挑战
客户面临的挑战
提高发电厂效率
我们的解决方案
横河电机通过改善对燃料、蒸汽和给水的控制,帮助电厂更高效地运行。
使能技术
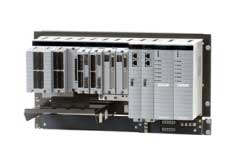
CENTUM VP集成生产控制系统
CENTUM VP集成控制系统可确保工厂性能实现无中断的“正常运行”,从而在可再生能源方面达到较高的生产率和盈利能力。
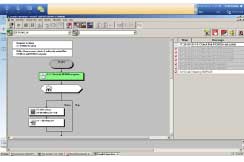
Exapilot提高操作效率软件
Exapilot是在线导航工具,可以指导操作员逐步进行工厂运行的操作步骤。Exapilot使系统按照标准操作程序(SOPs)自动运行,并对过程和设备异常进行早期检测。
客户面临的挑战
安全有效地启动锅炉,这是一个很有技术含量的复杂过程。
我们的解决方案
横河电机系统通过将燃料油加热转换为生物质燃料等自动化流程,使启动时更安全、更高效。图形显示为操作员提供了进入每个流程状态的实时窗口。
使能技术
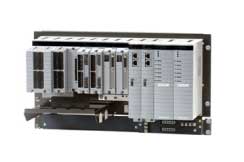
CENTUM
CENTUM VP集成生产控制系统
CENTUM VP集成控制系统可确保工厂性能实现无中断的“正常运行”,从而在可再生能源方面达到较高的生产率和盈利能力。
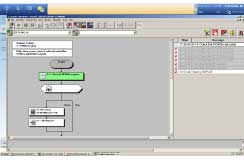
Exapilot提高操作效率软件
Exapilot是在线导航工具,可以指导操作员逐步进行工厂运行的操作步骤。Exapilot使系统按照标准操作程序(SOPs)自动运行,并对过程和设备异常进行早期检测。
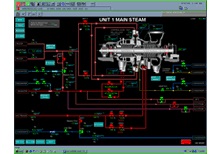
模拟器
高精度、全厂培训模拟机
客户面临的挑战
提高燃烧效率,减少/消除有害烟气排放。
我们的解决方案
横河氧气浓度分析仪可以测量烟气中的氧气(O2)浓度。根据此信息,可以调节空气的燃烧比以优化燃烧。同样,我们的烟道气体分析仪可通过测量烟气中氮氧化物(NOX)和硫氧化物(SOX)的浓度来减少有害物排放。
使能技术
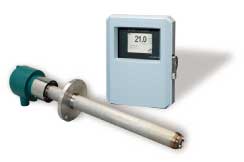
ZR系列氧化锆氧分析仪
横河电机的氧化锆氧分析仪用于燃烧监测和控制应用,并广泛应用于各行各业,以优化燃烧并减少NOX排放。

SG750烟道气体分析仪
SG750烟道气体分析仪由红外气体分析仪单元、氧化锆氧分析仪单元和取样单元组成,可同时测量多达五个组份:NOX、SO2、CO2、CO和O2。
客户面临的挑战
使用混合燃料时保持稳定的蒸汽供应。
我们的解决方案
横河电机的控制系统能够计算更好的燃料混合比并调整燃料供应,以稳定主要蒸汽压力。
使能技术
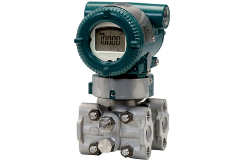
EJX / EJA系列压力变送器/差压变送器
DPharp系列数字压力变送器采用差压高精度共振压力(DPharp)传感器,代表了变送器技术领域革命性的先进技术之一。
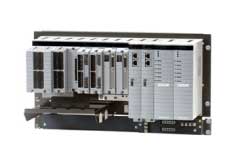
CENTUM VP集成生产控制系统
CENTUM VP集成控制系统可确保工厂性能实现无中断的“正常运行”,从而在可再生能源方面达到较高的生产率和盈利能力。
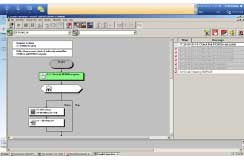
Exapilot提高操作效率软件
Exapilot是在线导航工具,可以指导操作员逐步进行工厂运行的操作步骤。Exapilot使系统按照标准操作程序(SOPs)自动运行,并对过程和设备异常进行早期检测。
详细介绍
生物质发电过程
生物质电厂大致分为直接燃烧、混合燃烧及气化等类型。利用直接燃烧发电的方法,蒸汽是由燃烧诸如木材废料、农业废料和牲畜废料得来的热量所产生。蒸汽转动涡轮机,然后涡轮机驱动发电机发电。使用这种方法重要的是确保生物质材料的稳定供应,并在这些材料中保持水分含量均匀分布。混合燃烧发电方法依赖于生物质燃料和煤来提供稳定的电流。当生物质燃料不足以为工厂供电时就加入煤。在气化发电方法中,加热生物质燃料以提取可燃气体,可燃气体被净化后,可为燃气发动机或燃气涡轮机提供动力来发电。
控制和测量技术
全厂系统和仪器仪表 | ||
---|---|---|
信息
|
控制
|
测量
|
处理方式 | ||
燃料卸载 | 锅炉 | 涡轮 |
|
|
|
烟气处理 | ||
|
|
|
参考
- Yokogawa's CENTUM CS 3000 DCS Monitors and Controls Operations at Poultry Litter-to-energy Plant
- The boiler and turbine startup procedures reduces operator workload and helps to ensure a smooth and safe startup
- Thai SPP uses CENTUM CS 3000 to improve efficiency of Biomass Power Plant
- The burning of the ground rice husks in the boiler's furnace chamber is a complex process that must be carefully controlled
- Complex starting up and shutting down operations of a biomass power plant were automated with CENTUM VP.
- Operator errors and interventions were eliminated in all critical processes.
The automation suppliers that will be successful in the long term will be those that effectively address application or industry specific problems for end users with a value proposition that cannot be ignored. These problems exist throughout the process industries today, and they won't be solved by simply offering a product, but through a combination of hardware, software, services, application expertise, and knowledge.
