Offshore exploration and production requires maximum uptime under harsh conditions. Manned and unmanned facilities need reliable integrated control and safety systems (ICSS) with advanced remote monitoring capabilities. Yokogawa has state-of-the-art technology and extensive experience in executing offshore projects of all sizes and automation levels of complexity.
Herausforderungen
Customer Challenge
System Integration
Our Solutions
As a supplier of integrated control and safety system (ICSS) for FPSO, Yokogawa deliveres solutions, including CENTUM VP process control system (PCS) and ProSafe-RS safety system for hull / topside control, subsea control and turret mooring system with interface solution and the Plant Resource Manager (PRM) package for instrument management. These are integrated with third-party systems such as machine monitoring system, process data server and operator training and maintenance system.
ICSS performs the monitoring and control of processing facilities, including associated topside facilities, regulatory control and on/off controls. It also generates production data reports, interfaces with other subsystems and human machine interface (HMI) consoles, archives, records and transmits data to other interface systems and a management reporting system.
ICSS makes possible centralized plant supervision and management of all control and safety functions.
Customer Benefits
Reliable and Efficient Operation
Enabling Technology
CENTUM VP Integrated Production Control System
CENTUM VP is Yokogawa's latest integrated production control system, also known as a distributed control system (DCS). CENTUM VP has a more intuitive human machine interface and more powerful field control stations capable of processing data faster and more reliably. Thanks to features such as a pair & spare CPU configuration, CENTUM VP achieves 99.99999% (seven‐9s) availability.
ProSafe-RS Process Safety System
Yokogawa puts an end to DCS-SIS incompatibility with the ProSafe-RS, the world’s first truly integrated "safety PLC" for the process industries.
Customer Challenge
System Integration by Flexible and modular approach
Our Solutions
Yokogawa ICSS architecture and solution for FLNG utilize the technology in a flexible and modular approach. We are using our distributed ICSS architecture to its full extend when designing a Total Integrated Modular System to minimize RISK during Design, Installation and Commissioning until “The first LNG”.Autonomous Control and Safety/Fire & Gas system of different process modules are ensured by utilizing dedicated network segment and controllers, as well as distributed I/O modules for each autonomous systems.
In large modules, dedicated operation stations supporting the segment are installed in the Local Equipment Room (LER).
Our concept for implementing a solution for ICSS onboard a FLNG facility, is made in modular design. Cost effective and time saving execution are implemented in multiple locations, and delivered to each modules on schedule. Each module can be tested locally, before shipped to the assembly yard for final integration.
The Hull ICSS can be implemented separately from topside process modules and put into operation in due time before installation of topside. This is also applicable to Subsea ICSS, which Yokogawa is able to integrate the Subsea Master Control in a same manner.
Customer Benefits
Minimize RISK during Design, Installation and Commissioning
Enabling Technology
Yokogawa's ICSS with N-IO (Network I/O), the next-generation smart configurable I/O, allows flexible-binding I/O assignments. Matched with the FieldMate Validator, our commissioning tool, this allows for significantly faster project completion and reduced costs without compromising on quality.
Details
Floating Production Storage and Offloading (FPSO)
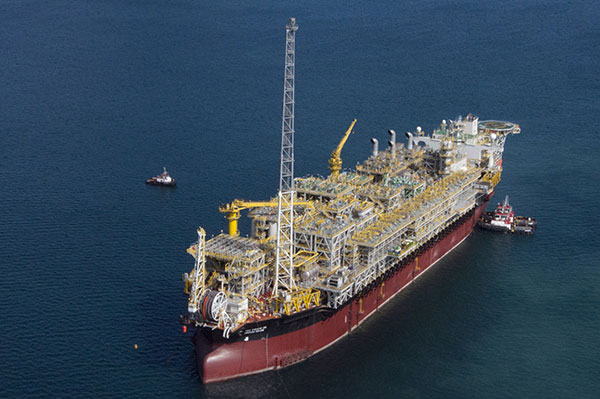
Photo courtesy of MODEC, Inc.
A Floating Production, Storage, and Offloading (FPSO) unit is a floating offshore production facility that stores both processing equipment and storage for produced hydrocarbons. Hydrocarbons are produced by platforms or subsea templates, and then passed to the FPSO facility. The FPSO facility then processes the oil and stores it until it can be transported via a pipeline or oil tanker. Floating Production Storage and Offloading (FPSO) units are used by oil companies make it economically feasible to produce oil in remote areas and in deeper water.
