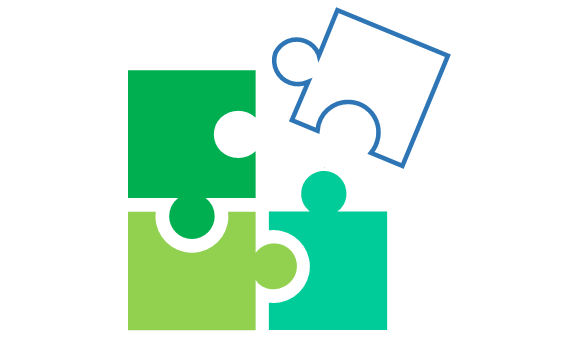
Yokogawa has focused on developing a supply chain that considers environmental protection and human rights. We will actively identify risks that impede sustainable procurement, embark on a path to improvement with our business partners, and strengthen activities aimed at achieving our sustainability goals "Three Goals".
Summary of Activities
1) Activity Policy
We are identifying risks that impede sustainable procurement with our business partners, focusing on understanding the actual conditions of the following 4 areas(defined in Yokogawa Group Sustainable Procurement Guidelines for Suppliers) : "Labor and Human rights" "Health and safety" "Environment" and "Ethics". In case a risk is realized, we work with our suppliers to take measures against it. We also develop educational programs on sustainable procurement both inside and outside the company. We set KPIs to manage and measure the progress of sustainable procurement activities.
2) Activity System
Yokogawa Electric Corporation Global Business Service Headquarters has established a sustainable procurement policy that incorporates human rights due diligence (DD) in the supply chain. We are actively implementing sustainable procurement activities in collaboration with our group affiliates Product and Business Divisions.
The Global Business Service Headquarters has established common rules for the group, such as items to be checked when initiating transactions, and each affiliate/Business Divisions is monitored through the procurement process. We gather various types of information, including transactional details and supplier information, from our affiliates who directly interact with suppliers. In addition, concerning transaction information, we use integrated systems and other product business information among group affiliates for data analysis as a view of Yokogawa group.
Overview of Suppliers
1) About our Suppliers
The Yokogawa Group deals with more than 10,000 suppliers in 70 countries annually. The FY2022 procurement status by country surveyed in sending out the FY2023 SAQ is shown below:
2) Communication and Education with Suppliers
We are actively engaging with key suppliers in each region by interacting with their management and key personnel, aiming to enhance our partnerships.
For example, we regularly hold "Partners' Day" events to provide explanations on our management policies, business plans, and procurement strategies. These events also serve as educational platforms where we promote the understanding of environmental policies and legal regulations related to the supply chain, using the "Sustainable Procurement Guidelines" Booklet.
In addition, we organize "Component Exhibitions" and "Technical Seminars" by our providers where we offer a platform to showcase their products, market trends, and component updates to our product development teams.
SAQ Activity Report
We implement a PDCA cycle for evaluating and improving CSR risks using SAQs (self-assessment questionnaires) for suppliers. The period from 2020 to 2022 is designated as Stage 1, and from 2023 onwards as Stage 2.
1)PDCA Cycle of Activities
In Stage 1, starting in 2020, we worked on lowering CSR risks in the supply chain with a focus on human rights due diligence. From 2023, we began Stage 2, which includes environmental considerations.
The cycle for promoting sustainable procurement using SAQ is illustrated below.
We select our key suppliers based on various factors, including transaction data such as transaction amounts and transaction details mentioned earlier, information obtained from affiliates’ procurement departments, and compliance with regulations.
2)SAQ Implementation Process
We select important suppliers (approximately 600) for SAQ (Supplier Assessment Questionnaire) based on transaction information data and other relevant information, using specialist knowledge and logic. Over three years, our affiliates’ procurement departments, which handle direct communication had divided the task and requested the implementation of SAQ from approximately 200 companies annually. These suppliers are asked to respond to questions related to sustainable procurement at their own company or their providers, covering areas such as policies, organizational structure, labor rights, occupational health and safety, and environmental practices. We will convert the responses we receive into numbers and analyze them to conduct a risk analysis. We will also return the SAQ to each business unit that submitted it, along with information such as their score and areas for improvement based on the questionnaire results, as well as a graph comparing the average score of other business units.
Please refer to the chart below.
3)KPI Monitoring
We continue to record the responses to the SAQ from 2020 (Stage 1) and our requests, and analyze changes in the responses of individual suppliers and trends in the overall average score.
In Stage 2, we place emphasis on engagement with business partners, and compare the average percentile values of business sites that responded to the SAQ as critical suppliers in both Stage 1 and Stage 2 for the items "human rights and labor" and "occupational health and safety" that are common to Stage 1 and Stage 2. (Since the questions are different, we cannot compare the scores themselves, so we compare the percentile values.).
The percentile indicates the ranking of the responding companies and whether there are any other facilities that have a lower score than the one in question; a higher number can be inferred to mean that there has been improvement.
About Risk Analysis
We conduct risk analysis based on the answers to the SAQ and other information.
1)SAQ score analysis
We conduct detailed analysis of responses to the SAQ and attitudes regarding response submission, and instead of just calculating averages, we continually record the score distribution for each field, such as "human rights and labor," "occupational health and safety," and "environment," and analyze responses to our requests to analyze changes in individual supplier responses, trends by category, and overall average scores. The distribution of overall scores is shown below.
The histogram of overall scores for the submitted issues is shown below. In addition, although we do not make the results public, we identify trends by item and response and conduct risk assessments.
2)Other Investigations apart from SAQ
We have verified the information provided on CMRT (Conflict Minerals Reporting Template) sheets for purchased goods containing 3TG materials and confirmed that there have been no purchases from high-risk smelters over the past three years.
In addition, when necessary, we check whether our suppliers are listed on the entity list. Currently, we do not find their names on the list.
Education for Implementing Sustainable Procurement
1)Confirmation of Sustainable Procurement Policy for Yokogawa Procurement Members
We are holding meetings with global procurement members to discuss issues and deepen our knowledge about sustainable procurement, using the Sustainable Procurement Guidelines Handbook that we have distributed to the above-mentioned suppliers.
2)Subcontract Act
Our products are supported by excellent subcontractors. In fiscal 2023, we asked 42 subcontractors to carry out the SAQ, and received responses from 36 of them. In the implementation, in early 2024, in light of changes to payments for subcontracting transactions, we will conduct study of our original textbook linked to the purchasing system and a simple test for approximately 3,000 domestic employees involved in purchasing and payment, not only to improve their knowledge but also to raise interest in our suppliers.
3)Encouraging Suppliers to Promote Sustainable Procurement
In order to encourage small and medium-sized enterprises to engage in sustainable procurement, we actively participate in JEITA(Japan Electronics and Information Technology Industries Association) and GCNJ(Global Compact Network Japan) working groups, developing tools and providing educational opportunities.