Creating a Sustainable Future for Specialty and Fine Chemicals Together Through the Realization of Smart Manufacturing
High-value-added, Specialty and Fine Chemicals are essential across industries, from semiconductor materials to automotive components. Manufacturers face challenges with production launches, quality stability, and sustainability compliance that cannot be solved through individual optimization alone.
Yokogawa addresses these challenges by combining century-old measurement expertise with modern AI technologies to promote smart manufacturing. Through our global support network, we collaborate with the entire ecosystem to create sustainable solutions for the Specialty and Fine Chemicals industry.
Work with Yokogawa to achieve sustainable manufacturing that goes beyond conventional approaches.
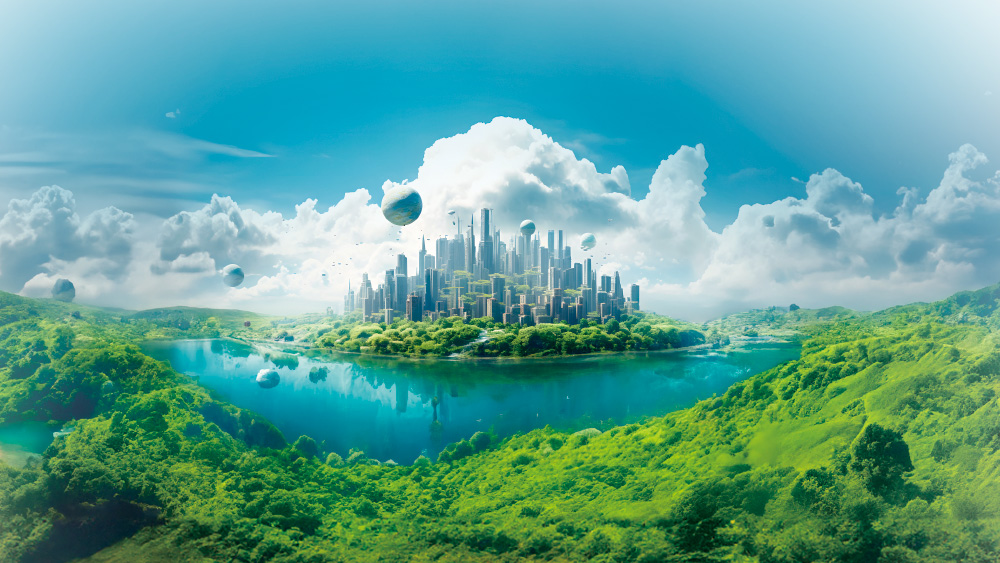
Smart Manufacturing
