Introduction
Level transmitter configuration can be very time consuming. Calculations required to determine proper range values for traditional transmitters can become complex due to the physical layout of an application.
DPharp transmitters with advanced software functionality eliminate this time consuming task. With maintenance shops getting smaller, finding equipment that allows us to do more with less becomes a priority.
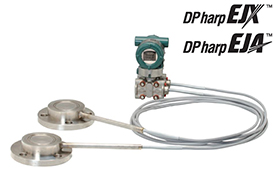
Application
Using typical smart or conventional products all of the following must be considered:
- The specific gravity (SG) of the process;
- Precise location of 0% and 100%;
- Specific gravity of the capillary fill fluid or sealing liquid (for impulse tubing);
- Vertical height of capillary or impulse piping;
- Exact orientation of the transmitter to the vessel;
- Vertical distance between the flanges.
Depending on the application, the vessel may be open (referencing atmosphere), or closed (under some blanket pressure).
Elevation is typically used when the vessel is closed. To reference blanket pressures, a low side wet leg or remote seal must be used. The low side pressure creates a negative force on the transmitter equal to the vertical height times the specific gravity of the fill fluid.
Suppression is positive pressure created on the high side of the transmitter typically due to a zero point above the transmitter. It is normally employed in an open vessel referencing atmosphere. This is a positive pressure equal to the vertical distance between the 0% point and the transmitter times the specific gravity of the liquid.
Elevation/suppression distance almost never agrees with the piping and instrumentation diagram (P&ID) because actual piping (or remote seal capillaries) do not form exacting angles in the field. In most cases, the precise vertical height is not known until the unit is installed.
Span is the vertical distance of the process times the specific gravity: Figure 1. 10.5 * 0.9 = 9.45 mH2O (31.5 inH2O).
Calibration range is the calculated 0 and 100% taking into consideration positive and negative pressures. In figure 1, the following applies:
Figure 1
0 % = H - L
= ( 4.5 x 0.8 ) - ( 15 x 0.8 )
= 3.6 - 12
= -8.4 mH2O ( -28 inH2O )
100 % = H - L
= ( 4.5 x 0.8 ) + ( 10.5 x 0.9 ) - ( 15 x 0.8 )
= 3.6 + 9.45 - 12
= 1.05 mH2O ( 3.5 inH2O )
The calibration range is: -8.4 to 1.05 mH2O ( -28 to 3.5 inH2O )
Note: SG stands for specific gravity.
The information required to perform the calculation is not readily available. It exists in vendors instruction manuals, P&ID's, but not until the unit is actually installed will all the variables be known because the process piping and capillaries do not form exacting angles in the field.
Solution
DPharp has a smart level setup feature that eliminates the need for elevation/suppression calculations, making set up quick and painless.
Calibration is accomplished by simply following these four steps (for Brain):
- Span the transmitter to the process, height * specific gravity of 0 to 9.45 mH2O (0 to 31.5 inH2O) using the BT200 in C21: LRV and C22: HRV.
- Install to the process using either capillaries or impulse tubing.
- Bring the process to a zero (4mA) condition.
- Through the BT200 execute H10: Auto LRV in the H: AUTO SET menu.
DPharp will calculate the total elevation/suppression and automatically setup the device for that installation. It will even correct the values in software at C21: LRV -28 and C22: HRV 3.5 so the customer can print and record the actual configuration for their maintenance documents.
But what if I cannot bring my process to zero? I have installed the unit, fluid is now in the tank, and the output of the transmitter does not agree with my sight glass. What do I do?
Most transmitters can only make adjustments at 0% or 100%. DPharp can make adjustments anywhere with full elevation or suppression. Once the transmitter is programmed with the correct span, all that is needed is a known point in the process (usually provided by the sight glass.) The output can be adjusted in one of two ways.
- Simply adjust the encoder on the DPharp until the output reaches the known point. In figure 1, the output would be adjusted to 60%.
- The correct value can be entered into J10: Zero Adj. In the case of this example, the proper output value of 60% would be entered. The amount of deviation can be viewed in J11: Zero Dev.
DPharp's digital sensing technology makes this possible. With analog sensing technologies (like capacitance sensors), range changes often necessitate a re-calibration or a trimming of the A/D converter to achieve specified performance. The digital DPharp sensor has no A/D converter, no trimming is necessary. The new range is guaranteed to perform within specification.
Notes
- In level measurement, it is important to maintain a consistent reference pressure. On a closed tank system, this is most efficiently achieved by the use of remote seals and capillary systems.
- It is important to note that the span is to be calculated on process height x specific gravity of the process fluid, and will not necessarily agree with the physical height.
- Output will be linear to the level, regardless of fluid or blanketing system.
- Use of remote seals eliminates problems such as condensation in impulse piping, the requirement for maintenance of condensate pots and fill fluid leaking into the process.
