A State-of-the-Art Gas Chromatograph (GC) to Help Streamline Plant Operations
The Process Gas Chromatograph GC8000 is a state-of-the-art process gas chromatograph (process GC) that separates out multi-component mixtures of gases or volatile liquids into individual components for detection. The newly developed GC module enables analysis under optimal conditions for each component, such as parallel gas chromatography for multiple simultaneous analyses and the high-precision analysis required in the fine chemicals field.
Unlike laboratory gas chromatograph (lab GC), which mainly perform batch analyses with manual operation, process gas chromatographs fully automate continuous analysis in the manufacturing process. This addresses issues such as labor-intensive analysis, chronic personnel shortages, and increased costs, thereby contributing to more efficient plant operations.
In 2023, Yokogawa will start offering gas chromatograph AI maintenance support (GCAI), in which AI continuously monitors the GC8000 and reads changes in measurement status and signs of abnormality. The results of the AI analysis are used to perform maintenance and prevent problems before they occur, leading to stable plant operation.
> Gas Chromatograph AI Maintenance Support (GCAI)
The GC8000 meets the following needs:
- Freedom from routine tasks involved in manual analysis
- Avoiding inconsistency in sample collection
- Saving costs for operation and maintenance
- Improving reproducibility in high-precision analysis
The Process Gas Chromatograph GC8000 has features that make it more suitable for use in plants than typical laboratory gas chromatographs. Here are some of the benefits the GC8000 brings to plant operations.
Labor savings through automation of continuous analysis
The GC8000 is an industry-leading process gas chromatograph that can perform highly difficult measurements at the several hundred to several thousand ppm level in the fine chemicals field. Analysis of pre-set components to be measured is fully automated and performed continuously 24 hours a day.
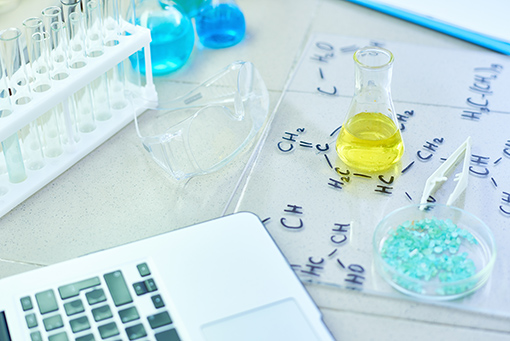
Unlike laboratory gas chromatographs, which are used in laboratories, etc. away from the work floor, the GC8000 is used close to the manufacturing process, eliminating the need for laborious manual analysis, including sampling and transportation, and thus allowing for significant labor and manpower savings. In addition, freeing operators from the routine tasks of manual analysis allows them to devote more time to more important analytical work.
Improved quality through high reproducibility and consistency
A typical laboratory gas chromatograph involves a series of manual operations: sampling from a mixture, transport, pretreatment, injection, and analysis. However, in recent years, there has been an increasing concern about the variability and degradation of work quality owing to a decreasing number of skilled workers.
The GC8000, on the other hand, allows the components to be measured and their appropriate concentrations to be pre-set for each manufacturing process, providing fully automated, continuous analysis of their respective amounts. Because it is not dependent on the experience and knowledge of the operator, it can improve reproducibility and consistency in the high-precision analysis required in the fine chemicals field. In addition, continuous analysis in 24-hour operation enables rapid detection of defects and irregularities, contributing to improved product quality at plants.
Reduction of running costs, etc.
Full automation of continuous analysis in the manufacturing process reduces three-shift labor costs and work-hours spent on manual analysis and reporting. As such, the GC8000 contributes to reductions in running costs, etc. over the medium to long term. The frequency of analysis is higher than that of laboratory gas chromatographs, which allows for quicker detection and handling of defects and irregularities, thereby reducing costs associated with the disposal of defective product.
