NH3 injection lowers NOx in stack flue gas, boosts dust collection efficiency, and prevents erosion. Precise measurement and control of NH3 are crucial to avoid excess use, which increases costs and causes odors. The TDLS8000 solves these issues with direct measurement for effective NH3 management.
Introduction
In a boiler application, ammonia (NH3) gas is injected to remove nitrogen oxides (NOx) and reduce the NOx concentration in the stack flue gas. Conventional analyzers obtain the NH3 concentrations indirectly through a sampling system. The sampling system introduces time delays in the measurement and increases maintenance costs. Since the TDLS8000 Laser Analyzer does not use a sampling system, it solves such problems. The TDLS8000 Laser Analyzer solves these issues with direct measurement, eliminating sampling needs and offering real-time data, necessary accuracy, and efficiency for effective NH3 management.
Continuous Monitoring: Ensures constant NH3 emission sampling system,
it is a solution to track environmental compliance.
Process Overview
The NH3 gas is injected to reduce the NOx concentration in the stack flue gas, increase the dust collection efficiency of the dust collector (ESP), and prevent erosion. Excess NH3 injection increases the running cost and the amount of residual NH3, which results in a foul odor. Therefore, it is essential for boiler operators to closely monitor and control the NH3 concentration in the stack flue gas.
(Oil and Gas Fuels)
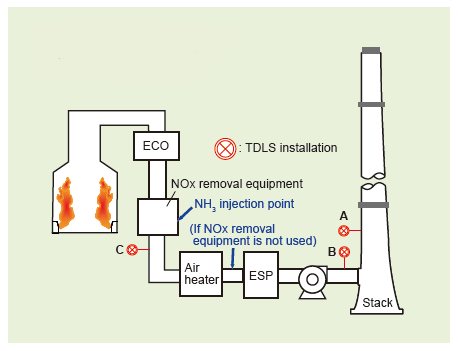
Cost Reduction: No sampling system is needed, cutting maintenance and operational costs.
Solution
Compared to conventional NH3 analyzers, which perform measurements through a sampling system, the TDLS8000 can measure the NH3 concentrations in furnaces directly and, thus, reduce maintenance and running costs. The TDLS8000 is entirely field repairable; there is no need to return the analyzer to the factory for service or repair.
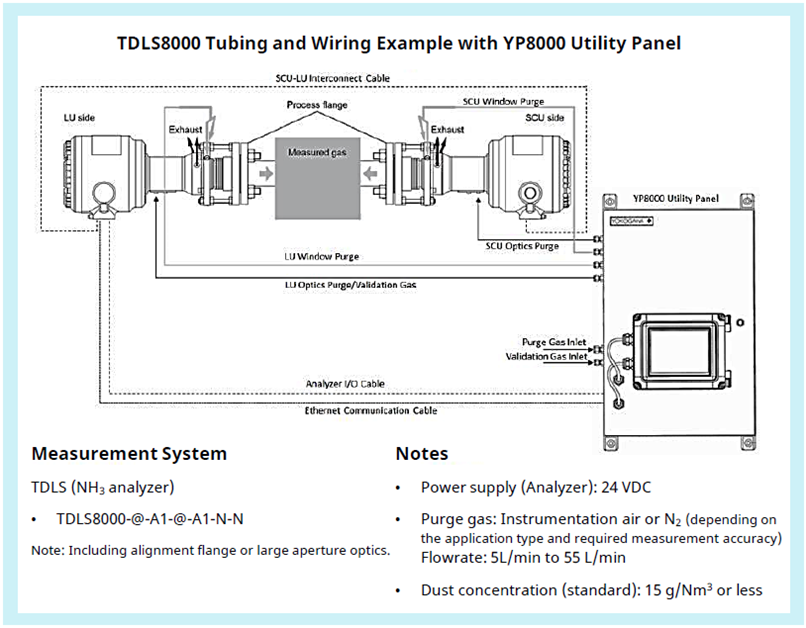
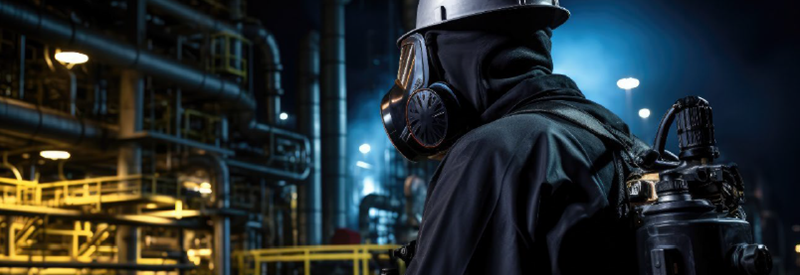
Enhanced Equipment Life: Real-time measurements extend NOx removal,
equipment lifespan, and reduce ammonium sulfate buildup.
