Executive Summary
Nagasaki Works
Saibu Gas Co., Ltd. built an LNG receiving terminal at its Nagasaki Works to ensure a stable supply of clean-burning utility gas to its customers in Nagasaki Prefecture. In a project that will serve as a model for future terminals, Saibu Gas achieved a superb design that fit all plant functions into a limited area. Yokogawa's 30 years of experience in providing control systems for LNG receiving terminals was instrumental in ensuring a successful outcome for this project.
- Scalable, flexible configuration with functions distributed to multiple controllers on a facility basis
- Redundant architecture optimally designed for requirements of entire plant
- General-purpose communications network used for control bus
- Integrated operation environment through web-based human-machine interface (HMI)
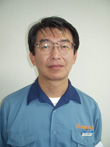
“We are very satisfied with the STARDOM system as it has exactly the kind of ultra-distributed configuration that we had in mind. The plant started up smoothly, and our operators are comfortable working with this system.”
Mr. Hayakawa
Manager
Nagasaki Works, Saibu Gas
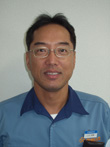
Mr. Yamanaka
Manager
Nagasaki Works
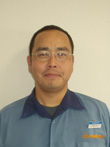
Mr. Murashima
Leader
Nagasaki Works
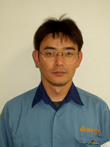
Mr. Masumoto
Leader
Nagasaki Works
The Challenges and the Solutions
Scalable, flexible configuration with functions distributed to multiple controllers on a facility basis
The Nagasaki Works employs many cutting-edge technologies at its LNG receiving terminal facilities, which include a berth for arriving LNG tankers, an LNG regasification plant, and a terminal where LNG is reloaded onto tank lorries for shipping. STARDOM controllers are assigned to the monitoring and control of the individual facilities, each of which carries out a different function.
Redundant architecture optimally designed for requirements of entire plant
Assigning controllers on a facility basis ensures each facility's independence, improving the reliability of the entire LNG terminal. For greater safety, high-priority facilities have redundant controllers. Facilities with a redundant configuration employ a single CPU, eliminating extra investment for higher cost performance.
General-purpose communications network used for control bus
Controllers installed over a wide area spanning from the central control room (CCR) to the berth and shipping terminal communicate with each other through Ethernet and fiber-optic cables. The cost of the new system is reduced by using general-purpose network cables and equipment, and reliability is improved through the use of redundant control buses and repeaters.
Integrated operation environment through web-based HMI
A SCADA system with a web-based HMI enables the same operation to be performed at the CCR and the berth control room, which are 1 km away from each other and are connected by fiber-optic cables.
The Site Configuration
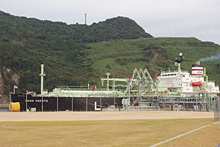
Berth
In late September 2003, the Nagasaki Works received its first shipment aboard the tanker Aman Hakata, which arrived from Malaysia with 18,800 m3 of LNG. This was the ship's first visit to Japan.
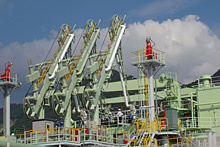
Loading arm
LNG is received through the on-shore piping, which is connected through these loading arms to the tanker moored at the berth.

Berth control room (FCN autonomous controller)
Displays are mounted next to the controller in the berth control room to enable monitoring of the overall site status. A web browser displays the same information here and at the CCR, which is 1 km away.
As the HMI information is transmitted via the control bus, there was no need to install a separate network.
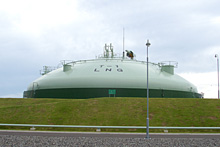
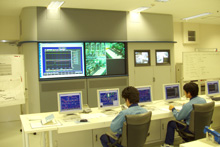
CCR
All LNG terminal functions including gas production and storage, maintenance, and disaster prevention are centrally controlled from the CCR. The two large displays give an integrated overview of operating status, making it possible to deal with abnormal incidents quickly and operate the terminal safely.
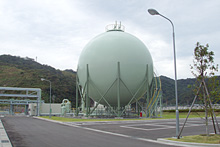
About Saibu Gas Co., Ltd.
Founded in 1930, Saibu Gas stably supplies gas to 16 cities and 16 towns (as of June 2007) in three prefectures of the Kyushu region. Its business operations can be categorized into:
- Production, supply, and sales of utility gas
- Heat supply
- LNG sales and cold energy utilization
- Production, sales, and installation of gas appliances, and related construction work
About the Nagasaki Works
The LNG receiving terminal at the Nagasaki Works was built in 2003 to facilitate the supply of gas to Nagasaki Prefecture. In this rugged and confined coastal area, Saibu Gas succeeded in designing and constructing a berth, regasification plant, shipping terminal, and other facilities that enable the stable supply of gas to 120,000 households in the Nagasaki area.
<System Details>
Controller: STARDOM FCN Autonomous Controller
HMI: STARDOM SCADA VDS
Průmysly
-
LNG Regasification & Storage
YOKOGAWA's production control systems are operated at 54 LNG receiving terminals around the world, and 2/3 of the terminals in Japan. YOKOGAWA contributes to stable and efficient gas supply at LNG receiving terminal through the total process, loading, storage, regasification, and metering.
-
LNG Supply Chain
YOKOGAWA has been engaging in LNG automation by supplying the latest sensors, analyzers, control and information systems for more than 50 years since LNG was first imported to Japan. YOKOGAWA is one of the biggest automation suppliers to the worldwide LNG supply chain, liquefaction, transportation, and regasification.
-
Terminály
Today, many end-users not only in the oil, gas, and petrochemical industries, but also in the LNG/LPG and bulk industries are facing common logistical challenges. Those challenges include shortening the product delivery time, improving loading efficiency, adapting to changes in the manufacturing process, improving safety, increasing administrative efficiency, reducing labor costs, integrating data systems, visualizing operations, managing traffic, and so forth.
Yokogawa has been providing solutions to meet customers’ needs for terminal automation and management for decades.
Související produkty a řešení
-
FAST/TOOLS
Originating as the Flexible Advanced System Techniques (FAST) project, FAST/TOOLS today is a comprehensive, fully-integrated SCADA application suite. Powerful and flexible, FAST/TOOLS serves installations ranging from 50-point unit processes to multimillion-point offshore production and pipeline systems that extend over thousands of miles.
-
Process Control PLC/RTU
From process plants to remote locations, our process control PLC and Remote Terminal Unit (RTU) help users maximize operational excellence.