Main Features of DPharp
- ±0.03% Overpressure calibration protection
- ±0.1% per 10years long term stability
- 100:1 turndown
- ±0.055% accuracy
- SIL2 standard
- ±0.1% per 15years long term stability
- 200:1 turndown
- Best-in-class high accuracy, 0.04%
- Multi-sensing output
- Multi-variable transmitter as EJX family line-up
- SIL2 standard
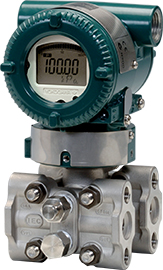
Looking for more information on our people, technology and solutions?
Contact UsIndustries
-
Chemical
Chemical plants rely on continuous and batch production processes, each posing different requirements for a control system. A continuous process calls for a robust and stable control system that will not fail and cause the shutdown of a production line, whereas the emphasis with a batch process is on having a control system that allows great flexibility in making adjustments to formulas, procedures, and the like. Both kinds of systems need to be managed in available quality history of product, and to be able to execute non-routine operations. With its extensive product portfolio, experienced systems engineers, and global sales and service network, Yokogawa has a solution for every plant process.
-
Iron & Steel
In the iron and steel industry, it is crucial to improve the quality of not only products but also manufacturing and operation technologies, as well as to address environmental and energy-efficiency issues. Yokogawa helps customers to create the ideal plant and evolves with them for mutual growth.
-
Oil & Gas
Yokogawa has a wealth of experience in every part of the oil and gas business, from offshore and onshore facilities to pipelines, terminals, and deepwater operations. We provide solutions that enhance safety, ensure accurate and reliable operation, and increase plant efficiency.
-
Oil & Gas Downstream
The oil & gas downstream industry has been facing an increasing number of challenges in recent years. These include the changing characteristics of the feedstock to be processed, aging of process facilities and equipment, rising cost of energy, lack of skilled plant operators who can run a refinery safely and efficiently, and the ever-changing requirements from both the market and the customer.
Over the years, Yokogawa has partnered with many downstream companies to provide industrial solutions focused on solving these challenges and problems. Yokogawa's VigilantPlant solutions have helped plant owners to achieve maximum profitability and sustainable safety within their plants.
-
Power
In the mid 1970s, Yokogawa entered the power business with the release of the EBS Electric Control System. Since then, Yokogawa has steadfastly continued with the development of our technologies and capabilities for providing the best services and solutions to our customers worldwide.
Yokogawa has operated the global power solutions network to play a more active role in the dynamic global power market. This has allowed closer teamwork within Yokogawa, bringing together our global resources and industry know-how. Yokogawa's power industry experts work together to bring each customer the solution that best suits their sophisticated requirements.
-
Water & Wastewater
Water resources are finite, and therefore contributing to a sustainable water cycle is one of the Sustainable Development Goals (SDGs). Yokogawa has been providing advanced digital control solutions for the stable supply of clean and safe water, wastewater treatment for protecting the water environment, water loss management and optimization of plant operation for reducing CO2 emissions and running costs. With our leading-edge technologies, dependable products and extensive expertise and experience of diverse water projects around the world, we work with you to provide sustainable water solutions that boost your business and add value throughout the plant lifecycle.
Yokogawa supports a wide range of water control applications in both the municipal and industrial water markets.
Related Products & Solutions
-
EJA110E
Standard Traditional-mount Differential Pressure Transmitter based on the EJA-E Series.
-
EJA115E
Standard Differential Pressure Transmitter attached to an IFO assembly based on the EJA-E Series.
-
EJA118E
Standard Differential Pressure Transmitter with Remote Diaphragm Seals based on the EJA-E Series.
-
EJA120E
Standard Traditional-mount Differential Pressure Transmitter designed for Draft Range applications based on the EJA-E Series.
-
EJA130E
Standard Traditional-mount High Static Differential Pressure Transmitter based on the EJA-E Series.
-
EJA210E
Standard Flange-mounted Differential Pressure Transmitter designed for Liquid-level applications based on the EJA-E series.
-
EJA310E
Standard Traditional-mount Absolute Pressure Transmitter based on the EJA-E Series.
-
EJA430E
Standard Traditional-mount Gauge Pressure Transmitter based on the EJA-E series.
-
EJA438E
Standard Gauge Pressure Transmitter with Remote Diaphragm Seal based on the EJA-E Series.
-
EJA440E
Standard Traditional-mount High Gauge Pressure Transmitter based on the EJA-E Series.
-
EJA510E
Standard In-Line Mount Absolute Pressure Transmitter based on the EJA-E Series.
-
EJA530E
Standard In-Line Mount Gauge Pressure Transmitter based on the EJA-E Series.
-
EJAC60E Hygienic Adapter System (Fluidless Type)
Yokogawa introduces Fluidless series – EJAC60E Hygienic Adapter System (Fluidless Type).
