The risks of industrial digital transformation in process manufacturing
Today, fluctuating market and technology conditions are driving accelerated change in the process industries. Process manufacturers need a long-term, reformative solution to meet the considerable challenges such change poses, or they risk falling behind. Digital transformation (DX) offers such a solution by supporting long-term growth, innovation, and sustainability for companies that successfully implement it.
Digital Transformation (DX) is the novel use of digital technology to accelerate business strategy. It is about the application of digital technologies to empower people, optimize processes and to automate systems of the organization to achieve a step-change in business performance.
While DX has enormous potential value, it also raises questions and poses new challenges. Therefore, manufacturers should understand the risks they are likely to encounter along the way. This article examines these risks. It groups them into three risk categories—people risks, process risks, and technology risks—then summarily investigates common challenges with each.
The people-related risks of digital transformation
With DX, technology is evaluated as an integrated set in combination with the business strategy, people, processes, data, and assets. DX is often viewed as a program with prioritized digital initiatives oriented around business processes, rather than point solutions or Proof of Concept - POCs.
DX therefore covers every part of a process-manufacturing organization. And its people—workers, stakeholders, and customers—ultimately tend to experience its disruptive effects the most.
For the worker, DX means upskilling and retraining to learn new technical skills and operational processes. For stakeholders, it means increasing investment and finding new ways to optimize the value chain. For customers, it means navigating new channels to buy products.
So, all digital initiatives should consider how DX affects people in an organization and address risks associated with them. A DX project simply cannot succeed without input and support from key workers and players on all organizational levels--especially company leaders.
Risk #1: Leadership
According to Jay Ferro, an innovative technology leader, the dynamics of a digital transformation are similar to any big change management program or change management philosophy. They require bold, determined, and consistent leadership in order to achieve success.
Without effective leadership as a driving force, a DX project can fall prey to discordance and disorganization and quickly fall apart, wasting considerable time, money, and resources.
Since DX impacts every part of an organization, its CEO tends to be the ideal DX champion. Increasingly, though, CIOs or chief digital officers (CDOs) are taking up the task since DX relies so heavily on information technology (IT). The responsibility to champion and organize the resources and investments that DX requires falls on these individuals. And putting together a dedicated internal DX task force of key players and stakeholders throughout a process organization is part of that task. This task force is ultimately responsible for steering DX initiatives toward strategic goals.
DX requires an organization to challenge its culture, common practices, and mindset, which are products of leadership working styles and communication. Therefore, it falls upon leaders at all organizational levels to recognize the need for change. They must advocate the importance and benefits of change throughout their organization and come up with a strategy to address change resistance.
Risk #2: Risistance to Change
While not necessarily everyone is affected, a percentage of an organization’s workforce will be facing a change in their day-to-day working pattern due to digital transformation. Shop-floor workers and other employees comfortable following historical practices on the job will only produce incremental results in improving old work processes. DX requires new work processes throughout an organization. This can result in strong resistance to change, especially among departments hesitant to share knowledge or collaborate and workers worried about how transformation will affect their jobs.
Resistance to and anxiety over change are understandable. Digitalization and DX are complex, ambiguous, strategic, and operational—a consuming challenge from start to finish. Once leaders recognize the need for change in organizational culture and mindset, they must look for key players able to meet the challenge and become change agents or champions.
These change champions must inspire and connect people across departments to introduce cross-functional collaboration to an organization. Together, with C-level support, organizations should incorporate programs to assess and develop technology, leadership, and change management skills. Often a small but carefully curated team with cross-functional experience and a dedicated focus on DX is created first.
However, as key players remove boundaries between departments and people, they may face another challenge: unlocking tribal knowledge, without which unification efforts might ultimately fail to produce a productive work environment for DX to succeed.
Risk #3: Tribal knowledge
It is impossible for any one individual to know the way around all industrial work processes and technologies an industrial, process-driven organization puts to use or intends to put to use through DX. Knowledge gaps between departments—particularly between the IT and operational technology (OT) spaces—can set up barriers in departmental, people, and process unification.
“Tribal knowledge” refers to the knowledge locked away in siloed departments and shared only between learned groups of people, often subject-matter experts. And it is frequently a challenge for process manufacturers, which need departments, people, and processes to work together using open, accessible, and comprehensible information.
