挑战
客户面临的挑战
化学工业的专业化程度很高,化工厂生产中从原料产生的中间产品,会被其他工厂用来生产其他产品。每个化工企业都需要仔细考虑在激烈的市场竞争中如何定位。
我们的解决方案
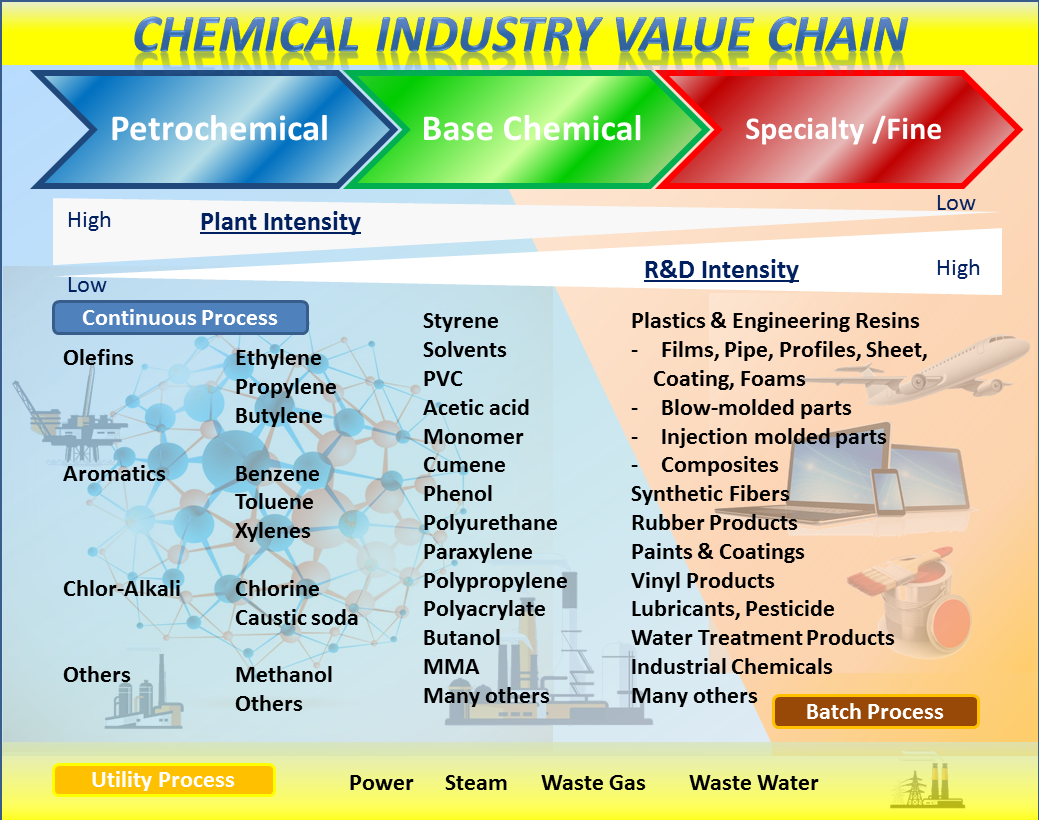
基础化工的生产通常是一个连续的过程,需要高度可靠和稳定的控制系统。CENTUM VP综合生产控制系统是非常符合要求的解决方案,可根据工艺要求创建舒适的操作环境,并在稳定的过程控制下提供舒适的驱动环境。Exapilot在线导航工具为操作员提供了强大的支持,能可靠执行很多非常规操作,例如停车和启动等。
使能技术

生产控制系统:CENTUM VP
统一的综合控制和安全系统(ICSS)数据库简化了工程设计、图形、报警窗口和系统状态屏幕,使它们都具有相同的外观和感觉,操作也更加简便。
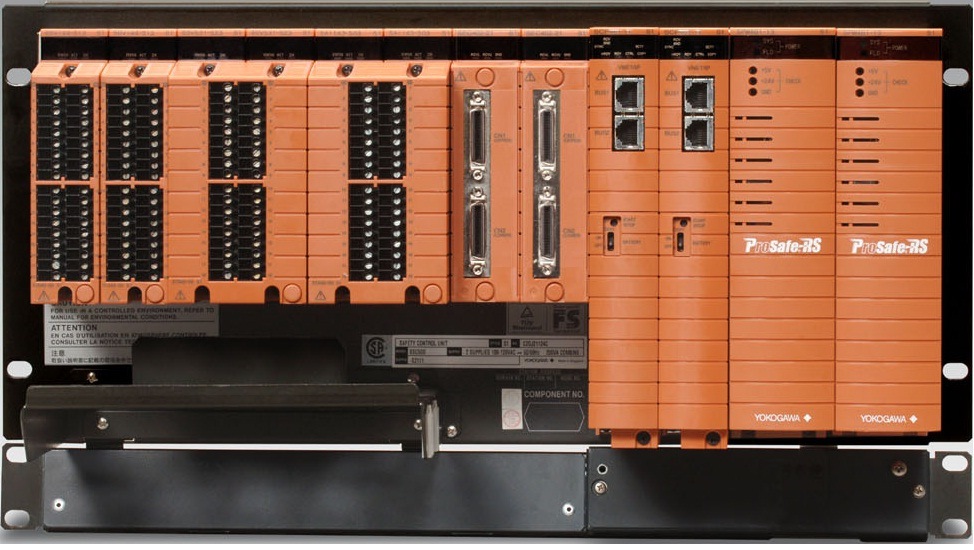
安全仪表系统:Prosafe-RS
横河提供从固态和硬接线类型到DCS-SIS集成类型的安全仪表系统的产品线,涵盖化工行业的安全完整性等级(SIL 1至4)。
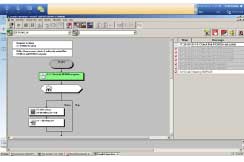
提高操作效率:Exapilot
Exapilot是一种在线导航工具,可指导操作员逐步完成工厂操作程序。
使用Exapilot按照规范格式创建标准操作程序(SOP)。通过减少或消除人为错误来提高效率并降低业主总成本。
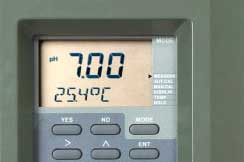
分析
高度响应分析系统有助于准确测量产品/中间产品特性,帮助石化公司满足日趋严格的质量控制和环境法规。
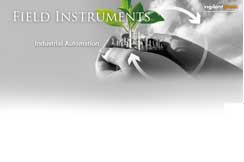
现场仪表
“安装和忘记”的数字现场仪表可提供稳定、准确的过程测量,安装成本低、零维护,并有智能自诊断功能。横河电机将FOUNDATION fieldbus™设备推向市场,除ISA100 11a的无线通信产品之外,还开发了一系列完整的兼容FOUNDATION fieldbus™、HART和Profibus协议的仪表。
参考
Caustic soda and hydrochloric acid, produced in electrolyzer plants, are fundamental materials used in varieties of industries; chemicals, pharmaceuticals, petrol-chemicals, pulp and papers, etc. Profit is the result of the effective production with minimized running / maintenance cost. Proper control of the process brings you stabilized quality of products with the vast operational profit.
If a sensor is not operating, the manufacturer cannot detect moisture in the chlorine and must stop the process. Unfortunately, sensors can deteriorate and deliver inaccurate measurements due to contact with the process.
Many different types of gases are consumed in industries as varied as chemicals, food & beverages, and medical. These gases are normally delivered in liquid form by trucks and dispensed at the customer site. Although the flow volume of cryogenic liquefied gas is used for billing purposes, it is not easy to accurately measure this because the gas is always at saturation temperatures.
Storage tanks are used in a variety of industries ranging from holding crude oil to holding feedstock for vinyl chloride monomer (VCM).
