The upstream industry includes offshore and onshore activities including wellhead automation, fractionation, completion, and separation to recover and prepare underground or underwater crude oil and natural gas.
As petroleum is brought to the surface, it must be separated prior to transport. Primary and secondary separation stages commonly distribute gas flow, water flow, and oil flow in three phase separation. Gas movement requires pipeline and can include a fractionation process in the upstream stage prior to movement. Liquids can be placed into a tanks or pipelines and sent for processing, requiring accurate level measurements.
Challenges
Customer Challenge
Oil and gas wells are being drilled to greater depths and are distributed over ever wider areas, necessitating the adoption of increasingly complex technologies. Costs have risen proportionally. To help keep costs under control, it is essential to prevent equipment failures that can lead to unplanned downtime.
Our Solutions
Unplanned downtime disrupts production plans and hurts the bottom line. The high availability of Yokogawa products prevents oil & gas fields from unplanned downtime, saving you money and increasing the safety of your process.
At the heart of the Yokogawa CENTUM series of distributed control system (DCS) systems is a unique “Pair and Spare” controller architecture, consisting of a redundant set of CPU modules, each of which is equipped with dual microprocessors. These two processors continuously compare their output and initiate a bump-less switchover if any mismatch is detected. By such means, CENTUM series systems attain an availability of 99.99999% (seven 9s). Other Yokogawa products such as the STARDOM RTU follow a similar design concept, utilizing the same error check and correct (ECC) memory found in high-end PCs and featuring twice the normal memory capacity to facilitate the long-term storage of gas volume data and other on-site information. This helps reduce downtime, improves system reliability, and increases maintenance efficiency by eliminating the need to travel to remote well locations.
Enabling Technology
CENTUM VP
All of the hardware and software in the CENTUM series field control stations (FCSs) were developed by Yokogawa. With our knowledge of these systems inside and out, we have what it takes to help you maintain 99.99999% availability.
STARDOM
With features such as a 256 MHz 32 bit RISC processor, the FCN-RTU is an evolution of the field proven FCN/FCJ architecture, delivering both high performance and low power consumption. This low-cost model has four serial I/O ports and one Ethernet port, and thus meets the minimum requirements of SCADA applications.
Customer Challenge
Manned and unmanned wellheads are often distributed over a wide area and connected by many types of communications infrastructure. Integrating such complex operations is a key contributor to improved efficiency.
Our Solutions
Unified real-time monitoring
Yokogawa offers an integrated human machine interface (HMI) that enables unified monitoring and alarm handling. It makes the system easier to operate, results in fewer operator errors, improves safety, and reduces training time and expense. A Yokogawa unified gateway station (UGS) supports native network connectivity with Yokogawa intelligent RTUs (STARDOM) and PLCs that use technologies such as Modbus (TCP/RTU), OPC, and EtherNet/IP, allowing both unmanned and manned wellheads to be easily integrated. As the graphics from different networks all have the same CENTUM VP look & feel, operators only need to learn how to use the CENTUM VP HMI, making the overall system much easier to operate and handle alarms. UGS also complies with all types of communications such as single and dual-redundant communication networks for STARDOM, Modbus and EtherNet/IP. Only simple programming is required to build a highly reliable system with an additional UGS.
Enabling Technology
UGS has the following features for unified operation and monitoring environment on HIS.
- Seamless process operation and monitoring (for process data and alarms) and system monitoring among different controllers
- Wide range of operation and monitoring
- Improved engineering efficiency
System configuration example
UGS works as a gateway between CENTUM VP and subsystem controllers. UGS operates and monitors subsystem controllers in the same way as a CENTUM VP field control station.
HIS: human interface station
ENG: engineering station
FCS: field control station
SCS: safety control station
Customer Challenge
Oil and gas companies are trying to stay competitive and become more profitable. One way this is being done is through the application of field digital technologies for enhanced performance.
Our Solutions
Yokogawa's highly accurate and stable field digital technology gives oil and gas companies a competitive edge by reducing unplanned downtime and eliminating the need for travel to field sites. Yokogawa provides a path for migration to this state-of-art technology.
