Executive Summary
Seibu Oil Company Limited, Yamaguchi, Japan
Seibu Oil Company Limited, a subsidiary of Showa Shell Sekiyu K.K., operates a 120,000 barrel per day oil refinery in Sanyo Onoda that supplies a wide range of environmentally friendly petroleum products to Showa Shell Sekiyu and other companies in the region. The refinery has secondary processing facilities that include vacuum distillation, diesel hydro desulfurization, continuous fluid catalytic cracking, and naphtha hydrotreating units, etc.
To improve the efficiency of this refinery’s offsite operations, Seibu Oil decided to replace its Yokogawa CENTUM-XL distributed control system and other legacy computer systems with Yokogawa CENTUM VP production control and oil movement system (OMS). To minimize the impact on refinery operations, Yokogawa was given just 48 hours to complete the switchover to the new systems and get them operational again. Working closely with engineers from Shinkawa Electric, a Yokogawa distributor, as well as engineers from Seibu Oil who were familiar with the workings of the existing systems, Yokogawa prepared a detailed plan and successfully carried out the upgrade of these systems.
The Challenges and the Solutions
The refinery's off-site systems had been in use for 25 years, and needed to be replaced to improve efficiency. An added concern was that the refinery’s most experienced operators were up for retirement within the next few years and needed to pass on their knowledge to their younger colleagues, yet their heavy workloads often made this difficult.
Careful planning for a 48 hour system switchover
Seibu Oil’s management was very concerned about the impact that any long interruption in the deliveries of their petroleum products would have on their customers, and gave Yokogawa just a 48 hour shutdown period to complete the switchover to the new systems. One year in advance, Yokogawa began discussing this with Seibu Oil and Shinkawa Electric’s engineers. Taking a team approach, they discussed the feasibility of carrying out all the installation work, communication testing, and loop testing in advance of the system switchover while reduce risking and ensuring that quality work was performed, and successfully created a concrete plan for this difficult project.
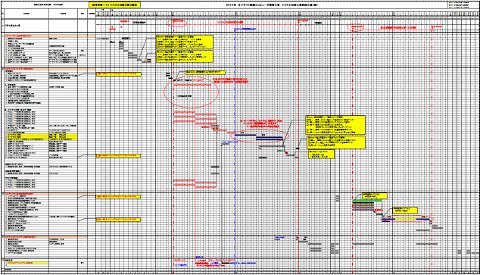
A very detailed schedule
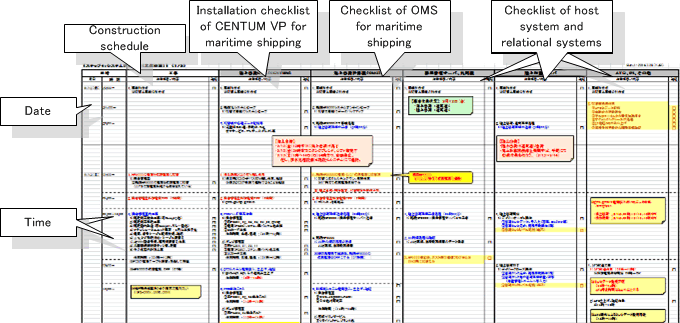
Step-by-step work checklist
New CENTUM VP human interface stations (HIS) with large displays were installed to the side of the existing operator consoles in the control room. Field control stations (FCS) and OMS servers were installed next to the existing systems in the computer room.
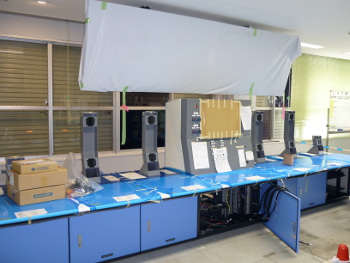
Control room during the construction phase
While the existing systems continued to control operations, engineers carried out system start-up tests and tested communications between the new systems and the host computer. All of this work was finished before the switchover.
On the appointed day, the existing systems were shut down and all signal cables were disconnected from the old FCS cabinet and reconnected to the new CENTUM VP FCS. Working around the clock, engineers started up the new system, conducted comprehensive tests of approximately 1,000 control loops, and performed a final test of all systems, including the host system. The switchover was successfully completed on schedule, within the 48 hour shutdown period, and the new off-site systems operated smoothly, with no complications. With the subsequent removal of the old systems hardware, the project was completed.
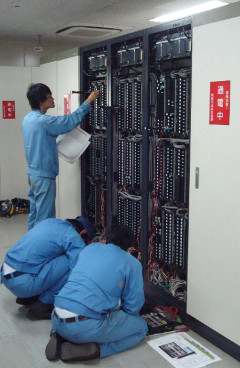
Loop testing and commissioning
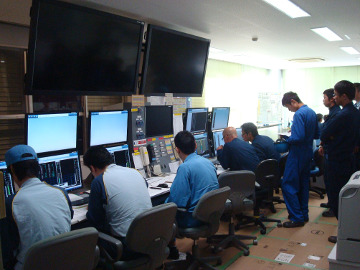
Loop testing and commissioning
Improved oil movement management
Seibu Oil chose to replace its legacy oil movement system with a Yokogawa OMS because Yokogawa is a proven supplier of comprehensive oil movement solutions, with over 30 years’ experience in this field.
There are approximately 3,500 oil movement paths at this refinery that connect loading and unloading facilities and the tank complex, and with the legacy system all the information on these paths was managed using paper documents. Tapping the knowledge of the refinery’s veteran operators, Yokogawa began preparations for configuring the OMS by digitizing the complicated path information to make a path list. A path list is an essential item for the construction of an oil management system that contains information on valves, pumps, and all other equipment at the off-site location.
