Leverage of Remote Asset Monitoring
Don’t you entrust equipment maintenance solely to operator rounds? There is a limit to monitoring all the equipment deployed across a large plant.
Why don’t you to remotely monitor the condition of the equipment instead of having operator rounds throughout the plant? Most operator rounds simply verify that the equipment works normally. By being able to monitor the condition of equipment remotely at all times, you can inspect specific equipment that shows anomaly in advance without having to visit a site, thus improving efficiency. However, remote monitoring requires IT technology to cover a wide range of factories and centrally manage them. Therefore, realizing remote asset monitoring is a challenge due introducing the necessary IT technology.
Challenges in Deploying Remote Asset Monitoring
- Many monitoring points deployed over a wide area.
- Mounting sensors hazardous or difficult-to-access locations.
- Saving time: Large number of installation and configuration tasks, including power and communication wiring
Industrial IoT Solutions Using Sushi Sensor for Remote Asset Monitoring
Yokogawa advocates Industrial IoT Wireless Solutions.
We offer remote monitoring using the IoT technology in Sushi Sensor.
- Uses the LoRaWAN® wireless standard for long-distance communication
- Water and dust proof, and explosion proof
- Battery-powered sensor equipped with wireless communication
Benefits of Remote Asset Monitoring
- Monitor the condition and health of equipment constantly without having to be in the site.
- Detect "something wrong" before the equipment shows an abnormal value to know when maintenance and inspection is necessary, and respond to problems quickly.
- Know the "signs" and respond early—shorten downtime from sudden shutdowns and malfunctions, minimize waste due to equipment failure or deterioration in product quality, and increase efficiency in equipment maintenance and production.
Contributing to Reducing Greenhouse Gas (GHG) Emissions
A new monitoring device has been added to Sushi Sensor portfolio due to detect the condition of steam traps in steam systems. Increased frequency monitoring of steam trap conditions enables optimal maintenance opportunities, allowing for efficient repairs or replacements. This contributes to the reduction of greenhouse gas (GHG) emissions.
*A steam trap is an equipment that properly discharges the condensate and the air from steam systems in plants.
Please click here for more details on Sushi Sensor.
Note: Sushi Sensor is sold in different regions for each product.
Please check general specification for details.
-
Wireless Pressure Sensor
This product acts as a battery-powered wireless pressure sensor, and it is suitable for Industrial IoT (IIoT) applications. Wireless Pressure Sensor has the function of measuring the gauge pressure of gases and liquids in a piping.
-
Wireless Temperature Sensor
This product acts as a battery-powered wireless temperature sensor, and it is suitable for Industrial IoT (IIoT) applications. Wireless Temperature Sensor supports 2 inputs of IEC standard thermocouples (any of 9 types including Type B, E, J).
-
Wireless Vibration Sensor
This product acts as a battery-powered wireless vibration sensor and it is suitable for Industrial IoT (IIoT) applications. Wireless Vibration Sensor measures vibration along the X, Y, and Z axes in addition to monitoring the surface temperature.
-
Wireless Steam Trap Monitoring Device
This product acts as a battery-powered wireless steam trap monitoring device, and it is suitable for Industrial IoT (IIoT) applications. Wireless Steam Trap Monitoring Device detects the condition of a steam trap by its acoustic sensor and temperature sensor.
Details
What is Sushi Sensor?
To improve the availability ratio and profitability of plants, timely identification of health conditions and efficient maintenance of aged equipment are required. Various sensing technologies are needed to monitor conditions and maintain diverse equipment. In order to maintain equipment distributed across a plant efficiently with limited man-hours, quantification of measurement data and automated data acquisition and storage systems are required. Sushi Sensor monitors vibration, temperature, and pressure as data and detects the condition of steam traps for inviting the maintenance of the equipment. The monitored sensor data and detected conditions are stored in host systems such as the cloud or the on-premises via wireless communication.
Since Sushi Sensor complies with LoRaWAN®, which is a low-power wide-area (LPWA) network for long-distance communication, the Sushi Sensor can be deployed anywhere in a plant and cover a vast area. Also, it has environmental resistance features to support heavy-duty use (IP66/67, explosion proof).
Users can identify equipment conditions by trend monitoring in the cloud or the on-premises, and then plan and perform maintenance efficiently, tailored to the equipment conditions. Comprehensive monitoring the condition of the whole plant helps create priorities of equipment risks and maximize investment in equipment maintenance in a balanced manner.
System Configuration
Features
[Easy Installation]
- Compact, lightweight, battery-powered sensors.
- Operable in harsh environments including hazardous areas (waterproof, dust-proof, and explosionproof).
- The LoRaWAN® standard enables long-distance communication of up to 1 km, and thus flexible installation.
[Easy Setting]
- Parameters can be set with a smartphone via near-field communication (NFC).
[Easy Data Collection and Monitoring]
- Data can be collected over a wide area via long-distance wireless communication.
- Collected data can be accessed from user applications in the cloud.
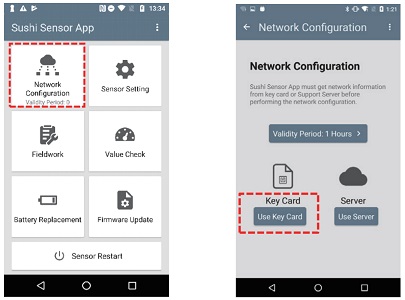
Benefits
(Digitizing)Sensing
Sushi Sensor monitors vibration, temperature, and pressure and detects the conditions of steam traps as data for maintaining equipment. The monitored sensor data and conditions are stored in host systems such as the cloud or the on-premises via wireless communication.