Enabling Technology
Field Digital
Yokogawa started developing field digital technology in earnest with the release of its first FOUNDATION fieldbus™ compliant products in 1998. By being a leading advocate for the definition of FOUNDATION fieldbus™international standards, Yokogawa is playing a central role in the optimization of operations by reducing the need for field wiring, allowing the introduction of intelligent field devices, and improving the management and diagnosis of digital field devices.
Field Wireless
Yokogawa wireless technology takes all the time and effort out of adding measurement points. Transmitters can easily be installed in locations where the installation of wiring is physically difficult and/or prohibitively expensive. The linking of sensors over a wireless network greatly improves the efficiency of monitoring while optimizing both power consumption and communications, and so maximizes measurement availability. The integration of wireless measurements over a wide area network facilitates the flow of field information to the control room, where it can be visualized and managed by Yokogawa’s FAST/TOOLS SCADA system.
Technology Upgrades
The introduction of digital technology in gas and oil field operations can help to optimize production, improve operational safety, and protect the environment. An added benefit is the ease by which these digital technologies can be deployed. As Yokogawa’s STARDOM RTU and hybrid PLC can control both analog sensors and digital sensors at the same time, no longer is there a need to install a gateway or set up a dedicated network or some other type of field network using Modbus, FOUNDATION fieldbus™, HART, DNP3, or DeviceNet. So, a step-by-step upgrade to a digital field network can be achieved.
Details
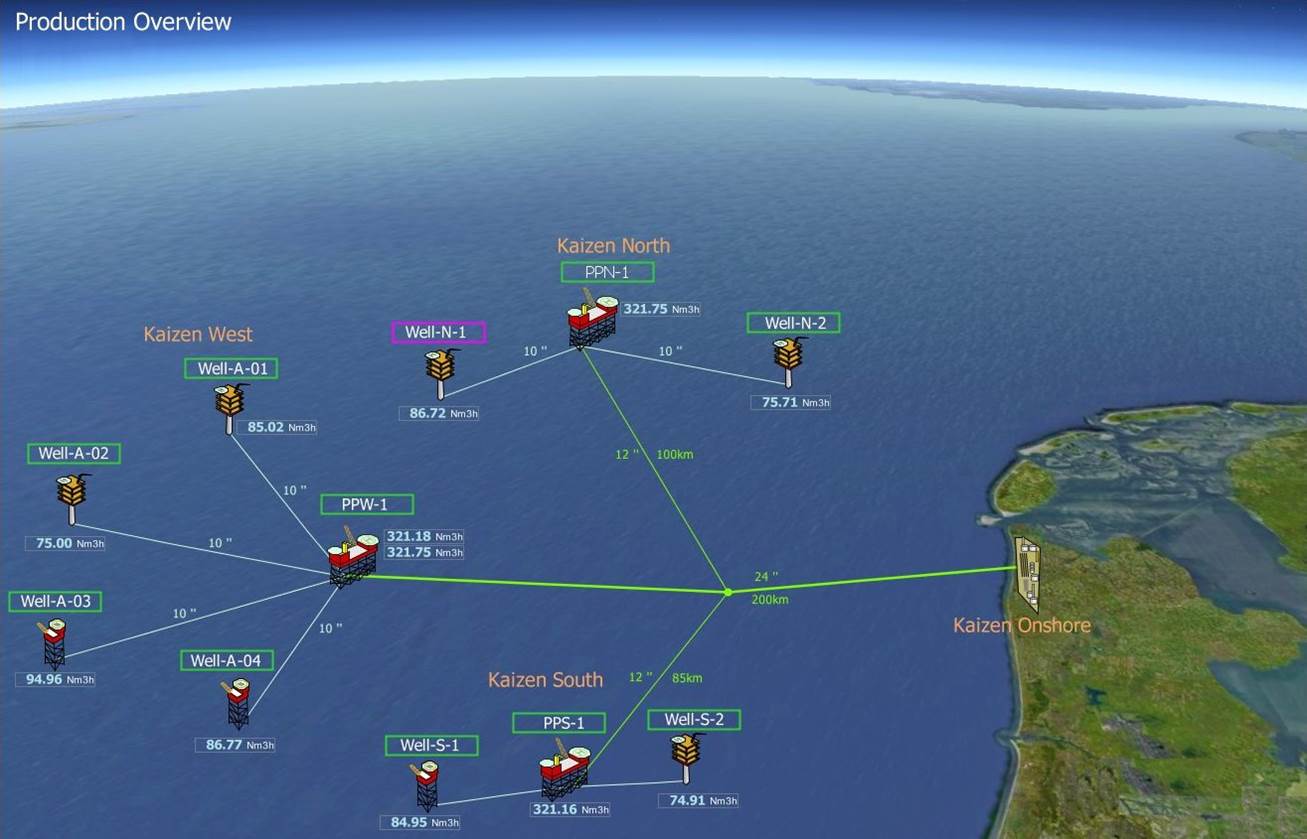
The management of offshore oil & gas fields is moving towards integrated operations using integrated data across disciplines and business domains. By integrated operation, upstream oil & gas company is challenging increased complexity in unconventional and remote environments. Integrated operation is achieved with integrated system. Tightly integrated system changes the way to work and enhance decision making quality and speed.
