Introduction
Industrial Combustion sources such as thermal cracking furnaces and, process heaters play a critical role in the process industry. Because the large amount of fuel such as gas or fuel oil which is consumed in these processes, their combustion efficiency directly affects the performance and operational costs of the production facilities.
Incomplete combustion and the use of too much excess air can lead to higher level of toxic emissions such as CO (carbon monoxide), CO2(carbon dioxide), NOx (nitrogen dioxide), and SO2 (sulfur dioxide).
Challenges
Combustion requires fuel and air (oxygen), and insufficient air causes fuel residue, resulting in incomplete combustion with soot and smoke. On the other hand, excessive air caused problems, such as a larger amount of exhaust gas and heating of excessive air, resulting in lower fuel efficiency. Figure 1 shows the principle of the air-fuel ratio and state of combustion. The air-fuel ratio plotted on the horizontal axis shows the ratio of actual supply air to the theoretical amount of air required for fuel combustion (theoretical air amount).
For combustion furnaces such as heating furnaces and boilers in plants and factories, small-scale controllers such as single loop controllers are employed to optimize the air-fuel control ratio for improving the combustion efficiency. In large combustion furnaces, distributed control systems (DCS) and advanced control (multivariable predictive control, etc.) are used. These mainly control the air-fuel ratio and internal pressure of the furnace to prevent CO, CO2 and NOx (nitrogen oxide) from being emitted and apply a cross limit circuit to prevent incomplete combustion while controlling combustion to maximize efficiency.
Figure 1 : Relationship Between Air-Fuel Ration and Heat Efficiency (Combustion)
Solution
Overview of the TDLS8000 Laser Analyzer
Figure 2 shows the appearance of the TDLS8000 laser analyzer. This analyzer measures the process gas component concentration using tunable diode laser absorption spectroscopy (TDLAS), which measures molecule-specific optical absorption spectra. Figure 3 shows an example of using the TDLS8000 to measure the concentration of flue gas.
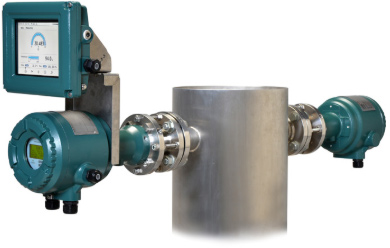
To measure spectra, we employ our originally developed peak area method for accurate measurement even in process environments where the composition, pressure and temperature fluctuate simultaneously. The TDLS8000 suffers no component interference owing to its high spectrum measurement resolution and is directly installed in a process enabling the laser beam to travel through the process windows in a non-contact measurement as shown in Figure 3.
Figure 3 : Installation Example of the TDLS8000
The specific process gas of interest can be reliably measured in near real-time (5 seconds) and at high speed even in high temperature (Max. 1500ºC) or corrosive environments. This advantage enables analysis signals to be utilized directly for process control and management systems, and the TDLS8000 has been rapidly introduced in various industries such as refineries, petrochem, iron and steel and thermal power generation to achieve process improvement and safe operation.
Measurement of O2 and CO Concentrations in Combustion Gas by the TDLS8000
Figure 4 shows an example of using the TDLS8000 analyzer to measure O2 and CO concentrations in a combustion furnace. This example shows that concurrent measurement of O2 and CO concentration while gradually and manually reducing the amount of air supplied to the burner. This experimental data describes the situation; CO generation begun nearly at the O2 concentrations of 2% and sharply increased at the concentration of almost 1.5%, resulting in incomplete combustion, then by increasing the amount of air supply to avoid incomplete combustion, the O2 concentration rapidly increased and the CO concentration decreased again, resulting back to complete combustion. This data also indicated that the CO concentration increased from 100 ppm to 4,000 ppm in just a few minutes.
Figure 4 : O2 and CO Concentration Changes in a Combustion Furnace at Low Oxygen Concentration Operation
Air-Fuel Ratio Control Utilizing CO and O2 Concentrations
According to Lyman F. Gilbert, the CO concentration in the optimum combustion zone (having the highest heat efficiency per unit amount of fuel) is around 200 ppm irrespective of fuel types and devices. However, CO concentration increases rapidly once it has broken through as shown in Figure 4. Thus, either a stable combustion must be kept with sufficient supply of air or a control system must monitor the CO concentration in real-time and keep it constant at a relatively low level.