In some cases, the pass standards for laboratory gas chromatographs are set higher in analytical results to account for the variability and delay time resulting from manual analysis. On the other hand, the GC8000, which can perform the analysis fully automatically, minimizes the risk caused by variability and delay time.
Plant-wide optimization
The GC8000 can be linked to integrated control systems and distributed control systems (DCS). Yokogawa's CENTUM VP integrated production control system is made up of a variety of functions related to plant operations, including operational monitoring, control, engineering, field digital, and security. It provides an optimal operating and engineering environment throughout the entire lifecycle of a plant, from plant design to the end of operation.
By using the GC8000 in conjunction with CENTUM VP, analytical results from manufacturing processes can be quickly shared and reflected in equipment control. The ability to respond quickly to the occurrence of defects and irregularities leads to stable product quality and more efficient maintenance, accelerating plant-wide optimization.
About OpreX
OpreX is the comprehensive brand for Yokogawa’s industrial automation (IA) and control business and stands for excellence in the related technology and solutions. It consists of categories and families under each category. This product belongs to the OpreX Analyzers family that is aligned under the OpreX Measurement category.
Details
The Process Gas Chromatograph GC8000 offers five major advantages.
1. High-speed analysis with a multi-oven structure
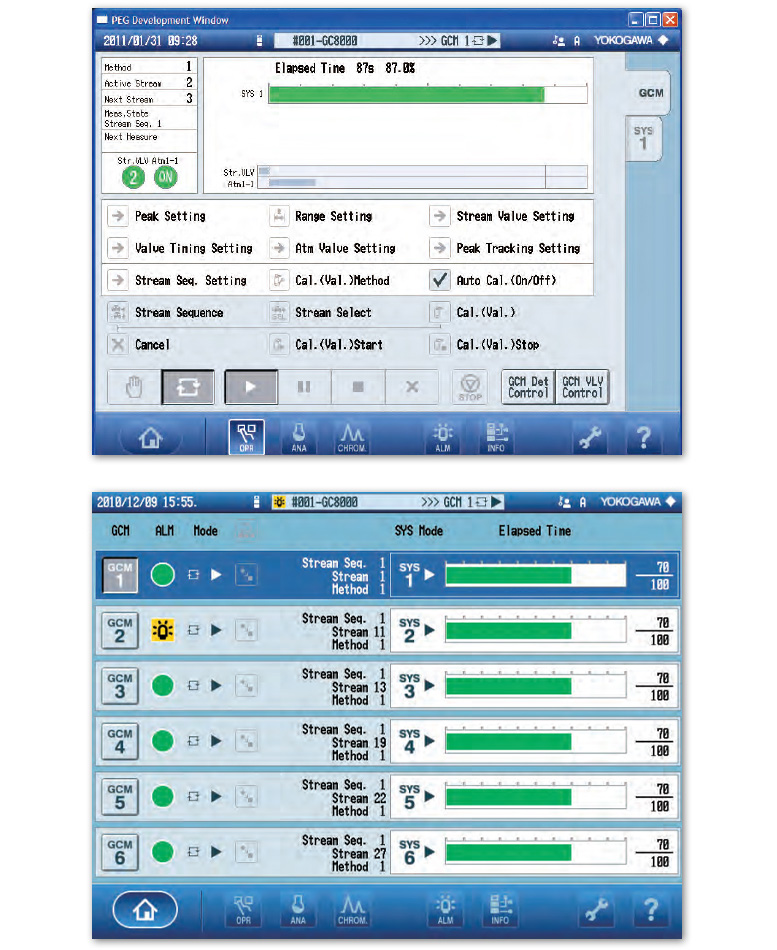
The GC8000 can be configured with multiple GC modules to form a single system, as though it were equipped with multiple gas chromatographs. This enables shorter analysis times and flexible configurations of instruments tailored to customers’ needs.