Enterprise Automation Solution (EAS) is a solution that delivers real-time and historical automation information from the plant or field to the enterprise level for analysis, research, asset monitoring, and control of distributed automation systems. In order to improve safety, production and efficiency, people need to have the best possible information in a way they can work with. EAS delivers the right automation-related information to the right people at the right time to make the right decision.
Offshore exploration and production requires maximum uptime under harsh conditions. Manned and unmanned facilities need reliable integrated control and safety systems (ICSS) with advanced remote monitoring capabilities. Yokogawa has state-of-the-art technology and extensive experience in executing offshore projects of all sizes and levels of complexity.
Natural-gas processing is designed to control the dew point of the natural gas stream and to separate the natural gas liquids for sale and distribution. Oil and condensate removal, water removal, separation of natural gas liquids and sulfur & carbon dioxide removal are processes used to separate impurities in the feed coming from upstream reservoirs. The fractionation process takes the liquid streams from the gas processing plant, which may consist of methane, propane, butane and pentane and treats them in separate fractionation columns which may then go to an impurity treatment plant before being sold as separate components.
Resources
INPEX Corporation (INPEX) is Japan's biggest oil and gas development company and is involved in all aspects of this business, from research to exploration, production, and sales. INPEX is engaged in projects all over the world, in a total of 29 countries, including Japan, where it operates a gas production plant near Oyazawa, a town in Niigata prefecture.
ADNOC Gas selected Yokogawa's Exapilot modular procedural automation for safe and efficient operation.
MPA based on the company's expertise is a step toward digitalization plant operation.
- Exapilot improves operations and reduces energy use at PTT Khanom Gas Separation Plant #4.
- This is a real solution package and a good tool for the plan-do-check-act (PDCA) cycle to achieve operational excellence in the plant.
- Yokogawa receives award for hot cutover of BP Sharjah plant DCS.
- Yokogawa was selected by BP as main automation contractor (MAC) for a project to replace the Sharjah plant's existing legacy DCS with Yokogawa CENTUM VP.
- CACT Offshore platform reduces unplanned downtime by migrating from Legacy PLC System to reliable CENTUM CS 3000.
- It is possible for CACT engineers to modify the system configuration, download software updates, and hot-swap I/O cards while the process control system is online.
- Yokogawa completes automation replacement.
- A one-team approach by BP and Yokogawa was achieved by managing the business relationship in an open, performance-focused, and collaborative manner.
- This is the first offshore platform in Thailand that is designed to make full use of FOUNDATION fieldbus technology.
- Thanks to Yokogawa's highly reliable systems and products, a safe working environment has been achieved.
A Malaysian Gas Processing and Transmission Company a subsidiary of the national oil & gas major, plays a prominent role in the gas business value chain. The company operates as a throughput service company providing the services of processing and transmission of gas to the power generation sectors and various customers.
- World's largest control systems and PIMS for securing production over an extended period
- Fully-automated, alarm-free operation and reduced total cost of ownership
- NAM needs to remotely monitor field devices and organize their maintenance schedule.
- True value in instrument diagnostics and preventative maintenance with powerful software tools like DTM.
- Yokogawa revamp of control systems at NAM Den Helder plant ensures stable gas supply in the Netherlands.
- Site survey, creation of a function design specification (FDS) from the existing TDC system database, documentation verification.
