화학 플랜트는 연속 및 Batch 생산 공정에 의존하며, 각각은 제어 시스템에 대한 다양한 요구 사항을 제시합니다. 연속 공정은 실패하지 않고 생산 라인을 중단시키는 견고하고 안정적인 제어 시스템을 필요로하는 반면, Batch 공정의 중요성은 수식, 절차 및 공정을 조정하는 데 있어 큰 유연성을 허용하는 제어 시스템을 갖추는 데 있습니다. 두 종류의 시스템 모두 제품의 사용 가능한 품질 내역에서 관리되어야 하며 비일상적인 작업을 수행할 수 있어야 합니다. Yokogawa는 광범위한 제품 포트폴리오, 숙련된 시스템 엔지니어 및 글로벌 영업 및 서비스 네트워크를 통해 모든 공장 공정에 대한 솔루션을 제공합니다.
-
기초화학
Yokogawa는 세계적으로 벌크 화학 시장에 서비스를 제공해 왔으며 이 시장에서 인정받는 선두 주자입니다. Yokogawa는 제품, 솔루션 및 업계 전문 기술을 통해 시장 및 생산 요구 사항을 이해하고 플랜트의 라이프 사이클을 통해 안정적이고 효율적인 솔루션을 제공하기 위해 협력합니다.
-
특수화학 및 정밀화학
Yokogawa는 오랫동안 특수 및 정밀 화학 시장에서 고객을 지원해왔습니다. Batch 솔루션 설계의 복잡한 요구 사항을 이해하는 업계 전문가는 물론 업계 최고 수준의 안정성과 유연성을 제공하는 시장 선도 일괄 처리 솔루션을 사용하면 Yokogawa와의 파트너십에서 안전 및 규정 준수를 유지하면서 고객의 요구 사항을 충족시키는 제품을 생산할 수 있습니다.
-
바이오연료
지구 온난화를 막기 위해 바이오 연료의 생산과 소비가 전 세계적으로 증가하고 있습니다. Yokogawa는 화학, 석유 및 기타 산업에 대한 측정 및 제어 솔루션의 선도적 제공 업체로서 바이오 에탄올 및 기타 재생 가능 연료의 안정적이고 효율적인 생산을 보장하는 데 사용할 수 있는 기술을 개발했습니다.
-
벌크화학
석유 화학 제품, 무기물 또는 중간체를 생산하든 관계없이 화학 회사는 안전하고 호환되는 작업을 유지하면서 적시에 효율적인 방법으로 제품을 제공하는 비용과 마진 압박에 시달리고 있습니다. 또한 화학 회사들은 공급 원료 및 에너지 가격의 변동에 적응하고 가장 수익성 높은 제품 혼합을 시장에 제공해야 합니다.
Yokogawa는 벌크 화학 시장의 자동화 요구 사항을 세계적으로 지원해 왔으며 이 시장에서 인정받는 선두 주자입니다. Yokogawa는 제품, 솔루션 및 업계 전문 기술을 통해 시장 및 생산 요구 사항을 이해하고 플랜트의 수명주기를 통해 안정적이고 비용 효율적인 솔루션을 제공하기 위해 협력합니다.
Details
Chemical Industry Value Chain
Yokogawa는 1975년 세계 최초의 DCS를 출시했습니다. 이 DCS는 전세계 화학 업계의 많은 고객들 사이에서 급속히 보급되었습니다. 따라서 Yokogawa는 이 업계에서 프로세스 제어 솔루션의 선도적인 공급 업체로서 고객의 공장을 안전하고 안정적으로 운영하는 데 기여해 왔습니다.
화학 산업의 프로세스, 제품 및 가치 사슬이 점점 더 복잡해지고 복잡해짐에 따라 고객 요구 사항도 커지고 있습니다. Yokogawa는 풍부한 경험과 노하우를 활용하여 이러한 요구를 충족시키기 위한 산업 솔루션 및 서비스를 지속적으로 제공합니다. 플랜트 운영을 최적화하기 위해 에너지 관리와 같은 다양한 새로운 솔루션을 출시했습니다.
Yokogawa는 포괄적인 공급자로서 최첨단 자동화 솔루션을 제공함으로써 화학 산업의 고객들 기대에 부응할 것입니다.
Production Excellence
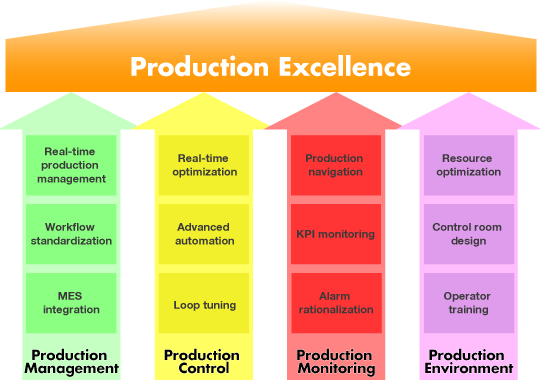
Production Management
-
MES integration
스케줄링 및 기타 기능을 수행하는 다양한 개별 시스템이 MES (Manufacturing Execution System) 도메인에 포함됩니다. 시스템 간 연결성은 민첩한 생산 관리를 위한 핵심 요소입니다. - Workflow standardization
신뢰할 수 있는 생산 관리를 위해 생산 워크 플로우를 정의하고 모니터링 해야합니다. 워크 플로의 표준화는 여러 생산 현장에 있는 회사에서 특히 효과적입니다. - Real-time production management
전반적인 실시간 생산 관리는 생산 계획 점검 - 조치 (PDCA)주기를 단축하는 데 필요합니다.
Production Control
-
Loop tuning
프로세스 식별 (PID) 제어는 프로세스 제어에서 기본적인 역할을 합니다. 안정적인 프로세스 제어를 위해서는 적절한 튜닝이 필요하며 고급 제어를 위한 필수 조건입니다. - Advanced automation
고급 공정 제어 및 지식 기반 내비게이션 시스템은 자동화된 운영에 중요한 기여를 합니다. - Real-time optimization
공장 전체 최적화는 엄격한 모델 계산을 사용하여 실시간 옵티마이저를 통해 이루어질 수 있습니다.
