Measure and Connect Together for a Green Battery Future
Demand for batteries has surged with EV popularity and renewable energy needs, alongside requests for improved capacity, size, and weight. These changes have made production capacity and quality major challenges, while carbon-neutral management and security concerns emerge. Yokogawa addresses these issues with advanced measurement and control technologies, helping realize a prosperous future with our customers.
Realize the Future of Green Battery Together With Yokogawa.
Smart Manufacturing
Measure and Connect Together for a Green Battery Future
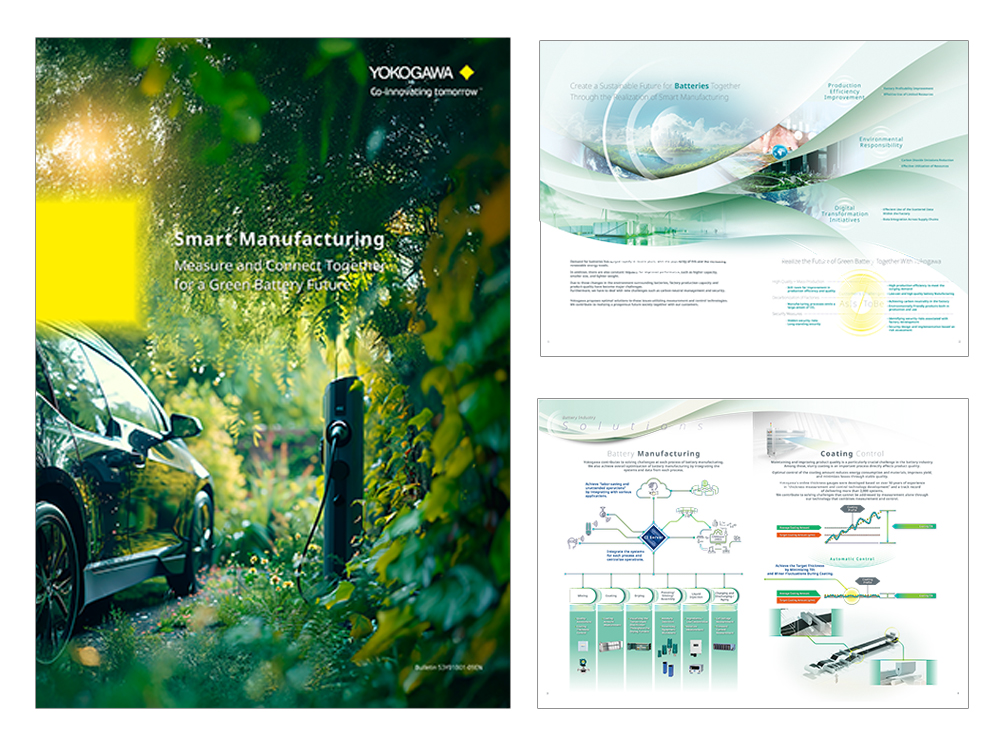
Key Industry Challenges and How Yokogawa Responds
Production Efficiency Improvement
- Factory Profitability Improvement
- Effective Use of Limited Resources
Environmental Responsibility
- Carbon Dioxide Emissions Reduction
- Effective Utilization of Resources
Digital Transformation Initiatives
- Efficient Use of the Scattered Data Within the Factory
- Data Integration Across Supply Chains
Yokogawa's Solutions
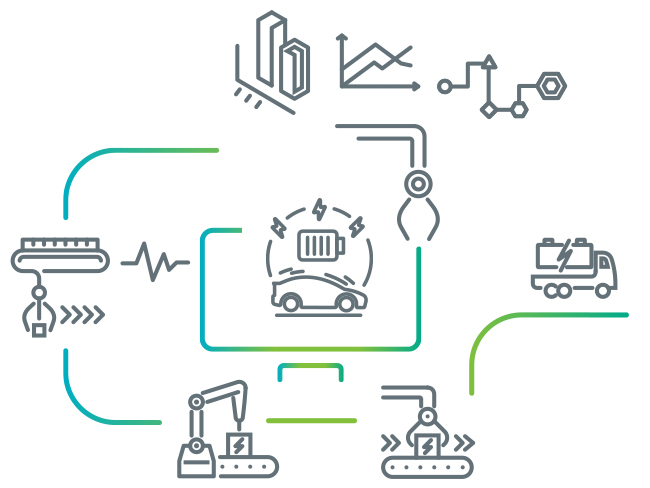
Battery Manufacturing
Yokogawa contributes to solving challenges at each process of battery manufacturing. We also achieve overall optimization of battery manufacturing by integrating the systems and data from each process.