Floating LNG (FLNG)
Yokogawa has more than 30 Years’ experience in executing LNG projects, and has acquired significant engineering knowledge through the whole chain. Combining Yokogawa’s knowledge from Liquefaction, Regasification and LNG transportation, together with the rich experience in offshore production facilities, Yokogawa provides unique know how and capabilities in executing global FLNG projects throughout the lifetime of the facility.
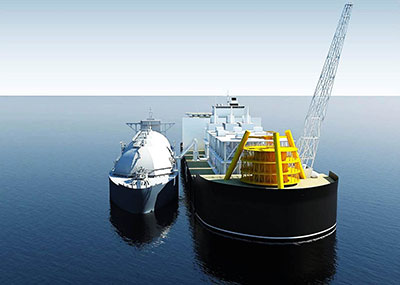
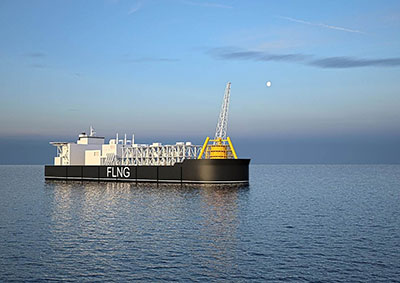
Floating Storage and Regasification Unit (FSRU)
Years of study have shown that large floating production, storage, and off-loading (FPSO) vessels are increasingly feasible solutions for LNG projects. Even though offshore and onshore natural gas liquefaction and regasification plants have different requirements, both must rely on proven liquefaction and regasification processes. Ballast and cargo loading/unloading control are also very similar on LNG carriers. Based on its rich LNG liquefaction, regasification, and carrier experience and its expertise in various kinds of floating production systems, Yokogawa is confident in its ability to provide a full range of production management, asset management, safety management, power management, and compressor control solutions for floating LNG (FLNG) and floating storage and regasification unit (FSRU) projects.
Publikationen
- Completion of First FPSO Project for Prosafe Production Services Pte Ltd
- Integrated Control & Safety System (ICSS) makes possible centralised plant supervision and management of all control and safety functions on this FPSO.
- Yokogawa's integrated solution contributed to reliable and efficient operation.
- All the instrument information is fully integrated with the instrument management system.
- Yokogawa provides CENTUM VP subsea and topsides integrated control systems to Stones subsea wells in the Gulf of Mexico.
- The high reliable CENTUM VP system was ideally suited for the world's deepest subsea facility.
STARDOM field control node (FCN) autonomous controllers allow both Modbus master and slave functions to run simultaneously.
Operators must receive diagnostic information before a line block leads to a malfunction. Yokogawa provides predictive diagnostics based on trend analysis of the blocking factor, which improves maintenance efficiency and reduces maintenance costs.
One of the most common applications for differential pressure transmitters is flow measurement. DPharp differential pressure transmitters have some unique signal conditioning features to eliminate instability at low flow rates.
The major methods of improved oil recovery are water flooding and steam injection. "These technologies make a tremendous contribution to recovering additional oil from old wells as well as improve primary recovery of operating oil fields."
The paperless recorder DX series instruments allow you to determine temperature and humidity, and manage the results as manufacturing and quality data at a reasonable cost with a simple configuration.
Yokogawa provides controller embedded flow calculation library based on AGA (American Gas Association) reports.
Reverse osmosis (RO) is a separation process that uses pressure to force a solution through a membrane that retains the solute on one side and allows the pure solvent to pass to the other side. More formally, it is the process of forcing a solvent from a region of high solute concentration through a membrane to a region of low solute concentration by applying a pressure in excess of the osmotic pressure.
Floating-point format calculations have enabled physical quantities (in engineering units) to be used in calculations.
- Effeciently controls the inlet valve and blow-off valve when the compressor starts and stops.
- During steady operation, controls the inlet valve so that the amount of discharged compressed air becomes constant (flow control)
- Surging: Load decreases, the amount of discharge flow and pressure drop, and a limit is exceeded, possibly destroying the compressor.
Industrial Combustion sources such as thermal cracking furnaces and, process heaters play a critical role in the process industry.
