Introduction
Industrial Combustion sources such as thermal cracking furnaces and, process heaters play a critical role in the process industry. Because the large amount of fuel such as gas or fuel oil which is consumed in these processes, their combustion efficiency directly affects the performance and operational costs of the production facilities.
Incomplete combustion and the use of too much excess air can lead to higher level of toxic emissions such as CO (carbon monoxide), CO2(carbon dioxide), NOx (nitrogen dioxide), and SO2 (sulfur dioxide).
Challenges
Combustion requires fuel and air (oxygen), and insufficient air causes fuel residue, resulting in incomplete combustion with soot and smoke. On the other hand, excessive air caused problems, such as a larger amount of exhaust gas and heating of excessive air, resulting in lower fuel efficiency. Figure 1 shows the principle of the air-fuel ratio and state of combustion. The air-fuel ratio plotted on the horizontal axis shows the ratio of actual supply air to the theoretical amount of air required for fuel combustion (theoretical air amount).
For combustion furnaces such as heating furnaces and boilers in plants and factories, small-scale controllers such as single loop controllers are employed to optimize the air-fuel control ratio for improving the combustion efficiency. In large combustion furnaces, distributed control systems (DCS) and advanced control (multivariable predictive control, etc.) are used. These mainly control the air-fuel ratio and internal pressure of the furnace to prevent CO, CO2 and NOx (nitrogen oxide) from being emitted and apply a cross limit circuit to prevent incomplete combustion while controlling combustion to maximize efficiency.
Figure 1 : Relationship Between Air-Fuel Ration and Heat Efficiency (Combustion)
Solution
Overview of the TDLS8000 Laser Analyzer
Figure 2 shows the appearance of the TDLS8000 laser analyzer. This analyzer measures the process gas component concentration using tunable diode laser absorption spectroscopy (TDLAS), which measures molecule-specific optical absorption spectra. Figure 3 shows an example of using the TDLS8000 to measure the concentration of flue gas.
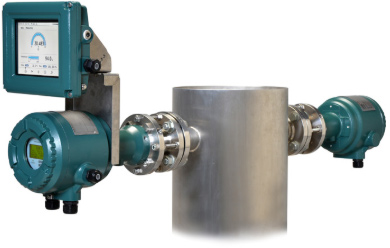
To measure spectra, we employ our originally developed peak area method for accurate measurement even in process environments where the composition, pressure and temperature fluctuate simultaneously. The TDLS8000 suffers no component interference owing to its high spectrum measurement resolution and is directly installed in a process enabling the laser beam to travel through the process windows in a non-contact measurement as shown in Figure 3.
Figure 3 : Installation Example of the TDLS8000
The specific process gas of interest can be reliably measured in near real-time (5 seconds) and at high speed even in high temperature (Max. 1500ºC) or corrosive environments. This advantage enables analysis signals to be utilized directly for process control and management systems, and the TDLS8000 has been rapidly introduced in various industries such as refineries, petrochem, iron and steel and thermal power generation to achieve process improvement and safe operation.
Measurement of O2 and CO Concentrations in Combustion Gas by the TDLS8000
Figure 4 shows an example of using the TDLS8000 analyzer to measure O2 and CO concentrations in a combustion furnace. This example shows that concurrent measurement of O2 and CO concentration while gradually and manually reducing the amount of air supplied to the burner. This experimental data describes the situation; CO generation begun nearly at the O2 concentrations of 2% and sharply increased at the concentration of almost 1.5%, resulting in incomplete combustion, then by increasing the amount of air supply to avoid incomplete combustion, the O2 concentration rapidly increased and the CO concentration decreased again, resulting back to complete combustion. This data also indicated that the CO concentration increased from 100 ppm to 4,000 ppm in just a few minutes.
