"Temperature Monitoring Solutions for Early Detection of Abnormal Overheating in Bus Ducts (Bus bars)"
> Link to Document Download Page
What if you could detect signs of abnormalities in bus ducts (bus bars) quickly during maintenance and inspection work and respond to them at just the right time? Yokogawa DTSX monitoring solution constantly monitors connections that tend to deteriorate over time and contributes by pinpointing abnormality locations and reducing workload of maintenance personnel, helping to ensure stability in plant operations.
Overview
Because bus bars are conductors that carry large electrical currents to manufacturing equipment, they are often covered with bus ducts, making visual inspection difficult. In addition, bus ducts (bus bars) are generally routed through ceilings, high places, or under floors, and it is not unusual for maintenance and inspection to require dangerous or harsh conditions.
The Fiber Optic Temperature Sensor DTSX provides a solution that contributes to stable plant operations by enabling efficient and accurate maintenance of bus ducts (bus bars).
Customer Challenges
Loose Bus Bar Connections
Bus bar connections and branches are generally bolted or clamped. A bolted connection, for example, may loosen due to an earthquake or a temperature rise in the bus bar itself, and this can lead to various risks or accidents.
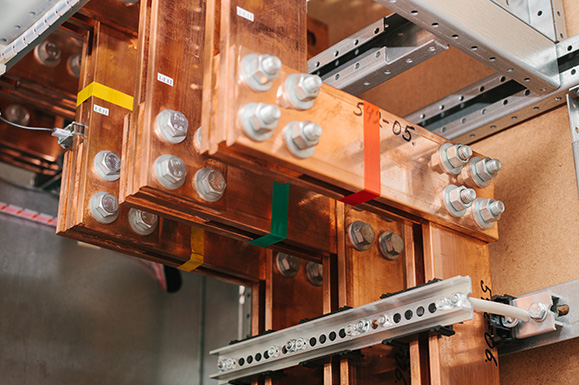
Power Supply Interruption Risk
If the bolts used in the bus bar connection loosen, this may lead to an increase in electrical resistance in the area, causing temperature to rise. Overheating causes greater electrical resistance, which raises the possibility of operational shutdown due to damage in the bus duct (bus bar) and stoppage of electrical supply.
Increased Workload in Maintenance and Inspection
Some methods for maintenance and inspection include attaching thermo labels to bus ducts near bus bar connections and making patrols using thermal cameras. However, bus ducts (bus bars) can be connected several hundred meters in length or more, and visual inspection of such a huge number of connection points is no easy task.
Challenge of Retaining Personnel Due to Harsh Working Environment
In many cases, bus ducts (bus bars) are routed inside factory ceilings, in high places, and under floors. Although the stable operation of bus ducts (bus bars) requires constant monitoring, the working environment is harsh and can be unsuitable for human monitoring, so retaining personnel can be a major challenge.
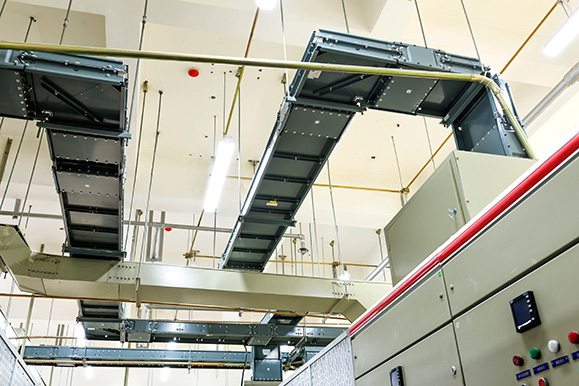
Products & Solutions
1. Constant Monitoring with Optical Fiber Temperature Sensor
DTSX is a temperature sensor that can provide 24 hours, 365 days monitoring of temperature changes over long distances and wide areas using sensing technology that takes advantage of the characteristics of fiber optic cable.
DTXS can be laid out following the path or shape of the object to be measured, so it can be laid on the surface of bus ducts, contributing to predictive maintenance of bus ducts (bus bars).
2. Locating Abnormalities without Effects of Electromagnetic Noise
Bus bars that carry large currents cause strong electrical fields around them, making it difficult to measure temperatures with thermocouples or other electrical sensors. Thermal cameras cannot be used to monitor bus bars because they are spread over wide areas and complex routes.
However, DTSX uses fiber optic cables that are unaffected by electromagnetic noise even when subjected to strong electrical fields, so they can accurately and quickly identify abnormal overheating locations, allowing appropriate action to be taken.
3. Making Bus Duct (Bus Bar) Maintenance and Inspection More Efficient
DTSX can quickly and accurately monitor temperature distribution every one meter and pinpoint abnormal overheating location, contributing to faster initial response.
If any signs of abnormality are found in the bus duct (bus bar), bolts can be tightened and other work can be performed at the appropriate timing, helping to make maintenance and inspection work more efficient.
Anticipated Benefits
-Provides Constant Monitoring Over a Wide Area
It can provide accurate temperature monitoring with no blank areas, even when there are strong electrical fields or complex areas for measurement.
-Enables Predictive Maintenance of Equipment
It provides 24 hours, 365 days monitoring without missing any temperature changes, contributing to predictive maintenance of equipment.
