在20世纪70年代中期,横河电机发布EBS电子控制系统,从而正式进入电力行业。从那时起,横河电机一直坚持不断发展技术和能力,旨在为客户提供更好的服务和解决方案。
横河电机凭借着电力解决方案网络,在充满活力的电力市场中发挥着积极的作用。通过结合资源和行业知识,使得团队合作更加紧密。横河电机的电力专业人员们将携手合作,为客户提供适合其复杂要求的解决方案。
详细介绍
POLLUTEC 2016

November 29 - December 2, 2016
Lyon Eurexpo France,
Lyon, France
Latin America Utility Week 2016
September 13-15, 2016
Booth B06, Transamerica Expo Center,
Sao Paulo, Brazil
Myanmar Green Energy Summit 2016

August 15-16, 2016
Booth 6, Sule Shangri-La,
Yangon, Myanmar
POWER-GEN Europe 2016
June 21-23 2016
Milan, Italy
Middle East Electricity 2016
March 1-3, 2016
Dubai, UAE
POWER-GEN Europe 2015
June 9-11, 2015
Amsterdam, The Netherlands
International Power Summit 2015
February 25-27, 2015
Lisbon, Portugal
POWER-GEN International 2014

December 9-11, 2014
Orange County Convention Center, Orlando, USA
International Energy Congress and Fair 2014
November 24-25, 2014
Congresium Ankara, Turkey
POWER-GEN Middle East 2014

October 12-14, 2014
Abu Dhabi National Exhibition Centre, Abu Dhabi, U.A.E.
POWER-GEN Europe 2014

June 3-5, 2014
Cologne, Germany
Hannover Messe 2014
April 7-11, 2014
Hannover, Germany
Power Plant Controls and Instrumentation Asia 2014
February 24-26, 2014
Kuala Lumpur, Malaysia
POWER-GEN International 2013

November 12-14, 2013
Orange County Convention Center, Orlando, USA
World GeoPower Markets Indonesia & Philippines
June 18-19, 2013
Ritz Carlton Hotel, Jakarta, Indonesia
Energy & Water Conservation Expo & Forum 2013
June 17-19, 2013
Bahrain International Exhibition Centre (BIEC), Bahrain
POWER-GEN Europe 2013

June 4-6, 2013
Messe Wien, Vienna, Austria
ELECTRIC POWER 2013
May 14-16, 2013
Donald E. Stephens Convention Center, Rosemont, USA
Hannover Messe
April 8-12, 2013
Hannover, Germany
POWER-GEN Middle East 2013

February 4-6, 2013
Qatar National Convention Centre, Doha, Qatar
涡轮机控制解决方案
用于涡轮机械控制应用的输入和输出(IO)模块为涡轮机械的高速控制和保护提供了强大的功能保证。
它们具有高度可靠的双冗余配置和混合信号接口,用于处理模拟和数字数据。
IO模块有两种类型,可以为发电行业提供非常好的控制解决方案。
伺服模块设计用于通过与特定传感器和执行器连接来控制涡轮速度、操纵蒸汽和燃料控制阀。
高速保护模块设计用于通过关闭蒸汽和燃料阀来保护涡轮机免受超速和其他重大条件的影响。
特点
-
用于涡轮机械速度控制的伺服模块
-
用于保护涡轮机械的保护模块
-
以5或10毫秒的间隔周期进行高速控制
-
可编程保护逻辑
-
双冗余配置
-
模拟 - 数字混合信号接口

典型控制算法:
-
涡轮机启动和关闭序列
-
入口/提取值比控制
-
入口压力控制和限制器
-
提取压力控制
-
发电机本地控制
-
涡轮机保护 - 燃烧器管理控制
-
锅炉控制
-
工厂平衡(BOP)控制

集散控制系统(DCS)
CENTUM VP是先进DCS系统,符合热能、燃气轮机和可再生能源发电厂的要求。CENTUM VP经常被用于许多电厂中运行使用,其可扩展性、稳定性、功能和可靠性已得到广泛认可。
电厂模拟机
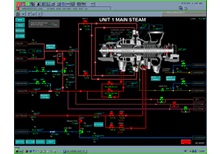
高精度,全厂培训模拟机
您可以利用使用横河电机的高精度全厂模拟机(>99%稳态; 95%动态)为自己的工厂提供量身定做的培训计划。
横河电机模拟机可以服务于运营化石燃料、燃气轮机和热电联产发电厂的各类客户。
受益/产品特点:
-
灵活的培训
无论您的工厂采用哪种控制系统,我们都能提供可以覆盖全厂的模拟机系统。灵活的培训方案可以帮助操作员游刃有余、灵活敏捷地掌控整个工厂。 -
减少调试时间
在模拟机上进行控制回路的测试和调整,可尽量将风险降至较小,从而确保工厂调试过程可以平稳地进行。 -
工厂运营优化
模拟机模拟工厂运营的功能,可识别对操作程序的修改也可优化工厂操作。 -
高精度
横河电厂仿真系统为您带来惊人的99%准确度(> 99%稳态;> 95%动态)。
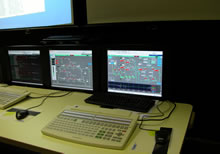
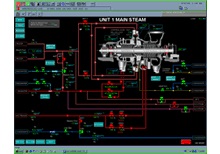
客户的声音
“如果没有横河电机的全厂模拟机,我们将无法想象该如何操控我们的工厂。”
越南电力生产商越南电力公司(EVN)的子公司Pha Lai Thermo Power Joint Stock Company执行官Nguyen Khac Son说:“通过模拟机培训,我们的试用期员工和新操作员都可以通过使用与真实系统完全相同的操作员界面很快学会如何操作公司300兆瓦的燃煤机组。即使是经验丰富的操作员也可以有效地学习如何处理每个可能会发生的事故,因为它是如此的真实。如果没有横河电机的全厂模拟机,我们无法想象怎样运行我们的工厂。不但是我们的工厂,即使对EVN其他工厂的操作员也都是至关重要。此外,许多PVN†的发电厂运营商来到这里进行模拟机培训,以了解如何使用横河电机DCS操作燃煤发电厂。因此,我们的模拟机用于培训越南生产商的大多数运营商。”
电厂服务

我们的承诺并不会随着项目完结而结束。基于我们对客户工厂生命周期的整体考虑,横河电机将提供一致、可靠的服务。
更重要的是,Yokogawa电力服务公司(TechComm)是横河电机的子公司,可以在操作员培训、调试、工厂运营和维护方面提供广泛的服务。
我们的全球网络
参考
The Bahia de Bizkaia Plant is one of the most significant power projects to be carried out in this region. The project has been led and financed by Ente Vasco de la Energia, Repsol-YPF, British Petroleum, and Iberdrole S.A., with the total investment coming to approximately 600 million euros.
