuando el compresor arranca y se detiene.
- Durante el funcionamiento continuo, controla la válvula de entrada para que la cantidad de aire comprimido descargado sea constante (control de caudal).
- Surgimiento: La carga disminuye, la cantidad de flujo de descarga y la caída de presión, y se supera un límite, posiblemente destruyendo el compresor.
En el proceso de fabricación de las industrias farmacéutica, química y de alimentos y bebidas, la limpieza y esterilización de depósitos y tuberías se realiza con diversas soluciones de limpieza, agua dulce o caliente y vapor después de fabricar los productos. Clean-In-Place (CIP) es el sistema diseñado para la limpieza y desinfección automáticas.
- Los circuitos de enclavamiento de emergencia de las plantas petroquímicas y otras instalaciones deben ser independientes del sistema de control principal.
- El instrumento de bastidor YS80 no sólo interactúa con los dispositivos de campo y los sistemas de control aguas arriba, sino también con los circuitos de enclavamiento de emergencia que protegen contra las anomalías del proceso.
¿Y si pudiera detectar rápidamente indicios de anomalías en los conductos de barras (barras colectoras) durante los trabajos de mantenimiento e inspección y responder a ellos en el momento justo? Yokogawa La solución de supervisión DTSX supervisa constantemente las conexiones que tienden a deteriorarse con el tiempo y contribuye señalando con precisión los lugares donde se producen anomalías y reduciendo la carga de trabajo del personal de mantenimiento, lo que ayuda a garantizar la estabilidad del funcionamiento de la planta.
Se consumen muchos tipos de gases en industrias tan variadas como la química, la alimentaria y de bebidas y la médica. Estos gases se suministran normalmente en forma líquida en camiones y se dispensan en las instalaciones del cliente. Aunque el caudal de gas licuado criogénico se utiliza con fines de facturación, no es fácil medirlo con precisión porque el gas está siempre a temperaturas de saturación.
Con el desarrollo industrial y económico llegan centrales eléctricas y fábricas cada vez más grandes y avanzadas. Sin embargo, encontramos muchos casos en los que los cables originales, los túneles portacables y otros componentes de la infraestructura eléctrica han languidecido bajo un funcionamiento continuo.
El vertido de productos químicos industriales y gases combustibles tratados de forma inadecuada puede tener un gran impacto en el medio ambiente y suponer una grave amenaza para la salud pública. Paralelamente al crecimiento global de las operaciones de fabricación para seguir el ritmo de las tendencias del mercado, muchos países están tomando medidas para hacer frente a los problemas medioambientales.
En los sistemas de desulfuración de gases de combustión con piedra caliza y yeso, el consumo de un agente de desulfuración (cal) se controla mediante analizadores de pH en línea.
La ósmosis inversa (OI) es un proceso de separación que utiliza la presión para forzar una solución a través de una membrana que retiene el soluto en un lado y permite que el disolvente puro pase al otro lado. Más formalmente, es el proceso de forzar un disolvente desde una región de alta concentración de soluto a través de una membrana hasta una región de baja concentración de soluto aplicando una presión superior a la presión osmótica.
Las calefacciones por combustión se utilizan para diversos procesos en refinerías de petróleo y plantas petroquímicas.
- En el YS170 y el SLPC, el control de un solo elemento debe configurarse dentro del programa de usuario.
- El YS1700, sin embargo, ofrece el modo directo primario para que el programa de usuario pueda activar y desactivar el control de un solo elemento cambiando un parámetro.
Tanto los inventarios a granel como los acabados se almacenan en depósitos distribuidos alejados de las operaciones de la planta. Estos depósitos son difíciles de controlar debido al coste de la infraestructura. Se controlan diariamente mediante rondas de vigilancia. Aunque eficaz, este método requiere una gran mano de obra cualificada para vigilar todos los tanques. Esto puede suponer un riesgo adicional cuando el medio almacenado es de naturaleza peligrosa.
Instale un YTMX580 en el lateral del horno giratorio que pueda transmitir de forma inalámbrica los valores medidos de varios sensores de temperatura.
Los tanques de almacenamiento se utilizan en una variedad de industrias que van desde el almacenamiento de petróleo crudo hasta el almacenamiento de materias primas para el monómero de cloruro de vinilo (VCM).
- La lectura manual de la temperatura requiere caminar unos 130 m y subir y bajar secciones elevadas de las etapas del secadero.