-Contributes to BCP
It prevents power supply shutdowns caused by bus bar temperature abnormalities, minimizing the losses that result from production cuts, late delivery penalties, and lost opportunities.
-Reduces Maintenance Personnel Workload
It optimizes the intervals between inspections, realizing easier workloads for maintenance workers.
How Temperature Monitoring with DTSX Works
Measuring Temperature Using the Intensity of Raman Scattered Light
Pulses of light launched into an optical fiber propagates down the fiber while producing backscattered light with different wavelengths from the launch of the light source. The intensity of this light, which is called Raman scattered light, correlates with the temperature, and DTSX uses this to monitor the temperature of the installation site.
Pinpoint Measurement Every One Meter
DTSX monitors temperatures at one-meter intervals by calculating the round-trip time and the speed of light launched into an optical fiber. For example, with a 6 km optical fiber, 6,000 temperature points can be measured. Monitoring points can also be pinpointed every one meter.
Looking for more information on our people, technology and solutions?
Contact UsIndustries
-
Chemical
Chemical plants rely on continuous and batch production processes, each posing different requirements for a control system. A continuous process calls for a robust and stable control system that will not fail and cause the shutdown of a production line, whereas the emphasis with a batch process is on having a control system that allows great flexibility in making adjustments to formulas, procedures, and the like. Both kinds of systems need to be managed in available quality history of product, and to be able to execute non-routine operations. With its extensive product portfolio, experienced systems engineers, and global sales and service network, Yokogawa has a solution for every plant process.
-
Food & Beverage
At Yokogawa, we understand that today’s food and beverage companies face unprecedented challenges in climate change, consumer demand, and increased global competitiveness. Overcoming these challenges will require innovative solutions that focus on key areas of production, asset management, and food safety and quality.
-
Iron & Steel
In the iron and steel industry, it is crucial to improve the quality of not only products but also manufacturing and operation technologies, as well as to address environmental and energy-efficiency issues. Yokogawa helps customers to create the ideal plant and evolves with them for mutual growth.
-
Oil & Gas
Yokogawa has a wealth of experience in every part of the oil and gas business, from offshore and onshore facilities to pipelines, terminals, and deepwater operations. We provide solutions that enhance safety, ensure accurate and reliable operation, and increase plant efficiency.
-
Pharmaceutical
Pharmaceutical companies must achieve increased flexibility and agility through better use and monitoring of manufacturing data to improve quality management in real time. Pharmaceutical experts work with Yokogawa to create manufacturing solutions that deliver safe and reliable medicines. Together, we use digital transformation and manufacturing advances to meet regulatory requirements, ensure quality, accelerate time to market, and thus providing a stable and reliable supply of medicine to patient.
-
Power
In the mid 1970s, Yokogawa entered the power business with the release of the EBS Electric Control System. Since then, Yokogawa has steadfastly continued with the development of our technologies and capabilities for providing the best services and solutions to our customers worldwide.
Yokogawa has operated the global power solutions network to play a more active role in the dynamic global power market. This has allowed closer teamwork within Yokogawa, bringing together our global resources and industry know-how. Yokogawa's power industry experts work together to bring each customer the solution that best suits their sophisticated requirements.
-
Pulp & Paper
The paper and pulp industry is highly competitive and must meet ever-changing market needs. Yokogawa helps realize energy-efficient plants which are globally sustainable.
-
Renewable Energy
Renewable energy helps protect the environment and brings both society and industry closer to the goal of achieving sustainability. We provide solutions for renewable energy applications worldwide, thus contributing to the sustainable development goals. In 2024, Yokogawa strengthened its commitment to innovation in the energy transition by acquiring BaxEnergy, a global leader in renewable energy software solutions. BaxEnergy serves as the digital engine driving Yokogawa's renewable energy vision, specializing in asset performance management, energy control, and data analytics.
-
Semiconductor
Yokogawa provides the products and solutions that support for the semiconductor industry.
Related Products & Solutions
-
DTSX1 Fiber Optic Heat Detector
DTSX1 stores the functions required for heat detection in one box. DTSX1 analyzes the temperature data with high accuracy by measuring with fiber optic sensor cable and perform high temperature heat detection.
-
DTSX200 Distributed Temperature Sensor
The DTSX200 is a standard version that is ideal for temperature measurement, for medium-sized areas, and for areas where the distance of fiber optic sensor cables is short. It has excellent environmental resistance because it consumes less power and is less dependent on the temperature measurement environment.
-
DTSX3000 Distributed Temperature Sensor
The DTSX3000 is a distributed temperature sensor developed in response to the demand that “one unit be used to monitor temperature distribution a longer distance and a wider area”. A flagship model that meets the expectations for long-distance temperature measurement and high temperature resolution.
-
Fiber Optic Temperature Sensor DTSX
The DTSX fiber optic temperature sensor, which uses optical fiber for the temperature sensor, quickly detects and locates abnormalities in equipment by monitoring temperatures at production facilities located far away and across wide areas 24 hours a day, without omission. Highly accurate predictive maintenance avoids downtime and ensures stable plant operation.