The amount of air supplied to a burner is controlled by two methods: using a forced draft fan (FD) and damper as shown in Figure 5, or using natural air intake by controlling the opening degree of the damper of an induced draft fan (IDF). The O2 and CO concentrations are measured by the TDLS8000 at the entrance of the flue and then supplied to the control system. The measured CO concentration can be used for combustion control by two methods: controlling O2 when the O2 concentration exceeds a prescribed value and overriding to CO control when the O2 concentration falls below the value, or giving a CO concentration bias (compensation) to the O2 concentration.
Figure 5 : CO and O2 Control System for Combustion Furnaces
Estimation of Economic Effects by Air-Fuel Ratio Improvement
Because the fuel required for generating the same amount of energy can be saved by lowering the set value of O2 concentration in exhaust gas when performing air-fuel ratio control, the direct economic effect by the decrease of O2 concentration in exhaust gas can be estimated. As the economic effects by the improvement, reduction in fuel cost which can be achieved by reducing the excessive O2 while keeping the furnace temperature constant is calculated. Table 1 summarizes a calculation example.1
Table 1 : Example of Economic Effect Calculation by Reducing Excessive Oxygen
*1: Assume to be constant, though it varies depending on the temperature, CO2 concentrations, etc.
*2: (m-l)*A0 is air volume not used for combustion
This example shows a trial calculation for 0.5% reduction of excessive oxygen in the heating furnace of a petroleum normal pressure distillation apparatus(topper) which process oil of 100,000 barrels per day. The result indicates a fuel saving of about 240 kiloliters, worth $113,000 per year assuming a price of $470 per one kiloliter fuel oil.
Furthermore, by reducing the amount of fuel used, CO2 emissions can be reduced. The carbon emission per one kiloliter of fuel is about three tons, so CO2 emissions are reduced by 720 tons per year.
Safety Control by the TDLS8000
A burner management system (BMS) safely controls the burner of the combustion furnace and includes an interlock mechanism and a safety shut-off mechanism to prevent explosion. The BMS must comply with safety standards based on risk assessment such as the international standard (ISO12100) and the EU, USA and Japanese standards (EU standard: EN746, USQ standard: NFPA86, Japanese standard: JIS B9700).
Because the TDLS8000 monitors the CO concentration in near real-time, it increases the reliability of the safety system by inputting a signal of the detected CO concentration to the BMS and is expected for implementing the defined safety requirements. Figure 6 shows a typical system configuration in which the CO measurement capability is added to the BMS burner shut-off system. Yokogawa’s ProSafe-RS integrated safety instrumented system can be employed as the BMS.
Figure 6 : Safety Control in the Burner Control Equipment
In addition to the measurement of CO the TDLS8000 can accurately measure CH4 (Methane) levels providing an extra level of safety during start up where a flame out or a failed burner ignition can cause an explosion.
Conclusion
The TDLS8000 is attracting considerable attention from many refinery and petrochemical plants because it requires little maintenance and can measure the concentrations of O2/CO/ CH4 in the furnace in near real-time.
The technology for combustion efficiency optimization, by measuring O2 can CO concentrations in this application note was established more than twenty years ago.
The TDLS8000 provides a near real time measurement of O2/CO/CH4 in the radiant section of a large scale combustion furnaces and process heaters allowing process owners an unprecedented opportunity to optimize combustion.
Product Recommendations
TDLS 200 (O2/CO/CH4 analyzer)
Note: Various options are available please consult your local Yokogawa Sales Office for more information.
Notes
- Response time: 2-5 seconds
- Process pressure up to 20 bar
- Interference Free
- Process temperature up to 1500ºC
- TruePeak Measurement
- Optical Measurement- No sensor contact with process
References:
- Tsuneo, Hiraoka, “Reduction of Fuel Costs and CO2 Control for Packaged Boilers,” Yokogawa Technical Report, Vol. 44, No. 2, 2000, pp. 85-86 in Japanese
- American Petroleum Institute, “Instrumentation, Control & Protective Systems for Gas Fired Heaters”, API 556 2nd edition, April, 2011.
Industries
-
Chimie Fine et de Spéciclité
Yokogawa est depuis longtemps au service des clients du marché de la chimie fine et de spécialité. Avec une solution de dosage leader sur le marché qui offre la meilleure fiabilité et flexibilité de sa catégorie ainsi que des experts industriels qui comprennent les exigences complexes dans la conception d'une solution de dosage, vous pouvez être assuré que dans votre partenariat avec Yokogawa vous aurez un système qui vous permettra de produire des produits qui répondent aux besoins de vos clients à l'avenir tout en maintenant la sécurité et la conformité réglementaire.