Figure 4 : O2 and CO Concentration Changes in a Combustion Furnace at Low Oxygen Concentration Operation
Air-Fuel Ratio Control Utilizing CO and O2 Concentrations
According to Lyman F. Gilbert, the CO concentration in the optimum combustion zone (having the highest heat efficiency per unit amount of fuel) is around 200 ppm irrespective of fuel types and devices. However, CO concentration increases rapidly once it has broken through as shown in Figure 4. Thus, either a stable combustion must be kept with sufficient supply of air or a control system must monitor the CO concentration in real-time and keep it constant at a relatively low level.
The amount of air supplied to a burner is controlled by two methods: using a forced draft fan (FD) and damper as shown in Figure 5, or using natural air intake by controlling the opening degree of the damper of an induced draft fan (IDF). The O2 and CO concentrations are measured by the TDLS8000 at the entrance of the flue and then supplied to the control system. The measured CO concentration can be used for combustion control by two methods: controlling O2 when the O2 concentration exceeds a prescribed value and overriding to CO control when the O2 concentration falls below the value, or giving a CO concentration bias (compensation) to the O2 concentration.
Figure 5 : CO and O2 Control System for Combustion Furnaces
Estimation of Economic Effects by Air-Fuel Ratio Improvement
Because the fuel required for generating the same amount of energy can be saved by lowering the set value of O2 concentration in exhaust gas when performing air-fuel ratio control, the direct economic effect by the decrease of O2 concentration in exhaust gas can be estimated. As the economic effects by the improvement, reduction in fuel cost which can be achieved by reducing the excessive O2 while keeping the furnace temperature constant is calculated. Table 1 summarizes a calculation example.1
Table 1 : Example of Economic Effect Calculation by Reducing Excessive Oxygen
*1: Assume to be constant, though it varies depending on the temperature, CO2 concentrations, etc.
*2: (m-l)*A0 is air volume not used for combustion
This example shows a trial calculation for 0.5% reduction of excessive oxygen in the heating furnace of a petroleum normal pressure distillation apparatus(topper) which process oil of 100,000 barrels per day. The result indicates a fuel saving of about 240 kiloliters, worth $113,000 per year assuming a price of $470 per one kiloliter fuel oil.
Furthermore, by reducing the amount of fuel used, CO2 emissions can be reduced. The carbon emission per one kiloliter of fuel is about three tons, so CO2 emissions are reduced by 720 tons per year.
Safety Control by the TDLS8000
A burner management system (BMS) safely controls the burner of the combustion furnace and includes an interlock mechanism and a safety shut-off mechanism to prevent explosion. The BMS must comply with safety standards based on risk assessment such as the international standard (ISO12100) and the EU, USA and Japanese standards (EU standard: EN746, USQ standard: NFPA86, Japanese standard: JIS B9700).
Because the TDLS8000 monitors the CO concentration in near real-time, it increases the reliability of the safety system by inputting a signal of the detected CO concentration to the BMS and is expected for implementing the defined safety requirements. Figure 6 shows a typical system configuration in which the CO measurement capability is added to the BMS burner shut-off system. Yokogawa’s ProSafe-RS integrated safety instrumented system can be employed as the BMS.
Figure 6 : Safety Control in the Burner Control Equipment
In addition to the measurement of CO the TDLS8000 can accurately measure CH4 (Methane) levels providing an extra level of safety during start up where a flame out or a failed burner ignition can cause an explosion.
Conclusion
The TDLS8000 is attracting considerable attention from many refinery and petrochemical plants because it requires little maintenance and can measure the concentrations of O2/CO/ CH4 in the furnace in near real-time.
The technology for combustion efficiency optimization, by measuring O2 can CO concentrations in this application note was established more than twenty years ago.
The TDLS8000 provides a near real time measurement of O2/CO/CH4 in the radiant section of a large scale combustion furnaces and process heaters allowing process owners an unprecedented opportunity to optimize combustion.
Product Recommendations
TDLS 200 (O2/CO/CH4 analyzer)
Note: Various options are available please consult your local Yokogawa Sales Office for more information.