- Múltiples puntos de medición de la temperatura a lo largo de las distintas etapas del secador requieren muchos cables a la Sala de control.
- Humedad muy alta.
- La temperatura se controla para mantener la consistencia de la fibra viscosa que entra en el tambor.
- El sistema actual requiere lecturas manuales de la temperatura.
- La medición de la temperatura por cable no está disponible porque el tanque está girando.
- Medición inalámbrica de la temperatura
Pasarela x1, transmisor (YTA) x1, repetidor x2 (Los 2 repetidores son para redundancia) - Antena extendida para sortear obstáculos y mejorar la trayectoria de radio para una medición estable (la comunicación era inestable cuando la altura de la antena era baja).
El gas amoniaco (NH3) se inyecta para eliminar los NOx y reducir así la concentración de NOx en los gases de combustión de la chimenea. Con los analizadores de NH3 convencionales que realizan mediciones de forma indirecta, las concentraciones de NH3 se obtienen a través de un sistema de muestreo. Por lo tanto, existen problemas con el mantenimiento y los costes de funcionamiento del sistema de muestreo, así como retrasos en la medición. El analizador láser TDLS8000 es la solución a todos estos problemas.
Los transmisores inalámbricos de temperatura y presión ISA100 con placas de orificio permiten:
- Sin instalaciones de cableado ni mantenimiento.
- La escasa cantidad de hardware y la sencillez de implantación de los equipos implican minimizar los posibles actos vandálicos.
Monitorización inalámbrica ISA100
- Pasarela x1, Transmisor de temperatura (YTA) x3, Transmisor de presión (EJX) x1, Repetidor x1
La puerta de enlace se instala en Sala de control y se coloca una antena extendida de 3 m de altura.
- En cada punto de control se instalan un transmisor de temperatura (YTA) y un transmisor de presión (EJX).
- El repetidor está instalado en posición alta.
Controla la temperatura y adquiere datos de varios componentes internos de los equipos de fabricación de películas de plástico. Puede montarse un sistema de adquisición y supervisión de datos fácil de usar y de alto rendimiento económico utilizando instrumentos compatibles con Ethernet y GA10.
En el mantenimiento y la gestión de plantas industriales, el control del pH/ORP de las aguas residuales es tanto una obligación legal como una necesidad ineludible para proteger el medio ambiente. Una monitorización sin un ojo atento puede acarrear graves consecuencias.
La medición de la presión de los neumáticos sin cámara para controlar la pérdida de aire es una de las pruebas de rendimiento clave en las unidades de fabricación de neumáticos. La reubicación de los neumáticos de un bastidor de pruebas a otro para diversas pruebas y el movimiento frecuente de la configuración de pruebas para pruebas condicionales a diversas ubicaciones requiere una implementación sin cables para facilitar la manipulación.
Para sufragar los costes energéticos, muchas plantas industriales tienen sus propias calderas para generar vapor con el fin de producir una parte de sus necesidades energéticas. Además de generar energía, el vapor también puede utilizarse directamente en los procesos de la planta o indirectamente a través de intercambiadores de calor o recipientes con camisa de vapor.
Tras la extracción de la caña de azúcar o de la remolacha azucarera, el zumo debe purificarse para eliminar los muchos otros compuestos orgánicos y minerales que lo acompañan. El proceso para lograrlo depende en gran medida de una medición y un control fiables del pH, como se ilustra en la figura.
Visual MESA© es un programa informático de optimización y gestión de sistemas de vapor desarrollado originalmente en Chevron y comercializado actualmente por Nelson & Roseme, Inc. Visual MESA se utiliza actualmente en refinerías y plantas de fabricación de productos químicos para optimizar el sistema de vapor global de la planta y las partes del sistema eléctrico que se compensan económicamente con el sistema de vapor.
Este documento explorará las variables de optimización significativas y las restricciones que se encuentran comúnmente en la optimización del sistema de vapor de refinería, las estrategias que Visual MESA utiliza para tratar con ellos.
A lolargo de más de veinte años como ingeniero involucrado directamente en proyectos relacionados con servicios públicos en diversas industrias, he visto una gran variedad de proyectos y programas de eficiencia energética que cubren todo el espectro de eficacia. La planta de Deer Park, Texas, de Rohm and Haas Empresa tiene un programa único de gestión de la energía que ha demostrado un gran éxito. Este programa ha dado como resultado una reducción del 17% en el consumo de energía por libra de producto, lo que supone un ahorro de 3,25 billones de btus y 15 millones de dólares al año. Este artículo analiza este programa, su historia, sus éxitos y las características únicas que han contribuido a esos éxitos.
