In the agitation process of a chemical plant, raw materials (liquids and powders) supplied by pumps are mixed using an agitator to produce products through chemical reactions. If the supply pump deteriorates and the material supply is unstable, unexpected changes may occur in the production recipe, impacting product quality. Additionally, if the supply of raw materials is stopped, the agitator to run idle, potentially shut-down production due to damage to the motor bearings or couplings.
By appropriately monitoring the condition of supply pumps, deterioration and breakdowns can be prevented, however, it is difficult to monitor a large number of supply pumps deployed in a wide plant with the operator rounds.
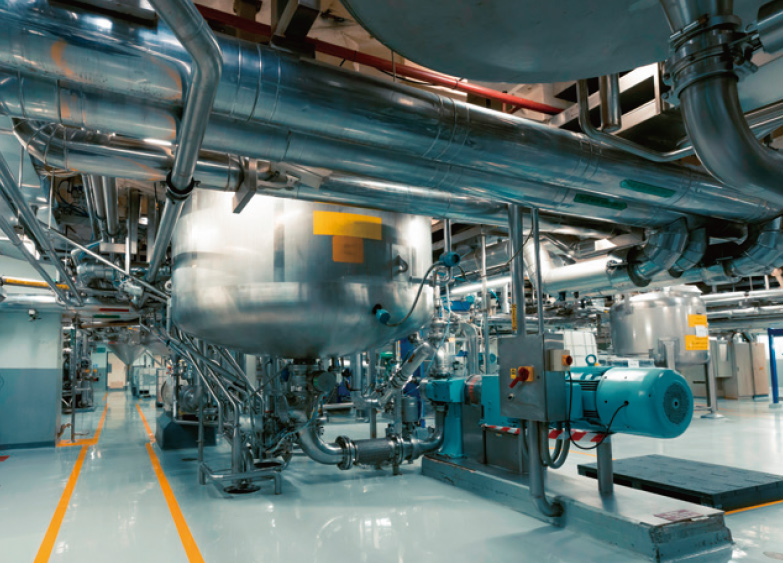
Customer Issues
Equipment monitoring with limited man-hours
A chemical plant utilizes a large number of supply pumps, making it difficult to monitor them through operator rounds. Instead of relying on operator rounds carried out by workers, there is a need to automate constant monitoring.
Impact on production quality due to deterioration of supply pumps
To stabilize product quality, it is necessary to detect signs of abnormality in the supply pumps, and perform appropriate maintenance.
Industrial IoT Wireless Solution Sushi Sensor
Online monitoring
The condition of equipment can be monitored online by utilizing the Sushi Sensor. Wireless vibration sensors are installed on the center of shaft coupling between the motor and supply pump. The condition of the bearings is constantly monitored to detect signs of equipment abnormality (“something wrong”)
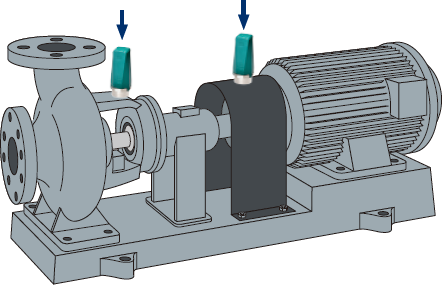
Maintaining and improving inspection quality
The collected data can be monitored and recorded using the Data Logging Software GA10 through the LoRaWAN® network. By digitizing the condition of equipment and enabling quantitative judgments based on the collected data, the monitoring system prevents the overlooking of signs of abnormalities. In utilizing GA10's Anomaly Detection Function, the AI detects changes in equipment conditions as signs of abnormality and alerts the user of such signs.
Benefits
By replacing operator rounds of equipment monitoring with the Sushi Sensor, equipment with a high risk of failure can be efficiently identified.
In one case at a chemical plant, the wireless vibration sensor is installed on multiple supply pumps to monitor the condition of equipment online, stabilizing to improved product quality. As a result of the detailed diagnosis of the equipment that exceeded the threshold, bearing wear was detected in the motor, and maintenance was carried out. This enabled the equipment to maintain its health condition and prevented product quality from being impacted. Currently, the temperature of raw material storage tanks, piping and containers are also being monitored by Sushi Sensor, expanding the scope of monitored processes and equipment.
By installing the Sushi Sensor, the entire plant is monitored online to contributes to maintaining the health of equipment and stabilizing product quality.
Example of System Configuration
Отрасли
-
Химическая промышленность
Химические производства применяют периодические и непрерывные технологические процессы производства, каждый из которых имеет свои особые требования для систем управления. Непрерывному технологическому процессу требуется надёжная и стабильно работающая система управления, защищающая от внеплановых остановов, в то время как для периодических процессов более важна гибкость организации партий, возможности внесения корректировок в рецепты и формулы. Для обоих типов процессов одинаково важно вести управление с поддержанием требуемого качества и способность управлять не рутинными операциями. Имея в наличии обширный послужной список и богатое портфолио проектов, а также опытных системных инженеров и обширную сеть поддержки по всему миру, у компании Yokogawa имеются решения для всех видов таких систем.
Related Products & Solutions
-
Data Logging Software GA10
The latest software that enables you to build a DAQ system without programming. Designed for maximum compatibility with Yokogawa recorders, data loggers, temperature controllers, and power monitors, GA10 can also acquire data via Modbus communications.