Sandi Electricity Company selected Yokogawa to replace Foxboro IA Series at its power plant.
Yokogawa carefully extracted the configuration of old systems and successfully replaced with CENTUM VP and ProSafe-RS.
Territory Generation supplies electricity to the NT's grid with their 8 geographically isolated power stations.
Territory Generation selected FAST/TOOLS to integrate new & renewable energy to the power grid.
- The community energy management system (CEMS) at F-Grid Miyagi efficiently supplies electricity and heat to the industrial park.
- During the two-year demonstration experiment, costs were reduced by 20% compared with the past.
Granite Power is a geothermal company that has developed GRANEX®, a patented direct supercritical fluid heat transfer technology for the efficient, eco- nomic, and zero carbon emission generation of electricity from low grade geothermal sources using the Organic Rankine Cycle (ORC).
TSE向客户提出了一种漂浮式太阳能光伏系统,该系统漂浮在工厂的蓄水池、冷却池和污水处理池中。
横河电机的CI服务器和FA-M3 PLC为工厂的清洁电力生产做出了贡献。
- All correct operation procedures are carefully configured in the CENTUM CS 3000 and smoothly in operation
- CENTUM CS 3000 ensures stable supply of electricity and steam to Bangkok's Suvarnabhumi airport
- The STARDOM network-based control system and FA-M3 range-free controllers play an important role in smoothing out the supply of this power to the grid
- STARDOM and FA-M3 ensure smooth supply of power to grid by wind farm equipped with large-capacity NAS batteries
- Thai SPP uses CENTUM CS 3000 to improve efficiency of Biomass Power Plant
- The burning of the ground rice husks in the boiler's furnace chamber is a complex process that must be carefully controlled
- Yokogawa's HXS10 solar controller optimizes conversion efficiency at Australian solar cooling plant
- Accurate sun tracking and visualization of all process data
- Australian National University's "Big Dish" controlled by Yokogawa PLC and FAST/TOOLS SCADA
- FAST/TOOLS benefits us in many ways and allows us to clearly see the entire process, giving us the information we need to take immediate action
- Fully automated power plant supplies steady flow of electricity to national grid
- The CENTUM CS 3000 plays a core role by controlling and enabling the monitoring of all processes at the EGCO Cogen plant
- Steady power supply and safe operation thanks to reliable Yokogawa CENTUM CS 3000 and transmitters
- Environmentally optimized operation by fine-tuned boiler combustion control and strict monitoring and control of CO, NOx and SOx in flue gas and pH of water from cooling towers
- Full replica plant simulator for effective plant operation and engineering staff training
- Annual maintenance contract
- Steady boiler control by CENTUM CS 3000 with dual redundant CPUs and seven 9s availability
- Total plant information integrated into supervisory information system via OPC interface
- Reduced water, coal and other resource consumption
- Power supply made dramatically reliable thanks to CENTUM CS 3000 with seven-nines availability
- Visualization of almost all plant data on the same HMI by linking up subsystems via Modbus
- Improved plant performance
- 2009 PACE Zenith joint winner project
- Reduced operating and maintenance costs
- Increased power generation
- Improved plant operating flexibility
- Modernized, screen-based operations
- Reduced emissions
- Modernized controls, assured stable power supply to Ulaanbaatar by a highly reliable, expandable distributed control system
- Fully automated boiler, burner, balance-of-plant operations
- Power plant simulator for efficient DCS operator training
At the age of approximately 30 years the plant underwent $A 72 million technology upgrade in 2001, to improve operating reliability and performance. Macquarie Generation, Yokogawa Australia and Ralph M Lee concluded an alliance agreement to supply and install the replacement control system at Liddell.
The Itoigawa Power Plant was constructed adjacent to a cement plant in Itoigawa City, Niigata Prefecture, and is operated by an IPP that supplies electricity to Tohoku Electric Power, one of Japan's major power companies. The use of a 149 MW coal-fired CFB boiler in this power plant is a first for an IPP in Japan, and this effectively reduces NOx emissions.
Unified operator interface solution enables remote operation
The construction of Tuas Power Station started in the mid 1990s. The plant has steadily grown to be a significant player in the competitive Singaporean electricity market. Stage One of Tuas Power Station is equipped with the country's largest steam generators which are capable of producing 600 MW each.
- Monitoring and control of the entire cogeneration plant including the two once-through steam generators
- Reliable and cost-effective power supply
- Operator-friendly HMI
- Easy set point definition for all plant power generation operations
- Stable electric power generation
- Power plant optimization
- Control of electric power generation based on net performance
Since entering commercial operation in 2000, the environmental control facilities at the Tachibanawan Thermal Power Station have been managed effectively by the CENTUM control system, achieving a stable electricity supply with minimal impact on the environment.
The customer has successfully brought online a greenfield 800 MW supercritical power plant, using a Yokogawa full-replica plant simulator to ensure a fast and smooth plant commissioning process.
- Reduced cabling costs by using a commodity GPRS network infrastructure
- Additional reduction in system cost by making full use of existing components
- Reduction in cost of software by using all web-based technology
- Long-term service contract — no need to worry about a suspension of maintenance services
"Installing the Yokogawa TDL improved our capability to optimize urea injection for the SNCR. The monitors provided more reliability and accuracy, in a harsh environment, than the previous monitors."
Aboitiz Power Corporation is a holding company that was set up by the Aboitiz Group to oversee its investments in power generation, distribution, retail, and services. The company owns and operates several hydroelectric and geothermal power plants as well as a number of non-renewable power facilities throughout the Philippines. It also owns distribution utilities that are centered in high-growth areas in Luzon, Visayas, and Mindanao.
- Modern waste to energy facility in UK uses CENTUM CS 3000 and ProSafe-RS
- Lakeside exports at least 34MW per hour to the country's national grid
- Italian waste to energy plant turns to CENTUM, PRM and FOUNDATION fieldbus solution
- Nearly 1500 FOUNDATION fieldbus devices are monitored and managed using the PRM
- Yokogawa's CENTUM CS 3000 DCS Monitors and Controls Operations at Poultry Litter-to-energy Plant
- The boiler and turbine startup procedures reduces operator workload and helps to ensure a smooth and safe startup
- FAST/TOOLS SCADA system to remotely monitor the optimization of the process and make any required engineering changes to the live system.
- The Yokogawa control system (FAST/TOOLS, STARDOM, HXS10) monitors not only the sunlight but also the weather conditions.
- The visualization of data using the Exaquantum PIMS plays an important role in efforts to improve operations at this power station.
- To reduce operator workload and eliminate unplanned shutdowns, HERA decided on the use of field digital technology at this power station.
- A robust and reliable integrated control and safety system (ICSS) made up of the CENTUM CS3000 PCS and the ProSafe-RS SIS ensures safe operations while fully automating key processes.
