Yokogawa's regulatory control stabilization service is a packaged service product including necessary engineering and consulting services to stabilize safety, improve efficiency, and reduce operators’ workload.
Click here to learn about Regulatory Control Stabilization
Key areas for Operational Excellence Transformation
Operational Excellence Transformation is Yokogawa and KBC’s co-innovated portfolio of solutions and services.We provides comprehensive solutions for business automation in all four areas using consulting and digital technology.
Operational Risk Management
Yokogawa's Operational Risk Management deals with managing safety, health and environmental risks on both individual and process levels in a reliable and risk-free manner. It involves the end-to-end process of designing, visualizing and orchestrating plant production and business systems.
Key Operational Competencies in Operational Risk Management
- Process Safety Management: Maintain License to Operate, preserve Business Reputation, and create value by utilizing and adhering to operating integrity processes to prevent loss of containment or catastrophic loss
- Personal Safety Management: Protect human assets by providing safe practices to improve behavior and culture
- Environmental Management: Provide processes to protect the environment through operating integrity, and ensure compliance with environmental, regulatory and/or internal requirements
- Community Relations: Define and establish processes and protocols to communicate and implement emergency response plans, and enhance interactions in the community
- HSSE Reporting and Compliance: Assure visibility and achievement of HSSE goals and compliance requirements, by monitoring, learning and improving continuously through processes, initiatives and KPIs
- Plant Protocols and Security: Provide processes and strategies to protect assets and infrastructure from threats, and control access to vulnerable processes and equipment
By combining Yokogawa’s product portfolio and KBC’s consulting services, we provide our customers best practices and domain knowledge that empower them to improve their operations, as well as a digital platform that supports such activities and initiatives. Our Operational Risk Management scope does not only cover partial improvements in the organization, but also optimizations in plant operations to achieve continuously improving safety, reliability and operability.
·Supply Chain Optimization
- Optimize management of supply, whether oil in the ground or feedstocks for a refinery or chemical asset, in light of product market demands. This provides operators with the agility to take full advantage of market conditions.
·Asset Operations and Optimization
- Optimize the potential of physical assets, by pushing throughput and maximizing the production of the highest value products, whilst minimizing variable costs such as energy.
- Deliver small and large capex projects, on time and on budget, to deliver growth and meet environmental requirements.
·Asset Management and Integrity
- Confidently ensure asset reliability and availability, whilst controlling maintenance costs. This assures the asset always meets expectations and is always available to capitalize on short term market opportunities.
Regulatory Control Stabilization
As raw material costs increase this is drawing increasing attention towards improvement of process efficiency, all industries now recognize Regulatory Control Stabilization to be the baseline step for all process efficiency initiatives. In depth evaluation is required to improve the effectiveness of the regulatory control loops and achieve regulatory control stabilization (e.g. control configuration, PID tuning, instrumentation).
Regulatory control stabilization and PID loop tuning are also pre-requisites for advanced process control (APC) implementation. Yokogawa's decades of hands-on experience as a global supplier of process automation solutions have provided a wealth of knowledge and understanding in regulatory control loops, both before and after APC implementation.
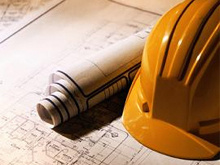
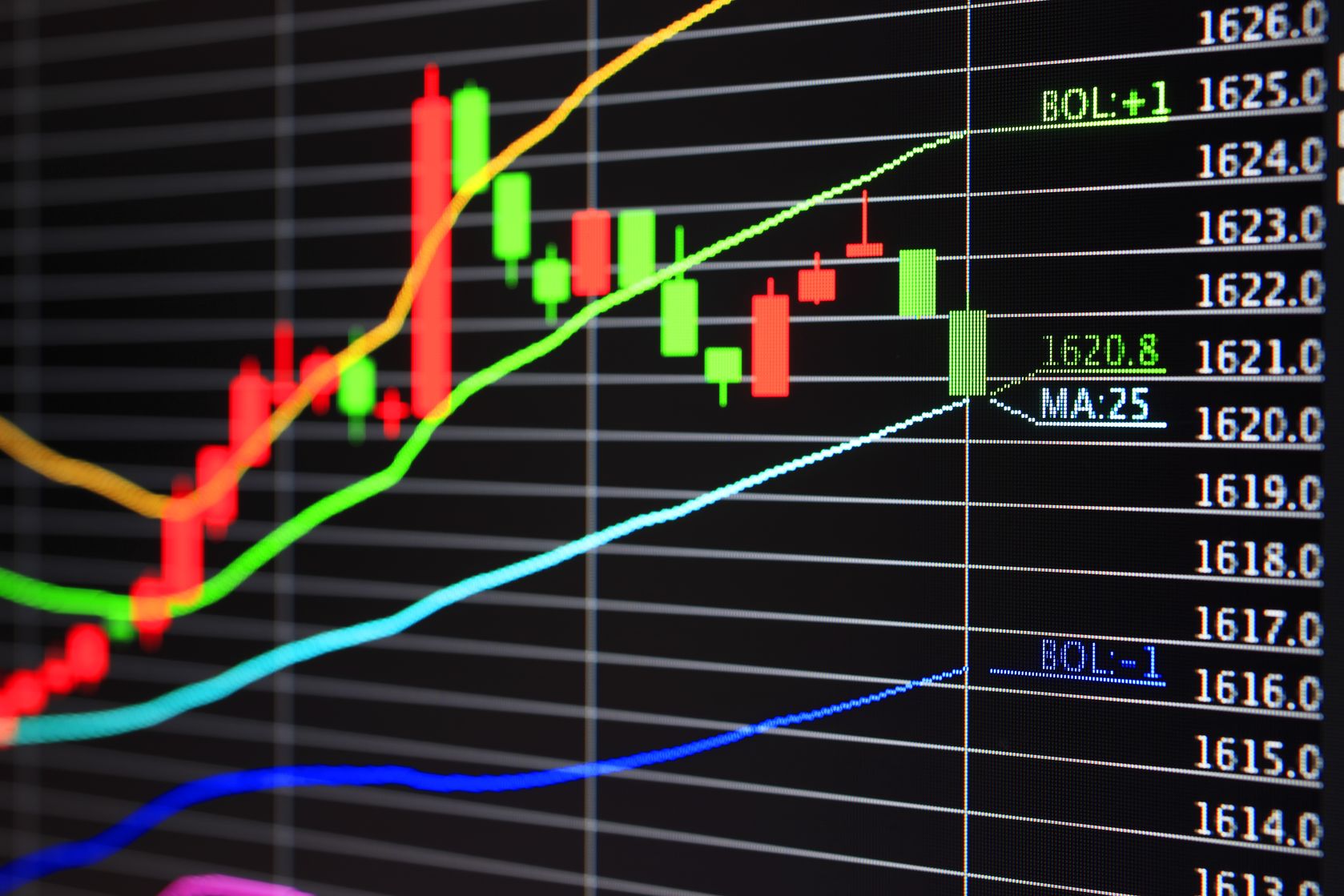
Customer Challenge
Quality, Efficiency, and Operators Workload Significantly Impact Profitability
Problematic control loops negatively affect many aspects of your plant. PID setup and tuning without a proper methodology lead to trial-and-error tuning, leaving the total regulatory control strategy sub-optimized and lacking a consistent control objective across all control loops (e.g. averaging level control).