The Future of Specialty and Fine Chemicals Evolving Through Digital Transformation
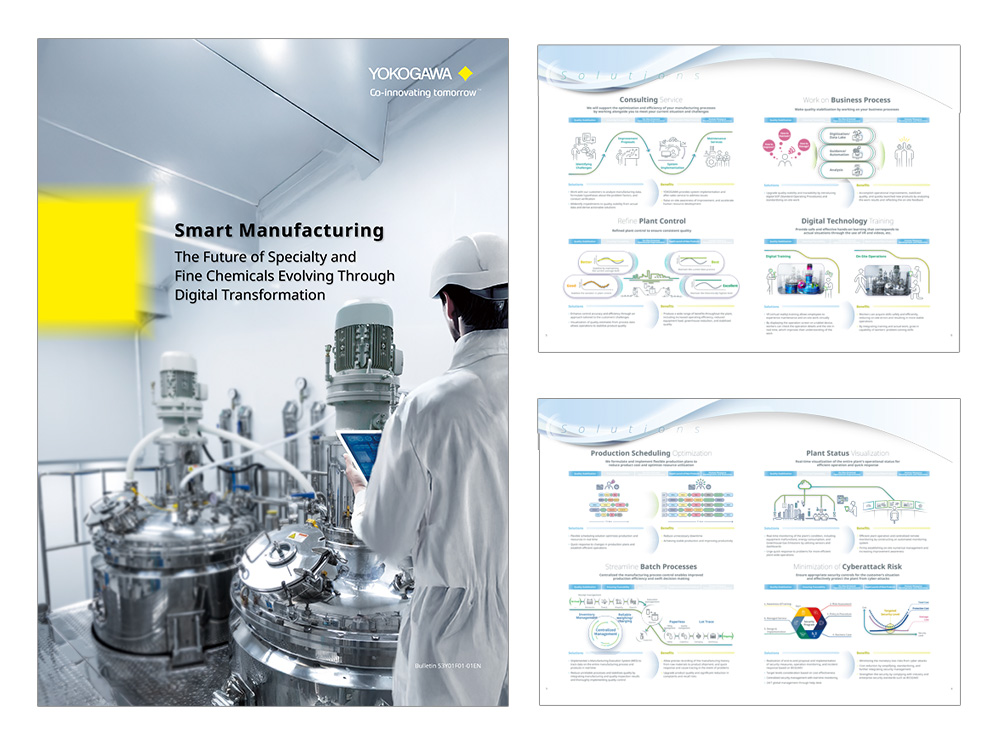
Industry Challenges and Yokogawa’s Approach
Resource Efficiency
- Productivity Enhancement Through the Integrated Use of AI and IoT
- Efficiency Optimization by Utilizing Data
Environmental Responsibility
- Carbon Dioxide Emissions Reduction
- Clean Energy Introduction
Integrated Operations
- Strengthening Supply Chain Collaboration through Digital Transformation
Yokogawa's Solutions
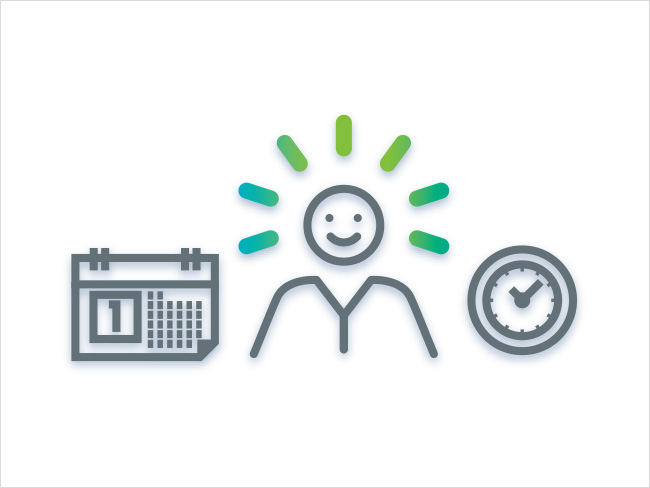
Production Scheduling Optimization
We formulate and implement flexible production plans to reduce product cost and optimize resource utilization
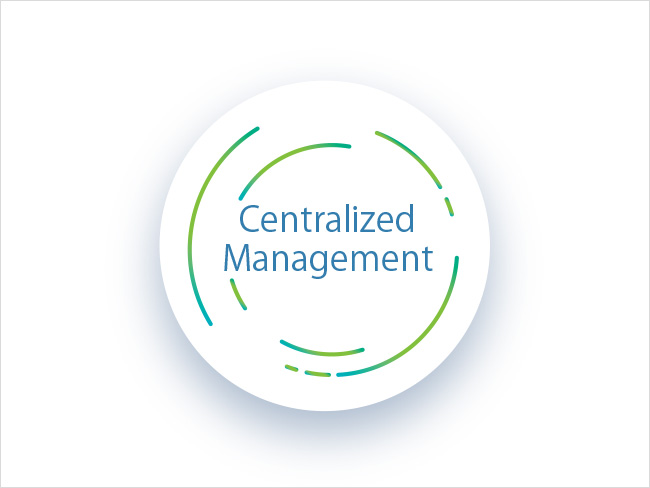
Streamline Batch Processes
Centralized the manufacturing process control enables improved production efficiency and swift decision making