In ARC's view, customers need a compelling business value proposition to justify investment in any kind of automation. Vigilance and VigilantPlant were created with this in mind. Yokogawa's vision with VigilantPlant is to create an environment where plant personnel and operators are well informed, alert, and ready to take action.
This white paper provides an overview of how Yokogawa believes its customers can best prepare for and position themselves to benefit from IIoT-enabled technology and solutions and digitalization in general to emerge as the successful connected industrial enterprises of the future.
Yokogawa’s industrial automation (IA) product and service offerings, industry domain knowledge, and VigilantPlant approach – which emphasizes safe, secure, and uninterrupted operations -- provide a solid foundation for an Industrial Internet of Things that specifically addresses the requirements of process automation, particularly for the OT side of the equation. To be able to provide an equally solid foundation for the IT side, Yokogawa is partnering with Cisco Systems and other industry leaders.
Yokogawa has come a long way in making its message clear to the world of process automation. Last year, the company embarked on a full-scale global marketing campaign to make customers aware of the company's focus on system reliability, security, dependability, and robustness. Dubbed "Vigilance", the campaign created a unified message for the company and greatly helped expand awareness of the Yokogawa brand and corporate philosophy.
Process automation end users are under more pressure than ever to do more with less. The current economic climate means that many automation capital projects are on hold. With capital budgets tighter than ever, users instead focus on operational budgets (where cost cutting is also a key concern), or on automation investments with a very rapid return on investment.
In today's dynamic industrial marketplace, the only constant is change. Raw material costs, energy costs, market demands, environmental and safety regulations, technology, and even the nature of the labor force itself are constantly changing, and not always in predictable directions.
Recently, manufacturing industries are trying to slash the total cost of ownership (TCO). Batch processes are not exceptions. Until recently, in comparison to continuous processes, batch processes have generally not yet undergone systematization and standardization.
As industrial plant systems have increased in scale and their automatic control algorithms advanced, today's operators are required to have more advanced skills and knowledge of theplant systems and to learn the actions to be taken in response to any possible situations including emergencies.
The trend of open system architecture is becoming an important issue with distributed control systems (hereinafter abbreviated as DCSs). To meet this demand, the operation and monitoring functions, and the system generation functions of the CENTUM CS 3000 system are designed to support Windows NT and OLE for Process Control (OPC).