- Nearly 1000 FOUNDATION fieldbus devices were connected to the CENTUM CS 3000.
- PRM provides a single window interface to all FOUNDATION fieldbus and HART devices and this gives maintenance personnel quick access.
- FAST/TOOLS SCADA system has helped NAM reduce its operational costs.
- By installing this onto the existing system, the ever greater data streams became easier to manage.
- Online hot cut over from the legacy Honeywell TDC3000 to the Yokogawa CENTUM CS 3000.
- The work was successfully completed 48 days ahead of schedule and without disruption to operations.
Saudi Aramco's operations span the globe and the energy industry. The world leader in crude oil production, Saudi Aramco also owns and operates an extensive network of refining and distribution facilities, and is responsible for gas processing and transportation installations that fuel Saudi Arabia's industrial sector. An array of international subsidiaries and joint ventures deliver crude oil and refined products to customers worldwide.
- The plant was designed to be unmanned, except for some first-line maintenance personnel who are stationed at the plant.
- Through the use of the latest control system and FOUNDATION™ fieldbus technology supplied by Yokogawa, process control and the diagnostic monitoring of field instrumentation is done from remote locations.
- Extremely cost-effective, reliable fieldbus solution to revive control system
- Minimized total cost of ownership and maximized total value of ownership
Nederlandse Aardolie Maatschappij (NAM) is the Netherlands' largest natural gas producer. In addition to onshore fields, NAM operates manned platforms and four unmanned monotowers in 19 offshore locations. These connect to a pipeline network that comes ashore at Den Helder.
STARDOM field control node (FCN) autonomous controllers allow both Modbus master and slave functions to run simultaneously.
Operators must receive diagnostic information before a line block leads to a malfunction. Yokogawa provides predictive diagnostics based on trend analysis of the blocking factor, which improves maintenance efficiency and reduces maintenance costs.
One of the most common applications for differential pressure transmitters is flow measurement. DPharp differential pressure transmitters have some unique signal conditioning features to eliminate instability at low flow rates.
The major methods of improved oil recovery are water flooding and steam injection. "These technologies make a tremendous contribution to recovering additional oil from old wells as well as improve primary recovery of operating oil fields."
HART communication is a means of transmitting multiple signals by superimposing long-standard 4-20 mA DC analog signals on digital signals. The figure below is an example of connecting field instruments and upstream devices using HART communication compatible VJA1/H signal conditioners.
The paperless recorder DX series instruments allow you to determine temperature and humidity, and manage the results as manufacturing and quality data at a reasonable cost with a simple configuration.
Yokogawa provides controller embedded flow calculation library based on AGA (American Gas Association) reports.
Reverse osmosis (RO) is a separation process that uses pressure to force a solution through a membrane that retains the solute on one side and allows the pure solvent to pass to the other side. More formally, it is the process of forcing a solvent from a region of high solute concentration through a membrane to a region of low solute concentration by applying a pressure in excess of the osmotic pressure.
Floating-point format calculations have enabled physical quantities (in engineering units) to be used in calculations.
- Effeciently controls the inlet valve and blow-off valve when the compressor starts and stops.
- During steady operation, controls the inlet valve so that the amount of discharged compressed air becomes constant (flow control)
- Surging: Load decreases, the amount of discharge flow and pressure drop, and a limit is exceeded, possibly destroying the compressor.
This paper introduces the ADMAG AXR 2-wire magnetic flomwmeter solution for chilled water application in air conditioning unit.
The client wanted to monitor the pressure of the gas well at offshore platform remotely to reduce maintenance cost and increase safety of maintenance personnel.
The client wanted to monitor the injection gas pressure of gas lift remotely in central control room. Antitheft measures are needed to install new equipments and cables.
ISA100 wireless temperature and pressure transmitters.
Industrial Combustion sources such as thermal cracking furnaces and, process heaters play a critical role in the process industry.
Recently, several ARC Advisory Group analysts and management team members had a chance to sit down with the new Yokogawa President and COO, Mr. Takashi Nishijima, and several other top Yokogawa executives to discuss the company's burgeoning presence in the worldwide upstream and midstream oil & gas industry.