(Digitalizing)Sensemaking
Users can identify equipment conditions by trend monitoring in the cloud or the on-premises, and then plan and perform maintenance efficiently, tailored to the equipment conditions.
(DX)Digital Transformation
Comprehensive monitoring the conditions of the whole plant helps create priorities of equipment risks and maximize investment in equipment maintenance in a balanced manner. For this purpose, quantification of measurement data and automated data acquisition and storage systems are required.
How Does Sushi Sensor Realize DX?
[Effects of Sensing and Sensemaking]
- Reduce inspection man-hours by automatically collecting data on equipment (even in high and hazardous areas) in online
- Quantify and visualize inspection results that depend on individual experience, intuition, and on-site know-how
- Reduce variance in inspection quality due to differences in staff skill
- Enable early detection of abnormal signs ("something wrong") and avoid oversight by trend monitoring of equipment
- Conserve steam and energy by detecting the condition of steam traps and maintain them efficiently
[Effects of Digital Transformation]
1) When an anomaly is detected by a simple diagnosis, the operator performs a detailed diagnosis and identifies the cause of failure.
2) Based on the results, the operator determines the appropriate next action and schedule of maintenance.
Where:
Simple diagnosis: Monitor trends of equipment and detect “abnormal sign” by Sushi Sensor.
Detailed diagnosis: Assess the cause of abnormal sign or failure by portable measurement instrument by the operator.
The operator can focus on value-adding tasks such as detailed diagnostics and determining next steps. Sushi Sensor detects signs of abnormalities and contributes to CBM.
Why is it Called "Sushi Sensor" ?
Sushi Sensor is named after sushi, a hand-pressed traditional Japanese food which combines rice with various toppings.
- Like sushi is easy to eat, Sushi Sensor can be easily installed.
- Like skilled professionals prepare sushi, Sushi Sensor is a robust, finely-crafted product.
- Like sushi comes with various toppings, various kinds of sensors are being developed for Sushi Sensor.
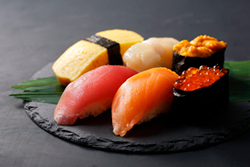
Yokogawa Advocates APM
Yokogawa enhances the value of customers’ equipment through asset performance management (APM).
To maximize the value of equipment, APM focuses on the availability of equipment and evaluates their performance. To maximize performance, APM should be performed not only in maintenance but also in operation and other areas where maintenance and operation must be collaborated to complement each other.
Conventionally, plant operation systems aim to improve production efficiency and product quality while equipment maintenance systems aim to both maximize operational efficiency and minimize costs. However, when maximizing production efficiency, maintenance costs are not necessarily optimized. Although operation information and maintenance information must be combined to maximize profits for the whole plant, this is rarely achieved mainly because maintenance is not always quantified.
To solve this problem, Yokogawa has developed Sushi Sensor, which consists of a sensor that collects basic data for equipment maintenance and functions that quantify, accumulate, and analyze these data, enabling operators to make objective judgements.
Sushi Sensor strengthens collaboration between operation systems and equipment maintenance systems, achieving APM that optimizes all phases from the detection of equipment conditions by sensors to decisions on appropriate actions by operators.
Yokogawa’s APM not only optimizes equipment maintenance but also improves the operation of the whole plant.
Complementary collaboration between operation and equipment maintenance.
Zasoby
Kyowa Hakko Bio monitors vibration trends with Yokogawa's Sushi Sensors to prevent unexpected equipment failures.
By using eServ, sensor data and maintenance information are shared with everyone involved in manufacturing.
Osaka Metro selected Yokogawa's Sushi Sensors to monitor vibration of huge ventilators.
Monitoring vibration trends prevents unexpected failures of air-conditioning systems in subway stations.
Maintaining the reliable performance of a furnace fan allows operators to avoid wasting large batches, which sometimes require days of heat-treat processing.
Remote monitoring of supply pump conditions in the agitation process reduces operator rounds and contributes to stabilization of the product quality.
Automated wireless temperature monitoring at cement plants, lime kilns, and asphalt plants prevents expensive chute clogging issues.
Automated wireless vibration monitoring improves safety and exposes rotating equipment (rollers, driers, etc.) conditions in polyester textile production lines.
Automated wireless pressure monitoring at a polyolefin facility producing high-density polyethylene and polypropylene prevents costly catalyst contamination and production losses.
Downloads
Instrukcje obsługi
- XS822 Steam Trap Monitoring Module (1.5 MB)
- Sushi Sensor Series Software Edition (5.1 MB)
Ogólne specyfikacje
- XS110A Wireless Communication Module (939 KB)
- XS822 Steam Trap Monitoring Module (1.0 MB)
Wideo
In plants, a steam trap failure not only diminishes the thermal efficiency of steam, but also poses the risks of damage and accidents in the steam system.
Sensor visualizes the condition of steam traps and supports secure management.
YOKOGAWA aspires to establish Smart GMP manufacturing facilities that provide consistent quality and supply while eliminating industrial waste, enhancing productivity and always using high-quality component parts and materials.
YOKOGAWA creates autonomous operations with high-efficiency automation and optimization that allows growth with minimal deployment of manpower.
In plants, the potential for significant steam loss exists due to the failure of steam traps.
The industrial IoT wireless solution, Sushi Sensor, supports energy monitoring by visualizing the condition of steam traps.
Wiadomość
-
Informacja prasowa lip 20, 2020 Yokogawa to Expand Sushi Sensor Wireless Industrial IoT Solution Lineup in Europe, North America, and Southeast Asia
- New sensors enable easy online collection of pressure and temperature data -
Szukasz dodatkowych informacji na temat naszych pracowników, technologii i rozwiązań?
Kontakt