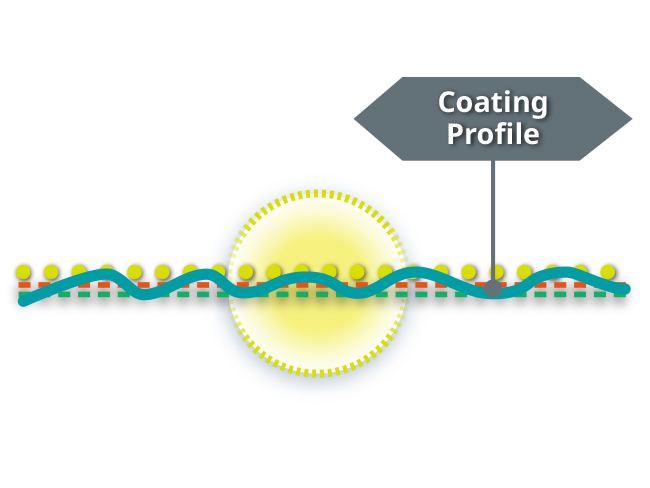
Coating Control
Maintaining and improving product quality is a particularly crucial challenge in the battery industry. Among these, slurry coating is an important process directly affects product quality.
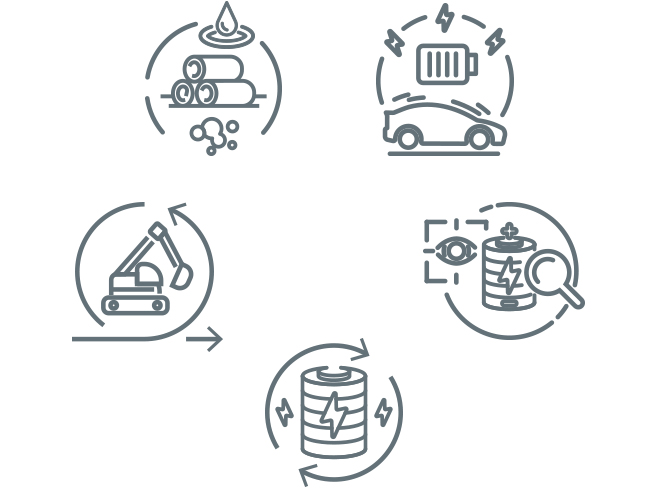
Battery Supply Chain
Providing customer value and solutions to challenges throughout the supply chain
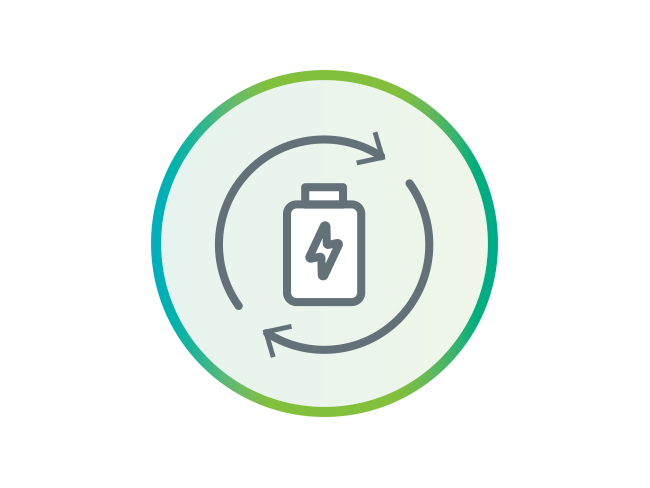
Reusing Batteries
Yokogawa's diagnostic technology enables the safe reuse of used storage batteries
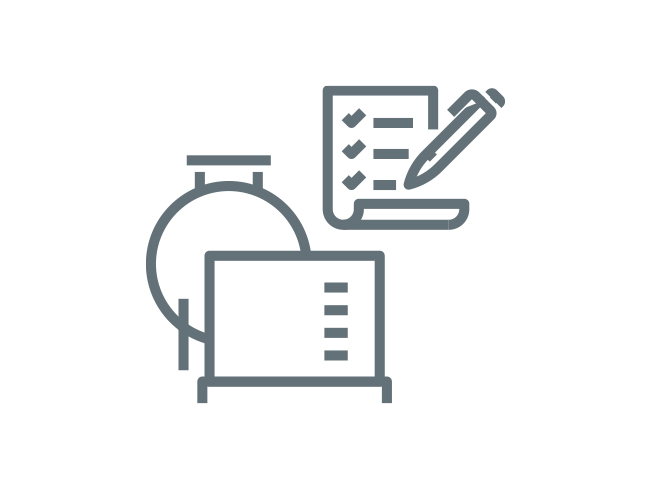

Battery Manufacturing
Yokogawa contributes to solving challenges at each process of battery manufacturing. We also achieve overall optimization of battery manufacturing by integrating the systems and data from each process.