- A variety of analytical instruments accurately measure the concentrations of key components, and this data can be monitored and controlled by the Yokogawa PCS.
The CENTUM CS 3000 / UOI was selected for this project. The control platform in the UOI is the GE Fanuc CIMPLICITY Human Machine Interface (HMI) system, which fully integrates the controls for the turbine and BOP auxiliaries and uses the same screens/formats at both the turbine and BOP HMI displays. The CIMPLICITY HMI used in the UOI is a SCADA based design that fully supports the customer's requirement for remote operation capability.
- CENTUM CS3000 seamlessly integrates with multivendor control systems through OPC interface.
- Challenging predictive maintenance to monitor many transmitter data through PRM.
- Yokogawa supplied an integrated boiler and turbine control, monitoring and protection system for each of the four generating units in a coal-fired power plant in Australia.
- Yokogawa also delivered two high fidelity operator training simulators for this plant.
- Yokogawa’s CENTUM VP and full-replica simulator contribute to the stable operation of this supercritical coal-fired plant.
- The two units have been operating successfully since start-up.
- 横河电机为工厂现代化提供控制、监视和保护系统。
- 没有任何问题和停车精细工程和横河产品成功运转。
Fully Automated Power Plant Supplies Steady Flow of Electricity to National Grid
There was possibility to operate a power generation unit without air heater during summer due to equipment failure.
AGL Energy successfully establish safe and economical operating conditions with Plant+ power plant simulator.
DP Level transmitter configuration can be very time consuming. Yokogawa DPharp EJA/EJX Pressure transmitters realize reduction in man hours by smart level setup feature.
Reverse osmosis (RO) is a separation process that uses pressure to force a solution through a membrane that retains the solute on one side and allows the pure solvent to pass to the other side. More formally, it is the process of forcing a solvent from a region of high solute concentration through a membrane to a region of low solute concentration by applying a pressure in excess of the osmotic pressure.
Measures temperature and vibration of the turbine for rapid identification of abnormalities.
What if you could detect signs of abnormalities in bus ducts (bus bars) quickly during maintenance and inspection work and respond to them at just the right time? Yokogawa DTSX monitoring solution constantly monitors connections that tend to deteriorate over time and contributes by pinpointing abnormality locations and reducing workload of maintenance personnel, helping to ensure stability in plant operations.
Yokogawa ensures a reliable heat and CO2 transfer system by using the standard GPRS protocol. The exclusive use of webbased technology enables the market gardeners to go online to order heat and CO2 and view information.
Power plant boiler houses designed to burn coal or high sulfur oil are required by Federal and State pollution regulations to "scrub" (remove) sulfur dioxide from flue gasses to meet emission limits. SO2 in flue gasses is known to be harmful to the environment, as it is one contributor to the formation of acid rain. pH control is critical for the proper functioning of the scrubber system.
The discharge of improperly treated industrial chemicals and fuel gas can have a major impact on the environment, posing a serious threat to public health. Concurrent with the global growth of manufacturing operations to keep pace with market trends, many countries are taking measures to deal with environmental problems.
A package boiler operates more efficiently if the oxygen concentration in the flue gas is reduced. Optimizing air intake for boiler operation requires continuous measurement of the oxygen concentration in the flue gas.
In flue gas desulfurization systems that use magnesium hydroxide (Mg(OH)2) slurry, the consumption of the desulfurization agent (Mg(OH)2) is controlled by using online pH analyzers. A great concern in the pH measurement is heavy staining of the pH electrodes by the Mg(OH)2 slurry. To ensure accurate measurement, frequent cleaning of the electrodes with an acid is required, adding to both maintenance workload and cost.
Industry:Chemical, Power
Recently, air pollution legislations such as the Clean Air Act to reduce the amount of air pollution are increasing worldwide. The Clean Air Act address numerous air quality problems. One of these problems is acid rain caused by sulfur dioxide and nitrogen oxide emissions from fossil-fueled power plants and other industrial and transportation sources.
One of the most common applications for differential pressure transmitters is flow measurement. DPharp differential pressure transmitters have some unique signal conditioning features to eliminate instability at low flow rates.
The SMARTDAC+ GM is best suited for applications where the voltage of each cell in fuel cells, secondary batteries and electrolyzers is measured.
Best Solution for Automatic Boiler Control
Sensors and controllers for the efficiency and environmental performance
In a pulverized coal-fired boiler of a large power plant, an oxygen analyzer is essential for combustion control. A pulverized coal-fired boiler is an industrial or utility boiler that generates thermal energy by burning pulverized coal (also known as powdered coal or coal dust).
STARDOM field control node (FCN) autonomous controllers allow both Modbus master and slave functions to run simultaneously.
In limestone-gypsum flue gas desulfurization systems, the consumption of a desulfurization agent (lime) is controlled using online pH analyzers.
Floating-point format calculations have enabled physical quantities (in engineering units) to be used in calculations.
The ammonia (NH3) gas is injected to remove the NOx and thus reduce the NOx concentration in the stack flue gas. With conventional NH3 analyzers that perform measurements indirectly, NH3 concentrations are obtained through a sampling system. Therefore, there are problems with the maintenance and running costs of the sampling system, and time delays in measurement. The TDLS8000 Laser Analyzer is the solution to all these problems.
A belt conveyor fire detection solution employing the DTSX distributed optical fiber temperature sensor can greatly reduce crises that can threaten a company's survival.
Industrial hydrogen fuel cells can be used to produce hydrogen and oxygen from distilled water as well as run in reverse to generate electricity. Fuel cells can also be used in conjunction with intermittent energy sources like solar or wind to provide regulated continuous energy output.
Seawater leak detection is the post-condensation water quality management processes. Damage to the ion exchange resin, which deionizes the supplied water, is also monitored during this process, and both of these applications are executed by a conductivity analyzer. (AN10D01P01-01E)
With industrial and economic development comes increasingly large and advanced power plants and factories. Nevertheless, we find many cases where the original cables, cable tunnels, and other components of the power infrastructure have languished under continuous operation.
Geothermal power plants create electricity from geothermal energy. These power plants are similar to other steam turbine station; however their heat source is that of the earth's core. The created steam is used to turn the turbine for the production of electricity. Technologies include Dry steam, Flash steam and Binary cycle power stations with Binary cycle being the most common geothermal plant in current production. In the process of geothermal power generation the facility needs to monitor various processes, as in this case steam line pressure sits in remote from control room's location.
Industrial Combustion sources such as thermal cracking furnaces and, process heaters play a critical role in the process industry.
Wet scrubbers are used in utilities, paper mills, and chemical plants to remove sulfur dioxide (SO2) and other pollutants from gas streams. Undesirable pollutants are removed by contacting the gases with an aqueous solution or slurry containing a sorbent. The most common sorbents are lime, Ca(OH)2, and limestone, CaCO3.
