An autonomous plant requires more than just technology
Artificial intelligence, digitalization, robotization, and smart industry. These are new technologies that are changing society and also the industrial sector. There are visions of fully autonomous factories and plants that automatically network with other parties in the value chain. The technology is there, but application in practice is proving to be difficult.
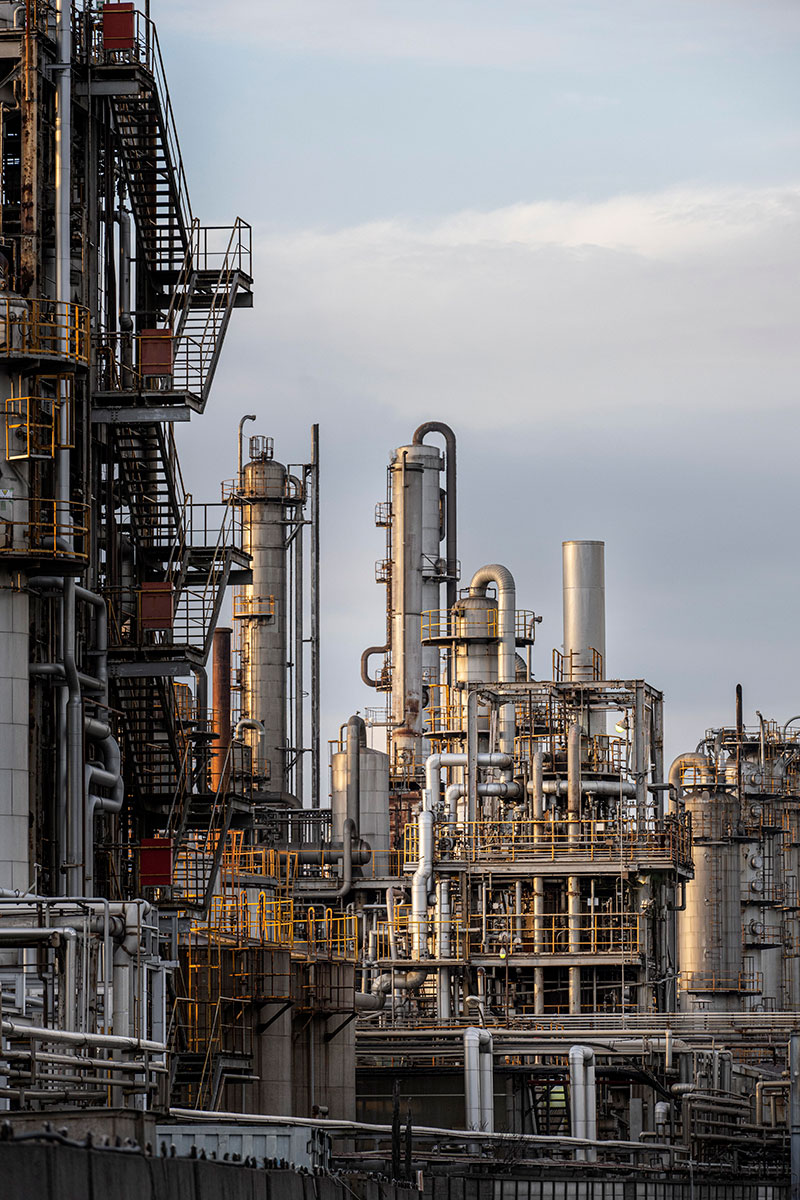
The world of industrial automation (OT) has always been different from the world of office automation (IT), says Patrick Kools, director of Clean Energy at Yokogawa. 'IT is about the availability of information and convenience. In factory automation process continuity is paramount, and with it, safety and data reliability. This leads to different priorities and process designs.' According to Bert Looman, who works as a solution architect at Emerson on projects in oil, gas, chemicals and renewables, industry is a decade behind the IT sector. 'We're just starting to send data to the Cloud, while for IT everything is already in the Cloud. In IT, hardware is replaced every three years, while in industry, it needs to last at least 15 years. This also means that the renewal of systems is slower.' With the rise of Cloud and Edge systems, there has been a shift in architecture in recent years to the use of sensors that send data to a cloud. As a consequence, all kinds of applications will come into being that can be used to optimise things such as energy, production and safety. 'There are still limits to this, however', Kools argues. 'Data collection to determine when to carry out maintenance can be done via the Cloud, but the software to control the plant is not yet in the Cloud. Instead, an on-premises setup is chosen because everything has to work at all times.'