One solution is to invest in digital/IT training and fluency for workers in the OT space and OT training and fluency for those in the IT space prior to the digitalization phase of DX. Preemptive cross-functional training and education can prevent considerable confusion between people as they start to work with applications outside of their regular areas of expertise.
Risk #4: Talent loss
On the whole, process industries are at risk of losing a skilled aging workforce to retirement, which spells trouble for current and future process manufacturers. A report from the Society for Human Resource Management, “Preparing for an Aging Workforce: Manufacturing Industry Toolkit,” states that a chief industry challenge is attracting new talent to alleviate "a slew" of anticipated retirements.
The report paraphrases a 2016 survey from Accenture for the American Chemistry Council. The survey found that 40% of executive respondents from North American chemical manufacturers could lose between 20 and 40% of their workforce to retirement within the next three to five years. Of these respondents, 86% stated that the retirement issue would affect profitability in the chemical industry. And finally, nearly half of respondents said that retirement is having an impact on cost control, unplanned operational challenges, efficiency, and performance.
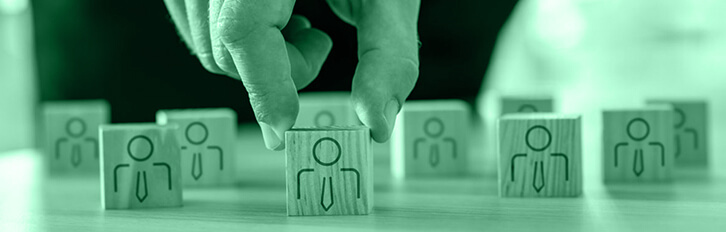
One of the last things an organization wants is to successfully execute a DX project, then lose the workforce that executed it. An exodus of workers would leave a void the organization has to fill. This would require additional time, money, and people resources the organization might not have coming out of transformation, as well as possible production downtime.
Compounding the issue, if a retirement-ready workforce leaves prior to DX, then the company executing it has to find new talent willing or able to work on old, outdated systems and equipment. To pre-empt the risks posed by losing skilled aging workers, process organizations should consider building investments in talent acquisition and retention into its DX strategy and budget.
Another way to prevent expertise loss when workers retire or move to a different organization is to digitalize domain knowledge. The new tech-savvy workforce entering the job market has higher expectations of human-machine interfaces and the user experience. Operator training simulation and digitalizing standard operating procedures can immortalize knowledge within an organization and make it easily accessible to whoever from the organization needs it.
The process-related risks of digital transformation
In general, processes help people define and standardize work, preventing people from reinventing the wheel. The 2018 Harvey Nash/KPMG CIO Survey, which was the largest survey of IT leadership in the world, comprising 3,958 respondents across eighty-four countries, stated that “improving business processes” was the respondents’ top priority. Even though adopting new cutting-edge technology is a key component to DX, restructuring and improving outdated processes is of greater importance.
A long-term goal of DX is increasing efficiency in the way people think and work to help them make faster, smarter decisions with better tools. DX paves the way for assessing and implementing process automation, industrial autonomy, and utilizing data better to think more critically and clearly about the way a process organization runs and meets the needs of its customers.
DX and Digitalization requires operational processes to evolve, which introduces new risks to the equation. Consider that people must upskill and conduct training, technology has to change and upgrade to support this process evolution. If people, processes, and technology do not integrate seamlessly, a DX project may fail. By extension, the value chain may fail to optimize and achieve critical long-term goals.
Risk #1: Process by Accident
One of the risks an industrial organization might foster over time is an environment that creates “process by accident.” For example, one of the effects of the traditional automation pyramid (Purdue Model) has been the normalization for process plants to execute operational processes independently and uncoordinated from one another.
Hence, processes that should work together—including supply chain planning, production planning, production scheduling, process control, production accounting, and other related business processes—often work in silos, or even against each other, functioning with limited scope to reach different objectives.
The following are some technology risks that can result:
1. Tools often fail to integrate with each other.
Often, different suppliers develop tools individually. Consequently, needed data, models, and solvers are different between tools, increasing the time it takes to build, maintain, and use them.
2. Linear models lose validity.
Linear models based on historical operations, which most planning systems use, lose validity when assets process new feeds, and operate outside of known envelopes.