To defray energy costs, many industrial plants have their own boilers to generate steam in order to produce a portion of their energy needs. In addition to generating power, the steam may also be used directly in plant processes or indirectly via heat exchangers or steam jacketed vessels.
This paper introduces the ADMAG AXR 2-wire magnetic flomwmeter solution for chilled water application in air conditioning unit.
Power monitoring package SMARTDAC+ GM and UPM100 system measures and quantifies the electrical energy consumption for each assembly line.
One of the primary applications for high purity water is for boiler feed water. The measurement of pure water pH can be one of the quickest indicators of process contamination in the production or distribution of pure water. Effective chemical treatment of the feed water is vital in maintaining the useful operating life and minimizing maintenance costs of the boiler.
Industry:Power, Pharmaceutical, Common
Process automation end users are under more pressure than ever to do more with less. The current economic climate means that many automation capital projects are on hold. With capital budgets tighter than ever, users instead focus on operational budgets (where cost cutting is also a key concern), or on automation investments with a very rapid return on investment.
Yokogawa has come a long way in making its message clear to the world of process automation. Last year, the company embarked on a full-scale global marketing campaign to make customers aware of the company's focus on system reliability, security, dependability, and robustness. Dubbed "Vigilance", the campaign created a unified message for the company and greatly helped expand awareness of the Yokogawa brand and corporate philosophy.
This paper describes the tasks performed together with Soteica, by using an on-line model, to help achieve site wide energy costs minimization. A detailed model of steam, fuels, electric, boiler feed water and condensates system has been built, contemplating all the real constraints and degrees of freedom for their operation. The electric power system is also modelled as it interacts with the steam production and usage. Such a model is continually validated with live data. A continuous calculation of equipment efficiencies is done as part of the performance monitoring activity of the model that is running as a service.
From engineering to installation, commissioning, operations, and maintenance, FOUNDATION fieldbus offer significant cost reductions of 30 percent or more versus conventional analog systems. Many of these cost reductions come from the advanced functions that fieldbus offers versus analog technology.
The world of process automation is governed by procedures. While we like to refer to the process industries as being largely "continuous", this could not be further from the truth. Process manufacturing is constantly in flux.
The worlds of process automation and production management have been converging for some time. What once used to be islands of automation and production management functionality connected through highly proprietary integration schemes that were costly to maintain have developed into integrated platforms that provide seamless data exchange between the world of automation and the plant floor, the functions of production and operations management, and integration with business level systems.
This white paper provides an overview of how Yokogawa believes its customers can best prepare for and position themselves to benefit from IIoT-enabled technology and solutions and digitalization in general to emerge as the successful connected industrial enterprises of the future.
Yokogawa’s industrial automation (IA) product and service offerings, industry domain knowledge, and VigilantPlant approach – which emphasizes safe, secure, and uninterrupted operations -- provide a solid foundation for an Industrial Internet of Things that specifically addresses the requirements of process automation, particularly for the OT side of the equation. To be able to provide an equally solid foundation for the IT side, Yokogawa is partnering with Cisco Systems and other industry leaders.
In general, refineries exhibit a very good potential for real time monitoring and optimization using Visual MESA Energy Management System.
Based on our extensive experience, overall benefit in the range of 2% to 5% of the total energy cost can be achieved. Expected project payback is always less than one year.
Current trend for increasing mercury awareness throughout the public sector has caused the government to take action. Recently, the Environmental Protection Agency (EPA) has focused their efforts on controlling mercury levels produced in various coal fired power plants. Based on information from several case studies, the EPA developed the Mercury and Air Toxics Standards to cut back mercury emissions. The most popular technology utilized by coal plants to meet the new standards is a scrubber which cleans the off gas from the combustion process. ORP sensors can further monitor the effluent from these scrubbers to ensure optimal mercury emission levels are achieved. By closely monitoring the mercury concentrations in the effluent, plant managers will be able to easily confirm their plants are meeting the EPA's standards.
Industrial facilities where power and steam is produced (i.e., Cogeneration) exhibit a very good potential for real time monitoring and optimization using Visual MESA Energy Management System.
Based on our extensive experience, overall benefit in the range of 2% to 5% of the total energy cost can be achieved. Expected project payback is always less than one year.
Visual MESA was successfully applied to many industrial facilities worldwide, several of them operating steam and power generation networks of different complexity and capacity but all with energy cost savings.
Power plants concerned with lowering NOx emissions are making tremendous changes to accommodate EPA regulatory requirements. A substantial number of these changes include the expansion and upgrade of the plant combustion oxygen measurement equipment. There is a striking relationship between the number of NOx reductions projects and the sales quantity of insitu oxygen detectors.
The automation suppliers that will be successful in the long term will be those that effectively address application or industry specific problems for end users with a value proposition that cannot be ignored. These problems exist throughout the process industries today, and they won't be solved by simply offering a product, but through a combination of hardware, software, services, application expertise, and knowledge.
In today's dynamic industrial marketplace, the only constant is change. Raw material costs, energy costs, market demands, environmental and safety regulations, technology, and even the nature of the labor force itself are constantly changing, and not always in predictable directions.
Chemical plants, nuclear power plants, and large-scale engineering systems including railways and aircraft must be operated at least safely enough so as to not affect the surrounding environment. Furthermore, it is apparent that even only one accident or problem becomes the target of fierce criticism from the general public, as seen in the response of people to the accident of the Fukushima I Nuclear Power Plant of the Tokyo Electric Power Company and the problems with Boeing's 787 jetliners.
Recently, there is an increasing demand for operation and monitoring of all the various controllers distributed in the field on the same screens to improve plant operation efficiency. The purpose of the Unified Gateway Station (UGS) is to connect external controllers, such as the STARDOM's FCN/FCJ autonomous controllers and other vendors' controllers, to the CENTUM VP integrated production control system and to operate and monitor those external controllers on the Human Interface Station (HIS) screens, the operation and monitoring screens for the CENTUM VP.
We have developed the "Econo-Pilot" energy-saving system for water pumps, which reduces the power consumption of motors for water supply. In the energy-saving control field, the conventional method used is that of constant pressure control of the water supply with inverters.
The reverse osmosis (RO) membrane is in use today as a main component of water filtering equipment, because it has a fairly high performance record in removing various impurities such as salt from water. Especially in isolated islands and desert regions where there is no other choice but to utilize seawater as the only water resource, the RO membrane is an indispensable component of the RO module for water purification systems.
One solution packaged for production control systems today is a system comprising a PLC and SCADA (Supervisory Control and Data Acquisition) software that runs on a PC. An advantage of these systems is that they can be configured at considerably lower cost than systems that use dedicated devices as they use commercially available PCs.