Production Monitoring
- Alarm rationalization
잘 알려진 엔지니어링 장비 및 재료 사용자 협회 (EEMUA) No.191 가이드라인을 기반으로 한 경보 관리 방법을 권장합니다. 경보 근본 원인 분석은 성공적인 경보 합리화에 대한 효과적인 접근법이기도 합니다. - KPI monitoring
다양한 핵심 성과 지표 (KPI)는 각 개인이 모니터링해야 합니다. KPI 모니터링에는 대상과의 비교와 자세한 정보를 위한 드릴 다운이 필요합니다. - Production navigation
생산 작업은 시스템에 의해 정확하게 관리되어야 합니다. 작업 진행 모니터링은 생산 관리에서의 협력을 용이하게 하는 계획 및 제조 간의 중요한 다리입니다.
Production Environment
- Operator training
운전자 교육 시스템을 통해 운전자는 장비 오작동 및 시동 및 기타 일상적인 작업 수행과 같은 다양한 상황을 경험할 수 있습니다. 운영자가 기술을 업그레이드하는 데 도움이 됩니다. - Control room design
제어실 설계는 인체 공학, 안전, 의사소통의 용이성, 기능, 시스템 자동화 및 비즈니스 정책을 포함하여 작업 환경의 모든 측면을 고려해야 합니다. - Resource optimization
중앙 통제실은 효과적인 생산 환경을 위해 바람직합니다. 모든 생산 관련 부서는 좋은 의사소통을 위해 인근에 배치되어야 합니다. 통제실을 중앙 집중화하는 것 외에도, 인적 자원 및 기타 활동의 최적화를 통해 생산 우수성을 달성할 수 있습니다.
자료실
- PRM allows a preventive maintenance approach where maintenance can be scheduled and performed before a field device fails.
- Exaquantum gathers plant data from the CENTUM VP to generate a variety of reports on the polymerization process.
Syngenta aimed to promote sustainable agriculture as a social responsibility through digital transformation. Syngenta selected Yokogawa to start the smart manufacturing transformation journey.
Kuraray Engineering provides IoT big data analysis solution in collaboration with Yokogawa.
Collaborative process data analysis achieved a high level of quality stabilization at a customer site.
Osaka Gas Chemicals selected Yokogawa to solve long-standing problem at carbon fiber manufacturing process.
Osaka Gas Chemicals established unique problem-solving method using Yokogawa's process data analytics solution.
Nippon Sanso Vietnam JSC (NSVN) equipped a digitalized supply-chain management system to optimize efficiency of industrial gases delivery.
The ODMS (Order delivery management system) was rapidly developed using the DevOps agile approach in collaboration with NSVN and Yokogawa.
- Sumitomo Seika achieved the quality stabilization by cross-department project.
- The fusion of process knowledge and data analysis technology was a key to the success.
- Based on a careful review of all operational procedures and operator roles and configured new SOPs in Exapilot.
- As a result, SFC has been able to reduce operator workload, improve product quality, and reduce production losses.
Operator Training Simulator helps improve human reliability in a young plant of PetroVietnam Ca Mau Fertilizer.
PVCFC and Yokogawa implemented OTS for third-party control and safety system as a team.
- Stable operation and proactive maintenance were realized at new coal-chemical plant in China.
- Yokogawa engineers ensured a successful and efficient commissioning and startup.
- Nan Ya had been using Yokogawa Micro-XL DCS since the plant opened in the 1990s.
- Step-by-step approach for migration from Micro-XL to CENTUM VP keeps downtime to a minimum.
Ube Corporation Europe and Yokogawa co-created the Field Assistant mobile solution.
Field Assistant innovates inspection patrol, supervisory management, and O&M efficiency in the plant.
- Legacy System Replaced with Yokogawa CENTUM VP and ProSafe-RS at PTA plant in Indonesia.
- PID parameters imported to CENTUM VP without complex calculations.
- Operational Excellence by Asset Maximization, Utilizing Yokogawa's DCS, SIS, Analyzers, and Field Instruments.
- The CENTUM VP PCS and ProSafe-RS SIS were integrated using the same engineering environment.
- Nearly 60 gas chromatographs and a large number of other types of analyzers in several analyzer houses.
The AFCO project is a showcase of the good coordination between Yokogawa Middle East, Yokogawa Thailand, Yokogawa Singapore, and Yokogawa Electric Corporation. Yokogawa Middle East and Yokogawa headquarters both were involved in the project execution.
- Yokogawa provides CENTUM CS 3000, Exaquantum and PRM solutions for China's largest refinery/petrochemical complex.
- Process data management by Exaquantum is a key issue in the petrochemical complex.
- Using the CENTUM CS 3000 system, many kinds of plant key performance indexes are calculated and analyzed to produce further improvements.
- During plant start-up, PRM helps the customer's engineers perform all the loop checks.
- Main instrument vendor (MIV) concept was applied in this project to reduce the total project engineering cost.
- This consisted DCS, SIS, all instruments, control valves and tank gauging system under working with project management consultant (PMC) and EPC.
- Integration of CENTUM CS 3000 with ProSafe-RS improves plant safety and reliability.
- Yokogawa's PRM package manages more than 500 HART field devices including control valves.
- CENTUM CS 3000 production control system contributes to smooth HDPE production.
- The challenge for this replacement project was in completing the work and starting up the new CS 3000 system as soon as possible, keeping downtime to a minimum.
- CS 3000 efficiently controls and monitors coal gasification process.
- Once an operator selects "Start", the necessary instructions are sent to all plant equipment via the sequence control.
- Rapid Implementation of Integrated CENTUM CS 3000 and ProSafe-RS.
- The highly reliable CENTUM CS 3000 system has also helped TOL maintain high productivity at this plant.
