Executive Summary
Fractionation Research, Inc. (FRI) is a non-profit research consortium supported by over 70 organizations, including many of the world's s largest petroleum, chemical, and engineering companies. The experimental unit is located on the Oklahoma State University campus in Stillwater, Oklahoma.
At the heart of the FRI experimental facility are two commercial-scale low and high pressure distillation columns along with the equipment needed to support their operation. The auxiliary equipment includes low and high pressure kettle reboilers, low and high pressure condensers, as well as a dedicated boiler and cooling water tower. The low pressure column has the capability to operate from a deep vacuum, while the high pressure column can operate at up to 500 psia. Each column has a 4 foot (internal diameter) by 28 foot section, but the low pressure column also has a section that is 8 feet in diameter and 12 feet high. Each column is equipped with a permanent, automated gamma ray scanner that measures liquid holdup density during the experimental runs. Strategically positioned windows on the columns allow technicians to look inside and even take video. The FRI facility also has viewing windows on one of its kettle reboilers, a feature not available anywhere else in the world. In addition, cross connections between the two columns allow the sharing of some auxiliary equipment and the parallel operation of both reboilers and condensers while the low pressure column is operating. From 2007 to 2009, the experimental unit was refurbished and debottlenecked, and has since been demonstrated to be capable of testing the full range of hydraulic capacity of all known column internal contact devices.
At this FRI facility, process control and data capture were handled by a Yokogawa Micro-XL DCS, and this has recently been replaced with a CENTUM CS 3000 system, also from Yokogawa. At the same time, FRI introduced Yokogawa's Exapilot operator support package and Exaquantum historian. FRI conducts many experiments throughout the year, and Exapilot has enabled this facility to achieve faster and safer start-ups and shut-downs, and has also helped improve another key parameter: time to steady state. This has reduced steam consumption. By providing operators real-time process data at the right time, Exaquantum helps them make quick decisions at every stage of a process.
The Challenges and the Solutions
(1) Smooth and safe start-up and shut-down
FRI normally has about 20 different test operations a year. Each test may last about two to three weeks. To minimize steam consumption, FRI needs to start up the unit quickly, smoothly, and safely. And when a test is completed, the operator has to shut down the unit smoothly and safely.
Exapilot is used to build and execute electronic, semi-automatic procedures using a modular procedural automation (MPA) methodology. Yokogawa and FRI engineers programmed Exapilot for start-ups, transitions, and shut-downs. The software is capable of providing control room technicians with all of the following:
- A step-by-step listing
- Prompts regarding next steps
- Warnings regarding next steps
- Initiation of the actual opening and closing of valves or changes at controller set-points, one at a time in sequence or more than one at the same time
- Performance of "watchdog" function for critical events
- A record of completed steps
- Status information on process changes
When the Yokogawa and FRI staff members first started working together, the learning curve was steep. The Yokogawa people needed to learn the two distillation columns, the three binary systems, and the steps associated with the starts, transitions, and stops. Fortunately, up-to-date and accurate PFDs and P&IDs were available, and these proved to be an essential asset. The FRI people needed to learn the software's capabilities and master electronic procedure building.
Several semi-automatic procedures were written. None were completely perfect when initially tested in the control room. It was very easy, however, to run a computer program in parallel with process changes, in offline mode, without handing over complete control to the computer program. FRI's best board operators were in the control room during these trial runs and had a hand in perfecting the program. With this program running under Exapilot, there is now uniformity in how starts, changes, and stops are executed.
CENTUM CS 3000 integrated with Exapilot and Exaquantum
(2) Easy data management
FRI needs to collect a lot of data from a test operation and analyze it as quickly as possible. Before Exaquantum was introduced, operators had to enter figures in a spreadsheet and then wait at least three hours to see the results of the distillation test. With Exaquantum, the process data is updated every second and displayed in a trend display along with a summary. At a glance, operators can verify the test situation and take immediate action. Data visualization is the key, giving operators a complete understanding of what is going on in the process, in real time.
In summary, the integrated use of the CENTUM CS 3000 DCS, Exaquantum, and Exapilot has reduced steam consumption and improved safety at the FRI test facility by facilitating the execution of non-routine operations.
Customer Satisfaction
According to Mike Resetarits, a technical director, "Manpower reduction is not one of the goals of semi-automatic procedures. In too many global control rooms, manpower reductions have already occurred. Additionally, many senior technicians have retired over the last 10 years. Semi-automatic procedures are intended to help, not eliminate, the present generation of technicians." He continues, "These days, in the FRI control room, the FRI technicians seem to enjoy using the semi-automatic procedure software. It collaborates, for them, their recollections, judgments, and decisions regarding next steps. They say, 'It's like having our best board "man" alongside us in the control room all of the time.'"
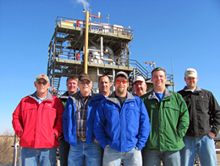
Unit operators are happy to use Exapilot and Exaquantum
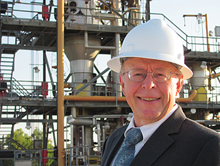
Mike Resetarits, Technical Director
Przemysł
-
Rafinerie
In the ever changing marketplace, refineries are seen not only as crude processing units but also as profit centers. At the same time, there is a keen awareness of the need for safety at such facilities. A total production solution that encompasses planning, scheduling, management, and control is required to achieve long-term goals for profitability, efficiency, and environmental protection. With years of expertise in the automation field, Yokogawa can bring you affordable total solutions for improved operability and a cleaner world.
-
Ropa i gaz downstream
The oil & gas downstream industry has been facing an increasing number of challenges in recent years. These include the changing characteristics of the feedstock to be processed, aging of process facilities and equipment, rising cost of energy, lack of skilled plant operators who can run a refinery safely and efficiently, and the ever-changing requirements from both the market and the customer.
Over the years, Yokogawa has partnered with many downstream companies to provide industrial solutions focused on solving these challenges and problems. Yokogawa's VigilantPlant solutions have helped plant owners to achieve maximum profitability and sustainable safety within their plants.
Powiązane produkty i rozwiązania
-
Procedural Automation (Exapilot)
Procedural Automation (Exapilot) provides a flexible methodology to capture, optimize and retain procedural knowledge in a process plant while meeting requirements in reliability, flexibility, and lifecycle costs.
-
Distributed Control System (DCS)
Our distributed control system (DCS) enables automation and control of industrial processes and enhanced business performance. Over 30,000 systems entrust Yokogawa DCS to deliver their production goals.