The engineering phase holds the largest ratios in control system configuration in terms of both time and money, so improving engineering efficiency is one of the biggest issues when it comes to system integration. In the STARDOM, Application Portfolios (APPF) are devised to dramatically slash engineering costs and increase software reliability.
As the world's societies become more connected, market competition is becoming more ruthless and transactions are performed at ever increasing speeds. Deregulation has ignited global competition throughout the world. The proliferation of Information and Internet technologies have accelerated the growth of global competition, with life cycles for high tech products having lives measured in "dog years" (in each normal year they advance seven years).
We have developed the FCN (field control node) and FCJ (field control junction) autonomous controllers as the core of STARDOM, a solution that actualizes a network-based control system (NCS) Yokogawa proposes for increased production efficiency.
The power generation facility in a pulp and paper plant is comprised of units, each of which is composed of a boiler, a turbine, a generator, and auxiliary equipment, and these pieces of equipment were traditionally controlled on a unit/equipment basis. This paper presents an application of CENTUM, Yokogawa's distributed control system (DCS) that integrates the independent control systems of such power generation facilities to achieve labor saving through operations via CRT display and keyboard.
PC software as the front end of a recorder has become more and more important recently in the industrial measurement field as the personal computer becomes increasingly popular. In the past, we were making efforts to develop PC software for acquiring, viewing and setting data for a single recorder only.
YOKOGAWA has successively released the DARWIN series (DA100/DC100/DR130, 230, and 240) as network- connectable data acquisition instruments, the DAQSTATION DX series as key industrial recorders, the MobileCorder MV series as measurement recorders, and the DAQSTATION CX series, a new product that comes with a PIC control function in addition to having the functionality of the industrial recorders.
Yokogawa Electric Corporation released the μR and VR series of industrial recorders to meet user demands for monitoring and recording field data. Since then, the recorders have been in wide use in a variety of industries.
Yokogawa's industrial recorders have been widely used in order to monitor and record data acquired from the field. Concurrently, sensors in the field have been made increasingly intelligent and come to hold not just "data" but "information" of additional value provided by such functions as failure detection and statistical analysis.
Yokogawa has set a new standard in data acquisition by rolling out the DARWIN series in 1995. The concept behind DARWIN is to offer features that are normally conflicting such as data acquisition that is easy-to-use yet highly expandable, by combining a data acquisition engine, a measuring unit with display and output mechanisms.
Many signal conditioners have been used on the input and output sections of large-scale distributed control systems (DCSs) for isolation purposes. Recently personal computer-based instrumentation and measurement systems have become popular and brought with them significant functional enhancements.
Yokogawa Electric Corporation, one of the leading manufacturers of industrial recorders, put the DAQSTATION DX series stations on the market in 1999, which added information processing and transmission functions to conventional recorders.
Wireless technology has a long history, and it began around the time that James C. Maxwell theoretically predicted and then proved the existence of electromagnetic waves in the 1860s, and when Heinrich R. Hertz experimentally confirmed the actual existence of the electromagnetic wave in 1888.
The innovation of wireless technology increases the use of wireless communication in the industry. The introduction of wireless communication to plants, however, requires strict features such as robustness, real-time responsiveness, and low power consumption. This has restricted the use of wireless communication to limited applications such as data logging and device status monitoring that does not require strict real-time responsiveness and data arrival reliability in communication.
One of Yokogawa's corporate philosophies is to contribute to society through broad-ranging activities in the areas of measurement, control, and information. To achieve this philosophy in the control industry, Yokogawa launched CENTUM, the world's first distributed control system (DCS), in 1975.
The manufacturing industry has grown based on solid production technologies for creating quality products. However, the economic environment is changing dramatically, forcing manufacturing firms to face tough global competition; firms must ship the right products at the right time as the market requests.
CENTUM VP is a next-generation Integrated Production Control System which provides solutions to improve operation efficiency (Operational Excellence) based on Yokogawa's VigilantPlant concept. In the development of Integrated Production Control Systems, we have expanded the functions of the Human Machine Interface (HMI) maintaining the main essence of CENTUM series, regardless of the changes of platforms.
As controlled objects have become more complex, plant operation schemes more concentrated, and plant operators fewer in number, the degree of engineering for a distributed control system (DCS) has both multiplied and diversified. Despite this, systems are required to be configured in a shorter time while engineering results are required to be of higher quality.
Yokogawa Electric has been using Pair & Spare method as a reliability-enhancing technology for its line of distributed control systems (DCS) since the release of the CENTUM CS in 1993. As a result, the system has achieved an availability factor of seven 9's (99.99999%) for the record of operation to date.
As more fieldbus devices are made practicable, demand is increasing for a distributed control system (DCS) which integrates fieldbus devices in its engineering, operation, and monitoring environments. Conventionally, control has been implemented by the dual-redundant CPUs and control bus within a DCS; however, sufficient reliability must be ensured even when it is distributed over field networks.
The recent increase of devices enabled for a field network such as the FOUNDATION™ Fieldbus is phenomenal. This has been amplifying a requirement for distributed control systems (DCSs) to be capable of constituting a more pliant and efficient production control system by means of flexible connections to field networks in addition to traditional 4 to 20 mA signals.
In order to run 24 hours a day in large-scale plants, such as an oil-refinery or others, a distributed control station (DCS) requires high reliability. In the CENTUM DCS from Yokogawa Electric Corporation, high reliability of each device and a network (bus) connecting devices have been realized by using techniques such as a dual CPU, dual I/O, and a dual communication bus since sales began in 1975.
FCSs, the control stations in a CENTUM CS system, have already demonstrated that they are highly reliable, effective and maintainable. These advantages are the result of such features as the dual-redundant hardware configuration, the online modification of application data, and so on.
The environment surrounding process control systems has changed dramatically as the performance of personal computers improves and the Windows operating system advances, there has been a move towards the trend of open architecture. As we are already aware, in addition to the traditional high reliability level and the unique operability there has been an increase in demand for the interoperability of human- machine interfaces (HMI), which are responsible for the operation and monitoring of our distributed control system (DCS).
Report functions in process control are often positioned as part of the logger functions. However, plant operation data in a batch process should be not only logged regularly but also acquired and managed for each batch execution. The report function for logging plant operations in a batch process mainly comprises a function to print out plant operation data collected for each batch execution, and there are various approaches available to implement this function.
Since their conception in 1975, distributed control systems (hereinafter, referred to as DCSs) have been changed drastically in accordance with the rapid advancements in computer technology. In terms of hardware technology, the development of microprocessors, memory devices, and communication devices has been significant in regard to both quality and quantity.
Drastic changes in the economy of manufacturing industries, has led to increasing demand for plant operations to reduce personnel, improve efficiency, and increase the operation rate of facilities. On the other hand, for plants to operate safely, improvements in reliability and operational safety cannot be neglected.