- Migration from Micro-XL and CENTUM CS 1000 to CENTUM CS 3000 Improves Reliability.
- Operations at this plant, which runs more than 330 days per year, are carefully managed by the CENTUM CS 3000 DCS and the CS Batch package.
- A certified emergency shutdown system
- Substantial reduction in maintenance work
- System configuration with reduced footprint
- System scalability
- CS Batch is used to automate a wide range of Reichhold's batch processes and multi-product/multi-path processes.
- Using PRM, process engineers can immediately find out the status of every field device without having to do an onsite inspection.
- Meet the IEC 61508/JIS C 0508 functional safety standards
- Proactively introduce leading edge technologies
- Accommodate the plant licensors' safety, reliability, and maintainability requirements
- Improve the monitoring and operation functions of the emergency shutdown system
Samsung Petrochemical Co. Ltd. (SPCL), a major Korean petrochemical company, produces 700,000 tons per year of purified terephthalic acid (PTA) at its Daesan plant. PTA, a white powder substance that is produced by oxidizing and refining para-xylene, is a precursor to polyethylene terephthalate (PET), a polyester material that has excellent thermal resistance and wear resistance and is widely used as a substitute for natural cotton fibers and in film packaging, beverage bottles, tire cords, paints, adhesives, and other applications.
- Installation of Exaquantum PIMS package improves efficiency of process data management.
- Improve quality and yield through proactive maintenance of plant assets.
- Introduction of CENTUM CS 3000 maximizes productivity and improves product quality at special polymer plant.
- A major improvement as a result of this project is that butadiene monomer recovery efficiency jumped huge.
- CENTUM CS 3000 distributed control system to control the ethanol plant and it's utility boilers
- Batch processes that require careful automated control for maximum efficiency and product quality
- CENTUM VP Batch replaces the legacy system and improves production efficiency in the acrylic plant.
- CENTUM VP Batch capability can handle the recipe management to Batch report handling and unit management.
- CENTUM VP Batch package improves productivity.
- Reduction of operator workload and safe operation.
- PetroChina Dushanzi Petrochemicals Polyethylene Plant system migration.
- The revamp included the challenging creation of function design specifications (FDS) as well as FAT and SAT.
- Highly reliable CENTUM CS 3000 replaces legacy system and automates batch plant operation.
- Working together, Hanwha Chemical and Yokogawa Korea project personnel completed this work on time and on schedule.
- Yokogawa provides STARDOM and FAST/TOOLS for biomass pilot plant.
- FAST/TOOLS is an "all in one" SCADA solution that functionsa a data historian.
- Implementation of multivariable optimizing controllers and robust quality estimators within a record short period
- 3% rise expected in CCR feed amount
- Fieldbus technology introduced to realize predictive and preventive maintenance.
- ISAE to improve the reliability of diagnosis and parameter setting, utilizing data collected by PRM.
- As the main automation contractor (MAC) for this plant construction project, Yokogawa Brazil engineered, installed, and commissioned an integrated control and instrumentation solution
- Yokogawa Brazil completed the commissioning of these systems ahead of schedule and the production of green polymer was started just one week later
- Kaneka Corporation has urgently needed to implement countermeasures that would reduce this facility's energy costs.
- Optimization of control strategy helps BTG plant save energy and operate more efficiently.
- Yokogawa's CENTUM VP and PRM improve efficiency at new nylon plant in Thailand.
- At the plant startup stage, PRM was used together with FieldMate to thoroughly check all loops.
- At the company's Ulsan resin plant, six Exaquantum servers were connected to CENTUM CS 3000 and other vendor's systems.
- KKPC needed to expand its SBC capabilities and improve production efficiency at its plants.
- CENTUM CS 3000 and Exaquantum PIMS improve production efficiency at Chinese synthetic rubber plant.
- Exaquantum provides data on long-term trends needed to make improvements to plant processes.
- Up to 90% of all manual tasks can now be carried out automatically.
- Increasing productivity by means of partially automated start-up and load change procedures.
- 16,000 FOUNDATION Fieldbus devices
- Main Automation Contractor (MAC)
- DCS anywhere concept integration with site SAP system
- Long term maintenance contract
- Sustainable development
- Reinstrumentation project at HDPE plant replaced legacy pneumatic instruments and PLCs with integrated CENTUM CS 3000 PCS and ProSafe-RS SIS.
- HART field devices can be monitored from the central control room with the plant resource manager (PRM) package, enabling a more predictive and proactive maintenance approach that reduces total cost of ownership.
- Single 'look and feel' operator interface for the DCS and NCS
- Fast and controllable integration cycle
- High speed hybrid compressor control solution
- Reduced OPEX for the compressor operation by replacing old and obsolete PLCs with a modern hybrid control platform
- All logistics of raw materials, intermediate products and final products are controlled and managed by MAS.
- MAS enables Operational Excellence with its seamless interface to enterprise resource planning system.
- Implementation of AOA package for improved grade-change operation
- Dramatically reduced operators' workload and transient products, as well as sharable operation know-how
- The work was based on a preceisely formulated roadmap with detailed checklists for every control cabinet, process station, and network component.
- The seamless use of the same HMI for both PCS and SIS, and improved safety and integrity.
- Exapilot automates comlex and non-routine decoking process of NCUs.
- Operator workload has been drastically reduced.
- Exapilot was built up as e-SOP system based on the standard operating procedures and the know-how of experienced operators.
- e-SOP system improved the quality and productivity in the performance chemical plant in China.
As the demand for food is increasing worldwide, fertilizers are playing an essential role in improving agricultural productivity. OCI Nitrogen (hereinafter OCI) is a leading producer of mineral fertilizers and the world's largest producer of melamine, which is used to make adhesives and resins for a wide range of applications, such as furniture panels, laminate flooring, coatings, paints, and plastics.
Tsurumi Soda Corporation,Yokohama,Kanagawa Prefecture, Japan
- IFCo chose Omegaland operator training system to make ready for a flawless and safe plant start-up.