3. Linear models do not consider logistics constraints.
They also do not adequately model time. Ergo, the support of corresponding operational-level decision-making to develop feasible schedules from logistics plans requires additional effort. To add, continuous solvers have to connect with discrete events to manage timing, sizing, allocation, and sequencing decisions.
4. Scheduling itself is suboptimal.
Supply chain scheduling tries to connect an ideal production plan to a real-world operation. But scheduling systems often do not have the capability to fully optimize. As a result, supply chain operations usually do not align with production plans.
5. Updating models requires subject matter experts and significant time investments.
Planning and scheduling systems often use linear models, which not only go unmaintained but also do not reflect actual operation. Subject matter experts are typically needed to maintain the models.
To read a complete list of challenges associated with misaligned operational processes, please download Yokogawa’s Value Chain Optimization Manifesto.
Focus on market needs and customer experience
If an industrial organization does not have a good understanding of what its business processes are, how they work together, and how it would like them to work in the future—or if it builds new technology only around old processes—then digitalization will only supply a very small, incremental improvement at best. At worst, the organization risks accelerating process issues with technology.
One tactical solution is to reorient operational processes around market dynamics and demand-pull—that is, shifting the operational mindset from a focus on product and organizational needs to a focus on market needs and customer experience, and aligning assets and supply chains accordingly.
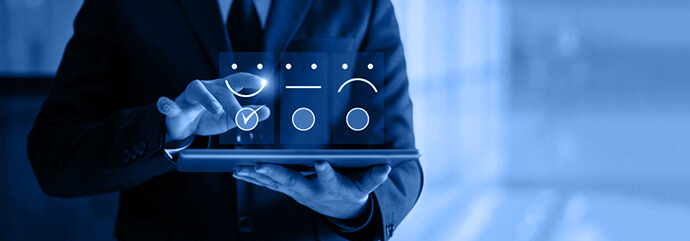
Reorienting operational processes to support a demand-pull business model can reduce inventory, improve the fulfillment rates and availability of premium products, and ensure an overall lean supply chain. Top-level DX decision-makers should consider adopting this business model early on in the DX journey. Strategizing ways to reorient people and technology around processes at the same time can help mitigate the risks associated with the people-process-technology separation.
Risk #2: Process management effectiveness
Effective process management expends fewer human, time, and money resources altogether. Strong management for work, business, and manufacturing processes is critical to the success of DX.
One risk a DX task force might run into is management not having a clear understanding of how those processes are supposed to work in the first place. Driving a DX project forward without a clear, uniform understanding of those processes can result in inefficient, resource-expensive, misaligned work, business, and manufacturing processes after digitalization. Misaligned processes within a process organization can create more silos between departments and people, lowering plant productivity and risking DX integrity.
Moreover, poor process management may lead to a waste of human resources and poor interdepartmental communication and cross-functional collaboration, lowering morale, and heightening frustrations.
The technology-related risks of digital transformation
Risk #1: Technology for the sake of technology
Process manufacturers must link technology investments to business and process value, not to “technology value.” In other words, technology use should always have a purpose—to support an enterprise’s business strategies and processes, not to satisfy a desire to have cutting-edge technology.
The separation between business and technology can create additional hurdles for organizations. Notably, it can prevent cross-functional collaboration, silo departmental DX projects, render transformation processes inflexible, and delay DX altogether.
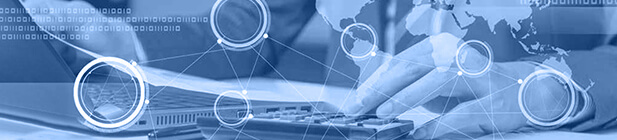
This separation happens because a process manufacturer’s main business strategy is not visible, so people from C-suite executives to shop-floor workers do not follow it. This risks all technology investments because the enterprise does not know exactly what issue it is trying to solve through transformation.
Risk #2: Legacy systems
One of the highest technological hurdles many process manufacturers have to leap over is upgrading legacy systems. Today, many plants employ control systems and other ancillary systems that are two or more decades old. Outdated hardware and operating systems make plants relics of a bygone era. Even worse, legacy systems often do not integrate with IIoT.