In this day and age, just simply buying a personal computer, taking it home and turning it on will enable you to be taken to the world of Internet. In such an era, communication connection capability and prospects is increasing in importance. DCSs are no exception for concern.
To date, Yokogawa has focused on DCS (Distributed Control System) which control the entire power generation plant, including boilers, in the electric power industry. In contrast, turbomachinery control has been handled by turbine manufacturers, but as the electric power market has been active internationally, especially in China and India, in recent years, Yokogawa has been developing turbomachinery control systems to to further develop the electric power industry.
For a transfer system in a plant, such as a transfer between tanks in a brewery, the transfer of pellets in a pneumatic transport system, or the transfer of oil at an offsite location, it is necessary to monitor the open/close status of valves or the on/off status of motors or blowers in reference to the transfer pattern (a combination of the transfer source(s) and destination(s), route, etc.).
Recently, manufacturing industries are trying to slash the total cost of ownership (TCO). Batch processes are not exceptions. Until recently, in comparison to continuous processes, batch processes have generally not yet undergone systematization and standardization.
The manuals of control systems such as a DCS provide a vast amount of information depending on their multi-functionality and functional integration. A conventional large-scale control system our company offers comes with more than 10,000 pages of paper documents.
As industrial plant systems have increased in scale and their automatic control algorithms advanced, today's operators are required to have more advanced skills and knowledge of theplant systems and to learn the actions to be taken in response to any possible situations including emergencies.
To improve efficiency and quality in the DCS application coding and inspection phases for an entire CENTUM CS system, engineering tools have been developed, along with the training required to operate these tools. In consideration of the time needed for development, the need for adequate operability, the basis of standard CS software architecture, and the use of freeware (e.g., Perl2 and Tcl/Tk3), we began development of these engineering tools with the objectives to reduce development costs and increase efficiency.
A fieldbus is a bidirectional, multidrop, digital communication system developed to replace the conventional 4-20 mA communication lines that connect intelligent field devices with a control system. Fieldbus is continually reviewed in an effort to standardize the fieldbus specifications to comply with the specifications of the IEC and ISA.1
The development of communications technologies has formed a system structure known as the communication network. This network has not only established itself in the industrial world but also in the general household. The recent spread of technologies such as the Internet has been quite spectacular.
The first stage in creating next-generation production control system that achieves innovative plant operation is providing "Visualized operation". "Visualized operation" for the customer means that he can reliably access and visualize plant data regardless of plant location and time.
A communication system for connecting stations in the system plays an important role in a distributed control system (DCS). The communication system determines the superiority or inferiority of the entire control system. In DCS communication as represented by CENTUM, a token-passing system and dual bus have been developed.
It goes without saying that the reduction of the total cost of ownership (TCO) for various facilities and equipment is an important objective for most enterprises, and distributed control systems (DCSs) are no exception.
Progress in digital signal processing and network technologies has enabled advanced functions which cannot be achieved by traditional field devices with 4-20 mA signal, to be implemented on field devices. Standardization of international fieldbus specifications, notably the FOUNDATION™ Fieldbus, has enabled users to build optimum field networks comprised of freely chosen field devices from various device vendors.
Differential pressure transmitters, which serve as the core of field instrumentation, are widely used to measure the flow rate, pressure and density of liquids, gases and steam, as well as the level of liquid in a tank.
Field instruments are expected to be equipped with diagnostic functions to predict abnormal process conditions, and are also expected to expand these functions. The ability to extract diagnostic information for prediction and prevention from various physical process quantities measured by devices and make it available allows the user to reduce non-essential and non-urgent maintenance and thus cut maintenance costs.
Safe plant operation has long been pursued in all industries. Specifically, in the process automation industry which involves many hazardous elements, safety measures including explosion-protected systems have been adopted based on numerous tragic experiences.
When evaluating mass flow rates using a primary device such as an orifice or nozzle in a differential pressure flow meter in order to make fluid density compensations, the upstream pressure (static pressure) and fluid temperature are measured in addition to the output of a regular differential pressure transmitter.
Since the release of the DPharp EJ series in 1991 and the DPharp EJA series in 1994, nearly 1.2 million of these transmitters have been operating all over the world. Recently, we have also developed the EJX series of even more compact, lightweight and advanced transmitters with multi- sensing capabilities built using silicon resonant sensor technology.
In recent years, more field wireless devices have been used in hazardous areas. Meanwhile, in plants that are usually recognized as hazardous areas, there are numerous metallic tanks and pipes that easily shield or reflect radio waves, as discussed later, thus resulting in a poor environment for wireless communication.
Combustion furnaces such as heating furnaces and boilers in plants include various sizes and types, and serve as energy sources, that is, they are cores in all production activities. Because a large amount of fuel such as gas or fuel oil is consumed in plants, their combustion efficiency directly affects the performance and running cost of the plants.
A laser gas analyzer employing the tunable diode laser absorption spectroscopy (TDLAS) method has a feature capable of measuring the concentration of the sample gas with high selectivity for gas components and without contact only by irradiating the gas sample with light from a tunable diode laser. Thus fast and accurate in-situ measurements can be performed in process lines under various measurement conditions.
In 1988, Yokogawa launched the ADMAG series of magnetic flow meters with increased resistance to fluid noise and zero stability, employing dual frequency excitation which was developed based on its long-cultivated technology for flow measurement. Since then, the ADMAG family has augmented its application range with such models as explosion-proof and integral types, and a capacitance type.
For large scale geographically dispersed projects, there may be a hierarchy of individual Process Automation systems, which in turn are each responsible for a specific region, and are managed by a higher level system. Engineering of systems on this scale is a huge challenge, because each individual system has its own database and its own configuration.
The Coriolis flow meter has many features such as direct measurement of mass flow and measurement of fluid density, which other flow meters do not support. Therefore, since being introduced for practical use in the late 1970s, its market has rapidly expanded in many industries such as oil, chemicals, and foods.
The rapid evolution of information technology (IT) has made possible the transmission of a wide range of information in a short period of time, resulting in the transformation of society in aspects such as logistics and business styles. During this transformation, quick assessment of the circumstances and prompt actions were also required in the production lines, making real-time collection of field information indispensable.
Vortex flow meters utilize a fluid phenomenon in which frequencies of Karman vortex streets released from a shedder bar inserted in a flow are proportional to flow velocities.
Vortex flow meters have been appreciated by users as volume flow meters, which can, in principle, be applied to any flow measurement of liquid, gas, or steam. Volume flow measurement is enough for substances with small variations in density such as liquid.
The environment surrounding the process plant industry has changed dramatically because of the recent economic changes, deregulation, and increasingly fierce competition among global companies. Users are strongly requesting instrumentation equipment vendors to reduce total cost throughout the life cycle and help improve the efficiency of plant operation.
