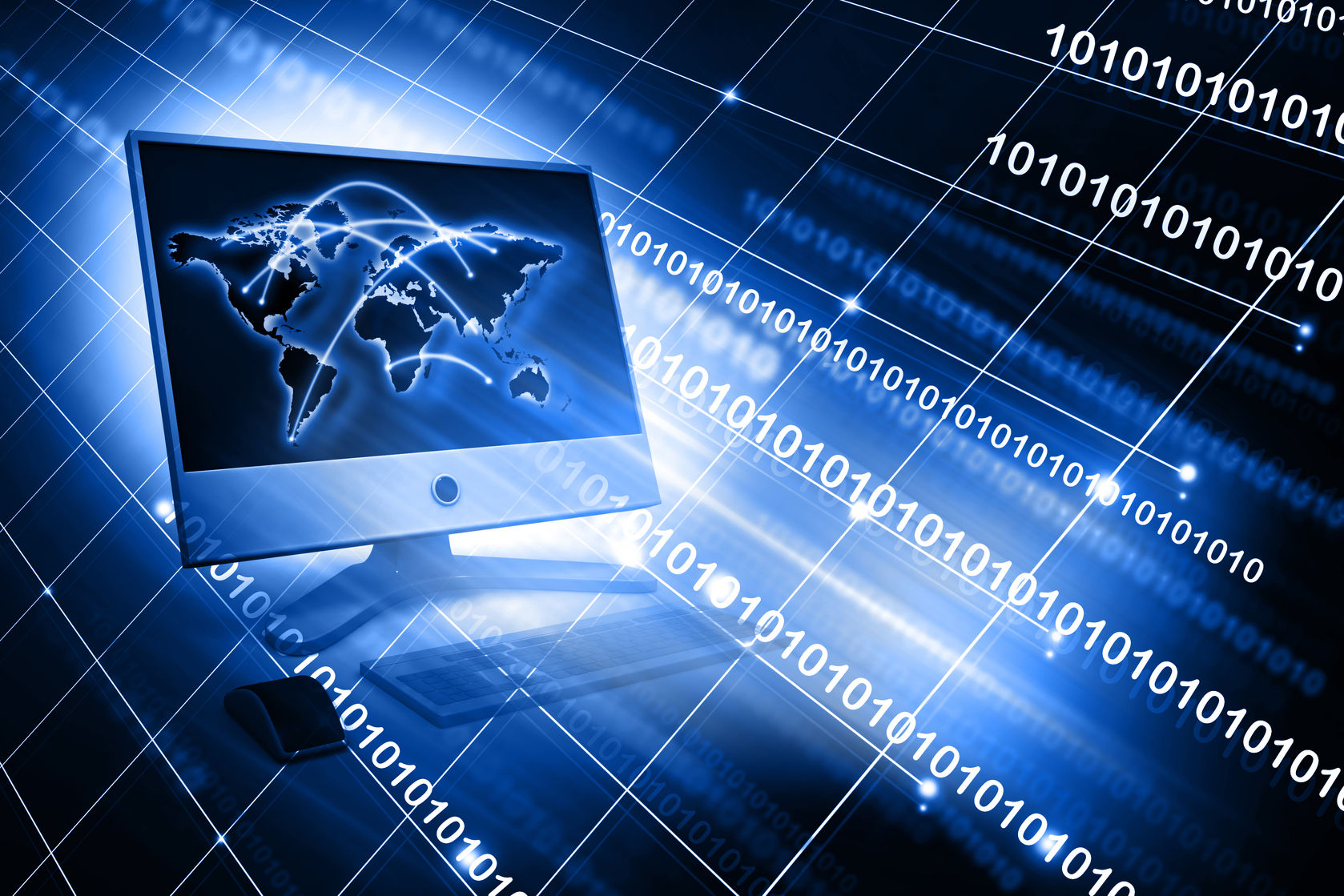
Both owners and EPCs require an easy way to assess if the integrated system approaches any of the defined design constraints before approving changes to be applied. Namur has also set up a work group to study how best to support and overcome these challenges.
Challenges for Customers
The level of complexity in system integration is increasing and strict adherence to design standards is the basis of a flawless start-up.