1. Achieve “labor-saving and unattended operations” by integrating with various applications.
2. Integrate the systems for each process and centralize operations.
Systems for Each Process
Mixing
- Quality Assessment
- Coating Thickness Control
Coating
- Coating Amount Measurement
Drying
- Visualizing the Temperature Distribution Throughout the Drying Furnace
Pressing / Slitting / Assembly
- Anomaly Detection
- Preventing Equipment Shutdowns
Liquid Injection
- Ingredients / Low Concentration
- Moisture Measurement
Charging and Discharging / Aging
- Cell Voltage Measurement
- Transient Current Measurement
Coating Control
Slurry coating is a critical process for battery quality. Optimal coating control reduces energy and material use while improving yield through stable quality. Yokogawa's online thickness gauges, backed by 50+ years of expertise and 2,000+ system deployments, combine measurement and control technologies to solve challenges conventional measurement alone cannot address.
Battery Web Gauge ES-5
Advanced thickness control for high-performance electrode coating — boosting quality, reducing waste, and streamlining battery production.
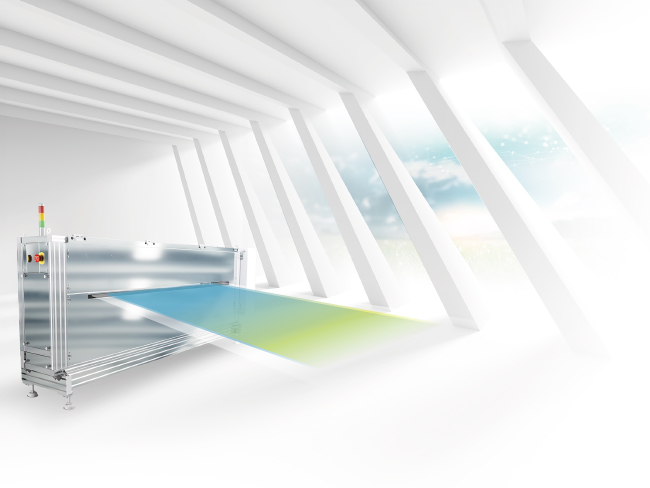
Battery Supply Chain
Providing customer value and solutions to challenges throughout the supply chain. Yokogawa contributes to achieving carbon neutrality with battery reuse solutions that are essential for environmental protection and efficient resource utilization. Providing customer value and solutions to challenges throughout the supply chain.
Reusing Batteries
Yokogawa's diagnostic technology enables the safe reuse of used storage batteries.
Carbon Neutral
Efficient Carbon-Neutral Measures Based on CO2 Emissions Visualization
Among the various carbon neutral measures, optimizing the manufacturing process has many benefits, including not only reducing CO2 emissions but also reducing production costs and improving production efficiency.
Yokogawa provides comprehensive support, from the formulation of decarbonization strategies to consulting on energy reduction after system introduction.Utilizing measurement and control technologies, we visualize factory CO2 emissions based on actual measured values rather than theoretical values. We identify energy losses in the manufacturing process, and develop and implement optimal reduction plans.
Cyber Security
Appropriate Security Measures Based on Risk Assessment
Digital transformation improves factory productivity, but it also increases cybersecurity risks. Yokogawa reveals potential security risks in factories through risk assessment. We design and implement security measures based on IEC62443*. We also propose the optimal security measures by considering the balance between security level and cost.
*IEC62443: International industrial security standards. Jointly developed by the International Electrotechnical Commission (IEC) and the International Society of Automation (ISA)
News
Looking for more information on our people, technology and solutions?
Contact Us