Acceptance
Looman also notes that it takes a long time for new technologies to gain acceptance in the marketplace. For the past 25 years, he has been involved in process automation, although he says that the term doesn't fully cover it. 'They have mostly been process control systems and not automation systems. With process control, we give operators a control system that allows them to control the plant. But automation allows processes or plants to operate more autonomously.'
The reluctance to adopt this technology largely has to do with safety, according to both experts. 'In our industry, the focus is on safety and control systems. There is a lot of reliance on the operator taking action when an alarm goes off, whereas a computer can analyse very well what is going wrong and take action. We have only partially realized those applications,' says Looman.
Autonomous Plants
At Shell, we are working toward being able to remotely control the plants and operate as much autonomously as possible. 'This will contribute to a safer and more sustainable business, moving towards Industry 4.0,' states Rinda Witteman. She is Enterprise Architect Assets at Shell and works on the company's digital strategy. Shell's goal is to be a net-zero emissions business by 2050 at the latest. Witteman emphasizes the importance of digitalization for achieving this corporate goal. 'The challenge is to achieve net-zero emissions while the worldwide demand for energy
Digital transformation is crucial to bring about the change that is needed. Data and artificial intelligence can help ensure that energy needs and generation are well matched.'
Shell is not the only company striving for as many autonomous plants as possible, but in practice developments are slow and there are still steps to be taken. Kools notes: 'There is a difference between something that is highly automated, where, for example, two people can control 15 plants remotely, and autonomy with intelligent algorithms that can control parts or sections or the entire process in a closed loop.'
In 2022, Yokogawa conducted an artificial intelligence trial in which a chemical plant ran autonomously for 35 days. Kools: 'It was a complex process consisting of multiple processes with similar boiling points. The results were largely positive but there were some snags. Production went well. The products were of good quality, and fuel, labor, and time were all saved. But sudden temperature changes in the atmosphere required human intervention.'
'The open standards will make it easier to integrate the options of the new technology.'
RINDA WITTEMAN ENTERPRISE ARCHITECT ASSETS SHELL
Value Chain
Kools expects that developments will not stop at autonomous processes. 'Plants are part of the value chain and you want that plant not only to manage the process well but also to be able to liaise with inbound logistics when inventory needs to be replenished. You want the entire chain to be digitalized and data to be available in a good way so that the plant can share it throughout the supply chain to optimize it.'
Renewal
The energy transition is a major driver of innovation with the construction of new plants. The focus here must then be on the digital design around which the physical plant is built. Many start-ups' business model is to build a pilot plant that then serves as a blueprint for the rollout of several similar plants. Examples include Holland Hydrogen, Avantium, and France's Lhyfe, which developed a business model for more than a hundred similar plants. Kools: 'These plants are becoming smaller and more distributed, and they need to operate remotely. You have to think carefully about maintenance and management. Questions that arise here include: Do you let such a plant operate unmanned or do you manage and maintain it remotely? What about cybersecurity and security? All digital issues to consider.' He sometimes sees a focus at the first plant on being as commercially efficient as possible, rather than on learning as much as possible and creating the right blueprint. The latter is more expensive at first but pays for itself when upscaled. Looman also sees that start-ups are primarily focused on making their first plant a reality. 'When I ask: "What's your plan for optimization or reusing data when you go on to develop the second plant?", there is generally no strategy for that yet.'
Time Pressure
According to Kools, the time pressure placed on the energy transition also leads to safe choices. 'Large parties building industrial plants talk for a long time about an investment decision. Then the project is transferred to the Capital Projects Department and engineering for construction. If the plant needs to be built quickly, all the risks are removed. They fall back on the existing blueprint with existing suppliers and existing methods to make sure that the plant is built.' There is tension between speed, the things we want to do, and the opportunities available, Kools argues. 'Many possibilities have been known about for some time, but have not yet been widely applied. It is difficult, when speed is key, to deliver a good blueprint for a smart factory with technologies that are not all proven yet, but that we can still use in the future.