Yokogawa has been offering the EXA200 series two- wire liquid analyzer for processes since 1990. This analyzer has been used in various fields including the quality control of raw materials in process plants in the electric power and petrochemical industries, reaction management of products, quality control in waste water facilities, and quality monitoring of river water and tap water.
There has been increasing demand for cost reductions and lower-priced products in the manufacturing industry, and maintaining cost competitiveness and achieving optimum costs have become necessary for the survival of manufacturers. This calls for minimizing TCO (Total Cost of Ownership) over the whole life cycle of plants and maximizing TVO (Total Value of Ownership).
Process automation involves both operation and maintenance. Plant operation and monitoring are mainly conducted by a control system such as CENTUM, while equipment maintenance is handled by Plant Asset Management (PAM) such as Plant Resource Manager (PRM).
As compared to Distributed Control Systems (DCS) such as CENTUM VP that monitors the operations of the overall plant, PRM is a type of Plant Asset Management (PAM) software package that primarily focuses on the maintenance of devices and instruments.
Asset Excellence (AE) provides a set of solutions for maintaining a plant in good condition at reasonable cost to ensure that it works as a production infrastructure. To reduce maintenance costs without causing a risk to production, it is necessary to change from breakdown maintenance to predictive or preventive maintenance.
Improved plant operation efficiency and reduced maintenance costs based on appropriate predictive maintenance are the common objectives that need to be achieved in every manufacturing domain. Exaquantum is positioned above the Process Control System (PCS) layer and gathers and stores huge volumes of process and laboratory data over long terms.
There is growing recognition of the importance of preventing serious accidents in the process control field in view of the potential scale of impact on society. The IEC 61508 and IEC 61511 international standards call for the reduction of risk using safety instrumented systems (SIS) as well as the configuration of multiple protective layers in a process control system in order to prevent major accidents.
There are already safety systems on the market that have achieved safety integrity level SIL3 of the functional safety standard, IEC61508. However, most of them have achieved SIL3 by conversion of modules into dual-redundant or triplex form.
In recent years it has become increasingly common for plants to be provided not only with the control layer of a production control system (DCS, etc.), but also with the protection layer of a safety instrumented system (SIS) to reduce the risk of industrial accidents. The safety instrumented system is indispensable for avoiding risks to a plant failure.
The CENTUM CS 3000, a reliable distributed production control system, has been introduced worldwide with the objective of operating plants efficiently 24 hours a day, every day. The CS 3000 handles abnormal conditions in a plant appropriately and minimizes the chance of them developing into faults.
Yokogawa Electric Corporation promotes the standardization of FOUNDATION™ fieldbus as the communication foundation supporting Asset Excellence for VigilantPlant, which is an approach aimed at the advancement of plant instruments and equipment. With the recent dramatic advancement of fieldbus technologies, information processing technologies, and network speed, it has become possible to process various kinds of information inside the field sensors and transmit the results to the distributed control system (DCS) and host computer.
In plant sites, there are various places such as those affording an unobstructed view like tank yards, and others surrounded by metal pipes and equipment obstructing the view (hereafter referred to "pipe jungles"), often seen in oil refinery and chemical on-site plants. The frequency band of radio waves used for field wireless communication is 2.4 GHz, which has high straightness and its ability to go around things can hardly be expected.
The changes in social environment, such as globalization of enterprise activities, depletion of natural resources, and eco-oriented movement will affect the structure of mass production. Control systems must be prepared with flexibility and scalability in both size and function to adjust to the changes.
The process industry in Japan faces increasingly critical environmental and safety issues. Additionally, in Japan, many skilled engineers with years of experience will be retiring in 2007. Although the process industries such as petroleum, petrochemical, steel and paper, etc., are highly automated, human skill is still required in an abnormal situation or for a critical production change.
In 2005, Yokogawa announced "VigilantPlant" as a concept to ward the realization of a type of plant operation that is considered ideal by our customers.
The purpose of blending in a petroleum refinery is to mix semi-finished products that have been rectified during various refining processes so as to manufacture a product that meets specification.
As a company that has strong relationship with nature and provides products using nature's blessings, Mercian Corporation is committed to the environment. Its environmental philosophy is "Mercian thanks nature's blessings and capability that sustain life, and seeks to balance environmental preservation with creating an affluent society."
Intelligent field instruments and process analyzers accumulate diverse field information including process values and diagnostic results. This data needs to be sent to upper systems such as distributed control systems (DCS) via digital communications such as FOUNDATION Fieldbus and analyzer buses, or hybrid communications such as HART and Brain, and visualized to enable the customer to utilize them for plant operations and maintenance.
Due to the rising energy demand in emerging countries in recent years, the amount of oil and gas production has been increasing, thus investment in the development of new oil and gas fields and replacement of old facilities has been booming.
Recipe management software refers to the computer software used to manage product names and their corresponding recipes and set the recipe data in the control system in order to control the operations of a plant in which multiple materials are blended to manufacture a number of different products.
Many field devices are now being connected to process control systems through fieldbus communication. These field devices have intelligence, and so many settings and adjustments can be made through fieldbus communication.
The development of the CENTUM CS 1000 distributed control system for small- and medium-scale plants was based on two basic design principles: 1) to have the same architecture as the CENTUM CS and 2) with the objective of becoming a global product.
As for a controller used in a distributed control system (DCS) shown in Figure 1, covering as many applications as possible with a single controller will bring cost reduction effects such as easy engineering and a small controller installation area. Therefore, the controller is required to process large amounts of data more quickly.
More than ten years have passed since the first digitized field devices were introduced. These support either a hybrid communication protocol such as HART or a full digital communication protocol such as FOUNDATION Fieldbus.
The specifications of the ISA100.11a wireless communication standard of the International Society of Automation (ISA) for industrial automation were published, and companies are developing products based on the standard. The ISA100.11a has many features such as high reliability including redundancy, network scalability, and support for various protocols for industrial automation.
For safe plant operations, it is critical to correctly understand the conditions encountered by operators inside the plants. In relation to this topic, human cognition has been studied in various fields such as human factors and ergonomics.
The recent variety of industrial and railway accidents happening right before our very eyes make us painfully aware that "safety" must be put first and foremost. "Safety first" is a concept accepted by everyone and there is no room for disagreement. However, the author feels that, in some cases, the concrete objectives of "safety first" are not actually clear, and the grasp of the hazards is insufficient.
The business world surrounding the manufacturing industry is undergoing rapid and drastic changes. Achieving production activities that can respond swiftly to such environmental changes has become an urgent task.
As field instrumentation devices become increasingly digitized and computerized, interactive and remote access to a large quantity of field information becomes possible. This will increase the efficiency of plant equipment maintenance by reducing labor requirements in field patrol work for example.