The GC module consists of valves, columns, detectors, etc., and also allows for independent analysis cycles, oven temperatures, etc. As a result, not only can parallel gas chromatography be used to analyze multiple components simultaneously, but complex applications can be divided into smaller units for analysis under optimal conditions.
2. Improved operation with a touch panel
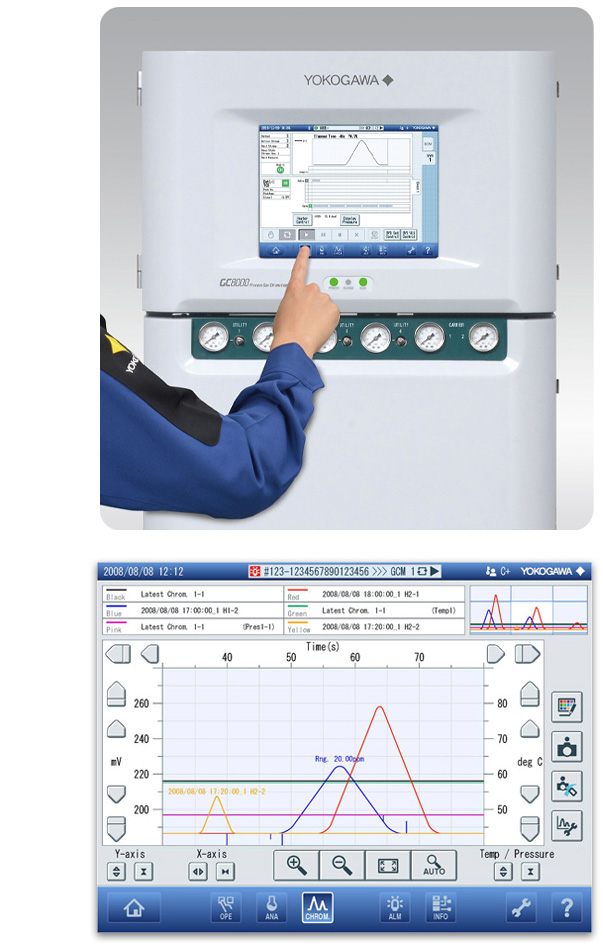
The GC8000 is equipped with a large 12-inch color touch panel with graphical display for easy operation and maintenance.
Analysis parameters and results can be easily viewed on site by simply touching the screen. The overview screen clearly displays important parameters and trend data, making it easy to determine the device’s measurement status. Furthermore, the system configuration is displayed graphically, making it easy to understand even for first-time users of the GC8000 and reducing the time required for operation and proficiency.
3. Flexible and secure networking
For communication networking, the GC8000 is equipped with an Ethernet connection as standard. This allows flexible and secure data transmission to and from GC workstations and distributed control systems (DCS) via PC. Network redundancy is also supported.
Thanks to the use of the Modbus TCP/IP protocol, in many cases a communication gateway is not required to connect to DCS devices. This not only simplifies the network configuration, but also reduces the risk of potential communication failures. For communication systems requiring a serial Modbus gateway, Yokogawa’s ASGW is used.
GC Workstation Configuration Diagram
PCAS Analyzer Server:
collects data from multiple gas chromatographs, performs command control and data communication to and from host systems.
ASET Engineering Terminal:
connects to multiple gas chromatographs via the analyzer server. Performs analyzer monitoring and maintenance via PC.
ASGW Analyzer Server Gateway:
gateway between multiple gas chromatographs and the host system.
Gas Chromatograph AI Maintenance Support (GCAI):
AI-equipped software continuously monitors the GC8000's gas chromatograms to detect signs of deviation from normal conditions and to predict the future separation states of measurement peaks.
4. Reliable preventive maintenance with state-of-the-art maintenance software
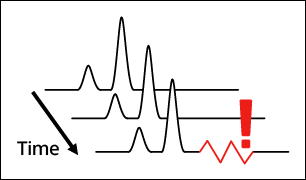
Gas Chromatograph AI Maintenance Support (GCAI) is maintenance software that improves the reliability of the GC8000 and enables preventive maintenance based on monitoring data.