The ammonia (NH3) gas is injected to remove the NOx and thus reduce the NOx concentration in the stack flue gas. With conventional NH3 analyzers that perform measurements indirectly, NH3 concentrations are obtained through a sampling system. Therefore, there are problems with the maintenance and running costs of the sampling system, and time delays in measurement. The TDLS8000 Laser Analyzer is the solution to all these problems.
This paper discusses real industrial examples in which the sitewide utilities system of refinery and petrochemical Sites are optimized with a real time, on line, industrially proven software. Experiences gained during more than 20 years of industrial projects deployed worldwide are commented (Refs. 1 to 10 are related to some recent projects). Main project steps are explained and critical details to be taken into account to assure successful use and proper technology transfer are presented. Specific case studies will be discussed in the paper.
Big and complex industrial facilities like Refineries and Petrochemicals are becoming increasingly aware that power systems need to be optimally managed because any energy reduction that Operations accomplish in the producing Units could eventually be wasted if the overall power system cost is not properly managed. However, process engineers always attempted to develop some kind of tools, many times spreadsheet based, to improve the way utilities systems were operated. The main drawback of the earlier attempts was the lack of data: engineers spent the whole day at phone or visiting the control rooms to gather information from the Distributed Control System (DCS) data historian, process it at the spreadsheet and produce recommendations that, when ready to be applied, were outdated and not any more applicable.
The energy systems, the steps for the implementation of Visual MESA and several features of the model are described in this article, with a focus on the use of the software for the calculation of energy-related KPIs. The EMS implementation project is discussed and the main conclusions relative to the reduction in operating costs are also presented.
Experiences gained during more than 20 years of industrial projects deployed worldwide are commented. Main project steps are explained and critical details to be taken into account to assure successful use and proper technology transfer are presented. Specific case studies will be discussed in the paper. Open loop vs Closed loop implementation is also presented.
Rohm and Haas Company is one of the world's largest manufacturers of specialty materials, including adhesives, sealants, coatings, monomers, electronic materials, inorganic and specialty solutions, and ion exchange resins. Founded in 1909 by two German entrepreneurs, Rohm and Haas has grown to approximately $6 billion in annual revenues.
This paper shows how to improve distillation operations by focusing on procedure automation. It will review the importance of using procedures in distillation operations and highlights the collaboration work underway between Fractionation Research Inc. (FRI) and Yokogawa Corporation to improve procedural operations.
The worlds of process automation and production management have been converging for some time. What once used to be islands of automation and production management functionality connected through highly proprietary integration schemes that were costly to maintain have developed into integrated platforms that provide seamless data exchange between the world of automation and the plant floor, the functions of production and operations management, and integration with business level systems.
Migration of a refinery's DCS provided an opportunity to reconfigure and consolidate the control rooms and operational management system.
July 2011
Process plants are run according to operational procedures. These procedures consist of a set of tasks that are executed in a consistent manner to achieve a specific objective, such as starting up, shutting down or transitioning a unit as part of making a product.
September 2008
Yokogawa is helping a large chemicals site in China manage product transfer by road, ship and pipeline.
The Wyoming Trona Ore Mine and Refinery upgrade from Yokogawa Centum CS3000 to CENTUM VP-R5 involved two domains, 21 RIO and FIO field control stations, 17 operator stations, 6 engineering stations and 8 different plant servers
CONTROL, January 2013
Standard Automation Methodology Improves Operations and Prevents Incidents by Enabling the Sharing of Best Practices Among Operators.
ARC believes that by implementing procedural automation, many process plants can minimize variability to help ensure smooth, efficient, and safe state transitions.
下载
宣传彩页
- Deliver Excellence and Create Success - To be the Leader in the Chemical Industry - (4.9 MB)
- Success Story Collection Chemical (Base Chemical, Fertilizer, Petrochemical) (7.6 MB)
- 离子膜电解装置应用仪表及解决方案 (2.9 MB)
- Solutions for the Chemical Operations Executive (2.0 MB)
- Differential Pressure Level Solutions (8.0 MB)
想要了解更多的信息,技术&解决方案?
联系我们