En general, las refinerías presentan un muy buen potencial para la monitorización y optimización en tiempo real mediante el Sistema de Gestión Energética Visual MESA.
Según nuestra amplia experiencia, se puede obtener un beneficio global del 2% al 5% del coste energético total. La amortización prevista del proyecto es siempre inferior a un año.
Esquema
- Introduction
- Qué es la optimización energética
- Cómo funciona un sistema en línea en tiempo real Gestión de la Energía basado en Visual MESA
- Base de cálculo de los indicadores clave de rendimiento
- Implantación de Visual MESA en Saudi Kayan (filial de SABIC) (SK)
- Acciones de optimización
- Económico Beneficios
- Relevancia de Visual MESA RTEMS para la iniciativa de sostenibilidad de SK
- Conclusiones
La empresa REPSOL tenía en mente la mejora del control en uno de sus reactores químicos. Se ha realizado un estudio de viabilidad para la implantación de una técnica de Control Avanzado (Control Predictivo para el control de temperatura de Reactores químicos - PCR) para un reactor discontinuo de producción de Polioles. La técnica PCR propuesta se basa en un modelo dinámico de la unidad que realiza la predicción del comportamiento de las variables del proceso.
En este trabajo no se describirán todas las características del programa informático ni se explicará por completo la tecnología de optimización en línea. El objetivo de este trabajo es presentar algunos hechos y lecciones interesantes de la experiencia de aplicar un programa de optimización basado en costes en treinta refinerías de petróleo y complejos petroquímicos de todo el mundo, desde 1997. Este trabajo se centrará en las variables de optimización y las restricciones clave en la optimización de sistemas de vapor, cómo deben tratarse y cómo pueden abordarse los aspectos humanos y organizativos.
Las instalaciones industriales en las que se produce energía y vapor (es decir, la cogeneración) presentan un potencial muy bueno para la supervisión y optimización en tiempo real mediante el sistema de gestión de la energía Visual MESA.
Según nuestra amplia experiencia, se puede obtener un beneficio global del 2% al 5% del coste energético total. La amortización prevista del proyecto es siempre inferior a un año.
Visual MESA se aplicó con éxito a muchas instalaciones industriales de todo el mundo, varias de ellas con redes de generación de vapor y electricidad de diferente complejidad y capacidad, pero todas con ahorro de costes energéticos.
En este artículo se analizan ejemplos industriales reales en los que el sistema de servicios públicos de una refinería o planta petroquímica se optimiza con un software en tiempo real, en línea y de eficacia probada en la industria. Se comentan las experiencias adquiridas durante más de 20 años de proyectos industriales desplegados en todo el mundo (las referencias 1 a 10 se refieren a algunos proyectos recientes). Se explican los principales pasos del proyecto y se presentan los detalles críticos que hay que tener en cuenta para garantizar un uso satisfactorio y una transferencia de tecnología adecuada. En la ponencia se analizarán casos prácticos concretos.
Los servicios públicos y los sistemas energéticos suelen ser la principal fuente de emisiones de SOx, NOx y CO2, por lo que el control de emisiones y la gestión de créditos y cuotas están estrechamente interrelacionados con la gestión energética.
En el caso de las refinerías y las plantas químicas y petroquímicas, la energía representa el principal coste (en segundo lugar después de la materia prima) y, por tanto, su reducción se ha convertido en una decisión empresarial fundamental. Los sistemas energéticos de estas instalaciones son intrínsecamente complejos, y el análisis del coste de las emisiones y el cumplimiento de los límites introducen un factor adicional a la complejidad del reto de la reducción de los costes energéticos.
Las plantas de proceso utilizan distintos tipos de combustibles, a menudo operan con unidades de cogeneración, sus redes de vapor constan de varios niveles de presión, hay distintos tipos de consumidores de energía y hay límites de emisión que respetar. La importación o exportación de electricidad en mercados desregulados, que además podría intercambiarse con más o menos emisiones de CO2 y otros gases contaminantes, aumenta la complejidad del problema de optimización.
