About TOL's New Oleochemical Plant
Oleochemical samples
In response to rising demand in Thailand for oleochemicals, which are environmentally friendly biodegradable substances used in applications such as fuels and personal care products, Thai Oleochemicals Co., Ltd. (TOL) has recently completed the construction of a new oleochemical production facility. The new plant is located at the Map Ta Phut Industrial Estate in Rayong, Thailand, which is 160 km southeast of Bangkok, and is capable of annually producing 100,000 tons of fatty alcohol, 200,000 tons of methyl ester (ME), and 31,000 tons of glycerine from crude palm oil.
The ME produced at this plant is blended with petroleum diesel to create biodiesel, a biodegradable and clean burning fuel than has the same combustion properties as conventional petroleum diesel fuel. To ensure that the new plant would operate reliably and safely, TOL relied on a solution from Yokogawa based on the CENTUM CS 3000 Integrated Production Control System and the ProSafe-RS Safety Instrumented System.
The Challenges and the Solutions
- Multiple licensors and consultants were involved in this project, so a key issue was maintaining consistency in all the information and specifications handled during the engineering stage. From the beginning of this project to the completion of the plant startup phase, Yokogawa's engineers worked with everyone on the project team to ensure a successful conclusion.
- Only four months were allocated for hardware installation and plant start-up. Within this tight timeframe, the CENTUM CS 3000 and ProSafe-RS system hardware had to be installed in the plant's control and rack rooms and their functions checked. Transmitters were also installed and loop checks were performed. Many software changes had to be accommodated quickly and flexibly. All this work was performed within specifications and on schedule.
- Plant safety and efficiency also had to be maintained by automating plant operations to the maximum possible extent. To accomplish this objective, the ProSafe-RS and CENTUM CS 3000 systems were fully integrated. The combination of feedback and sequence control with the graphic display of trend data, alarm summaries, operator guide messages, and other information have greatly enhanced operations at this plant. The highly reliable CENTUM CS 3000 system has also helped TOL maintain high productivity at this facility.
- Finally, as TOL only has a few DCS engineers who are available to work on these systems at short notice, the company relies on support provided by personnel from Yokogawa's Rayong service office. Its 24/7/365 support is very much appreciated by TOL.
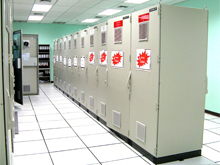
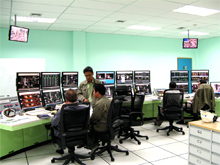
Customer Satisfaction
"Yokogawa's engineers were all very patient and cooperative during the early engineering and start-up phases. We worked as one team through to the completion of this plant project," said Sayan Saesue, TOL's Engineering and Maintenance Division Manager.
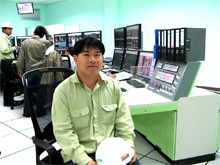
Mr. Sayan
in the control room
<System Details>
Control system: CENTUM CS 3000, ProSafe-RS, CCTV
Transmitters: HART communication
Number of I/O points: 3,000 for CENTUM, 600 for ProSafe-RS
Software package: Exaquantum
업종
-
화학
화학 플랜트는 연속 및 Batch 생산 공정에 의존하며, 각각은 제어 시스템에 대한 다양한 요구 사항을 제시합니다. 연속 공정은 실패하지 않고 생산 라인을 중단시키는 견고하고 안정적인 제어 시스템을 필요로하는 반면, Batch 공정의 중요성은 수식, 절차 및 공정을 조정하는 데 있어 큰 유연성을 허용하는 제어 시스템을 갖추는 데 있습니다. 두 종류의 시스템 모두 제품의 사용 가능한 품질 내역에서 관리되어야 하며 비일상적인 작업을 수행할 수 있어야 합니다. Yokogawa는 광범위한 제품 포트폴리오, 숙련된 시스템 엔지니어 및 글로벌 영업 및 서비스 네트워크를 통해 모든 공장 공정에 대한 솔루션을 제공합니다.
Related Products & Solutions
-
CENTUM VP
CENTUM VP는 HMI(Human Machine Interface), FCS(Field Control Stations), 제어 네트워크(Control Network)로 구성된 단순하고 일반적인 아키텍처를 가지고 있습니다.
-
Plant Information Management System (Exaquantum)
Exaquantum은 공정의 모든 측면에서 데이터를 수집하고 해당 데이터를 쉽게 사용할 수 있고 가치 높은 정보로 바꾸어 제공합니다.
-
SIS (Up to SIL 3) ProSafe-RS
ProSafe-RS는 IEC 61508에 명시된 SIL(Safety Integrity Level) 3을 충족하는 것으로 독일 인증 기관(TÜV)의 인증을 받은 안전 계측 시스템입니다.
-
Distributed Control System (DCS)
10,000개가 넘는 플랜트의 운영자는 매년 생산 목표를 달성하기 위해 Yokogawa의 DCS 기술과 솔루션을 신뢰합니다.