Temperature measurements over a wide range prevent inventory loss and reduce downtime.
The pasteurization process is important in beer manufacturing because it helps extend the shelf life of the beer and prevent spoilage. During the pasteurization process, the beer is heated to a specific temperature for a specific amount of time to kill any harmful bacteria or other microorganisms that may be present in the beer. This helps ensure that the beer remains safe to drink and does not spoil or become contaminated during storage or transportation.
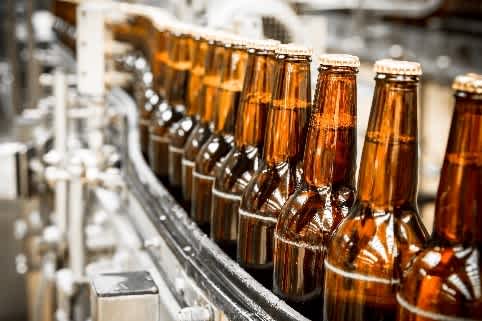
Figure 1. Brewery bottling
In addition to extending the shelf life of the beer, pasteurization can also help to stabilize the beer and improve its flavor and appearance. By removing any unwanted microorganisms or impurities, pasteurization can help to ensure that the beer has a consistent flavor and appearance, which is important for maintaining the quality and reputation of the brand.
Challenges
Bottled or canned beers are pasteurized by passing through the spraying chamber called a “tunnel” in which hot water is sprayed over the containers for a fixed time before cooling. To ensure the quality and safety of the beer that is produced, it needs to be heated at a certain temperature for a fixed period of time. When spray is clogged without being noticed, the quality and safety of beer is at risk as there remains unwanted bacteria and microorganism. However, it is difficult for a maintenance team to detect clogging in real-time. Usually, maintenance checks is being done in a 6–8-hour cycle, causing not properly pasteurized products can be shipped to customers. To avoid brand damage, real-time monitoring of a clogged shower is needed.
Solution
The tunnel in the pasteurization process is narrow, making real-time monitoring of temperature consistency difficult. Thermal cameras can be deployed, but they have many blind spots, and point-type temperature sensors are not practical due to the need for hundreds of wiring connections.
However, Yokogawa’s fiber optic temperature sensor DTSX can realize real-time monitoring of a whole tunnel without blind spots and measures the temperature profile over a far, wide area along the fiber optic cable.
Since the fiber optic cable is thin (φ2-4mm), it can be laid between the showers and the narrow spaces of bottles and cans without obstructing the spray, allowing temperature measurement throughout the entire tunnel. Based on testing and experience, Yokogawa proposes the use of protected fiber optic cables against heat, acid, and water pressure, as well as a laying method that eliminates measurement dead zones.
Temperature measurement data inside the tunnel in the pasteurization can be displayed in real-time on a screen as a heat map by utilizing Yokogawa‘s STARDOM and CI server. This enables monitoring of whether the temperature is appropriate, and if there is a clogged shower, the temperature will drop compared to the surrounding areas, allowing to pinpoint the anormal temperature location and giving off an alarm to operators by email.
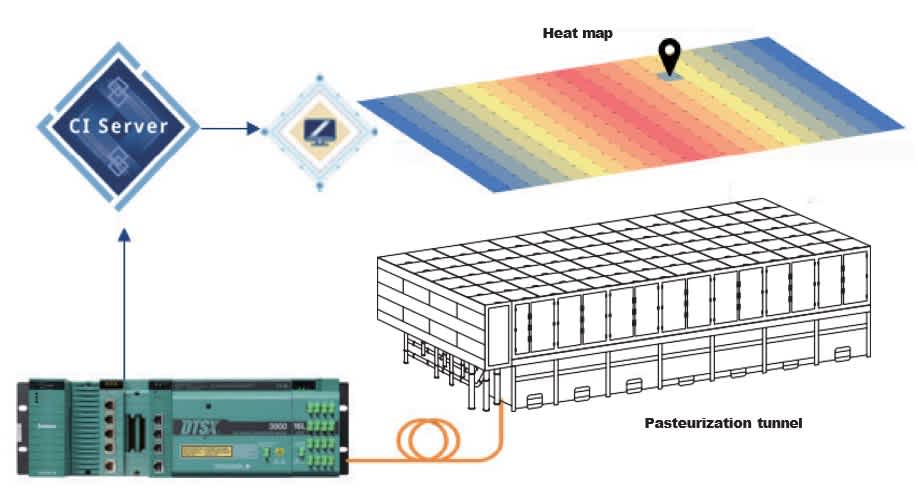
Figure 2. Yokogawa’s fiber optic temperature sensor DTSX measures temperature distribution over
the length of an optical fiber cable using the fiber itself as the sensing element.