Tras un estudio de viabilidad, Repsol YPF decidió aplicar un controlador predictivo basado en modelos a un reactor discontinuo de producción de polioles. El controlador predictivo para reactores (PCR) es un conjunto de módulos de control diseñados para hacer frente a la mayoría de las configuraciones de reactores. El importante aumento de la producción es consecuencia del mejor manejo de la temperatura del reactor. A continuación se describen la unidad y los objetivos de control, la metodología, las fases del proyecto, los resultados y los beneficios correspondientes.
Las grandes y complejas instalaciones industriales, como las refinerías y petroquímicas, son cada vez más conscientes de que los sistemas de energía deben gestionarse de forma óptima, ya que cualquier reducción de energía que las operaciones logren en las unidades de producción podría acabar desperdiciándose si el coste global del sistema de energía no se gestiona adecuadamente. Sin embargo, los ingenieros de procesos siempre han intentado desarrollar algún tipo de herramienta, muchas veces basada en hojas de cálculo, para mejorar la forma en que se gestionaban los sistemas de utilidades. El principal inconveniente de los intentos anteriores era la falta de datos: los ingenieros pasaban todo el día al teléfono o visitando las salas de control para recopilar información del historiador de datos del Sistema de Control Distribuido (DCS), procesarla en la hoja de cálculo y producir recomendaciones que, cuando estaban listas para ser aplicadas, estaban obsoletas y ya no eran aplicables.
Este documento aborda algunas de las causas fundamentales de los problemas y analiza las mejores prácticas que ayudarán a evitar el fracaso de los proyectos. Se explican las principales etapas del proyecto y se analizan los detalles críticos que deben tenerse en cuenta para garantizar el éxito de la utilización y la correcta transferencia de tecnología. También se presentan ejemplos industriales reales en los que se optimiza el coste de todo el sistema de servicios públicos de un centro de producción (es decir, vapor, combustibles, agua de alimentación de caldera y electricidad) con un software en tiempo real, en línea y bien establecido industrialmente.
Los servicios públicos y los sistemas energéticos suelen ser la principal fuente de emisiones de SOx, NOx y CO2, por lo que el control de emisiones y la gestión de créditos y cuotas están estrechamente interrelacionados con la gestión energética.En el caso de las refinerías y las plantas químicas y petroquímicas, la energía representa el principal coste (después de la materia prima) y, por tanto, su reducción se ha convertido en una decisión empresarial fundamental. Los sistemas energéticos de estas instalaciones son intrínsecamente complejos, y el análisis del coste de las emisiones y el cumplimiento de los límites introducen un factor adicional a la complejidad del reto de la reducción de los costes energéticos.
En este artículo se describen los sistemas energéticos, los pasos para la implantación de Visual MESA y varias características del modelo, centrándose en el uso del software para el cálculo de los KPI relacionados con la energía. Se analiza el proyecto de implantación del EMS y se presentan también las principales conclusiones relativas a la reducción de los costes de explotación.
Se comentan las experiencias adquiridas durante más de 20 años de proyectos industriales desplegados en todo el mundo. Se explican los principales pasos del proyecto y se presentan los detalles críticos que hay que tener en cuenta para garantizar el éxito de su uso y la correcta transferencia de tecnología. En la ponencia se analizan casos prácticos concretos. También se presenta la aplicación en bucle abierto frente a la de bucle cerrado.
Rohm and Haas Company es uno de los mayores fabricantes mundiales de materiales especiales, como adhesivos, sellantes, revestimientos, monómeros, materiales electrónicos, soluciones inorgánicas y especiales y resinas de intercambio iónico. Fundada en 1909 por dos empresarios alemanes, Rohm and Haas ha crecido hasta alcanzar unos ingresos anuales de aproximadamente 6.000 millones de dólares.
La gestión de alarmas no es sólo un proyecto que tiene una fecha de inicio y otra de finalización; es un ciclo continuo. Una vez revisado el sistema de alarma e identificadas las mejoras, hay que comprobar que se aplican los controles necesarios para garantizar que el sistema de alarma sigue funcionando. La clave está en asegurarse de que el sistema se supervisa continuamente y de que cualquier cambio queda plenamente documentado. Hay siete pasos fundamentales para Gestión de alarma. La racionalización es uno de esos pasos fundamentales.
