Alarm rationalization service collects and analyzes alarm as well as event during the operation to identify the rout causes of individual alarms and works out the solution. It also offers EEMUA#191-based Alarm System Design service and assists periodical review for continuous improvement activities.
Click here to learn about Alarm Rationalization
Key areas for Operational Excellence Transformation
Operational Excellence Transformation is Yokogawa and KBC’s co-innovated portfolio of solutions and services.We provides comprehensive solutions for business automation in all four areas using consulting and digital technology.
Operational Risk Management
Yokogawa's Operational Risk Management deals with managing safety, health and environmental risks on both individual and process levels in a reliable and risk-free manner. It involves the end-to-end process of designing, visualizing and orchestrating plant production and business systems.
Key Operational Competencies in Operational Risk Management
- Process Safety Management: Maintain License to Operate, preserve Business Reputation, and create value by utilizing and adhering to operating integrity processes to prevent loss of containment or catastrophic loss
- Personal Safety Management: Protect human assets by providing safe practices to improve behaviour and culture
- Environmental Management: Provide processes to protect the environment through operating integrity, and ensure compliance with environmental, regulatory and/or internal requirements
- Community Relations: Define and establish processes and protocols to communicate and implement emergency response plans, and enhance interactions in the community
- HSSE Reporting and Compliance: Assure visibility and achievement of HSSE goals and compliance requirements, by monitoring, learning and improving continuously through processes, initiatives and KPIs
- Plant Protocols and Security: Provide processes and strategies to protect assets and infrastructure from threats, and control access to vulnerable processes and equipment
By combining Yokogawa’s product portfolio and KBC’s consulting services, we provide our customers best practices and domain knowledge that empower them to improve their operations, as well as a digital platform that supports such activities and initiatives. Our Operational Risk Management scope does not only cover partial improvements in the organization, but also optimizations in plant operations to achieve continuously improving safety, reliability and operability.
·Supply Chain Optimization
- Optimize management of supply, whether oil in the ground or feedstocks for a refinery or chemical asset, in light of product market demands. This provides operators with the agility to take full advantage of market conditions.
·Asset Operations and Optimization
- Optimize the potential of physical assets, by pushing throughput and maximizing the production of the highest value products, whilst minimizing variable costs such as energy.
- Deliver small and large capex projects, on time and on budget, to deliver growth and meet environmental requirements.
·Asset Management and Integrity
- Confidently ensure asset reliability and availability, whilst controlling maintenance costs. This assures the asset always meets expectations and is always available to capitalize on short term market opportunities.
Alarm Rationalization
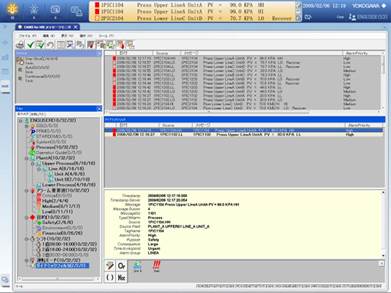
As plant operations become more complex, proper alarm annunciation becomes even more critical to plant operations. The Yokogawa Alarm Rationalization services provide the necessary engineering and/or consulting to sustain the defined alarm system performance throughout the lifecycle of the facility.
Customer Challenge
Avoiding Risks Caused by Inefficient Alarming
In recent years, plants have experienced increased alarm flooding. This leads to the oversight of important alarms while at the same time significantly adding to the scope of operator tasks. It is becoming increasingly difficult to realize safer, more stable, and efficient plant operation with limited human resources. Therefore, the necessity of alarm validation, optimization and management is becoming widely recognized as an important countermeasure. Implementing alarm management is not an easy task, because managing and coordinating the ongoing improvement effort requires the coordination of resources across several departments such as Maintenance, Engineering, Operations and Process Control.