The requirements for water supply and sewage services are becoming increasingly strict, such as consolidation of facilities, operational efficiency, lower cost, and information transparency due to stagnant demand. There is also demand for greater use of information technologies (IT), encouraged by the government's e-Japan strategy.
After having undergone several improvements, magnetic flow meters have become highly accurate and reliable and are widely used in the industrial instrument field today. Magnetic flow meters consist of a detector and a converter, with the principle of the detector adopting Faraday's electromagnetic induction law.
The introduction of wireless technologies into plants is anticipated as one of the measures for implementing field digital solutions not only to reduce cable wiring costs but also to improve plant wide safety/stable operations, operating efficiency, and so on.
Yokogawa proposed the VigilantPlant concept as an ideal plant that achieves fully optimized operation where all the necessary information is given to all the operators involved in the plant operation. In VigilantPlant, operators are able to quickly respond to changes in the external environment while the production activities run without any interruption.
Industrial automation (IA) systems and products, which utilize measurement, control and information technologies, are used across the world as fundamental infrastructure for achieving safe, stable and highly efficient plant operation. In order to keep the systems and products effective throughout the plant lifecycle, customers need to periodically check their effectiveness and take prompt action if any problem is identified.
Global market pressures are causing businesses world wide to strive to lower manufacturing costs and to become more agile companies in order to quickly respond to changes in market demands and to fend off competitive threats. Yokogawa's customers in all industries and markets are responding to this pressure by working to more closely integrate their plant manufacturing systems with their enterprise wide business systems in a seamless manner.
In Japanese industries which grew rapidly until the early 1990's, solid production techniques for creating high-quality products supported the development of manufacturing industries. However, the economic environment has been changing rapidly and tough global competition has become unavoidable. Particularly, the manufacturing industry must adapt not only to changes in economic environments but also to changes in social conditions such as emphasis on health, safety, and environment (so called HSE).
Recently, standardization of procedural automation of manual operations has been promoted mainly by the International Society of Automation (ISA), and the functional requirements necessary for automation are being studied by the ISA106 committee in the US.
For a coal fired power generation plant (hereafter referred to as "BTG facilities," in which "BTG" stands for boiler, steam turbine, and generator) supplying power to a large-scale production plant, the CO2 emissions from such facilities are a critical issue today.
Environment and safety are major topics on a global scale in recent times. As symbolized by the effectuation of the Kyoto Protocol, an interest in preserving the environment is growing worldwide, and there is also a tendency to criticize more severely, occurrences of industrial accidents that are accompanied by environmental contamination or which may cause damage, etc., to residents in the surrounding areas.
Conventional safety instrumented system (SIS) is typically installed separated from a distributed control system (DCS) to eliminate interference from the DCS and assure safety. However, users increasingly wish to integrate SIS with DCS while maintaining the safety of safety controllers.
Yokogawa's ProSafe-RS safety instrumented system is used for many applications as a system conforming to the safety integrity level (SIL) 3 defined in the IEC61508 international functional safety standard. To deal with temperature inputs, systems were conventionally configured using signal conditioners.
In recent years, expectations for control systems using wireless communications have been increasing in the process control market. This is because these systems do not require power and communication wiring for field instruments, enabling reduced initial and maintenance costs, and easy installation.
Yokogawa has been leading the process automation industries as one of the pioneers in field digital technologies represented by the FOUNDATION fieldbus™ and Field Device Tool/Device Type Manager (FDT/DTM).
With the recent rapid advancement of technology, user equipment has become more and more complicated, diversified and faster. This has been imposing an increase in engineering costs and increasingly many users require devices facilitating customization and the reuse of past resources (legacies).
Latest field devices have not only various self-diagnosis functions but also process-interface-diagnosis functions such as valve diagnosis of valve positioners and impulse line blockage detection of differential pressure transmitters. The YVP valve positioner can easily perform initial tuning, parameter adjustment, trend monitoring, and valve diagnosis, by using the ValveNavi YVP management software.
Due to emerging competitors from the rapidly growing countries such as India and China and the global economic downturn triggered by the Lehman shock, many companies in the process industries are struggling to survive the severe global competition.
The operation and monitoring functions of a plant control system are important means of understanding the condition of the plant and how it operates. Traditionally, user needs for the system focused on such features as increased operability and durability. As a result, these functions were developed for a dedicated machine in the form of dedicated human-machine interface software.
Honeywell and Yokogawa have both been producing Distributed Control System (DCS) platforms for decades, and both are very active in this area. In 1975, Honeywell introduced its TDC2000 platform and Yokogawa brought out CENTUM. These two competing systems emerged from a similar place, oil refining and petrochemical industries, so they started out with similar basic concepts and use cases in mind.
下载
认证信息
- EU_UK Declaration of Conformity FU20 2022-11-14 (170 KB)
- EU_UK Declaration of Conformity PR10 2022-11-14 (140 KB)
- EU_UK Declaration of Conformity SM23 2022-11-14 (121 KB)
- EU_UK Declaration of Conformity SC29 2022-11-14 (146 KB)
- EU_UK Declaration of Conformity SC21 2022-11-14 (146 KB)
- EU_UK Declaration of conformity SX42 2022-11-14 (152 KB)
- EU_UK Declaration of conformity SC42 2022-11-14 (158 KB)
视频
The YSS1000 setting software (hereinafter referred to as the YSS1000) is package software to configure the functions of the YS1000 series (hereinafter referred to as the YS1000) devices. Writing and reading of parameters and user programs of the YS1000, and PID tuning and monitoring of user programs can be performed through the use of communication.
DTSX has been increasingly used in variety of applications such as fire detection, leak detection and preventative maintenance.
As a gateway to further expand Yokogawa's messaging as a One-stop Solution Business, Yokogawa has partnered up with INCIT, to introduce the S.I.R.I. framework.
新闻
-
新闻 2017年11月29日 横河赢得西巴尔干地区初个烟气脱硫控制系统订单
- 安装在波斯尼亚和黑塞哥维那的燃煤发电厂 -
-
新闻 2020年3月26日 横河电机赢得土库曼斯坦燃气电厂控制系统和现场仪表的订单
- 确保面向市场的稳定电力供应 -
-
新闻 2020年11月27日 横河电机(中国)有限公司发布ADMAG SF 电磁流量计
-计划于2020年12月21日起接受订单-
-
新闻 2023年2月20日 横河电机与Radial Software Group建立合作伙伴关系,提供AI驱动的Viewport软件
- 为客户提供技术数据的单一视图 -
-
新闻 2024年10月30日 横河电机与Sensyn Robotics就无人机相关服务建立销售合作伙伴关系
- 对工厂和其他基础设施进行安全高效的检查 -
想要了解更多的信息,技术&解决方案?
联系我们