Este artículo muestra cómo mejorar las operaciones de destilación centrándose en la automatización de los procedimientos. Se revisará la importancia de utilizar procedimientos en las operaciones de destilación y se destaca el trabajo de colaboración en curso entre Fractionation Research Inc. (FRI) y Yokogawa Corporation para mejorar las operaciones de procedimiento.
Los mundos de la automatización de procesos y la gestión de la producción llevan algún tiempo convergiendo. Lo que antes eran islas de funcionalidades de automatización y gestión de la producción conectadas a través de esquemas altamente propietarios Integración cuyo mantenimiento resultaba costoso, se han convertido en plataformas integradas que proporcionan un intercambio de datos sin fisuras entre el mundo de la automatización y la planta de producción, las funciones de gestión de la producción y las operaciones, y Integración con sistemas de nivel empresarial.
El mundo de la automatización de procesos se rige por procedimientos. Aunque nos gusta decir que las industrias de procesos son en gran medida "continuas", esto no podría estar más lejos de la realidad. La fabricación por procesos está en constante cambio.
Desde Ingeniería hasta la instalación, la puesta en servicio, las operaciones y el mantenimiento, el bus de campo FOUNDATION ofrece importantes reducciones de costes del 30% o más frente a los sistemas analógicos convencionales. Muchas de estas reducciones de costes proceden de las funciones avanzadas que ofrece el bus de campo frente a la tecnología analógica.
Los proveedores de automatización que tendrán éxito a largo plazo serán aquellos que resuelvan eficazmente los problemas específicos de la aplicación o del sector para los usuarios finales con una propuesta de valor que no pueda ignorarse. Estos problemas existen actualmente en todas las industrias de procesos y no se resolverán simplemente ofreciendo un producto, sino mediante una combinación de hardware, software, servicios, aplicaciones Experiencia, y conocimientos.
En opinión de ARC, los clientes necesitan una propuesta de valor empresarial convincente para justificar la inversión en cualquier tipo de automatización. Vigilance y VigilantPlant se crearon con esto en mente. Yokogawa 's vision with VigilantPlant is to create an environment where plant personnel and operators are well informed, alert, and ready to take action.
Yokogawa ha recorrido un largo camino para dejar claro su mensaje al mundo de la automatización de procesos. El año pasado, la empresa se embarcó en una campaña mundial de marketing a gran escala para concienciar a los clientes de la importancia que concede a la fiabilidad, seguridad, fiabilidad y solidez de sus sistemas. Denominada "Vigilancia", la campaña creó un mensaje unificado para la empresa y contribuyó en gran medida a dar a conocer la marca Yokogawa y su filosofía corporativa.
Los usuarios finales de automatización de procesos se ven más presionados que nunca para hacer más con menos. La actual coyuntura económica hace que muchos proyectos de inversión en automatización estén en suspenso. Con unos presupuestos de capital más ajustados que nunca, los usuarios se centran en los presupuestos operativos (en los que la reducción de costes es también una preocupación clave), o en inversiones en automatización con un ritmo muy rápido Rentabilidad de la inversión.
En el dinámico mercado industrial actual, la única constante es el cambio. Los costes de las materias primas, los costes energéticos, las demandas del mercado, las normativas medioambientales y de seguridad, la tecnología e incluso la propia naturaleza de la mano de obra cambian constantemente, y no siempre en direcciones predecibles.
La migración del DCS de una refinería brindó la oportunidad de reconfigurar y consolidar las salas de control y el sistema de gestión operativa.
La medición del nivel de presión diferencial tiene un enemigo: la temperatura. La temperatura puede tener un efecto negativo en la precisión de la medición de nivel. Este artículo explica por qué la temperatura tiene este efecto y cómo puede reducirse.
Con los calefactores a fuego, los usuarios esperan obtener una mayor eficiencia y una reducción de las emisiones, pero a menudo se sienten decepcionados. Dado el número de calefactores a fuego que funcionan cada día y su importancia en las industrias de procesos, cualquier mejora que se consiga en todos los ámbitos tendrá un impacto enorme. Más unidades pueden alcanzar su potencial con unos simples cambios en las prácticas de trabajo y actualizaciones tecnológicas.
Julio de 2011
Las plantas de proceso funcionan de acuerdo con procedimientos operativos. Estos procedimientos consisten en un conjunto de tareas que se ejecutan de forma coherente para lograr un objetivo específico, como la puesta en marcha, el apagado o la transición de una unidad como parte de la fabricación de un producto.