- Omegaland is contributing to operator training prior to completion of the greenfield fertilizer plant.
Yokogawa CENTUM VP and SIS were selected for the Evonik Oxeno's BTX facility expansion project.
CENTUM provides the operational transparency, and more efficient diagnosis of compressors which are the heart of the facility.
Yokogawa's network healthiness check service helped the customer identify what they need to protect against cyber-attacks.
By “visualizing” network traffic in control system, the customer was able to detect unauthorized communication in their system.
- A Japanese petrochemical plant leverages FDT/DTM-compliant intelligent field devices and Yokogawa's PRM asset management system for maintenance efficiency.
- The customer aims to improve maintenance efficiency further by introducing condition-based maintenance (CBM).
- Yokogawa assisted in the project implementation by providing design review, calculation modifications, pre-commissioning, training of operators and engineers, commissioning and post implementation review.
- Shell Global Solutions and Shell Deer Park Management were completely satisfied with the way the project was implemented and with the results achieved.
- TOK decided to start local production of high-quality photoresist for semiconductor manufacturing near its customers in Taiwan.
- The MES with traceability comparable with pharmaceutical manufacturing is one of the factors to win the trust of its customers.
- Yokogawa's operational performance program bench mark service enhanced the automation performance at the chemical plant.
- Operator stress was dramatically reduced by identifying the causes of excessive manual interventions.
- Yokogawa joined forces with Air Liquide to co-innovate the step-by-step revamping plan based on Air Liquide's specific requirements.
- Customer was satisfied that Yokogawa was able to deliver its solutions on time and on budget.
- FDT compliant FieldMate manages a wide variety of digital process instruments of multi-vendors.
- The SNF engineers can manage the complete lifecycle of assets and configure devices by using FieldMate.
- Kuraray EVAL and Yokogawa prepared carefully for the expansion and modernization of the CENTUM system.
- Management of 400+ fieldbus instruments by Yokogawa's PRM plant resource manage also helped the project to proceed smoothly.
Remote monitoring of supply pump conditions in the agitation process reduces operator rounds and contributes to stabilization of the product quality.
The TC series of temperature controllers is perfect for controlling the heating temperature of sealing parts and the temperature of sealing rolls (pre-heating) in a variety of different wrapping machinery.
In the plants of food and beverage manufacturers, there are times when monitoring and recording of production equipment is necessary inside clean rooms. This is an introduction to monitoring and recording in clean rooms using paperless recorders.
DP Level transmitter configuration can be very time consuming. Yokogawa DPharp EJA/EJX Pressure transmitters realize reduction in man hours by smart level setup feature.
Operators must receive diagnostic information before a line block leads to a malfunction. Yokogawa provides predictive diagnostics based on trend analysis of the blocking factor, which improves maintenance efficiency and reduces maintenance costs.
This introduces a system that uses Ethernet communications to acquire measured values, target values, and control output values from a controller installed on site into a PLC at high speed (ten units' worth within one second).
Reactor/Furnace Wall Healthiness Monitoring with a Fiber Optical Temperature Sensor
Recently, air pollution legislations such as the Clean Air Act to reduce the amount of air pollution are increasing worldwide. The Clean Air Act address numerous air quality problems. One of these problems is acid rain caused by sulfur dioxide and nitrogen oxide emissions from fossil-fueled power plants and other industrial and transportation sources.
The GX20 and GX90UT offer an average value computation function making it ideal for controlling temperature and other fluctuating phenomena. The operating status can be controlled in real time, providing operating cost reductions.
In flue gas desulfurization systems that use magnesium hydroxide (Mg(OH)2) slurry, the consumption of the desulfurization agent (Mg(OH)2) is controlled by using online pH analyzers. A great concern in the pH measurement is heavy staining of the pH electrodes by the Mg(OH)2 slurry. To ensure accurate measurement, frequent cleaning of the electrodes with an acid is required, adding to both maintenance workload and cost.
Industry:Chemical, Power
O2 measurement in hydrocarbon vapor is used for safety monitoring in vacuum distillation columns in petroleum refining. With conventional paramagnetic oxygen analyzers, O2 concentrations are obtained through an extractive sampling system, which conditions the sample prior to being analyzed.
The ADMAG AXR is the world's first 2-wire magnetic flow meter which employs the unique "Dual Frequency Excitation Method," achieving 0.5% of rate of best-in-class accuracy and excellent stability for process measurement. In addition, the newly developed AXR key technologies," achieves the same level of noise immunity as 4-wire type under the fluid condition change and delivers enough performance to meet the requirement to apply in the control loop.
Control of sodium chloride (NaCl) concentration at a salt dissolver where solid salt is dissolved in water, is highly important because of the electrolysis efficiency. A conventional way of measuring the concentration of supersaturated NaCl solution had been performed by using non-contact type sensors (e.g., γ-ray density meter) since NaCl, impurities, and precipitates are in the solution.
There are various methods for continuous fabric dyeing as well as dye fixing. When dye is directly applied, steaming (heat treatment) is required. At present the pad-steam method is widely used for continuous dyeing. To ensure stable product quality, the humidity in the steamer is kept at a constant level.
Caustic soda is an important basic material in the chemical industry and is mainly produced by the electrolysis of soda. In the electrolysis process to make concentrated caustic soda, the DM8 Liquid Density Meter ensures high product quality through accurate measurement of liquid density.
Process liquid analyzers such as pH meters, conductivity meters, ORP meters, and density meters play an important role at electrolysis plants in the control of concentrations of various process solutions. This requires both precision and stability under harsh conditions that include highly corrosive substances, high temperatures, and many impurities.
For safe and efficient operation, the quality of feedwater, steam, and condensate in boiler plants must be controlled and maintained in the most favorable conditions.
- Effeciently controls the inlet valve and blow-off valve when the compressor starts and stops.
