A terminal (or large depot) is a storage area where oil and/or chemical products are received through cross-country pipelines and/or marine vessels and are stored in a tank farm. These products are then redistributed by truck, barge, rail tank car (or wagon), and similar means. Yokogawa has accumulated more than two decades of experience in the automation of such terminals and has released a packaged solution, Terminal Logistic Suite VP.
Les défis
Customer Challenge
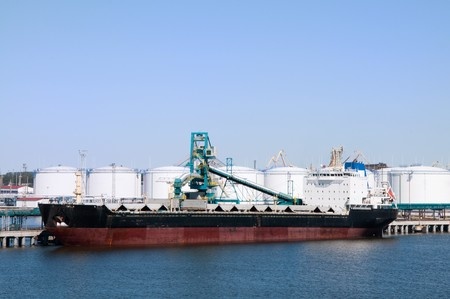
To maximize overall operational efficiency at terminals, a good terminal control system to improve the loading speed is indispensable. However, it is also necessary to integrate the terminal control system with the terminal's Manufacturing Execution System (MES) to guarantee the seamless and smooth flow of information throughout the terminal to achieve overall operational excellence.
Our Solutions
Terminal Logistic Suite VP is Yokogawa's true level 3 (production/MES layer) terminal automation solution. It has direct links to the upper ERP layer and to the lower control system, in addition to a collection of separate modules for materials transfer, path generation, jetty/bay scheduling, production scheduling and other logistic operations. It addresses challenges for faster and more efficient delivery of products. It also provides flexibility for changes, improves safety, reduces administrative work, enhances the visualization of operations and improves traffic management, thus allowing operators to make accurate decisions.
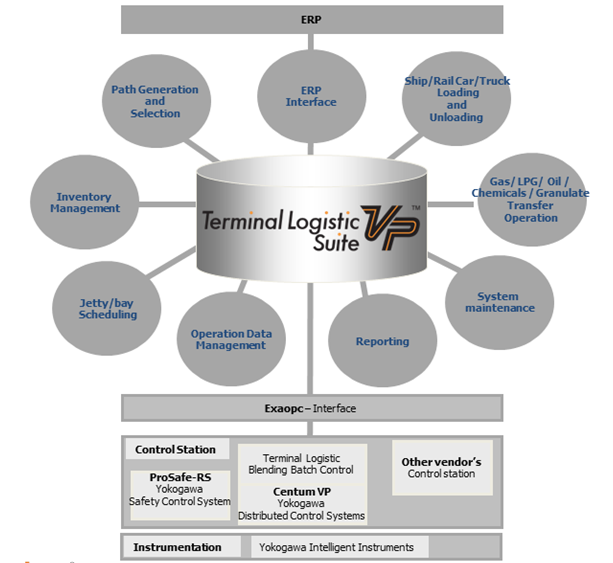
Customer Challenge
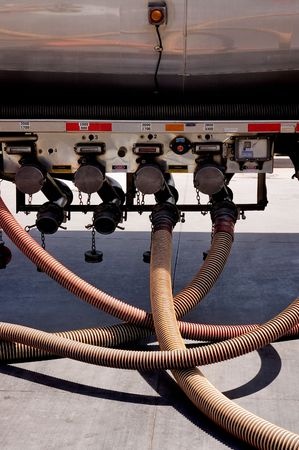
Manual operations at a terminal, such as manual loading/unloading and manual recording of bills of lading and bills of materials, are not only time consuming, but also can lead to injuries and unavoidable costs caused by human errors. Therefore, terminals with limited process automation solutions lack safety and efficiency, and might not be able to deliver products on schedule or that meet the minimum required specifications.
Our Solutions
Yokogawa's terminal automation solution, Terminal Logistic Suite VP, consists of level 3 solutions (production/MES layer) and level 2 solutions (control system layer). It satisfies the requirements of terminal customers in the oil, gas, LNG, LPG, chemicals and petrochemicals industries, without requiring a lot of customization work.
The control system in this solution handles the loading and unloading of products at the terminal. Its functionality comprises all necessary monitoring and control functions for excellent terminal operation. Definitions of control properties can be downloaded from the MES into the controller for execution. The controller then executes the movement control function with ease and efficiency, and monitors the quantities transferred to ensure accurate control, while issuing alarms as necessary in response to inadvertent operations or equipment malfunctions.
Control platforms can be selected to match the diverse needs of users. For example, a relatively small terminal for truck loading would use PLC (FA-M3), while a larger terminal would use either RTU (STARDOM) or DCS (CENTUM VP).
Examples of functions that can be automated by the solution at a terminal:
- Traffic control function
- Batch and sequence of ship, truck and wagon loading
- Additive control
- In-line blend control
- Tank-to-tank transfer control, etc.