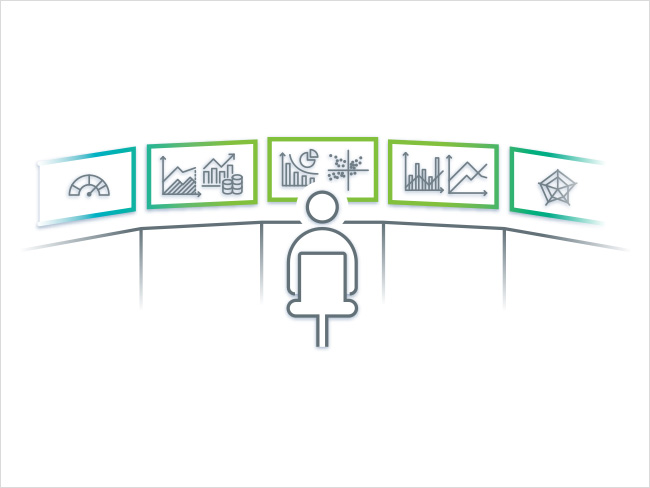
Plant Status Visualization
Real-time visualization of the entire plant's operational status for efficient operation and quick response
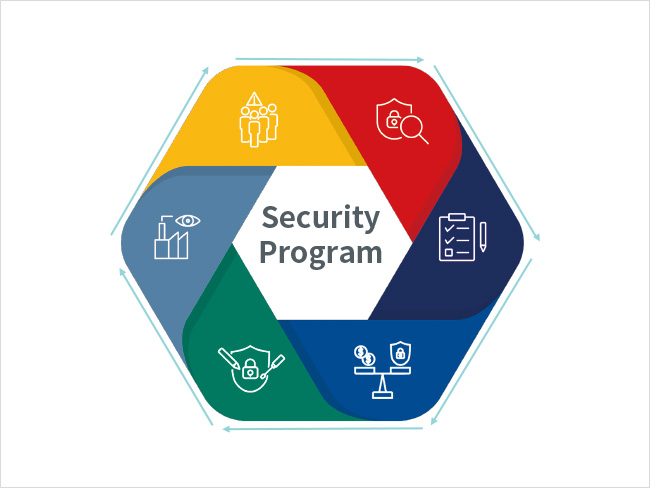
Minimization of Cyberattack Risk
Ensure appropriate security controls for the customer’s situation and effectively protect the plant from cyber-attacks
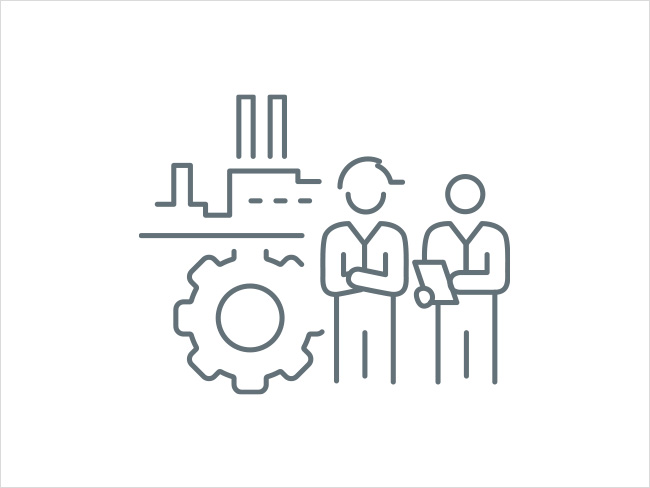
Consulting Service
We will support the optimization and efficiency of your manufacturing processes by working alongside you to meet your current situation and challenges
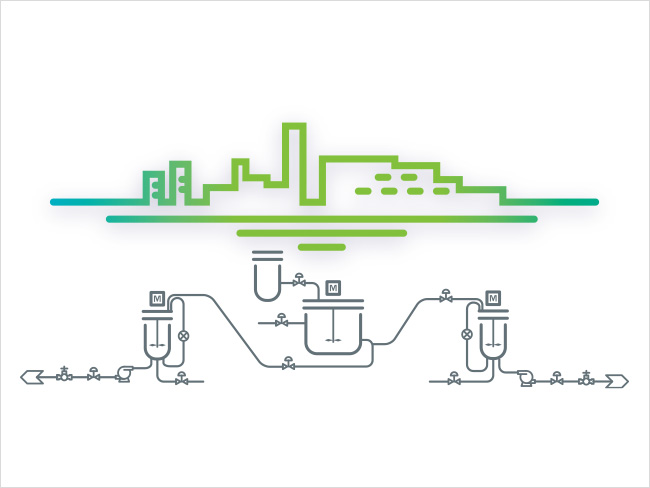
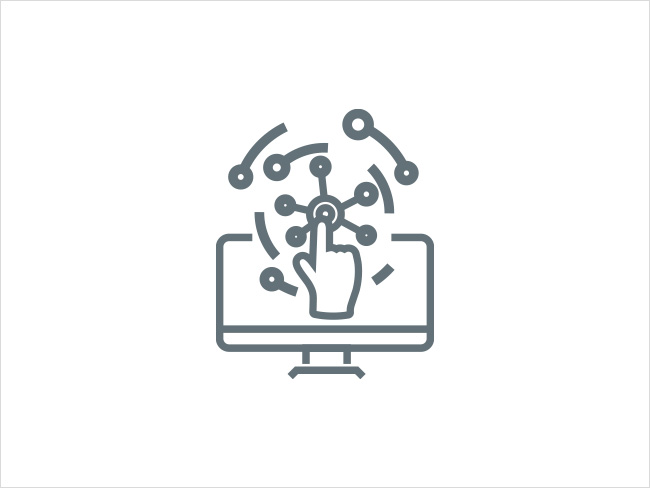
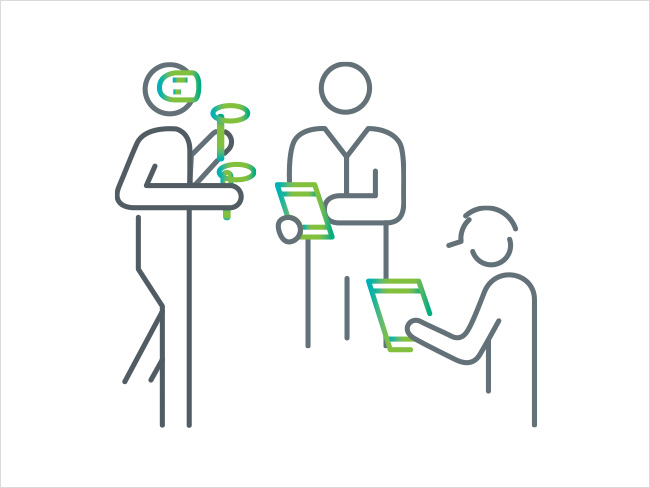
Digital Technology Training
Provide safe and effective hands-on learning that corresponds to actual situations through the use of VR and videos, etc.