As more fieldbus devices are made practicable, demand is increasing for a distributed control system (DCS) which integrates fieldbus devices in its engineering, operation, and monitoring environments. Conventionally, control has been implemented by the dual-redundant CPUs and control bus within a DCS; however, sufficient reliability must be ensured even when it is distributed over field networks.
The recent increase of devices enabled for a field network such as the FOUNDATION™ Fieldbus is phenomenal. This has been amplifying a requirement for distributed control systems (DCSs) to be capable of constituting a more pliant and efficient production control system by means of flexible connections to field networks in addition to traditional 4 to 20 mA signals.
The environment surrounding process control systems has changed dramatically as the performance of personal computers improves and the Windows operating system advances, there has been a move towards the trend of open architecture. As we are already aware, in addition to the traditional high reliability level and the unique operability there has been an increase in demand for the interoperability of human- machine interfaces (HMI), which are responsible for the operation and monitoring of our distributed control system (DCS).
Drastic changes in the economy of manufacturing industries, has led to increasing demand for plant operations to reduce personnel, improve efficiency, and increase the operation rate of facilities. On the other hand, for plants to operate safely, improvements in reliability and operational safety cannot be neglected.
In this day and age, just simply buying a personal computer, taking it home and turning it on will enable you to be taken to the world of Internet. In such an era, communication connection capability and prospects is increasing in importance. DCSs are no exception for concern.
The manuals of control systems such as a DCS provide a vast amount of information depending on their multi-functionality and functional integration. A conventional large-scale control system our company offers comes with more than 10,000 pages of paper documents.
Yokogawa Electric has been using Pair & Spare method as a reliability-enhancing technology for its line of distributed control systems (DCS) since the release of the CENTUM CS in 1993. As a result, the system has achieved an availability factor of seven 9's (99.99999%) for the record of operation to date.
Improved plant operation efficiency and reduced maintenance costs based on appropriate predictive maintenance are the common objectives that need to be achieved in every manufacturing domain. Exaquantum is positioned above the Process Control System (PCS) layer and gathers and stores huge volumes of process and laboratory data over long terms.
Environmental friendliness (E) must be assessed in today's product design in addition to the conventional design considerations of quality (Q), cost (C), and lead time (D). Hence, the product design system must be urgently restructured in order to minimize the environmental impact of a product throughout its life-cycle from purchase of the materials and parts, through manufacturing and distribution, to use and disposal.
As a company that has strong relationship with nature and provides products using nature's blessings, Mercian Corporation is committed to the environment. Its environmental philosophy is "Mercian thanks nature's blessings and capability that sustain life, and seeks to balance environmental preservation with creating an affluent society."
As for a controller used in a distributed control system (DCS) shown in Figure 1, covering as many applications as possible with a single controller will bring cost reduction effects such as easy engineering and a small controller installation area. Therefore, the controller is required to process large amounts of data more quickly.
Global market pressures are causing businesses world wide to strive to lower manufacturing costs and to become more agile companies in order to quickly respond to changes in market demands and to fend off competitive threats. Yokogawa's customers in all industries and markets are responding to this pressure by working to more closely integrate their plant manufacturing systems with their enterprise wide business systems in a seamless manner.
Recently, standardization of procedural automation of manual operations has been promoted mainly by the International Society of Automation (ISA), and the functional requirements necessary for automation are being studied by the ISA106 committee in the US.
For a coal fired power generation plant (hereafter referred to as "BTG facilities," in which "BTG" stands for boiler, steam turbine, and generator) supplying power to a large-scale production plant, the CO2 emissions from such facilities are a critical issue today.
Due to emerging competitors from the rapidly growing countries such as India and China and the global economic downturn triggered by the Lehman shock, many companies in the process industries are struggling to survive the severe global competition.
视频
How much do you know about pressure transmitters? Are you accurately, quickly and reliably measuring pressure? Ultimately, the drive of any good pressure transmitter is to get an accurate, reliable pressure measurement to the data user quickly. This video gives you the answers to your basic questions about pressure and pressure transmitters.
新闻
-
新闻 2022年5月25日 横河电机收购垃圾焚烧发电和生物质发电厂优化技术供应商Dublix
-
新闻 2024年6月5日 横河电机收购可再生能源管理解决方案供应商BaxEnergy
- 在40多个国家拥有超过120 GW的可再生能源发电装机容量 -
想要了解更多的信息,技术&解决方案?
联系我们