Recently, several ARC Advisory Group analysts and management team members had a chance to sit down with the new Yokogawa President and COO, Mr. Takashi Nishijima, and several other top Yokogawa executives to discuss the company's burgeoning presence in the worldwide upstream and midstream oil & gas industry.
Alarm management is not just a project that has a start and end date; it's a continuous cycle. Once the alarm system has been reviewed and improvements have been identified, we must check that controls are in place to ensure the alarm system remains functional. The key is to ensure that the system is continuously monitored and any changes are fully documented. There are seven key steps for alarm management. Rationalization is one of those critical steps.
Tuning PID controllers can seem a mystery. Parameters that provide effective control over a process one day fail to do so the next. The stability and responsiveness of a process seem to be at complete odds with each other. And controller equations include subtle differences that can baffle even the most experienced practitioners.
The worlds of process automation and production management have been converging for some time. What once used to be islands of automation and production management functionality connected through highly proprietary integration schemes that were costly to maintain have developed into integrated platforms that provide seamless data exchange between the world of automation and the plant floor, the functions of production and operations management, and integration with business level systems.
The world of process automation is governed by procedures. While we like to refer to the process industries as being largely "continuous", this could not be further from the truth. Process manufacturing is constantly in flux.
The automation suppliers that will be successful in the long term will be those that effectively address application or industry specific problems for end users with a value proposition that cannot be ignored. These problems exist throughout the process industries today, and they won't be solved by simply offering a product, but through a combination of hardware, software, services, application expertise, and knowledge.
In ARC's view, customers need a compelling business value proposition to justify investment in any kind of automation. Vigilance and VigilantPlant were created with this in mind. Yokogawa's vision with VigilantPlant is to create an environment where plant personnel and operators are well informed, alert, and ready to take action.
Yokogawa has come a long way in making its message clear to the world of process automation. Last year, the company embarked on a full-scale global marketing campaign to make customers aware of the company's focus on system reliability, security, dependability, and robustness. Dubbed "Vigilance", the campaign created a unified message for the company and greatly helped expand awareness of the Yokogawa brand and corporate philosophy.
Process automation end users are under more pressure than ever to do more with less. The current economic climate means that many automation capital projects are on hold. With capital budgets tighter than ever, users instead focus on operational budgets (where cost cutting is also a key concern), or on automation investments with a very rapid return on investment.
In today's dynamic industrial marketplace, the only constant is change. Raw material costs, energy costs, market demands, environmental and safety regulations, technology, and even the nature of the labor force itself are constantly changing, and not always in predictable directions.
Migration of a refinery's DCS provided an opportunity to reconfigure and consolidate the control rooms and operational management system.
July 2011
Process plants are run according to operational procedures. These procedures consist of a set of tasks that are executed in a consistent manner to achieve a specific objective, such as starting up, shutting down or transitioning a unit as part of making a product.
July 2010
Martin te Lintelo, Yokogawa Europe B.V., The Netherlands, discusses high level control system design for LNG receiving terminals. As demand for LNG increases worldwide, players face seemingly conflicting challenges. On one hand, they must expand capacity in different regions, make the business and production as agile and adaptive as possible, and improve operational efficiency.
The LNG sector presents challenges for the automation supplier, particularly in the implementation of automation systems for regasification terminals. Yokogawa Europe's business development manager, upstream oil and gas Martin te Lintelo looks at the handling of the potential automation-related problem areas and opportunities.
August 2006
Many published papers discuss the benefits of subsea HIPPS and many studies show the potential cost-benefit analysis of this technology in deepwater applications. An internet search for subsea HIPPS is informative; however, little appears that discusses the systems already delivered and operating successfully.
Chevron turns to deeper relationships with fewer suppliers to increase project execution consistency
Offshore, February 2013
Offshore and deep-water production has been a significant factor in the sustained growth of the oil and gas industries over the past decade and this trend is expected to continue beyond 2013.
Downloads
Bulletins
- Integrating the Hydrogen Ecosystem (9.5 MB)
Videos
Chet Mroz, President & CEO Yokogawa North America, discusses the benefits of IoT at the 2015 ARC Industry Forum in Orlando.
Möchten Sie weitere Informationen über unsere Mitarbeiter, Technologien und Lösungen?
Kontakt