Plant safety is paramount to the continuance of production operations and all process industries now recognize the importance of regulatory control stabilization as the baseline for plant safety. To achieve stability, plants must evaluate and improve the effectiveness of regulatory control loops (e.g. control configuration, PID tuning, instrumentation).
Also, control loops operated in manual mode require careful monitoring and overall have poor performance. They will lead to an increase in operators’ workload and are unable to maintain the consistent safety, product quality, and economical efficiency of your plants.
Our Solutions
Regulatory Control Optimization to Enable Improved Production
Yokogawa's regulatory control stabilization service is a packaged service product including necessary engineering and consulting services to stabilize safety, improve efficiency, and reduce operators’ workload.
Tune VP is designed to estimate the optimized P, I, D tuning parameters for the PID controllers reside in FCS of CENTUM DCS system. This application provides an effective and easy to use solution for PID controller tuning with the following key features:
- Online open and closed loop model identification and simulation
- Prevalent and effective model identification algorithm
- On demand P, I, D recommendation based on flexible SV or MV step test
- Auto detection of operational change for P, I, D recommendation opportunity
- Easy use by non control specialist
- Loop tuning history report and PID log book
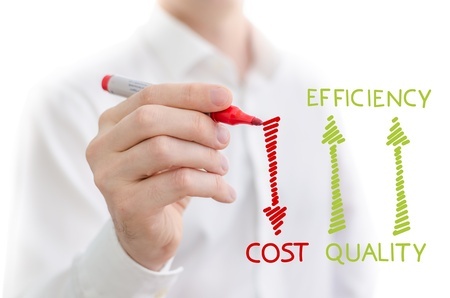
Customer Benefits
Economical Efficiency Now, Optimization Opportunities for the Future
The benefits of APC are vast. Companies can enjoy near immediate benefits in economic efficiency and safety, while several optimization opportunities are possible for the future. More specifically:
- Economical Efficiency through reductions in energy consumption
- Improvements in product quality through process stabilization
- Operators’ Workload is improved by automating troublesome control loops and reductions in Reduce painful manual-mode board operation
- Improvements in HSE (Health, Safety, Environment) are realized by avoiding plant upset with well-stabilized controls and a conservation environment with low-emission control
- Prepare for APC implementation allows for further optimization in the future
Enabling Technology
TuneVP
TuneVP is designed to estimate the optimized PID tuning parameters for various PID controllers such as CENTUM DCS, Foundation Fieldbus Controllers, GE Fanuc PLCs, etc.
Process dynamic response data obtained from step testing or normal operational setpoint value (SV) or manipulated output value (MV) change are collected via OPC interface. Transfer function model is derived from MV and PV (process variable) data relationship. Based on the model, IMC tuning method is used to calculate the optimized PID parameters, in tandem with the closed loop PID controller response simulation.
Details
Temperature Control Stabilization
Process: BTX plant
Purpose: Reduce the fluctuation of tray temperature in distillation column
Benefits: Stabilize product quality and reduce the number of operator intervention (MV change in manual mode)
Averaging Level Control
Process: De-ethanizer
Purpose:
- Reduce the fluctuation of de-ethanizer feed which is generated by improper level control tuning of de-butanizer accumulator
- Stabilize the tray temperature and product quality (C2 in propane) of de-ethanizer
Benefits: Stabilize product quality (C2 in propane) and increase propane yield
Operating Ratio Improvement in Closed Loop
Process: Chemical plant
Purpose:
- Reduce the number of control loop operations (e.g. SV/MV change, mode change)
- Increase the operating ratio in auto mode (closed loop) of control loops
Benefits:
- Reduce operators’ workload
- Reduce loop operations for 13 tags by 40% (3,700 à 2,200 operations)
*Deliverable of a full Service Report at the final stage
Middelen
- Yokogawa's operational performance program bench mark service enhanced the automation performance at the chemical plant.
- Operator stress was dramatically reduced by identifying the causes of excessive manual interventions.
Op zoek naar meer informatie over onze mensen, technologie en oplossingen?
Contact