No alternative products are available for this product.
Why Chemical Injection?
In the oil and gas industry, securing flow assurance plays a key role in maintaining production efficiency. During the production process, various substances contained in the producing fluid adhere to the inside walls of pipes. The accumulation of substances causes problems like corrosion, clogging and scaling, which potentially lead to catastrophic failure of assets and extensive operational downtime. To prevent such serious problems, certain chemicals are injected into the pipes. This process is called “chemical injection,” and improving the efficiency of this process is crucial.
Major challenges of the conventional chemical injection systems include:
A Game Changer in Chemical Injection
Yokogawa’s “FluidCom” is a fully automated chemical injection flow controller.
It integrates four components, which are the flow control valve, actuator, flowmeter and controller, into one module. With its minimal mechanical moving parts and self-cleaning mechanism, it doesn’t require regular maintenance.
This game changing chemical injection flow controller solves challenges that conventional chemical injection systems are facing today.
![]() |
![]() |
![]() |
|
Challenges | Challenge 1: Frequent manual flow rate adjustments/maintenance |
Challenge 2: Unstable chemical injection rates |
Challenge 3: Work under harsh environment |
---|---|---|---|
![]() |
![]() |
![]() |
|
|
|
|
|
FluidCom’s Benefits |
|
|
|
FluidCom’s Features |
|
||
Outcomes |
|
* Some graphs and images are quoted from the eBook ("Become Smarter with the New Industry Standard to Digitalize your Chemical Injection Process") created by Frost & Sullivan.
Detalles
Customers’ Challenges
Challenge 1: Frequent Manual Flow Rate Adjustments/Maintenance
Although some parts of chemical injection processes in conventional systems have been automated, the majority of them are still manually operated. In the systems that are manually operated, injection flow rates are unstable and need to be adjusted whenever deviations are found. The frequency of the adjustments depends on oil wells’ ambient conditions such as pressure, temperature, viscosity and specific gravity, and there are cases where adjustments are needed every few hours. Also, the conventional systems consist of multiple components. The more components they have, the more maintenance that is required. Such manual interventions result in huge labor costs.
Challenge 2: Unstable Chemical Injection Rates
There are mainly two types of chemical injection systems adopted by oil and gas companies. One type of system injects chemicals directly from a pump, controlling discharge rates by adjusting the stroke length of the pump. The other type of system uses Injection Rate Control Device (IRCD) to regulate injection rates.
In many cases, discharge rates or injection rates are set by manual manipulation. However, the discharge rate often drifts from the set rate, which is affected by changes in pressure at the injection point, chemical viscosity or ambient temperature. When chemical injection rates go underdosing, it may cause tremendous detriment to assets. Consequently, most operators tend to set the discharge rate 10 to 20 percent higher than the stipulated rate to prevent being underdosed, which leads to excessive chemical cost.
Challenge 3: Work under Harsh Environments
In order to maintain production efficiency, operators on offshore platforms work under harsh environmental conditions. However, some challenges need to be solved. These include reducing long working hours in high-risk situations as well as having operators do multi-week shifts on offshore platforms.
Benefits of FluidCom
![]() Frequent manual flow rate adjustments/maintenance |
![]() |
FluidCom, with its autonomous valve control system, can keep chemical injection with accurate and stable flowrate despite of external disturbances. It does not require manual operation to adjust the flowrate. Hence it can reduce labor cost eliminating manual operation. |
![]() Unstable Chemical Injection Rates |
![]() |
Mass flowmeter function and flow control function equipped in FluidCom make it autonomous control device. FluidCom can prevent both over injection and under injection of chemical which optimizes the chemical consumption. Hence it can reduce chemical cost. Customarily chemical injection rate is set to the system higher than the rate optimally calculated. Because the operator didn’t like the injection rate fluctuates and goes under injection which leads the assets to tremendous detriment. |
![]() Work under Harsh Environments |
![]() |
FluidCom can save technicians from visiting plant site to manipulate valves to adjust the chemical flowrate, which enhances the health and safety of them. Keeping the right volume of chemical injection reduces the environmental footprint. This improves HSE (Health, Safety, Environment) and helps the attainment of SDGs. |
Technology
1. Autonomous Valve Control
FluidCom’s autonomous valve control delivers accurate and stable chemical injection rates. The operating principle is very simple. FluidCom has a heater, a metal cylinder, a valve, and sensors. When power is applied to the heater, the metal cylinder heats up and expands, which makes the valve open in order to increase the flow rate. On the contrary, when power to the heater is reduced, the metal cylinder cools down and contracts, which makes the valve close in order to decrease the flow rate. The power to the heater is adjusted as the sensors monitor the chemical flow rate.