New projects are being built in more remote locations including floating plants. Access of experts to such locations during complex troubleshooting activities is becoming a critical risk factor.
Owners engage specialists to design architecture standards during project execution, but changes to plant operation in the network configuration and exchanged data are inevitable. These modifications require the maintenance engineers to re-assess the original design philosophy, and raise the risk that the interface equipment connecting the systems exceeds one of the design limits.
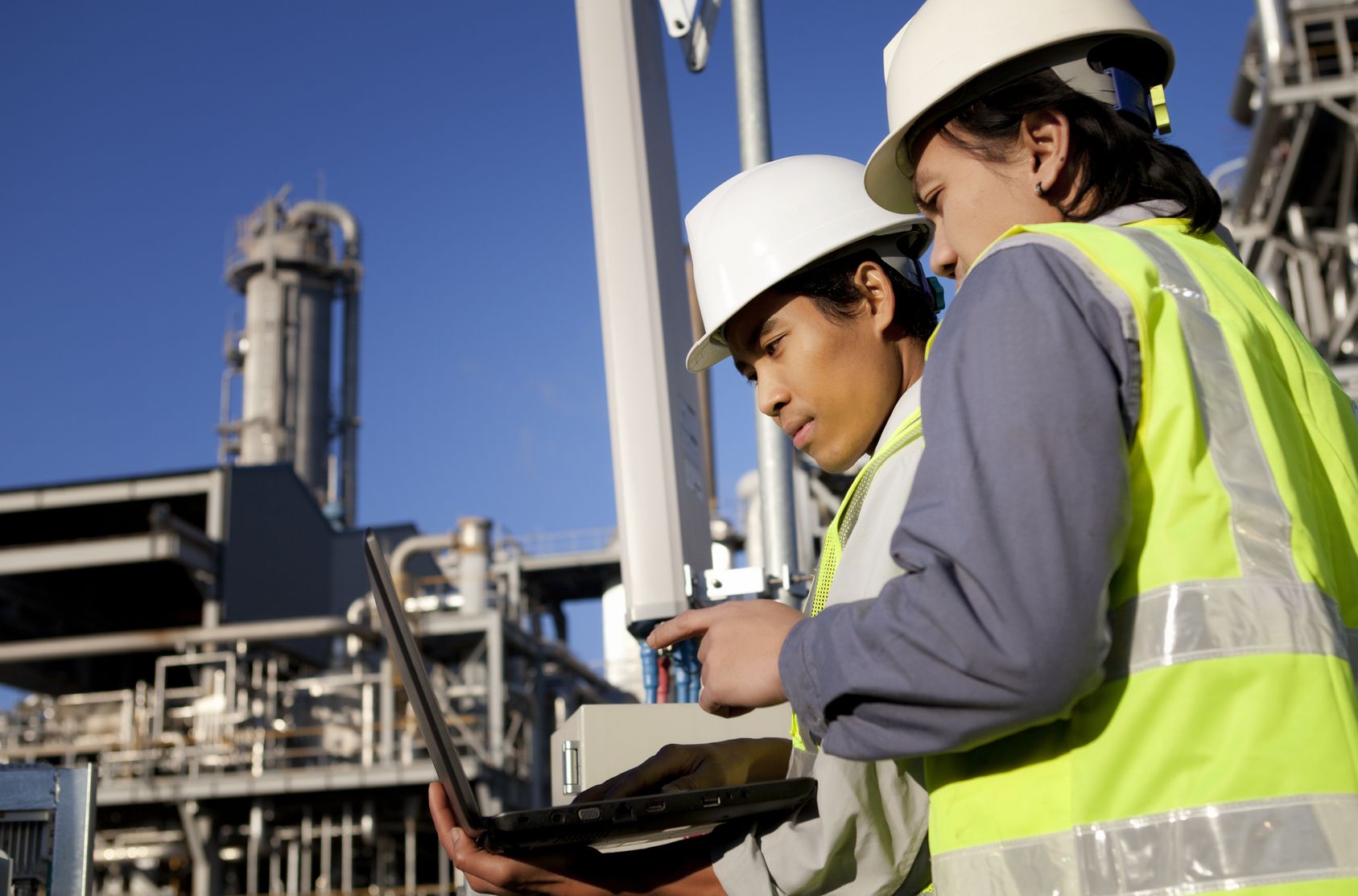
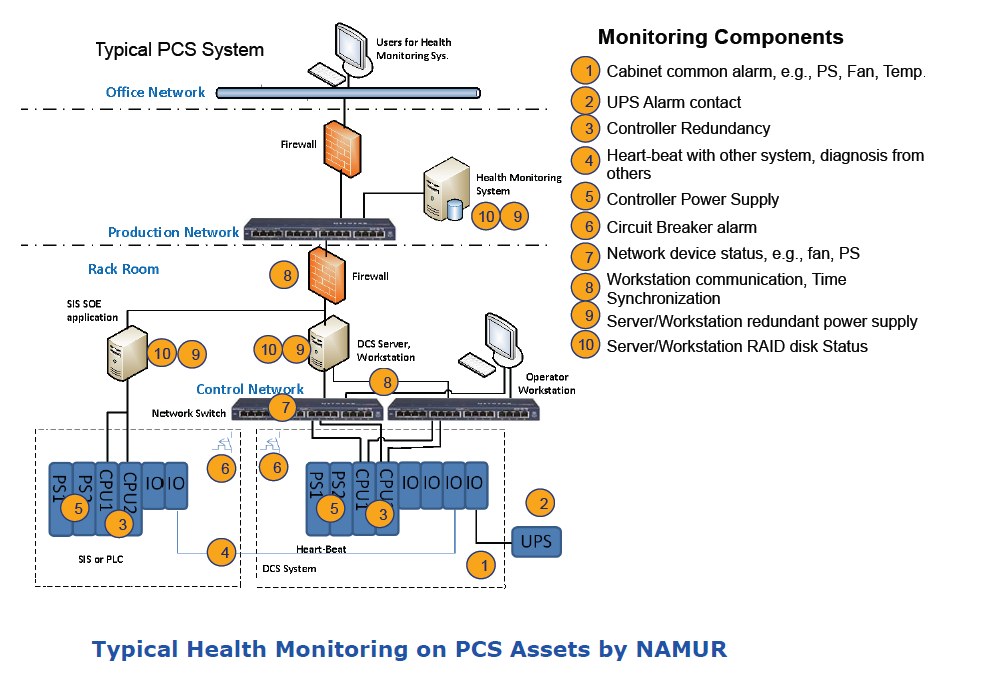
Our Solutions
The overall performance of the system is monitored by measuring various key design criteria, as specified in the original owner’s design requirements to the EPC. These criteria include network performance, field and safety controller performance, human interface performance, server performance, resource utilization (hard disks, etc.), security vulnerability (whether Microsoft security updates are applied, AV pattern files installed, etc.) and a list of obsolescent equipment (end of support).
As part of the system health monitoring service, Yokogawa gathers the health diagnosis data of the system equipment and then provides an evaluation report comparing the current data with data at the time the system was delivered or the last time such data was acquired. This service allows the EPC and/or owner to clearly grasp the health of the system at transition times or during maintenance periods.
As part of the periodical network health check service, the health of the network is monitored continuously and data is collected. This service collects and analyzes communication information, evaluates network health and detects any signs of potential cyber-attacks and/or new threats that cannot be detected by anti-virus software alone.
As part of the periodical asset health check service, our experts verify obsolescent equipment in the system and propose a plan for seamless upgrading to maintain sustainable plant. This approach can prevent failures caused by deterioration due to the environment.
The connections to upper level systems, integrated subsystems and connected field devices are monitored using a combination of the above services and data. Third-party tools are used to complement Yokogawa’s own diagnostics. These services monitor the average and peak throughput vs. maximum available bandwidth, as well as the status of communication registers which are usually the first sign of possible communication issues. Communication failures can then be prevented by taking corrective measures.
Customer Benefits
Yokogawa’s proven hardware reliability combined with superior diagnostics of the integrated system and earlier issue detection can prevent unplanned shutdowns due to a failure of automation or instrumentation assets.