Automation is an end product of thinking about how you want to work. As an industry, we have longstanding experience with refineries, but not with operating remotely with artificial intelligence. That means going back to the drawing board with automation specialists and operations, to see how you want to operate and maintain the plant. Which tools do you need to have an autonomous plant, to be able to operate it remotely, and how are you going to maintain it?'
Unlocking Data
Much production, maintenance, and equipment data is locked into specific applications. According to Bert Looman of Emerson, that data needs to be unlocked and brought to a Cloud environment. 'That way you create a data lake that allows us to do analysis through machine learning or through an experienced operator analyzing the data. It can also be a dynamic model that tells you the equipment isn't working properly and therefore needs maintenance. We see systems getting more and more data. We are making them smarter, so there is more and more data coming, but putting it all together is still a puzzle.'
An additional complicating factor is that many different specialisms are involved, such as safety, quality, maintenance, reliability, electric switchgear specialists, and so on. These need to be brought together in the IT domain to see the correlation between data from different systems.
'There is a lot of reliance on the operator, whereas a computer can analyze very well what is going wrong and take action.'
BERT LOOMAN SOLUTION ARCHITECT EMERSON
Companies such as Avantium build a pilot plant that then serves as a blueprint for the rollout of several similar plants. How can you juxtapose as many parties as possible for this plant in order to create a good blueprint for subsequent plants?
Standardization
Witteman argues from practical experience that the remote control of a plant is a complex issue where all the pieces of the puzzle must fall into place. 'The world of operational technology has to be properly connected to the world of IT. Properly here means safe in terms of cyber security, integrated in terms of data and speed, and accurate so that correct representation is used to make or prepare decisions. The OT is part of the installations, and each vendor has its own protocols, making it difficult for systems from different vendors to communicate with each other. For a small installation, this may not be such a problem because you can deal with just one supplier. However, for companies with Shell's IT complexity, this becomes impractical, because we work with a lot of vendors.'
The only way to powerfully connect OT and IT and create a plant that is as autonomous as possible, according to Witteman, is through standardization. 'The industry has agreed on open standards - OPAS and OPC-CUA. We require that all new apparatus meets these standards whenever possible. We are convinced that as an industry we need to join forces and embrace standards together. The open standards will make it easier to integrate the new technology and its options. Product-based working brings together not only Shell and the suppliers but also the various disciplines within Shell. An iterative way of working allows innovation to be embraced faster. In addition, knowledge-sharing is crucial.' New technology such as artificial intelligence and data platforms, according to Witteman, form the basis for the digital twin for generating operational advice and decisions. 'The amount of data from OT is immense and building an accurate digital twin is complex. A major limitation here is the absence of enough experts in this field of work and especially in the area of open standards.'
'Automation is an end product of thinking about how you want to work.'
PATRICK KOOLS DIRECTOR CLEAN ENERGY YOKOGAWA
Saving Time
The question arises as to how you can save time by incorporating flexibility in the design of a new plant to enable the switch to automation at a later date. Kools: 'I think we as an industry have a short period of time in which we need to learn a lot very quickly and then we have to become efficient again as regards rollout. Make sure that for your first projects, you don't immediately go for process efficiency and the lowest price, but instead try to juxtapose as many parties as possible for the new plant in order to work everything out and create a good blueprint for your subsequent plants. When building plants no. 2 or 3, you then start making improvements in order to scale up and become more commercial.'
For his many hydrogen projects, Looman sees more standardisation as part of the solution. 'That way, less project-specific engineering is needed, which helps with project realisation. One example are the suppliers of industrial gases such as nitrogen - Air Liquide, Air Products, Linde - who install standard air separation units at customers' premises and then control them remotely.'
ilgili Ürünler & Çözümler
-
IA2IA
IA2IA is what Yokogawa foresees as the transition from Industrial Automation to Industrial Autonomy.