Through improved visualization of path information and expert know-how, the new OMS made it possible for even relatively inexperienced personnel to control the operation of equipment, thus helping to prevent errors that result in problems such as product contamination and giveaway. In addition to improving product quality, the use of the path list improved the efficiency of the path change procedure and enabled improvements in device maintenance.
Control room design for HSE and smooth communication
The off-site control room was redesigned by Yokogawa's industrial design team, with Yokogawa designers visiting the refinery to consult with the customer and make a plan that satisfied their requirements. The new control room was designed with health, safety and environment (HSE) requirements in mind. The number of fluorescent tubes was reduced 35 percent without a decrease in luminance, and the lights were positioned to illuminate the walls, thus reducing operator eyestrain. And the vents for the air conditioning system were positioned so that operators would not have to sit directly under them.
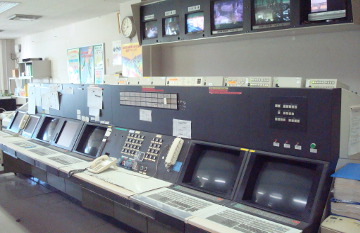
Pre-revamp control room with CENTUM-XL
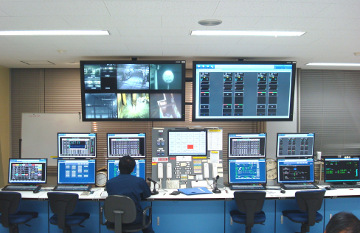
New control room with CENTUM VP
The designers divided the control room into operation and communication zones, with the communication zone being a place where veteran and younger operators can sit down together before a large HIS display to exchange information about current processes and give/receive advice on how to correctly carry out specific operations.

Communication zone with large display
Control room created by the industrial design team
(Cool, calm colors in the operation zone, warm colors in the communication zone)
Customer Satisfaction
Comments by Hidemichi Kasai, project leader:
"Securely and reliably replacing these systems was a top priority for us. In order to fulfill our responsibilities as a refiner, we must prevent shipment delays and emergency shutdowns. It is absolutely essential to prevent accidents. We wanted to be sure that we could complete the switchover within a 48 hour period. We selected Yokogawa because they are familiar with both our business and our systems.
Mr. Kasai
The time was right for this upgrade, with highly skilled veteran operators due to retire over the next 1 to 2 years. To work on this upgrade project, we assigned teams from each section that were made up of a veteran operator and a younger operator. The veterans had all worked on our last upgrade project and had advanced know-how. Thanks to the fusion of this expertise with Yokogawa’s rich experience in upgrading off-site systems, we were able to bring this difficult project to a successful conclusion, and our younger personnel were able to gain significant new knowledge and experience.
We accepted Yokogawa’s proposal for the control room redesign and are pleased that there is sufficient storage space so that we can keep everything in a set location. Everything, including manuals, is stowed away in convenient locations for immediate access, and this helps us keep this refinery operating safely and efficiently. At the start of each workday and at shift handovers, operators gather in the communication zone and use the large display to exchange information on the tasks that lie ahead. The large screen is also utilized for operator training. Operators are really satisfied with this clean new control room."
Hideo Yamamoto, Yokogawa’s project manager:
"One of the factors for the success was the close communication with Seibu Oil and Shinkawa Electric. We had meetings again and again to carefully plan everything. Thanks to that we were able to synchronize all of our project activities. I'm also glad that this project could help our customer develop their younger personnel. Our customer’s assistance in creating and verifying the path list, carrying out all migration tasks, and coordinating all these activities within their organization also contributed to this project’s success. Thanks to our customer, we were able to complete this upgrade without any incidents."
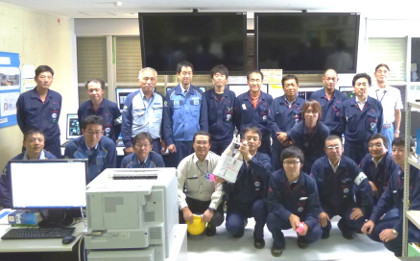
Celebrating completion of the project
Отрасли
-
Нефтепереработка
На постоянно меняющемся рынке нефтеперерабатывающие заводы рассматриваются не только как единицы переработки сырой нефти, но и как центры прибыли. В то же время существует острое осознание необходимости обеспечения безопасности на таких объектах. Комплексное производственное решение, которое включает в себя производственное и календарное планирование, управление и контроль, необходимо для достижения долгосрочных целей по прибыльности, эффективности и защите окружающей среды. Обладая многолетним опытом в области автоматизации, Yokogawa может предложить вам доступные комплексные решения для повышения работоспособности и более чистого мира.
Related Products & Solutions
-
CENTUM VP
CENTUM VP имеет простую и общую архитектуру, состоящую из человеко-машинных интерфейсов, полевых станций управления и сети управления.
-
Миграция / замена РСУ
Переход к «неустаревающей» системе с использованием сервисов по миграции РСУ, разработанных для того, чтобы помочь заказчику выполнять постоянно меняющиеся требования со стороны технологических процессов.
-
Планирование и выполнение переключения
Благодаря тщательному планированию и выполнению Yokogawa может оказать вам помощь в достижении безопасного и экономически выгодного процесса миграции для системы с горячим или холодным переключением, обеспечивая создание добавленной ценности