As a result, significant manual adjustments are no longer required, and labor costs are hugely reduced.
Operating Principle
Providing power to the heater makes the outer tube expand longitudinally moving the seat in relation to the pin enabling increased flow. Reducing power to the heater will make the outer tube retract and decrease the flow.
Temperature sensor (T1) measures the fluid temperature on the inlet prior to entering the heated section,
Temperature sensor (T2) measures the fluid temperature exiting the heated section.
The amount of thermal energy absorbed by the flowing fluid through the device allows the calculation of the Thermal Mass Flow. Thermal Mass Flow is calculated using the following equation:
From this equation, FluidCom’s internal control algorithm will control the heater power, and in turn control the fluid flow rate.
2. Virtually Maintenance Free with Its Self-Cleaning Mechanism
FluidCom has a self-cleaning mechanism in its flowline.
When chemical particles hinder the chemical flow rate, the valve automatically opens to flush the particles. With this mechanism, regular maintenance is no longer required.
Unique Self-Cleaning Capability
- If clogging is identified, FluidCom will automatically increase the flow rate opening the outlet valve fully to allow for debris/deposits to be flushed over the valve seat.
- As shown in the figure typically the auto clean function is shown by a spike in the flow rate and then a gradual return to the pre-determined chemical injection rate.
- The Self-cleaning functionality found in the FluidCom resolves the most common problem of plugging in a conventional valve which leads to periodic mechanical maintenance.
3. Integrated into One Module/Minimal MechanicalParts
FluidCom integrates the flow control valve, actuator, flowmeter and controller into one module. Fewer components require less maintenance.
Also, unlike conventional chemical injection systems, FluidCom uses few mechanical moving parts. This lowers the risk of malfunction and eliminates the burden of spare parts inventory management.
4. Independent of Pressure and Temperature Fluctuations
In conventional chemical injection system, chemical dosing rates are usually set higher than an optimal rate to avoid drifting to underdosing which could cause serious asset damages . This is because chemical dosing rates with conventional valves are affected by changes in temperature, differential pressure and chemical viscosity. However, FluidCom delivers accurate and stable chemical dosing where deviation is ±5 % from the set point regardless of ambient variables.
This enables a reduction of 5 to 15 % of chemical costs when a conventional system ought to be operated in the range of 10 to 20 % of excessive chemical dosing.
e.g.
Ideal flow rate: 15 L/h
Chemical cost: 5 USD/L
Assumed that your chemical injection system is overdosing chemicals 20 % more than the set flow rate.
Conventional: 15 × 1.2 (+ 20 % accuracy) = 18 L
FluidCom: 15 × 1.05 (+ 5 % accuracy) = 15.75 L/h
Chemical Cost reduction:
( 18 - 15.75 ) × 24 × 365 × 5 USD = 98,550 USD per injection point
* It depends on the process condition.
* This is only for 1 injection point.
5. Reduced Footprint/Size/Weight
FluidCom integrates the flow control valve, actuator, flowmeter and controller into one module. This reduces the overall footprint by a quarter compared with conventional chemical injection systems and provides operators to safe working space.
The Next Generation of Chemical Injection Valve & Metering Devices
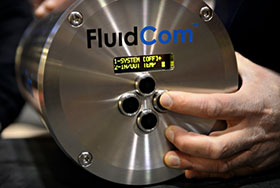
Yokogawa TechInvent has developed a unique integrated device for chemical injection valve and flow meter, FluidCom. It provides flow control and flow metering with one module using a unique combination of material and thermal effects.
FluidCom chemical injection controller is a fully automated, simple and reliable device equipped with autonomous valve controller, flow metering function, and self-cleaning mechanism.
Since FluidCom adopts minimal mechanical moving parts in its configuration, it provides users with an accurate, reliable chemical injection with maintenance free operation.
Introducing Chemical Injection Metering Valve, FluidCom
Customer Benefits
1. FluidCom Delivers Tremendous Labor Cost Savings
- Autonomous valve control eliminates overdosing, hence saves chemical consumption
- Integrated thermal flow meter always monitors chemical flowrate and feedback to valve control
- Valve control is independent from pressure and temperature fluctuations
2. FluidCom Delivers Tremendous Labor Cost Savings
- Fully automatic operation of FluidCom does not require technicians go to site for the adjustment of control valves or pump strokes.
- Using an optional remote-control communication line, 4-20mA or HART, flow settings and flow readings are possible in control room.