This system composes of replaceable adapters(16 adapters in total) with hygienic function of pressure detection.
Suitable for various kind of process including hygienic connection. -
EJX110A
Traditional-mount Differential Pressure Transmitter based on the EJX-A Series as a high performance model.
-
EJX115A
Differential Pressure Transmitter attached to an IFO assembly based on the EJX-A Series as a high performance model.
-
EJX118A
Differential Pressure Transmitter with Remote Diaphragm Seals based on the EJX-A Series as a high performance model.
-
EJX120A
Traditional-mount Differential Pressure Transmitter designed for Draft Range applications based on the EJX-A Series as a high performance model.
-
EJX130A
Traditional-mount High Static Differential Pressure Transmitter based on the EJX-A Series as a high performance model.
-
EJX210A
Flanged-mounted Differential Pressure Transmitter designed for Liquid-level applications based on the EJX-A Series as a high performance model.
-
EJX310A
Traditional-mount Absolute Pressure Transmitter based on the EJX-A Series as a high performance model.
-
EJX430A
Traditional-mount Gauge Pressure Transmitter based on the EJX-A Series as a high performance model.
-
EJX438A
Gauge Pressure Transmitter with a Remote Diaphragm Seal based on the EJX-A Series as a high performance model.
-
EJX440A
Traditional-mount High Gauge Pressure Transmitter based on the EJX-A Series as a high performance model.
-
EJX510A
In-Line Mount Absolute Pressure Transmitter based on the EJX-A Series as a high performance model.
-
EJX530A
In-Line Gauge Pressure Transmitter based on the EJX-A Series as a high performance model.
-
EJX610A
High Performance In-Line Mount Absolute Pressure Transmitter based on the EJX-A Series.
-
EJX630A
In-Line Mount High Performance Gauge Pressure Transmitter based on the EJX-A Series.
-
EJX910A
This transmitter precisely measures differential pressure, static pressure, and process temperature; then uses these values in a high-perfomance on-board flow computer to deliver fully compensated Mass Flow.
-
EJX930A
Designed specifically for high static pressure applications, this transmitter precisely measures differential pressure, static pressure, and process temperature; then uses these values in a high-perfomance on-board flow computer to deliver fully compensated Mass Flow.
-
EJXC40A (Digital Remote Sensor)
Digital Remote Sensor (DRS) Transmitter connects two pressure sensors, primary (high-pressure side) and secondary (low-pressure side) in a remote location, with DRS dedicated communication cable to measure differential pressure.
-
EJXC50A, EJAC50E (Gauge Pressure Direct Mounted Seal)
Direct Mounted Diaphragm Seal System consists of gauge pressure transmitter with single direct mount diaphragm seal.
-
EJXC80A, EJAC80E (Differential / Gauge Pressure Diaphragm Seal)
Diaphragm Seal System consists of differential pressure or gauge pressure transmitter with one or two diaphragm seal.
-
EJXC80A, EJAC80E (Differential Pressure Direct Mounted Seal)
Direct Mounted Diaphragm Seal System consists of differential pressure transmitter with single direct mount diaphragm seal.
-
EJXC81A, EJAC81E (Absolute Pressure Diaphragm Seal)
Absolute Pressure Diaphragm Seal System consists of absolute pressure transmitter with single diaphragm seal.
-
Absolute Pressure
Absolute Pressure transmitters compare a pressure relative to Absolute pressure. Absolute pressure is always a positive value.
-
Diaphragm Seal System
Diaphragm Seal System can be used to measure liquid, gas, or steam flow as well as liquid level, density, and pressure.
-
Differential Pressure
Differential Pressure (DP) is defined as the difference between two pressures. Differential Pressure Transmitters use a reference point called the low-side pressure and compare it to the high-side pressure. Ports in the instrument are marked high-side and low-side.
-
Draft Pressure
Draft Pressure transmitters are a unique type of differential transmitter that is designed to measure small differences in very low static pressure environments.
-
Gauge Pressure
Gauge Pressure transmitters compare a pressure relative to atmospheric measure.
-
Hygienic Pressure Transmitters
Hygienic Pressure Transmitters are designed to fulfil the requirements of hygienic and pharmaceutical application.
-
Liquid Level
Accurate level readings are essential to the safe, reliable, profitable operation of your plant. Liquid Level transmitters measure differential pressure to infer the level in a vessel.
-
Low Flow
Using Bernoulli's equation, Differential Pressure transmitters can be used to infer the flow of fluid through a pipe.
-
Mass Flow (Multivariable)
There are several technologies on the market to measure mass flow. One is the Multi-variable Pressure Transmitter.
-
Pressure Transmitters
The accurate and stable measurement of process pressure with Yokogawa Pressure Transmitters supports the safe, reliable, and profitable operation of your plant.