Hydropower is the most widely-used renewable source of energy and plays a major role in electricity generation in some regions. Yokogawa supplies control and instrumentation products and solutions for hydropower plants around the world.
Challenges
Customer Challenge
A hydroelectric power plant is comprised of numerous pieces of equipment such as hydro turbines, governors, pumps, oil pressure units, and cooling systems. Regular inspections are essential to maintain them. In recent years, the number of inspection items has significantly increased as it is now recommended also to check items that used not to be checked, such as the operating statuses of ancillary facilities. Moreover, manually entering data involves the risk of input errors in the ledger.
Although customers perform preventive maintenance through regular maintenance, unexpected changes in conditions may lead to equipment failures. Countermeasures for unexpected failures are essential to prevent an unplanned power plant shutdown and increase the maintenance efficiency.
On the other hand, although critical equipment is already monitored online, it is difficult to modify the existing monitoring system to incorporate additional items. Therefore, customers want a system which can collect necessary data easily without having to largely modify the existing operation and monitoring system.
Our Solution
Yokogawa offers the following solutions to help realize efficient hydropower plant operation.
Appropriate data collection during operation
- Proven reliability and superior long-term stability:
Proper sensing is the basis of stable operation. The high reliability and long-term stability of Yokogawa’s field instruments such as pressure transmitters and flowmeters are proven by a long track record. - Simplified measuring means:
Yokogawa Sushi Sensor is an IIoT sensor solution for asset maintenance. It realizes long-distance wireless communication without having to design a network. The Sushi Sensor wireless solution enables necessary condition data to be collected efficiently from dispersed equipment for equipment maintenance. - Flexible data input sources, easy engineering of monitoring screen:
Yokogawa’s modular GM10 Data Acquisition System supports universal inputs, allowing for data collection via various industry standard signals from a variety of devices and manufacturers. The GM10 also supports communication data inputs such as via Modbus/TCP and Modbus/RTU, and enables data of various existing equipment to be consolidated and supervised at the monitoring room.
Thanks to the ISA100 wireless connectivity, the GM10 minimizes the wiring cost. For example, the FN510 Field Wireless Multi-Function module supports 4–20 mA analog inputs, enabling measured values to be retrieved from existing equipment in a remote area. As the ISA100 host system supports the Modbus protocol, it is easy to consolidate remote data into the GM10. Meanwhile, the GA10 Data Logging Software makes it easy to build the monitoring screen. - Preventing input errors and grasping long-term trends:
Measured data is automatically collected by and continuously recorded in the GM10, and then displayed using the GA10. This helps prevent read errors during patrols and human input errors when aggregating data. Long-term trends of the measured data can be viewed to help the operators grasp the trends.
Improvement of operational efficiency
- Decreasing the burden of patrols:
Continuous online monitoring eliminates instrument checking and reduces the burden of operator patrols. - Improving communication between the head office and site:
Remote monitoring at the head office is possible via a public or private communication line. Staff can then use the monitored data to give appropriate instructions for inspections and provide proper technical advice to the plant site whenever needed.
Further use of data
- Prediction of equipment failures with artificial intelligence:
The GA10’s AI-based anomaly detection function learns normal conditions and continuously checks for any abnormal behavior. By analyzing multiple parameters in real time and comparing them with normal conditions, it can detect signs of failures before an equipment failure occurs. Customers can work on predictive facility maintenance without specialized knowledge.
Yokogawa solves customers’ operational challenges with a combination of a data acquisition system, wireless technology, and highly dependable precision sensors. Compared to building a large-scale system, the minimal additional cabling/wiring and installation work greatly reduce the lead-time to deployment as well as cost.
Enabling Technologies
Sushi Sensor Wireless Solution
Customer Challenge
A run-of-the-river hydroelectric power station does not have a reservoir like a dam but takes river water directly into the station to generate electricity. If stones or sand are drawn into the water intake, they may cause wear and damage to the hydro turbine. Therefore, such solids must be removed before the intake water reaches the turbine. When a muddy flow is expected due to heavy rain, it is necessary to shut the intake control gate and stop taking in water. To do this, non-contact radar level transmitters, which can measure the water level of rivers, dams, etc., are often used to trigger the action.