- During steady operation, controls the inlet valve so that the amount of discharged compressed air becomes constant (flow control)
- Surging: Load decreases, the amount of discharge flow and pressure drop, and a limit is exceeded, possibly destroying the compressor.
In the manufacturing process of Pharmaceutical, Chemical and Food & Beverage industries, the cleaning and sterilization of tanks and piping are done with various cleaning solutions, fresh or hot water and steam after manufacturing products. Clean-In-Place (CIP) is the system designed for automatic cleaning and disinfecting.
- Emergency interlock circuits for petrochemical plants and other facilities must be independent of the main control system.
- The YS80 Rack Instrument interfaces not only with field devices and upstream control systems, but also with emergency interlock circuits guarding against process abnormalities.
What if you could detect signs of abnormalities in bus ducts (bus bars) quickly during maintenance and inspection work and respond to them at just the right time? Yokogawa DTSX monitoring solution constantly monitors connections that tend to deteriorate over time and contributes by pinpointing abnormality locations and reducing workload of maintenance personnel, helping to ensure stability in plant operations.
Many different types of gases are consumed in industries as varied as chemicals, food & beverages, and medical. These gases are normally delivered in liquid form by trucks and dispensed at the customer site. Although the flow volume of cryogenic liquefied gas is used for billing purposes, it is not easy to accurately measure this because the gas is always at saturation temperatures.
With industrial and economic development comes increasingly large and advanced power plants and factories. Nevertheless, we find many cases where the original cables, cable tunnels, and other components of the power infrastructure have languished under continuous operation.
The discharge of improperly treated industrial chemicals and fuel gas can have a major impact on the environment, posing a serious threat to public health. Concurrent with the global growth of manufacturing operations to keep pace with market trends, many countries are taking measures to deal with environmental problems.
In limestone-gypsum flue gas desulfurization systems, the consumption of a desulfurization agent (lime) is controlled using online pH analyzers.
Reverse osmosis (RO) is a separation process that uses pressure to force a solution through a membrane that retains the solute on one side and allows the pure solvent to pass to the other side. More formally, it is the process of forcing a solvent from a region of high solute concentration through a membrane to a region of low solute concentration by applying a pressure in excess of the osmotic pressure.
Fired heaters are used for various processes in oil refining and petrochemical plants.
- In the YS170 and SLPC, single-element control needs to be configured within the user program.
- The YS1700, however, offers the primary direct mode so that the user program can switch on and off single-element control by changing a parameter.
Both bulk and finished inventories are stored in distributed tank farm remote from the site operations. These are difficult to instrument due to the infrastructure cost involved. These are then monitored daily by patrol rounds. While effective, this method does require a large skilled labor force to monitor all of tanks. This can impose an additional risk when the stored medium is of a hazardous nature.
Install a YTMX580 on the side of the rotating furnace that can wirelessly transmit measured values from multiple temperature sensors.
Storage tanks are used in a variety of industries ranging from holding crude oil to holding feedstock for vinyl chloride monomer (VCM).
- Manual temperature reading requires walking about 130 m and climbing up and down elevated sections of the dryer stages.
- Multiple temperature measurement points along the various stages of the dryer require many cables to the control room.
- Very high humidity.
- Temperature is monitored to maintain consistency of the viscous fiber entering the drum.
- Existing system requires manual temperature readings.
- Wired temperature measurement is not available because the tank is rotating.
- Wireless temperature measurement
Gateway x1, transmitter (YTA) x1, repeater x2 (The 2 repeaters are for redundancy) - Extended antenna to circumvent obstacles and improve the radio path for stable measurement (communication was unstable when the height of the antenna was low).
The ammonia (NH3) gas is injected to remove the NOx and thus reduce the NOx concentration in the stack flue gas. With conventional NH3 analyzers that perform measurements indirectly, NH3 concentrations are obtained through a sampling system. Therefore, there are problems with the maintenance and running costs of the sampling system, and time delays in measurement. The TDLS8000 Laser Analyzer is the solution to all these problems.
ISA100 wireless temperature and pressure transmitters with orifice plates allow:
- No cabling installations or maintenance.
- Small amount of hardware and simple equipment implementation means minimizing potential vandalism.
ISA100 Wireless Monitoring
- Gateway x1, Temperature Transmitter (YTA) x3, Pressure Transmitter (EJX) x1, Repeater x1
Gateway is installed at control room and 3m height extended antenna is set.
- Temperature Transmitter (YTA) and Pressure Transmitter (EJX) are installed at each monitoring point.
- Repeater is installed on high position.
Controls temperature in, and acquires data from, various internal components of plastic film manufacturing equipment. An easy to use, high cost-performance data acquisition and monitoring system can be assembled by using Ethernet compatible instruments and GA10.
In maintaining and managing industrial plants, monitoring waste water pH/ORP is both a legal obligation and an unavoidable necessity for protecting the environment. Monitoring without an attentive eye can lead to severe consequences.
Pressure measurement of tubeless tyres to monitor the air loss is one of the key performance tests in the tyre manufacturing units. Relocation of tyres from one testing rack to the other for various tests and frequent movement of the testing setup for conditional tests to various locations calls for cable free implementation for ease of handling.
To defray energy costs, many industrial plants have their own boilers to generate steam in order to produce a portion of their energy needs. In addition to generating power, the steam may also be used directly in plant processes or indirectly via heat exchangers or steam jacketed vessels.
After extraction from sugar cane or sugar beets, juice must be purified to remove the many other organics and minerals that accompany it. The processing to accomplish this is heavily dependent on reliable pH measurement and control as illustrated.
The proliferation of microorganisms and the resultant formation of slime is a problem which commonly occurs in aqueous systems. Problematic slime producing microbes may include bacteria, fungi and/or algae. Slime deposits typically occur in many industrial aqueous systems including cooling water systems, pulp and paper mill systems, petroleum operations, clay and pigment slurries, recreational water systems, air washer systems, decorative fountains, food, beverage, and industrial process pasteurizers, sweetwater systems, gas scrubber systems, latex systems, industrial lubricants, cutting fluids, etc.