3. FluidCom Is a Maintenance Free Device
- FluidCom adopts minimal mechanical moving parts in the configuration. Users are not required to keep any spare parts for maintenance.
- FluidCom has self-cleaning mechanism in its flowline. When chemical particles hinder the flow, FluidCom automatically open the valve to flush the particles. Then, after the cleaning process, flow returns to normal.
4. FluidCom Delivers Tremendous Space and Weight Savings
- FluidCom replaces conventional flow control valve, actuator, flowmeter and controller. All the functions are packed in one module. Thus, it occupies less space and weight.
- FluidCom requires only one cable, power cable 230VAC, and chemical tubing, inlet and outlet. Thus, installation can be done quick and simple.
Specification Summary
FluidCom chemical injection valve and metering controller is a fully automated, simple and reliable device equipped with integrated autonomous valve control, continuous flow metering and self-cleaning functionality.
Temperature induced viscosity changes are known to greatly affect the flow rate in conventional chemical injection control valves, resulting in unstable and inaccurate flow. Over and/or under dosing has significant economic, operational and environmental consequences, and the need for daily manual adjustment, downtime and high maintenance costs has resulted in pain for the operators for years.
With the FluidCom chemical injection solution, flow control is achieved by a controlled heater that causes thermal expansion in tubes for fluid flow, whereby this thermal expansion is used to choke and control the fluid flow through a unique flow control arrangement.
In the system, a thermal balance exists between the applied energy for thermal expansion in tubes (and rise of fluid temperature) and the mass of the fluid flowing. Any undesired deviations in mass flow will affect the thermal balance, and the valve will autonomously start compensating flow until the thermal balance and flow set point are re-established, independent of what caused the deviations.
This gives FluidCom the unique advantage to keep flow at a set point independent of variations in pressure, temperature, viscosity or specific gravity. In addition, the valve offers a self-cleaning functionality by its thermal autonomous behavior.
Mass flow metering is achieved by measuring the fluid temperature rise through the device. By knowing the controlled heat energy applied and the fluid heat capacity, the actual mass flow is continuously measured, reported and controlled.
Technical Specifications
Flow Range | Standard 0.6 to 30.0 L/h (Extended flow range available) |
---|---|
Design pressure | 5000 psi (345 bar) |
Operating temperature ambient |
-20 °C to +55 °C |
Material enclosure | AISI 316L SS |
Material wetted parts | AISI 316 SS/PEEK/FFKM/Ceramic (others available on request) |
Power supply | 230 to 240 VAC 50/60 Hz |
Dimensions and Weight |
Ø219 mm x 353 mm, 17.5 kg |
Explosion proof | ATEX and IECEx |
Ingress Protection | IP66 |
Valve failure mode | Closed |
Interface pipe connection |
1/4" NPT Female (others available on request) |
Communication | Local Display with Push Button |
4 to 20 mA, two-wire transmission with HART 7 |
|
Optional 4 to 20 mA for set-point |
Realize Optimal Chemical Injection Using FluidCom
FluidCom Enhances Ownership Proving Tremendous Opex Reduction
- Closed loop control to maintain injection rate
- Remote setting of injection rate
- Small footprint to save space
- Maintenance free operation
- self cleaning system to prevent clogging
- Stable injection rate guarantees within ±5 % of set rate
FluidCom Consists of Four Functions
- Control valve
- Actuator
- Flowmeter
- Controller
FluidCom Enhances Ownership Proving Tremendous Capex Reduction
- Installation of multiple FluidCom can eliminate heavy and costly multi-head pumps.
- Each FluidCom can be set individual injection rate with accuracy.
ROI Calculator
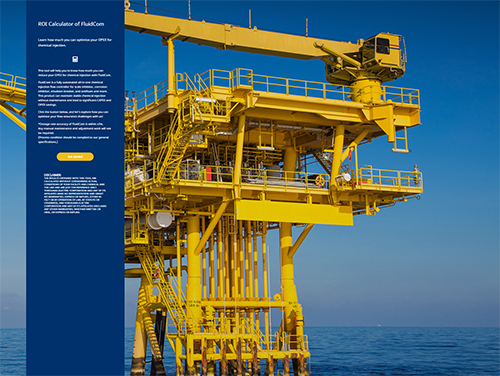
Welcome to our ROI Calculator site!
This tool will help you to know how much you can reduce your OPEX for chemical injection with FluidCom.
Please enter the values of your existing chemical injection system and we will provide you with potential OPEX savings by using FluidCom.
ROI Calculator
¿En busca de información adicional sobre Yokogawa Iberia, tecnología y soluciones?
Contáctenos