In particular, GCAI uses AI to achieve predictive detection via constant monitoring of chromatograms. A machine learning model built on GCAI detects anomalies (abnormalities) in chromatograms in real time and notifies the appropriate personnel. This makes it possible to plan maintenance measures such as part and column replacement in accordance with changes in the separation states of measurement peaks, helping to ensure highly reliable preventive maintenance.
*PCAS analyzer server software is required for GCAI operation.
> Gas Chromatograph AI Maintenance Support (GCAI))
5. Highly accurate and reliable process analysis
Over more than 50 years, Yokogawa has continued to provide highly accurate and reliable process gas chromatographs. The GC8000 continues to use key components, such as detectors and valves, for which we have amassed a wealth of experience and expertise. This allows for highly reliable use with peace of mind, as well as the shared use of serviceable parts with existing Yokogawa products.
In addition, combining various types of ovens makes it easy to optimize analysis and expand applications. By optimizing the combination of GC modules and ovens to meet customers’ analytical needs, even complex analyses can be simplified, leading to improved serviceability.
Oven temperature control
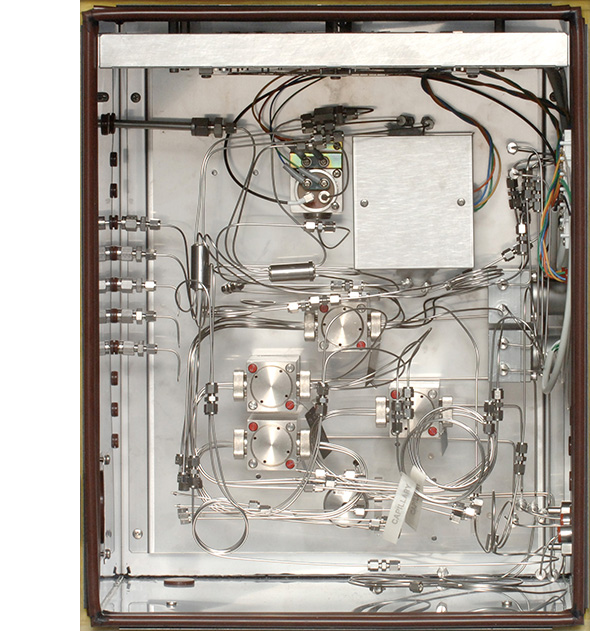
Thanks to its outstanding oven temperature control technology, the GC8000 provides excellent repeatability and long-term stability, even in harsh operating environments.
Fans in the isothermal ovens uniformly agitate the air inside to achieve the world’s highest level of temperature control relative to the set temperature. In addition, pressure reducing valves are also installed in the isothermal ovens to ensure stable carrier gas flow.
Detectors
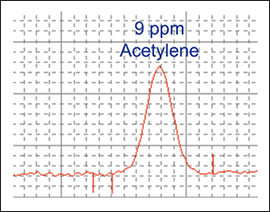
The GC8000 also uses innovative technology in its detectors.
Its thermal conductivity detectors (TCD) have the highest sensitivity in the world and are often used for measurements at the several ppm level, which would otherwise require the use of a hydrogen flame ionization detector (FID). The hydrogen flame ionization detector (FID) offers excellent long-term stability and can be re-ignited with the push of a button without changing the air-fuel ratio.
6.A New Platform for DX Solutions
Optional built-in Wireless LAN port* in GC8000 Type 6 enables GC operation using Ex Tablet PC in hazardous area at site.
Engineering terminal on the tablet PC provides more useful functions than HMI; including connection to analyzer servers, checking historical data and monitoring of any GC8000 in the network.
Real-time support by a remote specialist is also available thru the Tablet PC using video communication tools.
Accessibility to the maintenance records and other service references is also possible.