Industry:Refining, Food and beverage, Power, Oil and Gas, Pulp and Paper, Chemical
Visual MESA© is a steam system optimization and management computer program that was originally developed at Chevron and now marketed by Nelson & Roseme, Inc. Visual MESA is currently used at refinery and chemical manufacturing sites to optimize the overall site steam system and the parts of the electrical system that economically trade off with the steam system.
This paper will explore significant optimization variables and constraints commonly encountered in refinery steam system optimization, the strategies Visual MESA uses to deal with them.
In the course of more than twenty years as an engineer involved directly in utility related projects in a number of industries, I have seen a great variety of energy efficiency projects and programs covering the entire spectrum of efficacy. The Deer Park, Texas, plant of the Rohm and Haas Company has a unique energy management program that has proven to be highly successful. This program has resulted in a 17 percent reduction in energy use on a per pound of product basis, saving 3.25 trillion btus and $15 million each year! This article discusses this program, its history, successes, and the unique characteristics that have contributed to those successes.
In general, refineries exhibit a very good potential for real time monitoring and optimization using Visual MESA Energy Management System.
Based on our extensive experience, overall benefit in the range of 2% to 5% of the total energy cost can be achieved. Expected project payback is always less than one year.
Outline
- Introduction
- What is Energy Optimization
- How does a Real Time Online Energy Management System based on Visual MESA work
- Calculation Foundation for Key Performance Indicators
- Visual MESA implementation at Saudi Kayan (A SABIC Affiliate) (SK)
- Optimization Actionable Items
- Economic Benefits
- Relevance of Visual MESA RTEMS for SK's Sustainability Initiative
- Conclusions
The REPSOL company had in mind the improvement of the control on one of their chemical reactors. A feasibility study for the implementation of an Advanced Control technique (Predictive Control for temperature control for chemical Reactors - PCR) for a batch reactor for Polyols production has been performed. The proposed technique PCR is based on a dynamic model of the unit which makes the prediction of the process variables behaviour.
This paper will not describe just all the features of the software or fully explain on-line optimization technology. The objective of this work is to present some interesting facts and lessons from the experience of implementing a cost based optimization program at thirty oil refineries and petrochemical complexes, around the world, since 1997. This paper will focus on the key optimization variables and constraints in steam system optimization, how they should be handled and how the human and organizational aspects can be addressed.
Industrial facilities where power and steam is produced (i.e., Cogeneration) exhibit a very good potential for real time monitoring and optimization using Visual MESA Energy Management System.
Based on our extensive experience, overall benefit in the range of 2% to 5% of the total energy cost can be achieved. Expected project payback is always less than one year.
Visual MESA was successfully applied to many industrial facilities worldwide, several of them operating steam and power generation networks of different complexity and capacity but all with energy cost savings.
This paper discusses real industrial examples in which the sitewide utilities system of refinery and petrochemical Sites are optimized with a real time, on line, industrially proven software. Experiences gained during more than 20 years of industrial projects deployed worldwide are commented (Refs. 1 to 10 are related to some recent projects). Main project steps are explained and critical details to be taken into account to assure successful use and proper technology transfer are presented. Specific case studies will be discussed in the paper.
Utilities and energy systems are often the major source of SOx, NOx and CO2 emissions, therefore, emissions control and the management of credits and quotas are tightly interrelated with energy management.
In the case of refineries, chemical and petrochemical plants, energy represents the main cost (second to feedstock) and therefore its reduction has become a bottom line business decision. The energy systems at these sites are inherently complex, with the emissions cost analysis and limits compliance introducing an additional factor to the complexity of the energy costs reduction challenge.
Process plants use different type of fuels, they often operate cogeneration units, their steam networks consist of several pressure levels, there are different types of energy consumers and there are emission limits to be observed. Import or export of electricity in deregulated markets, which could also be traded off with more or less CO2 and other contaminant gaseous emissions, increase the optimization problem complexity.
After a feasibility study, Repsol YPF decided to apply a model-based predictive controller to a batch reactor producing polyols. The predictive controller for reactors (PCR) is a set of control modules that are designed to face most of the reactor configurations. The important increase of production is a consequence of the better handling of the reactor temperature. Here's a description of the unit and control objectives, methodology, project steps, results and the corresponding benefits.
Big and complex industrial facilities like Refineries and Petrochemicals are becoming increasingly aware that power systems need to be optimally managed because any energy reduction that Operations accomplish in the producing Units could eventually be wasted if the overall power system cost is not properly managed. However, process engineers always attempted to develop some kind of tools, many times spreadsheet based, to improve the way utilities systems were operated. The main drawback of the earlier attempts was the lack of data: engineers spent the whole day at phone or visiting the control rooms to gather information from the Distributed Control System (DCS) data historian, process it at the spreadsheet and produce recommendations that, when ready to be applied, were outdated and not any more applicable.
This paper addresses some of the root causes for issues and discusses the best practices that will help to avoid project failures. Main project steps are explained and critical details to be taken into account to assure successful use and proper technology transfer are discussed. It also presents real industrial examples in which the whole utilities system cost of a production Site (i.e., steam, fuels, boiler feed water and electricity) is optimized with a real time, online, industrially well established software.
Utilities and energy systems are often the major source of SOx, NOx and CO2 emissions, therefore, emissions control and the management of credits and quotas are tightly interrelated with energy management. In the case of refineries, chemical and petrochemical plants, energy represents the main cost (second to feedstock) and therefore its reduction has become a bottom line business decision. The energy systems at these sites are inherently complex, with the emissions cost analysis and limits compliance introducing an additional factor to the complexity of the energy costs reduction challenge.
The energy systems, the steps for the implementation of Visual MESA and several features of the model are described in this article, with a focus on the use of the software for the calculation of energy-related KPIs. The EMS implementation project is discussed and the main conclusions relative to the reduction in operating costs are also presented.