The benefits of this monitoring solution start during project execution when the project team can compare the design constraints against the simulated or actual measured loading. The use of cloud execution can make these design reviews complex and difficult to assess by EPCs and owners. Snapshot reports are now available for passing design quality milestones, wherever the project is executed. This solution also provides impact analysis, as part of Management of Change, before, during and after the Application Acceptance Test (previously known as FAT). The EPC and/or owner can now make a sound decision to approve a change, knowing it will stay within the design constraints. The benefits continue through project lifecycle.
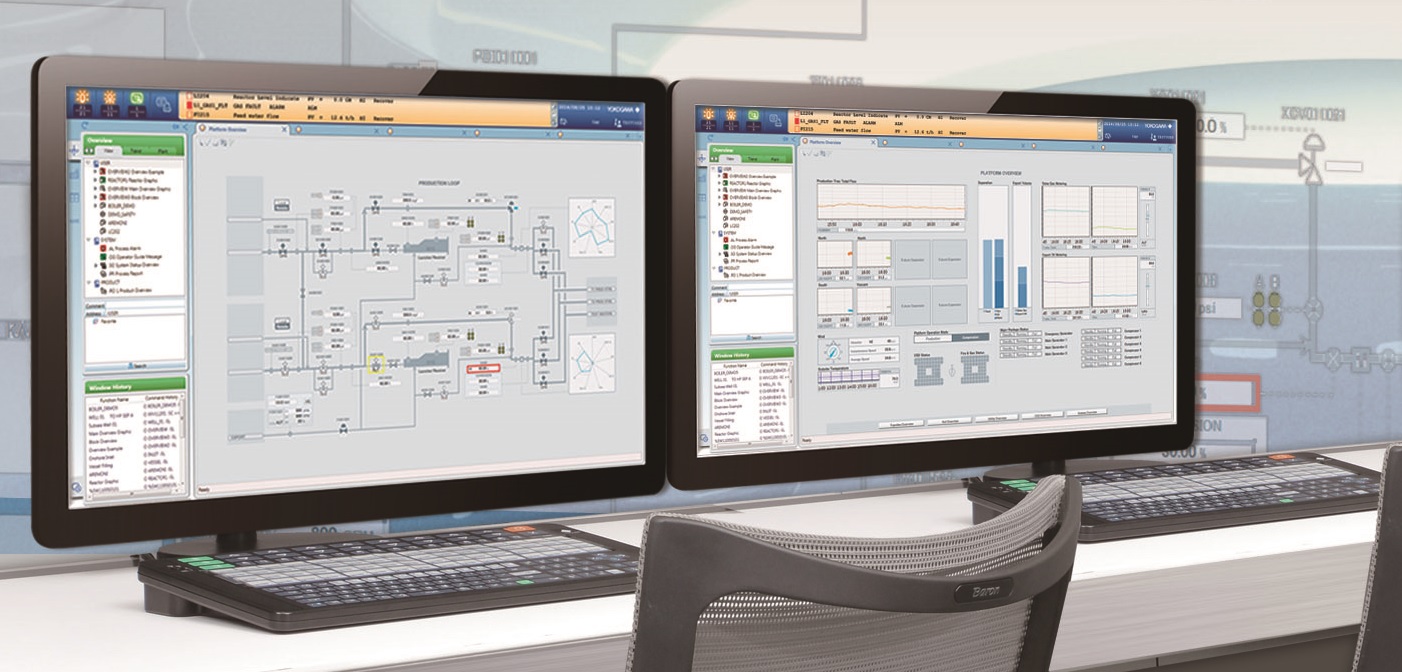

Enabling Technology
The solution not only monitors the status of the integrated system, but also allows remote log-in by experts from anywhere for troubleshooting when a secure link is set up. This removes the constraint of travel, availability, visas, etc. and speeds up site work. The added benefit of advanced diagnostics of integrated field instrumentation is apparent, as experts can analyze this information together with process data and process response. Design flaws can be analyzed and the root cause can be traced more quickly.
These services and solutions dramatically improve maintainability. Owners can now utilize Yokogawa’s superior condition based maintenance to achieve a level whereby shutdowns due to integrated asset failures can be prevented.
Rechercher plus d'informations sur nos compétences, technologies et solutions
Contactez-nous