*Wireless LAN port is available for USA, China and EU. Alternative solution using Remote Desktop shall be used in other regions.
Specifications
A summary of the Process Gas Chromatograph GC8000’s specifications is presented below.
Measurable objects | Gases or volatile liquids (400°C or lower boiling point) |
---|---|
Analysis method | Gas chromatography |
Measurable range | TCD: 1 ppm to 100% MTCD: 1 ppm to 100% FID: 1 ppm to 100% FID with methanizer: 1 ppm to 0.1% FPD: 1 ppm to 0.1% |
Number of components to be measured | Maximum of 999 (total number of components in all streams including calibration standard sample stream) |
Analysis period | Maximum of 21600.0 seconds (six hours) |
Number of streams to be measured | Maximum of 31 (including calibration standard sample stream) |
Material of sample-contact parts | RV: 316SS, Hastelloy-C, Rulon, PTFE (Teflon, Bearee) LSV: 316SS, Hastelloy-C, Rulon, PTFE (Teflon, Bearee), Glass, Fluororubber (Viton), perfloroelastomer (Kalrez) |
Repeatability | Depends on analysis conditions. Gas sample: ±1% of full scale for measuring ranges (2σ) Liquid sample: ±2% of full scale for measuring ranges (2σ) |
Analyzer
Type of protection | Pressurized enclosure, flame proof enclosure, increased safety, intrinsic safety and type of protection Certification standard: TIIS, FM, CSA, ATEX (DEKRA), IECEx (DEKRA), NEPSI TIIS: Ex pd IIB+H2 T1 to T4 FM/CSA: Type X Pressurization and Explosionproof for Class I, Division 1, Groups B, C and D. T1 to T4 Type X and Y Pressurization for Class I, Division 1, Groups B, C and D. T1 to T4 ATEX: II2G Ex db pxb IIB+H2 T1, T2, T3 or T4 Gb II2G Ex db ec ic nC pxb pyb IIB+H2 T3 or T4 Gb IECEx: Ex db pxb IIB+H2 T1, T2, T3 or T4 Gb Ex db ec ic nC pxb pyb IIB+H2 T3 or T4 Gb NEPSI: Ex db pxb IIB+H2 T1, T2, T3 or T4 Gb Ex db ec ic nC pxb pyb IIB+H2 T3 or T4 Gb |
||
---|---|---|---|
Protection degree of enclosure | Type 3R (ANSI/UL 50E, CSA C22.2 No. 94.2) 、Equivalent to IP54 (IEC 60529) (dust and water resistant structure) | ||
Ambient condition during operation | -10 to 50°C, 95 % RH or less (no condensation) Depends on analysis conditions. |
||
Weight | Wall-mounting version | Self-standing version | |
Type 1 | Approx. 100 kg | Approx. 140 kg | |
Type 2 | Approx. 155 kg | Approx. 190 kg | |
Type 3 | Approx. 200 kg | Approx. 220 kg | |
Type 4 | Approx. 140 kg | Approx. 170 kg | |
Type 5 | Approx. 175 kg | Approx. 195 kg | |
Type 6 | Approx. 85 kg | - |
Isothermal Oven / Programmed Temperature Oven
Volume | Large isothermal oven: Approx 45 L, Isothermal oven: Approx 31 L |
---|---|
Oven temperature range | Type1 to 5 : 55 to 225°C Type 6 : 55 to 135°C (Temperature can be set in one-degree step.) |
Temperature stability | ±0.03°C* *Reference value |
Temperature control | PID |
Input and Output
Analog Input/Output | Maximum of 16/Maximum of 32 |
---|---|
Contact Input/Output | Maximum of 32/Maximum of 20 |
PC communication | Ethernet communication |
DCS communication | RS422 Protocol: MODBUS, Y-Protocol, BTU for Japan Ethernet communication Protocol: Modbus/TCP |