Experiences gained during more than 20 years of industrial projects deployed worldwide are commented. Main project steps are explained and critical details to be taken into account to assure successful use and proper technology transfer are presented. Specific case studies will be discussed in the paper. Open loop vs Closed loop implementation is also presented.
Rohm and Haas Company is one of the world's largest manufacturers of specialty materials, including adhesives, sealants, coatings, monomers, electronic materials, inorganic and specialty solutions, and ion exchange resins. Founded in 1909 by two German entrepreneurs, Rohm and Haas has grown to approximately $6 billion in annual revenues.
Alarm management is not just a project that has a start and end date; it's a continuous cycle. Once the alarm system has been reviewed and improvements have been identified, we must check that controls are in place to ensure the alarm system remains functional. The key is to ensure that the system is continuously monitored and any changes are fully documented. There are seven key steps for alarm management. Rationalization is one of those critical steps.
This paper shows how to improve distillation operations by focusing on procedure automation. It will review the importance of using procedures in distillation operations and highlights the collaboration work underway between Fractionation Research Inc. (FRI) and Yokogawa Corporation to improve procedural operations.
The worlds of process automation and production management have been converging for some time. What once used to be islands of automation and production management functionality connected through highly proprietary integration schemes that were costly to maintain have developed into integrated platforms that provide seamless data exchange between the world of automation and the plant floor, the functions of production and operations management, and integration with business level systems.
The world of process automation is governed by procedures. While we like to refer to the process industries as being largely "continuous", this could not be further from the truth. Process manufacturing is constantly in flux.
From engineering to installation, commissioning, operations, and maintenance, FOUNDATION fieldbus offer significant cost reductions of 30 percent or more versus conventional analog systems. Many of these cost reductions come from the advanced functions that fieldbus offers versus analog technology.
The automation suppliers that will be successful in the long term will be those that effectively address application or industry specific problems for end users with a value proposition that cannot be ignored. These problems exist throughout the process industries today, and they won't be solved by simply offering a product, but through a combination of hardware, software, services, application expertise, and knowledge.
In ARC's view, customers need a compelling business value proposition to justify investment in any kind of automation. Vigilance and VigilantPlant were created with this in mind. Yokogawa's vision with VigilantPlant is to create an environment where plant personnel and operators are well informed, alert, and ready to take action.
Yokogawa has come a long way in making its message clear to the world of process automation. Last year, the company embarked on a full-scale global marketing campaign to make customers aware of the company's focus on system reliability, security, dependability, and robustness. Dubbed "Vigilance", the campaign created a unified message for the company and greatly helped expand awareness of the Yokogawa brand and corporate philosophy.
Process automation end users are under more pressure than ever to do more with less. The current economic climate means that many automation capital projects are on hold. With capital budgets tighter than ever, users instead focus on operational budgets (where cost cutting is also a key concern), or on automation investments with a very rapid return on investment.
In today's dynamic industrial marketplace, the only constant is change. Raw material costs, energy costs, market demands, environmental and safety regulations, technology, and even the nature of the labor force itself are constantly changing, and not always in predictable directions.
Migration of a refinery's DCS provided an opportunity to reconfigure and consolidate the control rooms and operational management system.
Differential pressure level measurement has an enemy- temperature. Temperature can have a negative effect on the accuracy of level measurement. This article covers why temperature has this effect and how it can be reduced.
With fired heaters, users hope to get greater efficiency and reduced emissions but often are disappointed. Given the number of fired heaters operating every day and their importance in the process industries, any improvements realized across the board will have huge impacts. More units can reach their potential with some simple changes in work practices and technology upgrades.
July 2011
Process plants are run according to operational procedures. These procedures consist of a set of tasks that are executed in a consistent manner to achieve a specific objective, such as starting up, shutting down or transitioning a unit as part of making a product.
September 2008
Yokogawa is helping a large chemicals site in China manage product transfer by road, ship and pipeline.
March 2006
The new CSPC (CNOOC and Shell Petrochemicals Company Limited) petrochemical complex at Daya Bay in southern China is one of the world's largest process industry projects (see box, Figure 1 and Table). It has a control system to match. Process Worldwide spoke to Johan Veerman, principal instrument and process control engineer at CSPC, about the challenges of managing such a huge job.
In times of abnormal operations, systems are configured to produce lots of data – humans are not configured to handle or interpret them. However, when presented with the right information, in the right context, during an abnormal condition, humans are able to do things machines cannot.
The Wyoming Trona Ore Mine and Refinery upgrade from Yokogawa Centum CS3000 to CENTUM VP-R5 involved two domains, 21 RIO and FIO field control stations, 17 operator stations, 6 engineering stations and 8 different plant servers
ISA S88.01 provides great benefit to users and vendors by solidifying batch operating models and standardizing batch control terminology. On the other hand, as befits an industry-wide standard, ISA S88.01 leaves great flexibility for individual users to apply their own project practices and implementation methodology. Even when utilizing ISA S88.01 models and terminology, many pitfalls remain for those who implement batch controls and recipe management without thinking ahead. Real-world project experience has demonstrated a number of design and implementation "lessons" which might be overlooked to the eventual grief of the batch engineer.
The S88.02 draft standard defines a means for depicting procedural control in master and control recipes. This depiction method is called a Procedural Function Chart (PFC). This standard depiction is based on the requirements of S88.01, technical report ISA-TR88.0.03-1996, user requirements, previous standards and commonly used procedure depiction methods in use today. PFCs can provide a common basis for the exchange of recipes, reduce the learning curve between control systems, and establish a common ground for improved human communication. This paper provides a brief overview of the development of PFCs, the rules for their use and some of the benefits expected by their adoption in the industry.
The case study in this paper illustrates the value of integrating front-end scheduling with a batch control system. Recipe changes, and addition of recipes, occur frequently in the target process. However, since both scheduler and batch packages were designed with the ISA-S88.01 model in mind, these packages could be tightly coupled (well integrated) – and, as a result, it is easy to add or change recipes. The front- end scheduler is not limited to performing scheduling; it also provides an easy-to-grasp real-time production status display which can help enhance efficiency and productivity.