Challenges of legacy systems
Efficiency on the modern factory floor relies on interconnectivity, enterprise resource planning (ERP) systems that integrate across all stages of production, and more extensive accessibility of real-time information. Legacy systems fall short of keeping pace with digitalization. And they prevent plants from taking advantage of the technological capabilities that DX aims to establish, such as better data integration.
Not only that, but legacy systems are difficult and expensive to maintain. Many plants conserve them by replacing individual components, which original vendors are often no longer supplying. Eventually, failures will mean the end of a system altogether.
Transforming a legacy system into a newer one designed to facilitate DX is understandably challenging. It uses tremendous labor and dollar resources. And the fear of change it introduces can create resistance from some in a process-manufacturing organization.
Furthermore, finding the skilled people an enterprise needs to migrate an old system to a new one might feel daunting: most legacy software uses outdated programming languages, original documentation might be next to impossible to find, and original developers might be retired or working for another company.
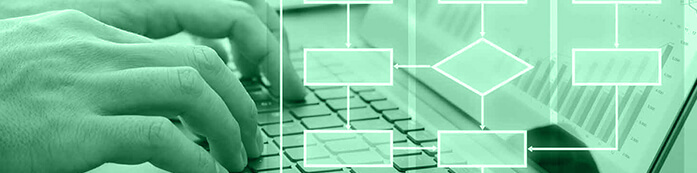
To help make modernizing legacy applications easier, IT specialists should consider using containers. These function by removing a legacy application’s reliance on its underlying infrastructure services, making access to the application’s resources abstractable, and the application itself portable. As a result, refactoring legacy applications becomes faster.
Tied to legacy systems, technical debt happens when system developers do not follow and document a project plan to expedite project delivery while not concerning themselves with refactoring and improvement costs in time, money, and resources in the future. It causes entropy in a system—the more a system changes, the more disordered it becomes. And like financial debt, the longer it is left, the worse it becomes.
Another issue a DX project might run into is reconciling “architecture by accident.” This is the result of siloed departments building their own systems to achieve department-specific goals, without thinking about how these systems can and might work with others. The result could be, that as a DX project pushes forward and its task force starts to remove departmental siloes, the task force discovers - unfortunately - that these systems do not work well together.
Risk #3: Data quality
Migrating partial, incomplete, or unreliable process and asset data to a repository is another challenge a process manufacturer might encounter when upgrading a legacy system. This data, poor as its quality may be, is still important to a plant.
So to successfully protect and migrate it, IT engineers have to extract it, transform it to match new formats, cleanse it to address quality issues, validate it to test for errors, then load it into the new system. It is a delicate process, akin to surgery. A mistake in data migration could mean the permanent loss of data, which can be a serious problem for DX efforts.
Data and analytics are critically important to the DX journey and its long-term outcomes. As an analyst for Gartner states in the article “Why Data and Analytics Are Key to Digital Transformation,” companies will require the ability to make faster-paced, forward-looking decisions in order to compete in the emerging digital economy. And the companies that lead said economy leverage data and analytics to make these decisions, which accelerate operations and catalyze innovation.
Digitization and digitalization—prerequisite phases in the DX journey—set up the technological foundations that process manufacturers need to gain better, clearer insights from data and analytics. But without existing good quality, meaningful data to start, the technological investments that process manufacturers make during digitization and digitalization—such as smart sensors, IIoT devices, and artificial intelligence (AI)—can either quickly stall further DX efforts or completely go to waste.
AI, for example, needs an input of usable data to perceive its environment and take meaningful actions on it. Without it, AI applications will not function as plant engineers intend them to.
Risk #4: Cybersecurity
Data breaches are a primary concern for the process industries. Research from Sikich highlights this fact, stating that 50% of surveyed manufacturers had experienced data breaches or cyberattacks involving computer systems or networks in 2019.
Cybersecurity challenges arise when process manufacturers migrate data and upgrade legacy systems. The convergence of IT and OT and the overall expansion of plant connectivity open doors to increased risks of hacking, system sabotage, IP theft, equipment damage, financial damage, reputation damage, and workplace injury and death.
