Click here to learn about Modular Procedural Automation (MPA)
Key areas for Operational Excellence Transformation
Operational Excellence Transformation is Yokogawa and KBC’s co-innovated portfolio of solutions and services.We provides comprehensive solutions for business automation in all four areas using consulting and digital technology.
Operational Risk Management
Yokogawa's Operational Risk Management deals with managing safety, health and environmental risks on both individual and process levels in a reliable and risk-free manner. It involves the end-to-end process of designing, visualizing and orchestrating plant production and business systems.
Key Operational Competencies in Operational Risk Management
- Process Safety Management: Maintain License to Operate, preserve Business Reputation, and create value by utilizing and adhering to operating integrity processes to prevent loss of containment or catastrophic loss
- Personal Safety Management: Protect human assets by providing safe practices to improve behaviour and culture
- Environmental Management: Provide processes to protect the environment through operating integrity, and ensure compliance with environmental, regulatory and/or internal requirements
- Community Relations: Define and establish processes and protocols to communicate and implement emergency response plans, and enhance interactions in the community
- HSSE Reporting and Compliance: Assure visibility and achievement of HSSE goals and compliance requirements, by monitoring, learning and improving continuously through processes, initiatives and KPIs
- Plant Protocols and Security: Provide processes and strategies to protect assets and infrastructure from threats, and control access to vulnerable processes and equipment
By combining Yokogawa’s product portfolio and KBC’s consulting services, we provide our customers best practices and domain knowledge that empower them to improve their operations, as well as a digital platform that supports such activities and initiatives. Our Operational Risk Management scope does not only cover partial improvements in the organization, but also optimizations in plant operations to achieve continuously improving safety, reliability and operability.
·Supply Chain Optimization
- Optimize management of supply, whether oil in the ground or feedstocks for a refinery or chemical asset, in light of product market demands. This provides operators with the agility to take full advantage of market conditions.
·Asset Operations and Optimization
- Optimize the potential of physical assets, by pushing throughput and maximizing the production of the highest value products, whilst minimizing variable costs such as energy.
- Deliver small and large capex projects, on time and on budget, to deliver growth and meet environmental requirements.
·Asset Management and Integrity
- Confidently ensure asset reliability and availability, whilst controlling maintenance costs. This assures the asset always meets expectations and is always available to capitalize on short term market opportunities.
Modular Procedural Automation (MPA)
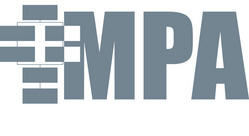
Standardization and automation of procedural operations based on the best practices of experienced operators realizes safer operation and improved profitability.
Process plants of all types are dominated by procedural activities that are critical to achieving safety and efficiency. These procedural activities come from many areas, including manual SOP's, legacy control systems and the tacit knowledge that operators have acquired through years of experience. With a high retirement rate in senior operations personnel, significant and valuable knowledge is being lost, and the new generation of engineers and operators are at a loss.
Inadequate availability of accurate procedures can lead to operation errors. With an emphasis on plants running at optimal efficiency and continuous vigilance on safety, it is critical that the operational knowledge and best practices are captured by the enterprise and are executed consistently and accurately.
A solution offering that address the issues covered in the emerging standard around automating procedures for automating continuous process operations.
Customer Challenge
Aging Workforce
Have you ever concerned about senior operators retiring? Can your workforce maintain procedural operations of your plants safely and efficiently after experienced operators are retired? Many plants rely on experienced process operators to deal with the procedures, and as long as they are around, it may not be a big problem. However, given the demographic problems with aging workers and hard to find replacements, this type of dependence is becoming ever more perilous.
Operational Safety
Besides aging workforce issues, safety should be another continuous challenge for your plants. Operational safety still depends on operators, which are human: they may follow operating procedures under pressure, interpret the same written procedure slightly differently, and perform them a little differently. Significant incidents have occurred due to poor procedural operations as a result of human error, not mechanical failure.