As batch processes are automated, it is common to leave certain less essential field devices without automatic actuators. Thus, the initial control design must accommodate both automated and manual activities. Later, the manual field devices may be automated, either one-at-a-time or in related groups as equipment modules. These field changes, often occurring over a period of years, each require rework of the batch control logic, which can easily exceed the cost of the actuator. In response to this undesirable situation, a technique has been developed which permits the batch design to automatically modify itself, or evolve, to accommodate changes in field automation.
Six Sigma is a quality improvement methodology applied to improving any type of process. It is a methodology endorsed by and heavily integrated into several major chemical companies.
Key Performance Indicators (KPIs) are used in batch processing industries as measurements of production performance. Their use is one element in the current trend of real-time performance management. A single KPI used as the primary measurement of production can cause other dimensions of production performance lose importance. When multiple KPIs are used to measure a batch's production performance it can be difficult to reconcile differences between them for individual batches or for groups of batches. KPIs based upon meeting a target, or specification, measure absolute performance yet do not provide relative information regarding how a batch performed against its peers. The peer comparisons are important for monitoring variability of production performance, which is a critical factor in documenting ROI.
The application of DCS-based "advanced controls" is a common method of achieving enhanced performance from continuous processes such as refinery units. However, it is less widely recognized, but nonetheless true, that modern DCS systems can include other software tools for the significant improvement of batch plant productivity, product quality, and economic performance. Due to the fundamental processing differences between the two types of plants, unique batch "advanced control" features are required which are different from those used for continuous plants.
CONTROL, January 2013
Standard Automation Methodology Improves Operations and Prevents Incidents by Enabling the Sharing of Best Practices Among Operators.
ARC believes that by implementing procedural automation, many process plants can minimize variability to help ensure smooth, efficient, and safe state transitions.
Wiring temperature sensors installed in a chimney back to a control room can be challenging and expensive, so many plants and facilities are instead implementing wireless solutions, such as this Yokogawa YTMX580 8-input temperature transmitter.
Process automation in oil refineries is undergoing major changes, driven by customers frustrated by what they consider to be slow and incremental advances from the main automation original equipment manufacturers (OEMs) in the industry. ExxonMobil has become a de facto industry representative and is driving vendors like Yokogawa and others to reevaluate how large-scale automation projects are implemented.
Supervisory control and data acquisition (SCADA) systems have been part of the process industries for many decades and cyber security measures need to grow as technology advances. SCADA systems are used in oil and gas pipeline and other remote control and monitoring applications, such as electrical transmission and distribution, and water/wastewater.
Many lubricant blending businesses find themselves in a challenging situation: there are opportunities to increase their overall business volume and profits by improving production flexibility, expanding their product slate and optimizing high-margin blends. At the same time, they find themselves constrained by current manufacturing limitations. However, launching a capital project for a significant manufacturing expansion may not be possible, and it may not be necessary.
Spectrometric technology can assess many critical characteristics about products, but it has limits. It can be challenging to determine when the line has been crossed
Machines can support humans when facing a stressful situation. Using a standards-based approach can reduce the likelihood of a problem escalating.
Honeywell and Yokogawa have both been producing Distributed Control System (DCS) platforms for decades, and both are very active in this area. In 1975, Honeywell introduced its TDC2000 platform and Yokogawa brought out CENTUM. These two competing systems emerged from a similar place, oil refining and petrochemical industries, so they started out with similar basic concepts and use cases in mind.
Downloads
Brochures
- Solutions for the Chemical Operations Executive (2.0 MB)
- Temperature Sensing Solutions (596 KB)
- Differential Pressure Level Solutions (8.0 MB)
General Specifications
Certificates
동영상
Showcases the OpreX Intelligent Manufacturing Hub, an AI-enabled platform that enhances manufacturing with seamless data integration, intelligent reporting, optimized workflows, and advanced visualization for smarter decision-making and efficiency.
Chet Mroz, President & CEO Yokogawa North America, discusses the benefits of IoT at the 2015 ARC Industry Forum in Orlando.
How much do you know about pressure transmitters? Are you accurately, quickly and reliably measuring pressure? Ultimately, the drive of any good pressure transmitter is to get an accurate, reliable pressure measurement to the data user quickly. This video gives you the answers to your basic questions about pressure and pressure transmitters.
As a gateway to further expand Yokogawa's messaging as a One-stop Solution Business, Yokogawa has partnered up with INCIT, to introduce the S.I.R.I. framework.
Join this webinar to better understand which manifolds you should use for specific applications and conditions. You will learn:
- A brief history of manifolds
- An overview of the different types of manifolds that are available
- The advantages, disadvantages, and application considerations you should consider when selecting a manifold
News
-
Press Release 2023년2월8일 Yokogawa, 중합 반응 공정 모니터링 디지털화의 선도기업 Fluence Analytics 인수
-
Press Release 2023년3월8일 Yokogawa, AI 기반 Viewport 소프트웨어를 전세계에 제공하기 위해 Radial Software Group과 파트너십 체결
-
Press Release 2023년6월22일 클라우드상에서 실험 데이터와 연구 자원의 통합관리를 실현하는「OpreX Informatics Manager」를 출시
-
Press Release 2024년10월28일 Yokogawa, 드론 관련 서비스를 위해 센신 로보틱스와 판매 파트너십 체결
- 전 세계 공장 및 기타 인프라의 안전하고 효율적인 검사를 위해 -
-
Press Release 2025년2월3일 Yokogawa, 제약 및 식음료 제조를 위한 품질 보증 프로세스에서 DX를 가속화하기 위한 OpreX Quality Management System 출시
- 신속하고 유연한 프로세스 개선을 가능하게 하는 클라우드 기반 시스템 -
기술 및 솔루션, 요꼬가와에 대한 자세한 정보를 찾고 계십니까?
견적 및 기술문의