Key Benefits
Longer shelf life with consistent quality by real-time monitoring of the pasteurization process while reducing work hours.
- Several daily hours can be saved for a maintenance team in the detection and investigation of showers that could be clogged.
- A fiber optic cable doesn’t require hundreds of wiring connections and maintenance is easier than point-type temperature sensors. It reduces the installation and running costs.
- The beverage quality, expiration date, and final product characteristics are guaranteed, avoiding brand reputation damage and maintain customer loyalty.
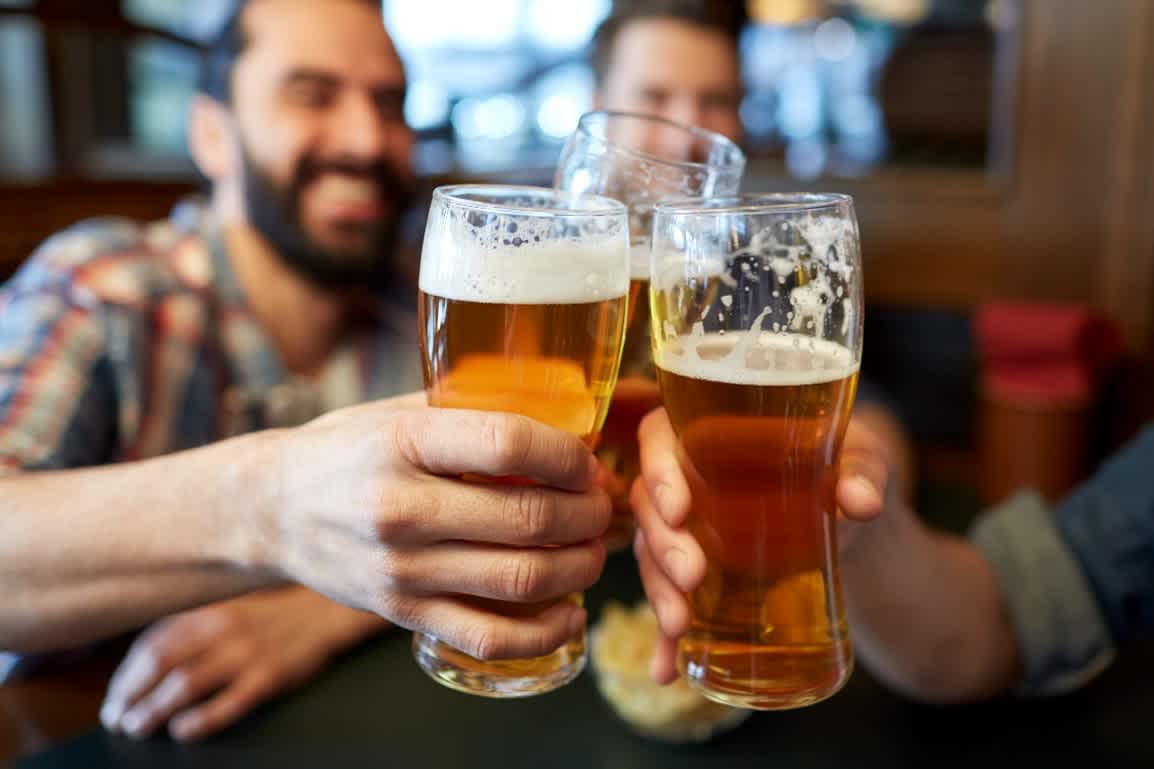
Industries
-
Food & Beverage
The food and beverage industry must produce safe, high-quality foods and beverages for consumers. In addition to quality control, the manufacturing processes include many challenges such as managing ingredients, improving efficiency and handling global environmental issues. Yokogawa leverages its decades of technological expertise to help customers build and operate the ideal factory.
Related Products & Solutions
-
DTSX3000
The DTSX3000 is the long range, high accuracy product, with a measurement range of up to 50km, a temperature accuracy of 0.01 °C, and 19" rack design.
-
Distributed Fiber Optic Temperature Sensor
Enhance process visibility and safety with cost-effective measurement solutions
Have Questions?
Contact a Yokogawa Expert to learn how we can help you solve your challenges.