Operational Consistency
Companies have invested in automating operational procedures but they often do not achieve operational or safety improvement goals because of the following reasons:
- They often use programming tools in a legacy control system that is difficult to use.
- Programmed procedures are often written with minimal structure and documentation.
- Programmers of original procedures are often not available to implement updates and modifications.
- It is difficult for others to understand the code and make changes.
- A single operator may have hundreds of loops and thousands of indicators to cope with.
Consequently, the operational staff of the process unit will go back to using manual procedures out of frustration and inflexibly of the automated procedures.
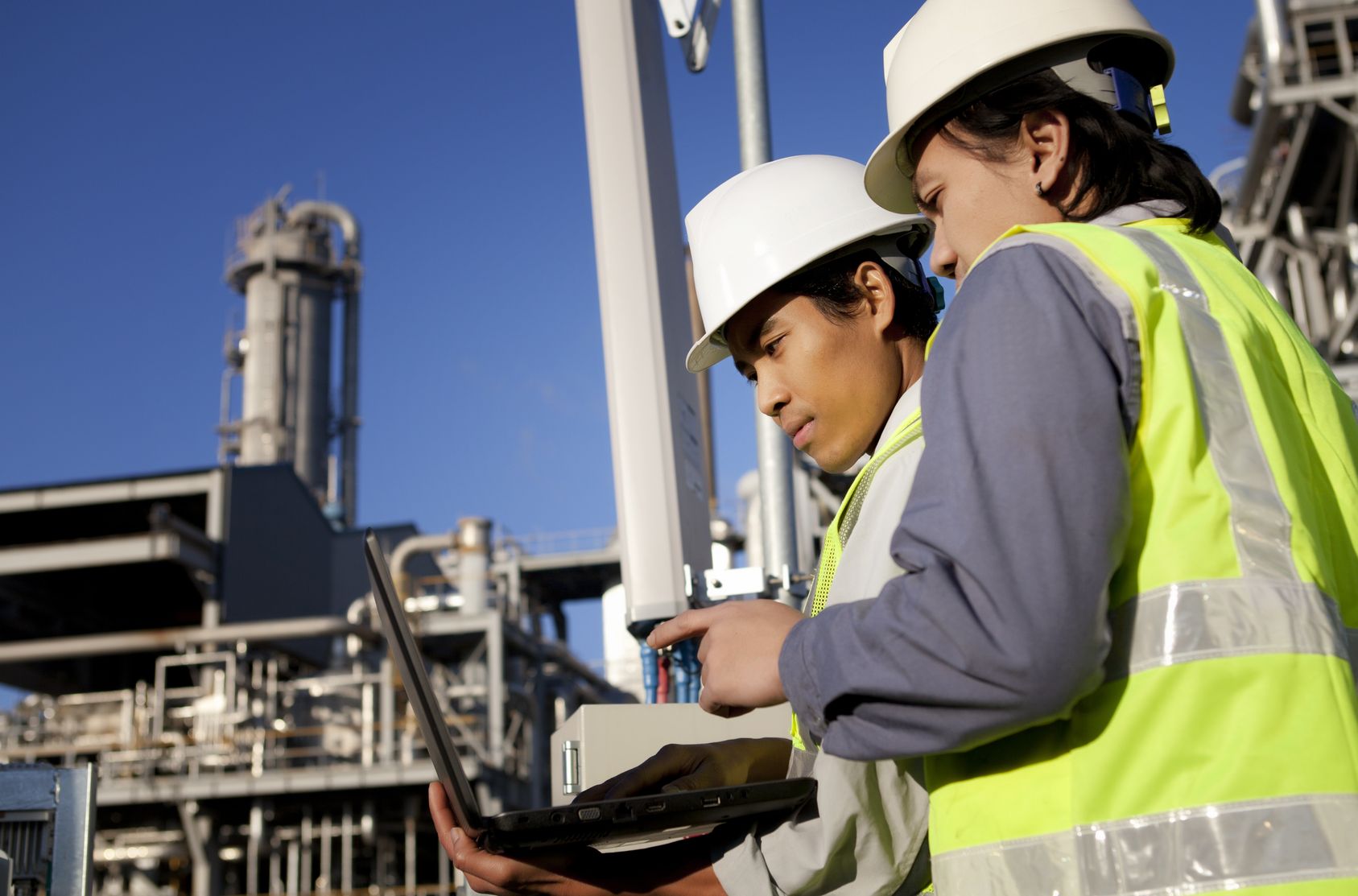
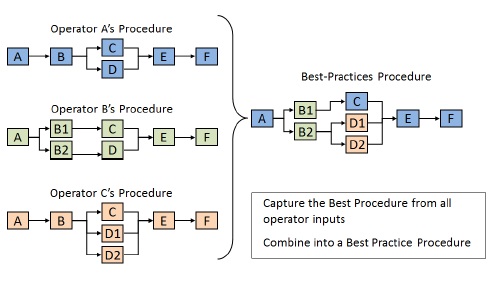
Our Solutions
Our consultancy is based on a long and diverse track record in many industries and processes. In 2000, Yokogawa introduced Exapilot, the world's first automated procedural control solution. Exapilot is an online navigation tool that guides operators step by step through plant operating procedures, and is now installed in over 1,000 plants around the world. The capabilities of MPA include:
Vigilant Procedure Consulting and Tools
Best in class tools, capabilities, & consulting expertise of embedding procedure implementation modules into the control system architecture based on operational requirements.
Knowledge Engineering