Septiembre de 2008
Yokogawa ayuda a una gran planta química china a gestionar el transporte de productos por carretera, barco y tubería.
El uso de la fibra óptica para la detección de la temperatura se está extendiendo más allá de las aplicaciones de seguridad.
Marzo de 2006
El nuevo complejo petroquímico de CSPC (CNOOC y Shell Petrochemicals Empresa Limited) en Daya Bay, al sur de China, es uno de los mayores proyectos de la industria de procesos del mundo (véase el recuadro, la figura 1 y la tabla). Tiene un sistema de control a la altura. Process Worldwide habló con Johan Veerman, ingeniero principal de instrumentación y control de procesos de CSPC, sobre los retos que plantea la gestión de un trabajo de tal envergadura.
El estándar inalámbrico LoRaWAN permite comunicaciones inalámbricas y digitales Transformación a larga distancia, complementando redes inalámbricas en planta como ISA100.
En situaciones anómalas, los sistemas están configurados para producir muchos datos, pero los humanos no están preparados para manejarlos o interpretarlos. Sin embargo, cuando se les presenta la información adecuada, en el contexto adecuado, durante una situación anormal, los humanos son capaces de hacer cosas que las máquinas no pueden.
La detección inalámbrica basada en la nube permite aumentar la seguridad, la fiabilidad y los beneficios mediante la supervisión generalizada de los activos.
La actualización de la mina de mineral y refinería de Wyoming Trona de Yokogawa Centum CS3000 a CENTUM VP-R5 implicó dos dominios, 21 estaciones de control de campo RIO y FIO, 17 estaciones de operador, 6 estaciones Ingeniería y 8 servidores de planta diferentes.
La norma ISA S88.01 proporciona grandes beneficios a usuarios y proveedores al solidificar los modelos operativos de lotes y estandarizar la terminología de control de lotes. Por otra parte, como corresponde a una norma de ámbito industrial, ISA S88.01 deja una gran flexibilidad a los usuarios individuales para aplicar sus propias prácticas de proyecto y metodología de implementación. Incluso cuando se utilizan los modelos y la terminología de la norma ISA S88.01, quedan muchos escollos para quienes implantan los controles de lotes y la gestión de Receta sin pensar en el futuro. La experiencia de proyectos reales ha demostrado una serie de "lecciones" de diseño e implementación que pueden pasarse por alto para desgracia del ingeniero de lotes.
Los sistemas de automatización de procesos están cada vez más conectados a los sistemas informáticos y al mundo exterior, lo que plantea problemas de ciberseguridad que pueden resolverse mediante técnicas como las redes definidas por software y los servicios de supervisión.
El proyecto de norma S88.02 define un medio para representar el control Procedimiento en las recetas maestras y de control. Este método de representación se denomina gráfico de funciones de procedimiento (PFC). Esta representación estándar se basa en los requisitos de la norma S88.01, el informe técnico ISA-TR88.0.03-1996, los requisitos de los usuarios, las normas anteriores y los métodos de representación de procedimientos comúnmente utilizados en la actualidad. Los PFC pueden proporcionar una base común para el intercambio de recetas, reducir la curva de aprendizaje entre sistemas de control y establecer una base común para mejorar la comunicación humana. Este documento ofrece una breve visión general del desarrollo de las PFC, las normas para su uso y algunos de los beneficios que se esperan de su adopción en la industria.
El estudio de caso de este artículo ilustra el valor de integrar la programación frontal con un sistema de control de lotes. En el proceso de destino se producen con frecuencia cambios y adiciones de recetas. Sin embargo, dado que tanto el programador como los paquetes de lotes se diseñaron teniendo en cuenta el modelo ISA-S88.01, estos paquetes podrían estar estrechamente acoplados (bien integrados) y, como resultado, es fácil añadir o cambiar recetas. El programador frontal no se limita a realizar la programación; también proporciona una visualización del estado de la producción en tiempo real de fácil comprensión que puede ayudar a mejorar la eficiencia y la productividad.
La gestión de activos desempeña un papel clave en la seguridad operativa, y es fundamental capturar y transmitir estos datos de forma segura y digitalizada para garantizar que estén actualizados, sean precisos y fácilmente accesibles.
Los robots se utilizan desde hace tiempo en aplicaciones de fabricación discreta y automatización de maquinaria, y su uso se está extendiendo ahora a aplicaciones de la industria de procesos.