Utility
Power supply | Type 1, 2, 3, 5, 6: 100/110/115/120/200/220/230/240 V AC, ±10%, 50/60 Hz ±5% Type 4: 200/220/230/240 V AC, ±10%, 50/60 Hz ±5% Note: Depends on analysis conditions. Protection devices, such as a breaker, are required to avoid overcurrent. |
---|---|
Maximum rated power | Type 1: 0.8 to 1.6 kVA, Type 2: 1.4 to 2.9 kVA, Type 3: 2.0 to 4.3 kVA, Type 4: 1.7 to 3.7 kVA Type 5: 1.9 to 3.0 kVA, Type 6: 0.8 to 1.2 kVA |
Instrument air | Pressure: 350 to 900 kPa, 500 to 900 kPa (with FPD) 350 to 900 kPa (Programmed temperature oven without cooler), 500 to 900 kPa (Programmed temperature oven with cooler) Maximum flowrate: Type 1: 140 L/min, 440 L/min (with FPD) (280 L/min typ. at Tamb=25℃) Type 2: 210 L/min, 510 L/min (with FPD) (340 L/min typ. at Tamb=25℃) Type 3: 280 L/min Type 4: 210 to 600 L/min (depends on specifications) Type 5: 210 L/min, 510 L/min (with 1 FPD)(340 L/min typ. at Tamb=25℃) , 870 L/min (with 2 FPDs)(550 L/min typ. at Tamb=25℃) Type 6: 70 L/min typ. (85 L/min max) |
Carrier gas | Types: H2, N2, He, or Ar Purity: Measuring range from 0 to 50 ppm or more: 99.99% minimum (water: 10 ppm or less, organic components: 5 ppm or less) Measuring range from 0 to less than 50 ppm: 99.999% minimum (water: 5 ppm or less, organic components: 0.1 ppm or less) Pressure: H2: 500 ±20 kPa (to meet explosion-proof requirements, install a separate pressure reducing valve and supply at 500 kPa) Other than H2: 400 to 700 kPa Consumption: 60 to 300 mL/min per oven |
Industry Applications Supported by Process Gas Chromatographs
The Process Gas Chromatograph GC8000 can be used for the maintenance and control of various types of product quality assurance and production facilities.
Chemical
Chemical plants produce a variety of substances through manufacturing processes involving chemical reactions. Recent years have seen ever-increasing needs in the field of fine chemicals, which is characterized by high functionality and high value-added. However, because of these chemicals’ complex compositions, advanced process control is essential during manufacturing.
The gas chromatographs used in chemical plants must be flexible enough to handle a wide variety of substances, provide high-precision analysis, and offer real-time control through interfacing with other instruments. With the latest advances in technology, process gas chromatographs are able to meet these requirements and are increasingly being installed in chemical plants.
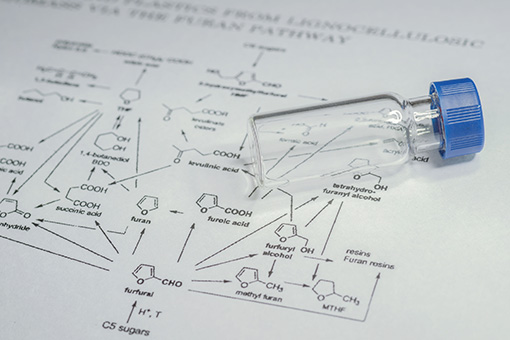
Example applications: alcohols, aldehydes, esters, vinyl, halides, phenols, cyclic olefin
Petrochemicals
The petrochemical industry produces chemicals used in many everyday products, including plastics, detergents, fertilizers, and pesticides. The largest segment in this industry is the production of various plastics and synthetic resins that are used extensively throughout modern society. Plastics and synthetic resins are made by polymerizing compounds to form long chains of molecules.