MPA consultants and engineers are experts at capturing and documenting currently used procedures whether they reside in a manual, legacy control system, or in the mind of the operator.
Modular Engineering
Standard based design on the emerging ISA-106 standard work/development methodology assures that your procedural investment will remain reliable and pertinent to operating staff.
Advanced Decision Support Integration
Procedures are integrated into high performance HMI and alarm systems to provide operators a high level of situational awareness in all process conditions and states.
Operator Simulation
MPA's value is enhanced by integration and deployment of an operator training system to train plant operators to initiate appropriate responses to abnormal conditions and efficient execution of process transitions.
This combination of consultancy skills and world leading applications provides the optimum solution to integrating procedural control, operator actions and the control system into a unified environment for a best practice plant operation.
Customer Benefits
Modular Procedural Automation combines consulting expertise with world class procedure control capabilities to:
- Capture, optimize,and retain procedural knowledge and control in a process plant
- Implement procedures at appropriate level in a plant control system to meet procedure reliabilty and flexiblity requirements
- Integrate procedures into operator interface and alarm system for improved situational awareness
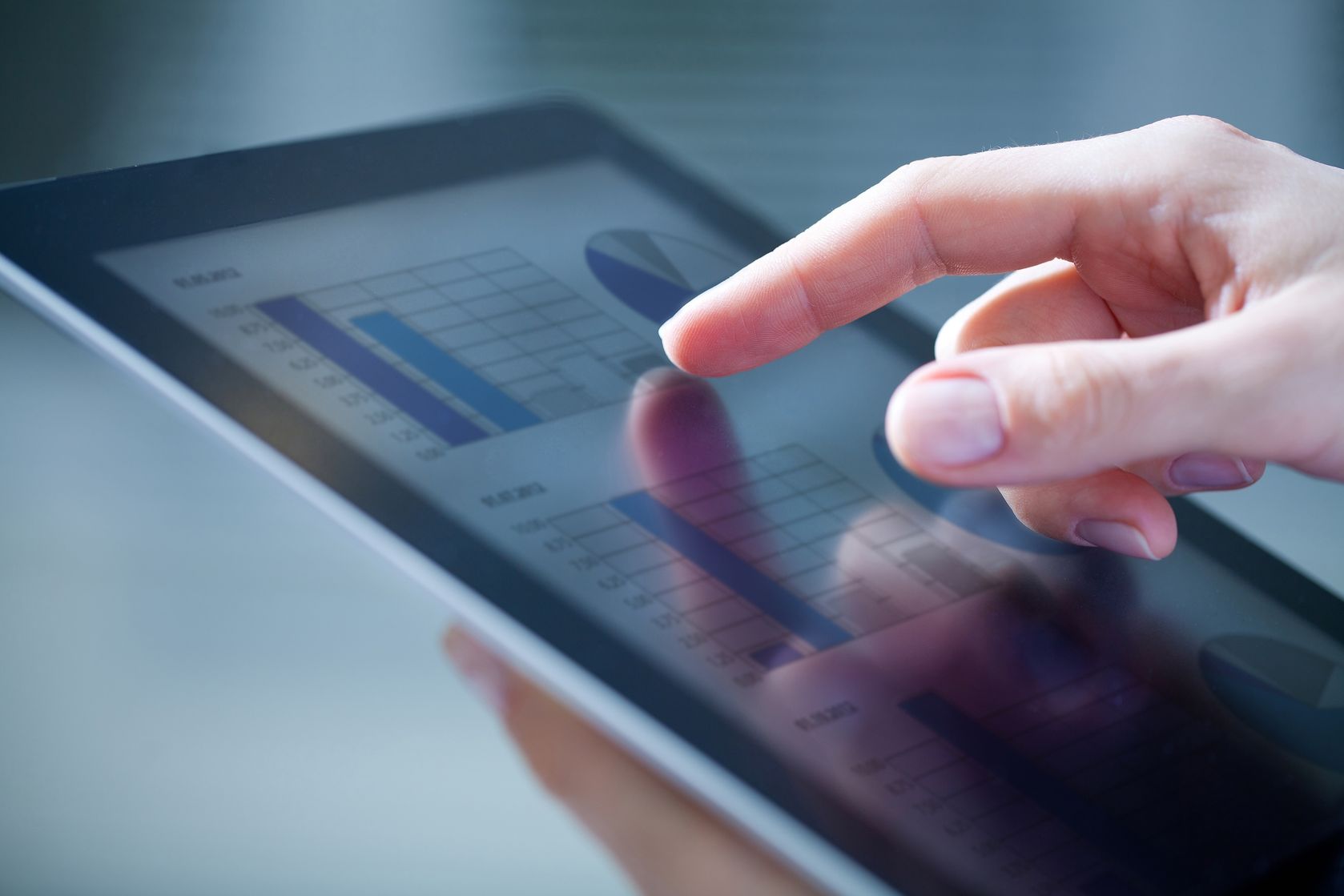
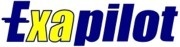
Enabling Technology