Production Scheduling Optimization
We formulate and implement flexible production plans to reduce product cost and optimize resource utilization
Solutions
- Flexible scheduling solution optimizes production and resources in real time
- Quick response to changes in production plans and establish efficient operations
Benefits
- Reduce unnecessary downtime
- Achieving stable production and improving productivity
Streamline Batch Processes
Centralized the manufacturing process control enables improved production efficiency and swift decision making
Solutions
- Implemented a Manufacturing Execution System (MES) to track data on the entire manufacturing process and products in real time
- Reduce unreliable processes and stabilizes quality by integrating manufacturing and quality inspection results and thoroughly implementing quality control
Benefits
- Allow precise recording of the manufacturing history from raw materials to product shipment, and quick response and cause tracing in the event of problems
- Upgrade product quality and significant reduction in complaints and recall risks
Plant Status Visualization
Real-time visualization of the entire plant's operational status for efficient operation and quick response
Solutions
- Real-time monitoring of the plant's condition, including equipment malfunctions, energy consumption, and Greenhouse Gas Emissions by utilizing sensors and dashboards
- Urge quick response to problems for more efficient plant-wide operations
Benefits
- Efficient plant operation and centralized remote monitoring by constructing an automated monitoring system
- Firmly establishing on-site numerical management and increasing improvement awareness
Minimization of Cyberattack Risk
Ensure appropriate security controls for the customer’s situation and effectively protect the plant from cyber-attacks
Solutions
- Realization of end-to-end proposal and implementation of security measures, operation monitoring, and incident response based on IEC62443
- Target levels consideration based on cost-effectiveness
- Centralized security management with real-time monitoring
- 24/7 global management through help desk
Benefits
- Minimizing the monetary loss risks from cyber attacks
- Cost reduction by simplifying, standardizing, and further integrating security management
- Strengthen the security by complying with industry and enterprise security standards such as IEC62443
Consulting Service
We will support the optimization and efficiency of your manufacturing processes by working alongside you to meet your current situation and challenges
Solutions
- Work with our customers to analyze manufacturing data, formulate hypotheses about the problem factors, and conduct verification
- Identify impediments to quality stability from actual data and derive actionable solutions
Benefits
- Yokogawa provides system implementation and after-sales service to address issues
- Raise on-site awareness of improvement, and accelerate human resource development
Refine Plant Control
Refined plant control to ensure consistent quality
Solutions
- Enhance control accuracy and efficiency through an approach tailored to the customers’ challenges
- Visualization of quality estimates from process data allows operations to stabilize product quality
Benefits
- Produce a wide range of benefits throughout the plant, including increased operating efficiency, reduced equipment load, greenhouse reduction, and stabilized quality
Work on Business Process
Make quality stabilization by working on your business processes
Solutions
- Upgrade quality stability and traceability by introducing digital SOP (Standard Operating Procedures) and standardizing on-site work
Benefits
- Accomplish operational improvements, stabilized quality, and quickly launched new products by analyzing the work results and reflecting the on-site feedback
Digital Technology Training
Provide safe and effective hands-on learning that corresponds to actual situations through the use of VR and videos, etc.
Solutions
- VR (virtual reality) training allows employees to experience maintenance and on-site work virtually
- By displaying the operation screen on a tablet device, workers can check the operation details and the site in real time, which improves their understanding of the work
Benefits
- Workers can acquire skills safely and efficiently, reducing on-site errors and resulting in more stable operations
- By integrating training and actual work, grow in capability of workers' problem-solving skills
Resources
Yokogawa provided the Smart Industry Readiness Index (S.I.R.I.) consulting service to Taiwan's Everlight Chemical Industrial Corp.
S.I.R.I. helps identify the digital maturity level of the customer's plant for future transformation.
DIC Corporation co-developed the Data Utilization Platform with Yokogawa. The solution dramatically reduces data preparation work for data analysis.
BASF Schwarzheide GmbH selected Yokogawa's Cavitation Detection System to detect pump cavitation at an early stage.
The Cavitation Detection System catches minute pressure fluctuations generated by low cavitation; problems are recognized before vibration occurs.
Ube Corporation Europe and Yokogawa co-created the Field Assistant mobile solution.
Field Assistant innovates inspection patrol, supervisory management, and O&M efficiency in the plant.
Downloads
Looking for more information on our people, technology and solutions?
Contact Us