Our Solutions
Our Experience Guides the Alarm Writing Process
Yokogawa's Alarm Rationalization Services are solutions meant to sustain your alarm system performance throughout plant lifecycle. Our services are provided in three phases:
- Fundamental Nuisance Alarm Reduction is the preparatory service to identify the root causes of existing nuisance alarms and take proper countermeasures to reduce them
- IEC-62682/ISA18.2/EEMUA #191-based Alarm System Design is the main service to establish the consistent philosophy for alarm system design based on EEMUA guidelines and ISA18.2/IEC-62682 standards, and incorporates it within CAMS (Consolidated Alarm Management System)
- Operational State-Based Alarm Management is the additional service to manage alarm thresholds and alarm suppression based on the different operational states
Clients are allowed to proceed immediately to the phase that corresponds to the current status of their alarm rationalization activities.
Customer Benefits
Optimized Alarms Lead to High-Level Safety
Typical benefits are:
- Optimized alarm messages sent to the right people, at the right time
- Operators spend less time on alarms and more time on true process concerns
- Decrease in potential risks such as:
- Serious plant damage
- Lost production
- Environmental incidents
- Endangering life
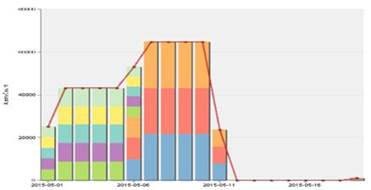
Details
Yokogawa's alarm rationalization service is based on standardized Six Sigma DMAIC methodology. This provides clear and effective steps to achieve a defined target while ensuring consistent and high levels of service quality.
Phase 1 Fundamental nuisance alarm reduction |
Phase 2 EEMUA #191-based alarm system design |
Phase 3 Operational state-based alarm management |
|
---|---|---|---|
1. Define | Establish cross-section task force Set target alarm system performance in steady-state operation |
Establish cross-section task force Set target for alarm system performance during plant upset Hold on-site CAMS for HIS training for team members |
Establish cross-section task force Set target for alarm system performance in steady-state operation Hold on-site AAASuite training for team members |
2. Measure | Acquire A&E logs for multiple operational states | Acquire necessary information regarding current design policy Acquire A&E logs for past plant upset (where possible) |
Acquire A&E logs and historical trends for multiple operational states |
3. Analyze | Sort acquired A&E logs Identify root causes of nuisance alarms through team discussion Decide proper countermeasures to reduce them |
Analyze acquired information to identify improvements Establish new design policy based on EEMUA #191 guideline |
Analyze acquired data to decide target operational states and tags Analyze acquired data to decide proper alarm threshold or AON/AOF condition Consider application of DCS sequence program for automatic switchover |
4. Improve | Take practical countermeasures within two months | Incorporate new design policy in CAMS for HIS within two months | Incorporate new policy in AAASuite package Incorporate DCS sequence logic for automatic switchover Debug implemented application with FCS test function |
5. Control | Evaluate improvement effect Confirm remaining actions Report on results of service |
Evaluate improvement effect Report on new design policy |
Evaluate improvement effect Report on new design policy |
*1: This is a consulting service for CAMS for HIS (Phase 2)/AAASuite (Phase 3) installation.
*2: This service is provided by executing the above five steps of the DMAIC cycle.
Resources
Alarm management is not just a project that has a start and end date; it's a continuous cycle. Once the alarm system has been reviewed and improvements have been identified, we must check that controls are in place to ensure the alarm system remains functional. The key is to ensure that the system is continuously monitored and any changes are fully documented. There are seven key steps for alarm management. Rationalization is one of those critical steps.
As plant operation becomes more intelligent and complex, the alarm system for safe and stable operation is becoming increasingly important. An alarm warns operators of an abnormal situation in a process and urges them to respond to it.
In recent years, safety and profitability have become ever more important in the process industry due to fierce global competition. Greater emphasis is being placed on highly efficient plant operation for reducing the increasing energy bill.
Downloads
Brochures
- Alarm Management Program (877 KB)
Videos
Dr. Maurice Wilkins - executive advisor at Yokogawa speaks with Alastair Greener from the Business Reporter at the Daily Telegraph and shares his thoughts on Process plant operators, automation and how they need to work together in a crisis.
Looking for more information on our people, technology and solutions?
Contact Us