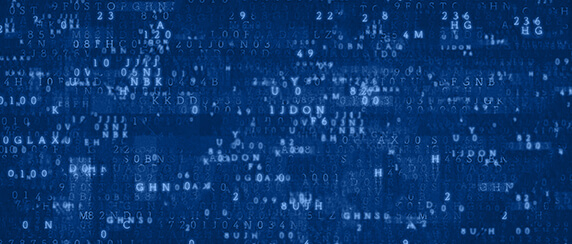
Unfortunately, while digitalization is a necessary way forward, it does away with the moderate degree of “security through obscurity” that many legacy systems offer. These older systems are proprietary closed systems from one vendor on an isolated, air-gapped private network. To penetrate such a network, a cyber threat actor would have to infiltrate a plant to recompile vendor-specific firmware—it would not be possible to access network attack vectors from outside the plant.
During digitalization, wireless network security becomes a challenge when plant data connects to the enterprise at large via the cloud and when systems adopt open architecture.
A cybersecurity solution
Implementing an effective end-to-end systems and solutions approach increases not only awareness and protection but also business agility while lowering operational costs and reducing downtime. Yokogawa stands behind a life cycle approach in its automation consulting and life cycle services. Such an approach comprises the following cyclical stages:
1. Assessment and analysis:
The consulting stage starts with life cycle service solutions for both new systems and installed base systems.
2. Design and implementation:
During this stage, IT specialists deploy and enhance optimal controls.
3. Operational support:
After design and implementation, Yokogawa’s plant life cycle services provide training, regular updates, continuous monitoring, and support for systems and solutions.
4. Life cycle support:
At this stage in plant life cycle services, Yokogawa provides periodic audits, analysis, and review of controls.
Plant owners need to continuously maintain measures to make sure they stay effective in the face of changing and new types of technologies. Without incurring excessive costs, Yokogawa’s approach to plant life cycle ensures customers can lower costs to manageable levels at all times.
Risk #5: Data Storage & Security
At the core of IT infrastructure modernization lies the cloud. Thanks to cloud computing, process manufacturers no longer always need on-premises IT data centers, historians, server colocation, and traditional in-house IT resources. It provides an opportunity to reduce the need for clunky, labyrinthine legacy IT systems by providing virtual access to computing infrastructure.
However, since the cloud stores information in an off-premise, data center accessible through the Internet, it can put sensitive data at risk. The cloud’s third-party provider stores a plant’s sensitive data and gives access to it over the Internet but limits data control and visibility, posing security concerns.
Even though a cloud-services provider stores a plant’s data, the plant is responsible for protecting its data while the provider protects the cloud. This is true for every cloud service, from software as a service (SaaS) to infrastructure as a service (IaaS), which present their own unique data security challenges.
Risk #6: Open architecture
The days of proprietary vendors creating leading application-development frameworks by themselves are almost over. Online communities of open-source developers around the world are taking up the task. And the innovative benefits of a globally connected talent pool are accelerating open-source frameworks such as Linux, JavaScript, and HTML5.
Open architecture offers process manufacturers speed, flexibility, and scalability. But benefits aside, it exposes security risks at integration points, which open-source developers are building with publicly available code. The risk of hacking is ever-present with open-source frameworks, so process organizations must take on the burden of continuously managing that risk.
How can Yokogawa help?
Partnering to create future-proof results
DX is a daunting challenge with many interdependent factors, and there is no one-size-fits-all solution for manufacturers. However, when done correctly, DX can lead to future-proof results. But just as a company’s business strategy and operations are unique, so too is the approach to DX.
Of the organizations that were triumphant in their DX efforts, 71% accomplished that feat with the aid of a partner. Process industry companies need a business partner who starts by engaging and aligning with their goals, aspirations, and business strategies. As the risks related to digital transformation are real, organizations need a partner with relevant domain knowledge to take any risk seriously and act in accordance.
To help organizations identify the risks and opportunities of DX, Yokogawa employs a discover-design-deliver framework to implement and contextualize any DX project. Understanding DX objectives, goals and risks, identifying challenges, quantifying financial impact, and estimating change complexity preface Yokogawa’s engagement model.
A strategic partnership with Yokogawa can fundamentally change business outcomes by driving the collaborative innovation process organizations need to meet changes in customer and market demands. All stakeholders in a process-manufacturing organization stand to benefit.
Související produkty a řešení
-
Koncept Digitální transformace
With Yokogawa's wide knowledge of and expertise in process manufacturing, Yokogawa can help bring about the realization of a digital transformation that will lead to a better future for its customers.