Alarm management is not just a project that has a start and end date; it's a continuous cycle. Once the alarm system has been reviewed and improvements have been identified, we must check that controls are in place to ensure the alarm system remains functional. The key is to ensure that the system is continuously monitored and any changes are fully documented. There are seven key steps for alarm management. Rationalization is one of those critical steps.
Tuning PID controllers can seem a mystery. Parameters that provide effective control over a process one day fail to do so the next. The stability and responsiveness of a process seem to be at complete odds with each other. And controller equations include subtle differences that can baffle even the most experienced practitioners.
The worlds of process automation and production management have been converging for some time. What once used to be islands of automation and production management functionality connected through highly proprietary integration schemes that were costly to maintain have developed into integrated platforms that provide seamless data exchange between the world of automation and the plant floor, the functions of production and operations management, and integration with business level systems.
The world of process automation is governed by procedures. While we like to refer to the process industries as being largely "continuous", this could not be further from the truth. Process manufacturing is constantly in flux.
From engineering to installation, commissioning, operations, and maintenance, FOUNDATION fieldbus offer significant cost reductions of 30 percent or more versus conventional analog systems. Many of these cost reductions come from the advanced functions that fieldbus offers versus analog technology.
The automation suppliers that will be successful in the long term will be those that effectively address application or industry specific problems for end users with a value proposition that cannot be ignored. These problems exist throughout the process industries today, and they won't be solved by simply offering a product, but through a combination of hardware, software, services, application expertise, and knowledge.
In ARC's view, customers need a compelling business value proposition to justify investment in any kind of automation. Vigilance and VigilantPlant were created with this in mind. Yokogawa's vision with VigilantPlant is to create an environment where plant personnel and operators are well informed, alert, and ready to take action.
Yokogawa has come a long way in making its message clear to the world of process automation. Last year, the company embarked on a full-scale global marketing campaign to make customers aware of the company's focus on system reliability, security, dependability, and robustness. Dubbed "Vigilance", the campaign created a unified message for the company and greatly helped expand awareness of the Yokogawa brand and corporate philosophy.
Process automation end users are under more pressure than ever to do more with less. The current economic climate means that many automation capital projects are on hold. With capital budgets tighter than ever, users instead focus on operational budgets (where cost cutting is also a key concern), or on automation investments with a very rapid return on investment.
In today's dynamic industrial marketplace, the only constant is change. Raw material costs, energy costs, market demands, environmental and safety regulations, technology, and even the nature of the labor force itself are constantly changing, and not always in predictable directions.
Migration of a refinery's DCS provided an opportunity to reconfigure and consolidate the control rooms and operational management system.
July 2011
Process plants are run according to operational procedures. These procedures consist of a set of tasks that are executed in a consistent manner to achieve a specific objective, such as starting up, shutting down or transitioning a unit as part of making a product.
September 2009
Partnering with Saudi Aramco, Yokogawa is providing local project execution including testing and implementing a continuing policy of Saudisation.
August 2006
Many published papers discuss the benefits of subsea HIPPS and many studies show the potential cost-benefit analysis of this technology in deepwater applications. An internet search for subsea HIPPS is informative; however, little appears that discusses the systems already delivered and operating successfully.
Chevron turns to deeper relationships with fewer suppliers to increase project execution consistency
Using wireless for gas detection is a very flexible method, and allowed ExxonMobil to establish it as a redundant system
Trinity integrated Systems' iDefine Suite reduces errors and streamlines design of safety instrumented systems
Offshore, February 2013
Offshore and deep-water production has been a significant factor in the sustained growth of the oil and gas industries over the past decade and this trend is expected to continue beyond 2013.
Videos
How much do you know about pressure transmitters? Are you accurately, quickly and reliably measuring pressure? Ultimately, the drive of any good pressure transmitter is to get an accurate, reliable pressure measurement to the data user quickly. This video gives you the answers to your basic questions about pressure and pressure transmitters.
News
-
News Brief Aug 2, 2019 Yokogawa Wins Bulk Order to Supply 1,350 Pressure Transmitters to Argentine National Oil Company
-
News Brief Jul 1, 2014 LNG World News, ‘Yokogawa developing Yamal LNG systems’
LNG World News, ‘Yokogawa developing Yamal LNG systems’
Looking for more information on our people, technology and solutions?
Contact Us