-
En mer
L'exploration et la production offshore exigent un temps de fonctionnement maximal dans des conditions difficiles. Les installations avec ou sans personnel ont besoin de systèmes intégrés de contrôle et de sécurité (ICSS) fiables avec des capacités de surveillance à distance avancées. Yokogawa dispose d'une technologie de pointe et d'une grande expérience dans l'exécution de projets offshore de toutes tailles et de tous niveaux de complexité d'automatisation.
-
Energie
Dans les années 1970, Yokogawa est entré dans le secteur de l'énergie avec le lancement du système de contrôle électrique EBS. Depuis lors, Yokogawa a poursuivi avec constance le développement de ses technologies et de ses capacités afin de fournir les meilleurs services et solutions à ses clients dans le monde entier.
Yokogawa a exploité le réseau mondial de solutions énergétiques pour jouer un rôle plus actif sur le marché mondial dynamique de l'énergie. Cela a permis un travail d'équipe plus étroit au sein de Yokogawa, en rassemblant nos ressources mondiales et notre savoir-faire industriel. Les experts de Yokogawa dans le domaine de l'énergie travaillent ensemble pour apporter à chaque client la solution qui répond le mieux à ses besoins spécifiques.
-
Exploration et Gaz
L'industrie en amont comprend des activités offshore et onshore, notamment l'automatisation des têtes de puits, le fractionnement, la complétion et la séparation pour récupérer et préparer le pétrole brut et le gaz naturel souterrains ou sous-marins.
Lorsque le pétrole est ramené à la surface, il doit être séparé avant d'être transporté. Les étapes de séparation primaire et secondaire distribuent généralement le flux de gaz, le flux d'eau et le flux de pétrole dans une séparation en trois phases. Le transport du gaz nécessite un gazoduc et peut inclure un processus de fractionnement en amont avant le transport. Les liquides peuvent être placés dans des réservoirs ou des pipelines et envoyés pour traitement, ce qui nécessite des mesures de niveau précises.
-
Pétrochimie
Les besoins des entreprises pétrochimiques sont extrêmement variés. Pour se démarquer sur le marché hautement concurrentiel d'aujourd'hui, les producteurs s'efforcent d'améliorer la qualité et la productivité. Yokogawa fournit des solutions sur mesure pour répondre à ces besoins en s'appuyant sur sa longue et vaste expérience dans ce domaine.
-
Pétrole et Gaz (exploration et production)
Yokogawa possède une grande expérience dans tous les domaines du pétrole et du gaz, des installations offshore et onshore aux pipelines, terminaux et opérations en eaux profondes. Nous fournissons des solutions qui améliorent la sécurité, garantissent un fonctionnement précis et fiable et augmentent l'efficacité des installations.
-
Pétrole et Gaz (raffinage et distribution)
Ces dernières années, l'industrie pétrolière et gazière en aval a été confrontée à un nombre croissant de défis. Ceux-ci comprennent les caractéristiques changeantes des matières premières à traiter, le vieillissement des installations et des équipements de traitement, l'augmentation du coût de l'énergie, le manque d'opérateurs d'usine qualifiés capables de faire fonctionner une raffinerie de manière sûre et efficace, et les exigences en constante évolution du marché et du client.
Au fil des ans, Yokogawa s'est associé à de nombreuses sociétés en aval pour fournir des solutions industrielles axées sur la résolution de ces défis et problèmes. Les solutions de Yokogawa ont aidé les propriétaires d'usines à atteindre une rentabilité maximale et une sécurité durable dans leurs usines.
-
Raffinage
Dans un marché en constante évolution, les raffineries sont considérées non seulement comme des unités de traitement du brut, mais aussi comme des centres de profit. Dans le même temps, il existe une conscience aiguë du besoin de sécurité dans ces installations. Une solution de production totale qui englobe la planification, l'ordonnancement, la gestion et le contrôle est nécessaire pour atteindre les objectifs à long terme en matière de rentabilité, d'efficacité et de protection de l'environnement. Avec des années d'expertise dans le domaine de l'automatisation, Yokogawa peut vous apporter des solutions globales abordables pour une meilleure opérabilité et un monde plus propre.
-
Thermique
L'énergie thermique utilisant le charbon, le pétrole ou le gaz comme combustible représente la majorité de la production d'électricité dans le monde.
Les produits et solutions liés
-
In-Situ Gas Analyzer TDLS8000
Yokogawa’s new TDLS™8000 houses all of the industry’s leading features in one robust device. The platform design is for in situ measurements which negate the need for sample extraction and conditioning.
-
Tunable Diode Laser Spectrometers
Tunable Diode Laser Spectrometer (TDLS) is a laser-based gas analyzer with fast-update optical analysis.