Notes
- Response time: 2-5 seconds
- Process pressure up to 20 bar
- Interference Free
- Process temperature up to 1500ºC
- TruePeak Measurement
- Optical Measurement- No sensor contact with process
References:
- Tsuneo, Hiraoka, “Reduction of Fuel Costs and CO2 Control for Packaged Boilers,” Yokogawa Technical Report, Vol. 44, No. 2, 2000, pp. 85-86 in Japanese
- American Petroleum Institute, “Instrumentation, Control & Protective Systems for Gas Fired Heaters”, API 556 2nd edition, April, 2011.
Industrien
-
Offshore (FPSO FLNG & FSRU)
Offshore exploration and production requires maximum uptime under harsh conditions. Manned and unmanned facilities need reliable integrated control and safety systems (ICSS) with advanced remote monitoring capabilities. Yokogawa has state-of-the-art technology and extensive experience in executing offshore projects of all sizes and automation levels of complexity.
-
Oil & Gas Downstream
The oil & gas downstream industry has been facing an increasing number of challenges in recent years. These include the changing characteristics of the feedstock to be processed, aging of process facilities and equipment, rising cost of energy, lack of skilled plant operators who can run a refinery safely and efficiently, and the ever-changing requirements from both the market and the customer.
Over the years, Yokogawa has partnered with many downstream companies to provide industrial solutions focused on solving these challenges and problems. Yokogawa's VigilantPlant solutions have helped plant owners to achieve maximum profitability and sustainable safety within their plants.
-
Petrochemical
Petrochemical companies’ needs are extremely diverse. To come out ahead in today’s highly competitive marketplace, producers are striving to improve quality and productivity. Yokogawa provides tailor-made solutions for these needs based on its long and wide-ranging experience in this field.
-
Power
In the mid 1970s, Yokogawa entered the power business with the release of the EBS Electric Control System. Since then, Yokogawa has steadfastly continued with the development of our technologies and capabilities for providing the best services and solutions to our customers worldwide.
Yokogawa has operated the global power solutions network to play a more active role in the dynamic global power market. This has allowed closer teamwork within Yokogawa, bringing together our global resources and industry know-how. Yokogawa's power industry experts work together to bring each customer the solution that best suits their sophisticated requirements.
-
Refining
In the ever changing marketplace, refineries are seen not only as crude processing units but also as profit centers. At the same time, there is a keen awareness of the need for safety at such facilities. A total production solution that encompasses planning, scheduling, management, and control is required to achieve long-term goals for profitability, efficiency, and environmental protection. With years of expertise in the automation field, Yokogawa can bring you affordable total solutions for improved operability and a cleaner world.
-
Specialty & Fine Chemical
This page introduces Yokogawa's messages and solutions for the Specialty and Fine Chemicals industry, showcasing our specialized offerings and expertise.
-
Thermal
Thermal power using coal, oil or gas as fuel accounts for the majority of electric generation throughout the world.
-
Upstream
The upstream industry includes offshore and onshore activities including wellhead automation, fractionation, completion, and separation to recover and prepare underground or underwater crude oil and natural gas.
As petroleum is brought to the surface, it must be separated prior to transport. Primary and secondary separation stages commonly distribute gas flow, water flow, and oil flow in three phase separation. Gas movement requires pipeline and can include a fractionation process in the upstream stage prior to movement. Liquids can be placed into a tanks or pipelines and sent for processing, requiring accurate level measurements.
Zugehörige Produkte & Lösungen
-
In-situ-Gasanalysator TDLS8000
Yokogawas neuer TDLS™8000 beinhaltet alle führenden Laser-Spektroskopie-Analysetechnologien in einem einzigen robusten Gerät. Das Plattform-Design eignet sich besonders gut für In-situ-Messungen und macht Probenentnahme- oder -aufbereitungssysteme überflüssig.
-
Spektrometer mit durchstimmbarem Diodenlaser (TDLS)
Das Spektrometer mit durchstimmbarem Diodenlaser (Tunable Diode Laser Spectrometer – TDLS) ist ein lasergestützter Gasanalysator, der eine optische Analyse in kurzen Abständen ermöglicht.