A medida que se automatizan los procesos por lotes, es habitual dejar ciertos dispositivos de campo menos esenciales sin actuadores automáticos. Así pues, el diseño inicial del control debe dar cabida tanto a las actividades automatizadas como a las manuales. Posteriormente, los dispositivos de campo manuales pueden automatizarse, ya sea uno a uno o en grupos relacionados como módulos de equipos. Estos cambios de campo, que a menudo se producen a lo largo de un período de años, requieren cada vez la reelaboración de la lógica de control de lotes, que puede superar fácilmente el coste del actuador. En respuesta a esta situación indeseable, se ha desarrollado una técnica que permite que el diseño del lote se modifique automáticamente, o evolucione, para adaptarse a los cambios en la automatización del campo.
Seis Sigma es una metodología de mejora de la calidad aplicada a la mejora de cualquier tipo de proceso. Es una metodología avalada y fuertemente integrada en varias grandes empresas químicas.
Los activos y las operaciones tendrán capacidades de aprendizaje y adaptación similares a las humanas, lo que permitirá responder sin interacción del operador a situaciones dentro de un dominio seguro y delimitado.
Los historiales proporcionan el almacenamiento de datos, la conectividad segura y las herramientas integradas necesarias para la implantación de iniciativas digitales Transformación.
Los indicadores clave de rendimiento (KPI) se utilizan en las industrias de procesamiento por lotes para medir el rendimiento de la producción. Su uso es un elemento de la tendencia actual a la gestión del rendimiento en tiempo real. Un único KPI utilizado como medida principal de la producción puede hacer que otras dimensiones del rendimiento de la producción pierdan importancia. Cuando se utilizan varios KPI para medir el rendimiento de la producción de un lote, puede resultar difícil conciliar las diferencias entre ellos para lotes individuales o para grupos de lotes. Los KPI basados en el cumplimiento de un objetivo o especificación miden el rendimiento absoluto, pero no proporcionan información relativa sobre el rendimiento de un lote en comparación con sus homólogos. Las comparaciones entre pares son importantes para controlar la variabilidad del rendimiento de la producción, que es un factor crítico para documentar el retorno de la inversión.
La aplicación de "controles avanzados" basados en DCS es un método habitual para conseguir un mayor rendimiento de los procesos continuos, como las unidades de refinería. Sin embargo, es menos reconocido, aunque no por ello menos cierto, que los sistemas DCS modernos pueden incluir otras herramientas de software para la mejora significativa de la productividad de las plantas discontinuas, la calidad del producto y el rendimiento económico. Debido a las diferencias fundamentales de procesamiento entre los dos tipos de plantas, se requieren funciones únicas de "control avanzado" de lotes que son diferentes de las utilizadas para las plantas continuas.
CONTROL, enero de 2013
La metodología de automatización estándar mejora las operaciones y evita incidentes al permitir compartir las mejores prácticas entre los operadores.
ARC cree que mediante la implementación de la automatización de procedimientos, muchas plantas de proceso pueden minimizar la variabilidad para ayudar a garantizar transiciones de estado suaves, eficientes y seguras.
Cablear los sensores de temperatura instalados en una chimenea a Sala de control puede resultar complicado y caro, por lo que muchas plantas e instalaciones están implementando en su lugar soluciones inalámbricas, como este transmisor de temperatura de 8 entradas YTMX580 de Yokogawa.
La automatización de procesos en refinerías de petróleo está experimentando grandes cambios, impulsada por clientes frustrados por lo que consideran avances lentos y graduales de los principales fabricantes de equipos originales (OEM) de automatización del sector. ExxonMobil se ha convertido en un representante de facto del sector y está impulsando a proveedores como Yokogawa y otros a reevaluar el modo en que se ejecutan los proyectos de automatización a gran escala.
Los sistemas de supervisión, control y adquisición de datos (SCADA) forman parte de las industrias de procesos desde hace muchas décadas y las medidas de ciberseguridad deben crecer a medida que avanza la tecnología. Los sistemas SCADA se utilizan en oleoductos y gasoductos y en otras aplicaciones de control y supervisión a distancia, como la transmisión y distribución de electricidad, y el agua y las aguas residuales.