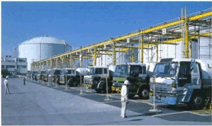
Customer Challenge
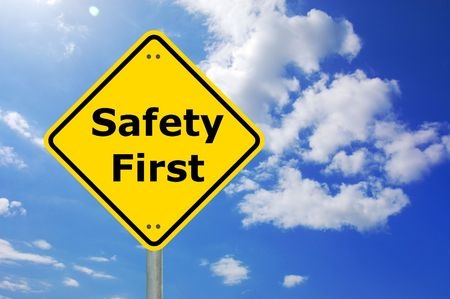
Safety is the first concern and top priority for terminal stakeholders, because it is the most critical element to ensure operational availability and profitability of the terminal in the long run.
Our Solutions
ProSafe-RS is Yokogawa's IEC61508 and ANSI/ISA 84 compliant safety system. Including terminals, it has been used in more than 1,500 projects, ranging from large-scale integrated process automation projects to stand-alone systems for small projects. By monitoring the safety loops consisting of field sensors, safety valves and final control elements, Yokogawa's Prosafe-RS solution can help customers achieve true safety at their terminal.
Yokogawa's Advanced Operating Graphics (AOG) solution is an enhanced redesign of the Process Control Station (PCS) graphics based on human factors engineering and knowledge engineering. AOG provides intuitive situational awareness through ergonomic design, such as color selection and layouts based on operating procedure and environment.
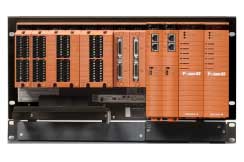
Details
Yokogawa has experience with approximately 120 projects in the terminal automation industry
Yokogawa has gained years of experience in automating terminals/depots and can provide concept-to-commissioning solution, based on proven technologies and its accumulated know-how for all your terminals.
Yokogawa's Terminal Logistic Suite addresses challenges such as shortening the product delivery time, improving loading efficiency, adapting to changes in the manufacturing process, improving safety, increasing administrative efficiency, reducing labor costs, integrating data systems, visualizing operations and managing traffics, etc.
Ressources
- World's largest LNG terminal relies on CENTUM to maximize safety and reliability.
- It is very important for KOGAS to be able to adjust flexibly to shifts in demand in the gas that it supplies to power plants, industrial companies, and residences.
- Yokogawa provides CENTUM CS 3000 and ProSafe-RS for the largest LNG terminal in Europe.
- Yokogawa's OmegaLand plant operator training simulator (OTS) helps to reduce costs, optimize LNG terminal processes.
- DCS, SIS, PRM with FOUNDATION fieldbus and OTS Installed in Thailand First LNG Terminal.
- Alarms are issued before any device fails completely, enabling predictive maintenance that reduces maintenance costs throughout the facility lifecycle.
- Legacy ProSafe-PLC SIS replaced with ProSafe-RS to improve sustainable lifecycle support at LNG terminal.
- The seamless use of the same HMI for both PCS and SIS, and improved safety and integrity.
Universal Terminal (S) Pte Ltd, one of the largest independent petroleum products storage terminals in the Asia Pacific, has been built on Singapore's Jurong Island at a cost of S$750 million.
- World's first offshore regasification terminal relies on Yokogawa ICSS (CENTUM CS 3000, ProSafe-RS).
- LNG carrier scheduling, unloading, tank storage, and vaporizing are all procedure based operations.
- All logistics of raw materials, intermediate products and final products are controlled and managed by MAS.
- MAS enables Operational Excellence with its seamless interface to enterprise resource planning system.
- Scalable, flexible configuration with functions distributed to multiple controllers on a facility basis
- Redundant architecture optimally designed for requirements of entire plant
- General-purpose communications network used for control bus
- Integrated operation environment through web-based human-machine interface (HMI)
- The work was based on a preceisely formulated roadmap with detailed checklists for every control cabinet, process station, and network component.
- The seamless use of the same HMI for both PCS and SIS, and improved safety and integrity.
As the demand for food is increasing worldwide, fertilizers are playing an essential role in improving agricultural productivity. OCI Nitrogen (hereinafter OCI) is a leading producer of mineral fertilizers and the world's largest producer of melamine, which is used to make adhesives and resins for a wide range of applications, such as furniture panels, laminate flooring, coatings, paints, and plastics.
July 2010
Martin te Lintelo, Yokogawa Europe B.V., The Netherlands, discusses high level control system design for LNG receiving terminals. As demand for LNG increases worldwide, players face seemingly conflicting challenges. On one hand, they must expand capacity in different regions, make the business and production as agile and adaptive as possible, and improve operational efficiency.
The LNG sector presents challenges for the automation supplier, particularly in the implementation of automation systems for regasification terminals. Yokogawa Europe's business development manager, upstream oil and gas Martin te Lintelo looks at the handling of the potential automation-related problem areas and opportunities.
Rechercher plus d'informations sur nos compétences, technologies et solutions
Contactez-nous