However, since there is little correlation between the water level of the river and the water’s sand content, controlling the gate position depending on only the river water level may cause large amounts of sand to enter the plant, which may damage equipment or cause a shutdown. In the worst case, the main equipment may be buried by soil and sand, taking a long time to recover. Therefore, appropriate control of the floodgates is required.
Our Solution
Reduction of equipment damage
The turbidity of river water is measured with Yokogawa’s TB400G Surface Scattering Light Turbidity Meter at the same time as the water level is measured with a water level meter. By using a turbidimeter to measure the amount of sand that is about to flow into the plant due to muddy flow, the water level and turbidity together are used as parameters to control the position of the intake control gate. As a result, a large amount of sediment can be detected early, the floodgates can be closed quickly, and water intake can be stopped, thereby reducing damage to equipment.
Fast deployment at low cost
In general, the intake floodgates are located far from the monitoring room, so wired connection causes a high cost and difficult cabling work. With the GM10 Data Logger and FA-M3 V industrial IIoT computing platform, the work duration and cost are greatly reduced, and the measured data can be collected by the remote monitoring room via an ISA100 field wireless system.
Increased availability
When the amount of sand flowing into the river decreases after the water intake is stopped, the floodgates can be opened to resume water intake, thereby helping to improve the availability of the hydropower plant.
Improved operational efficiency
Automating the opening and closing of the floodgates will reduce the work required for gate operation. In addition, the e-RT3 Plus industrial IIoT computing platform or GA10 data logging software enables visualization of the measured data and remote monitoring through a public or independent network. Furthermore, remotely monitored data can be used to reduce patrol inspection work and help streamline communication between the plant and head office.
Enabling Technologies
FN510 Field Wireless Multi-Function Module
FN110-R1 Field Wireless Gateway
VJET Ethernet/RS-485 Converter
FA-M3 Programmable Logic Controller
Customer Challenge
Reliably performing remote monitoring and control of two or more hydropower plants located far apart
Our Solution
Yokogawa installs remote I/O modules and utilizes a fiber optic redundant ring topology to ensure reliable communications between the integrated production control system and field devices.
Enabling Technologies
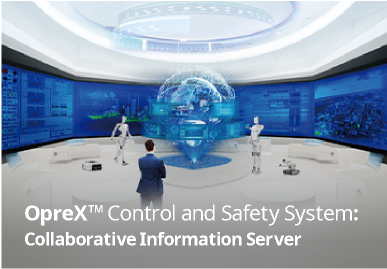
Collaborative Information Server (CI Server)
Yokogawa CI Server allows immediate improvement to production efficiency through digital transformation and reduction of operational maintenance whilst building a digital transformation framework.

STARDOM Procecss Control PLC/RTU
Dual redundant and low-power configurations are available for the STARDOM hybrid PLC/intelligent RTU. STARDOM supports HART, Modbus, FOUNDATION™ fieldbus, and other network protocols.
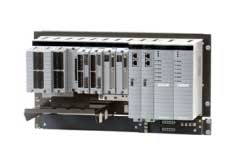
CENTUM VP Distributed Control System
The CENTUM VP integrated control system secures interruption-free “uptime only” plant performance for optimal productivity and profitability in the renewable energy field.
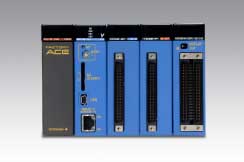
FA-M3 Range-free Multi-controller
A high-performance programmable logic controller (PLC) that combines very high processing speeds with stable control features. It can be utilized to monitor and control the operation of individual wind turbines.
Resources
- Yokogawa supplied control, monitoring, and protection systems for plant modernization.
- Fine engineering and Yokogawa's products made successful operation without any problem or shutdown.
News
-
Press Release Jun 5, 2024 Yokogawa Acquires BaxEnergy, a Provider of Renewable Energy Management Solutions
- Proven results across 120 GW+ of renewable energy operations in over 40 countries -
Looking for more information on our people, technology and solutions?
Contact Us