Exapilot
Exapilot is an online procedural automation tool that guides operators step by step through plant operating procedures. Since Exapilot was first released, over 1,000 licenses have been sold to companies all over the world, and the majority of users have come from the chemical, petrochemical, and oil & gas industries.
Exapilot Software Features:
- Operating procedures are represented as combinations of icons (during configuration)
- Avoids missed steps (during operations)
- Automating DCS operation and monitoring
- Seamlessly connecting with production control systems
- Documenting standard operation procedures (SOP)
- Making more effective use of your most skilled operators
Ressources
Williams Opal successfully reduced start-up time of stabilizer column and turbo expanders with Exapilot.
Exapilot also standardized operators' start-up processes as Standard Operating Procedures.
Manual operations live on and even thrive in largely automated process plants, and they are often the cause of safety incidents.
By Maurice Wilkins, VP Strategic Technology Marketing Center, Yokogawa Corporation of America
Marcus Tennant, Senior Principal Technology Strategist, Yokogawa Corporation of America
Vidéos
Dr. Maurice Wilkins - executive advisor at Yokogawa speaks with Alastair Greener from the Business Reporter at the Daily Telegraph and shares his thoughts on Process plant operators, automation and how they need to work together in a crisis.
Rechercher plus d'informations sur nos compétences, technologies et solutions
Contactez-nous