Muchas empresas dedicadas a la mezcla de lubricantes se encuentran en una situación difícil: existen oportunidades para aumentar el volumen global de su negocio y sus beneficios mejorando la flexibilidad de la producción, ampliando su gama de productos y optimizando las mezclas de alto margen. Al mismo tiempo, se ven constreñidas por las actuales limitaciones de fabricación. Sin embargo, lanzar un proyecto de capital para una expansión significativa de la fabricación puede no ser posible, y puede no ser necesario.
La tecnología espectrométrica puede evaluar muchas características críticas de los productos, pero tiene sus límites. Puede ser difícil determinar cuándo se ha cruzado el límite
Las máquinas pueden apoyar a los humanos cuando se enfrentan a una situación estresante. Utilizar un enfoque basado en normas puede reducir la probabilidad de que un problema se agrave.
Honeywell y Yokogawa llevan décadas produciendo plataformas distribuidas Sistema de control (DCS) y ambas son muy activas en este campo. En 1975, Honeywell presentó su plataforma TDC2000 y Yokogawa sacó al mercado CENTUM. Estos dos sistemas competidores surgieron de un lugar similar, las industrias de refinado de petróleo y petroquímica, por lo que empezaron con conceptos básicos y casos de uso similares en mente.
Descargas
Folletos
Especificaciones Generales
Certificados
- EU_UK Declaration of Conformity FU20 2022-11-14 (170 KB)
- EU_UK Declaration of Conformity SC29 2022-11-14 (146 KB)
- EU_UK Declaration of Conformity ISC40G 2022-11-14 (195 KB)
- EU_UK Declaration of Conformity PR10 2022-11-14 (140 KB)
- EU_UK Declaration of Conformity ISC40S 2022-11-14 (195 KB)
- EU_UK Declaration of Conformity SM23 2022-11-14 (121 KB)
- EU_UK Declaration of Conformity SB20 2022-11-14 (147 KB)
- EU_UK Declaration of Conformity SM29 2022-11-14 (147 KB)
- EU_UK Declaration of Conformity SC21 2022-11-14 (146 KB)
- EU_UK Declaration of Conformity SM60 2022-11-14 (147 KB)
- EU_UK Declaration of Conformity SR20 2022-11-14 (147 KB)
Vídeos
Presenta el OpreX Intelligent Manufacturing Hub, una plataforma basada en IA que mejora la fabricación con datos sin fisuras Integración, informes inteligentes, flujos de trabajo optimizados y visualización avanzada para una toma de decisiones y una eficiencia más inteligentes.
Chet Mroz, Presidente y CEO de Yokogawa North America, habla sobre los beneficios de IoT en el Foro de la Industria ARC 2015 en Orlando.
¿Cuánto sabe sobre transmisores de presión? ¿Están midiendo la presión de forma precisa, rápida y fiable? En última instancia, el objetivo de todo buen transmisor de presión es proporcionar rápidamente al usuario una medición de presión precisa y fiable. Este vídeo le ofrece las respuestas a sus preguntas básicas sobre la presión y los transmisores de presión.
Yokogawa se ha asociado con INCIT para introducir el marco S.I.R.I., con el fin de ampliar aún más el mensaje de Yokogawa como empresa de soluciones integrales.
Noticias
-
Nota de Prensa feb 3, 2025 Yokogawa Lanza el sistema OpreX Gestión de Calidad para acelerar la DX en los procesos de garantía de calidad para la fabricación de productos farmacéuticos y alimentos y bebidas
- Un sistema basado en la nube que permite mejorar los procesos de forma rápida y flexible.
-
Nota de Prensa oct 28, 2024 Yokogawa Sensyn Robotics se asocia para ofrecer servicios relacionados con drones
- Para inspecciones seguras y eficaces de plantas y otras infraestructuras en todo el mundo -
-
Nota de Prensa feb 20, 2023 Yokogawa Se asocia con Radial Software Group para ofrecer en todo el mundo software Viewport basado en IA
- Ofrecer a los clientes una visión única de todos sus datos técnicos.
-
Nota de Prensa feb 2, 2023 Yokogawa adquiere Fluence Analytics, empresa pionera en la digitalización de la monitorización de procesos de reacción de polimerización
- Permitir la supervisión continua en tiempo real de polímeros y biopolímeros -
-
Noticias Breves sep 18, 2019 Yokogawa admite la primera implantación mundial de un paquete tipo módulo en un entorno industrial
¿En busca de información adicional sobre Yokogawa Iberia, tecnología y soluciones?
Contáctenos