Field Data
Since the TDLS8000 rapidly responds to NH3 concentration changes, it can provide timely process variable updates for optimum injection control.
Changes in NH3 Injection Volume Measured Values
(Installation Point A / Without NOx Removal Equipment)
Key Benefits
- By eliminating the need for a sampling system, the TDLS8000 reduces maintenance and running costs.
- High-speed response to changes in the NH3 concentration enables optimal injection control.
- Continuous emissions monitoring is environmentally friendly and contributes to sustainability.
- The TDLS8000 extends the service life of NOx removal equipment and reduces the ammonium sulfate ((NH4)2SO4) precipitation in the air heater.
TDLS8000
Overall, the In-Situ Gas Analyzer TDLS8000 houses all the industry’s leading features in one robust device. The platform design is for in-situ measurements, eliminating the need for sample extraction and conditioning. For industries such as Chemical, Hydrogen, Power, Geothermal Power, Thermal, and more, this industry-proven laser analyzer is designed to meet all your requirements in one device that is easy to operate and maintain.
Industries
-
Ammonia
Ammonia producers are faced with rapid growth combined with many older control systems. Growth is driven by global demand for fertilizer and supported by cheap and plentiful shale gas.
-
Base Chemical
Yokogawa has been serving the bulk chemical market globally and is the recognized leader in this market. With products, solutions, and industry expertise, Yokogawa understands your market and production needs and will work with you to provide a reliable, and cost-effective solution through the lifecycle of your plant.
-
Chemical
Chemical plants rely on continuous and batch production processes, each posing different requirements for a control system. A continuous process calls for a robust and stable control system that will not fail and cause the shutdown of a production line, whereas the emphasis with a batch process is on having a control system that allows great flexibility in making adjustments to formulas, procedures, and the like. Both kinds of systems need to be managed in available quality history of product, and to be able to execute non-routine operations. With its extensive product portfolio, experienced systems engineers, and global sales and service network, Yokogawa has a solution for every plant process.
-
Geothermal Power
Generating electricity despite the weather.
-
Hydrogen
https://pages.yokogawa.com/hydrogen-free-consultation-offerA Comprehensive Solution Across the Entire H2 Ecosystem
-
Oil & Gas
Yokogawa has a wealth of experience in every part of the oil and gas business, from offshore and onshore facilities to pipelines, terminals, and deepwater operations. We provide solutions that enhance safety, ensure accurate and reliable operation, and increase plant efficiency.
-
Power
In the mid 1970s, Yokogawa entered the power business with the release of the EBS Electric Control System. Since then, Yokogawa has steadfastly continued with the development of our technologies and capabilities for providing the best services and solutions to our customers worldwide.
Yokogawa has operated the global power solutions network to play a more active role in the dynamic global power market. This has allowed closer teamwork within Yokogawa, bringing together our global resources and industry know-how. Yokogawa's power industry experts work together to bring each customer the solution that best suits their sophisticated requirements.
-
Thermal
Thermal power using coal, oil or gas as fuel accounts for the majority of electric generation throughout the world.
-
Water & Wastewater
All water, regardless of its source, has value. However, with water resources being finite, a focus on "One Water" is necessary to maximize every drop within the water system, ensuring a stable supply of clean and safe water. As we consider current and future needs, planning and implementation are critical for long-term resilience and reliability, meeting both community and ecosystem demands. Yokogawa believes water is a human right for all. Thus, contributing to a sustainable water cycle is one of our Sustainable Development Goals (SDGs).
Related Products & Solutions
-
In-Situ Gas Analyzer TDLS8000
Eliminate sample extraction and conditioning
-
Analyzers
Process analyzers are used to determine the chemical composition and physical properties of substances used in industrial processes.
-
Gas Analyzers
Enhance efficiency and product quality with real-time analysis
-
Oxygen Analyzers
Measure accurately and reliably across multiple applications
Have Questions?
Contact a Yokogawa Expert to learn how we can help you solve your challenges.