The process gas chromatographs used in the petrochemical industry must analyze compounds that are difficult to detect. Typically, these analyzers are built using a combination of highly sensitive detectors, advanced column technology, specialized hardware, and new materials.
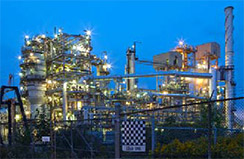
Example applications: ethylene, polypropylene, polyethylene, BTX, butadiene, vinyl chloride, styrene, alcohol, aldehyde, ester, and vinyl acetate
Petroleum refining
The gasoline produced in refineries has supported the development of modern society as a source of power for automobiles. Refineries separate out the small amounts of natural gasoline contained in crude oil, then react the remaining chemicals to convert them into gasoline. For example, the chemical octane is produced by reacting two C4 molecules with each other in a refinery’s alkylation unit. Components with molecular weights too large to be used in gasoline are removed by other equipment and then broken apart by catalytic cracking or thermal decomposition.
Because these chemical reactions occur simultaneously, on-line monitoring and control are extremely important. Indeed, process gas chromatographs have been installed in refineries on a large scale.
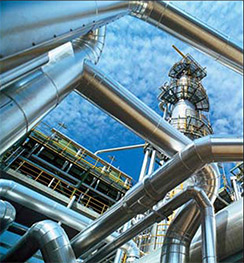
Example applications: distillation point analysis, PINA/PIONA analysis, FCC, sulfur recovery
Natural gas
Industries involved in the processing of natural gas are responsible for supplying the large quantities of natural gas consumed every day. During this process, the BTU value and composition of the gas are monitored using process gas chromatography.
The requirements of the natural gas processing industry are very different from those of other industries. Although the analytical aspect is relatively simple, the environmental requirements are very demanding. In addition, because the monitoring personnel are often located far away from the analyzers monitoring the natural gas, and the analyzers are installed over wide areas, remote communication is required.
Analysis applications: BTU analysis
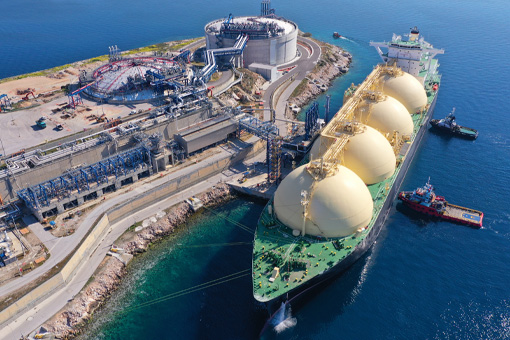
Environmental monitoring
The environmental monitoring market has grown out of the need to create safe working environments and minimize industry’s impact on the environment. Monitoring is necessary to prevent accidents and spills caused by chemicals and to ensure that hazardous materials are disposed of safely and reliably.
Process gas chromatographs are used for automated monitoring of some contaminants in wastewater, as well as air, water, and chemical processes. Process gas chromatographs in the environmental monitoring market must be able to accurately determine strict environmental standards, and also be capable of making measurements at multiple sites and recording data.
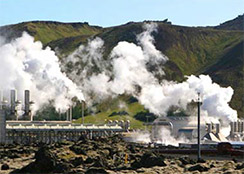
Example applications: Air/soil pollution monitoring, plant/work environmental analyses, water quality analysis (VOC)
Resources
GC8000 was selected to detect components responsible for stainless steel corrosion of pipeline.
GC8000 with custom container analyzes crude oil components every 4 mins at an offshore platform.
- Fast online gas chromatograph (GC) analysis for LPG distillation.
- The analytical upgrade project with Yokogawa's process GCs was complete success.
AN10B02D01-01EN
GC8000, CENTUM VP
High volumes of volatile organic compounds (VOCs), typified by trichloroethylene and tetrachloroethylene, have long been used in various industrial fields for their high degrees of industrial usefulness. On the other hand, there is a growing awareness of environment preservation today, and of the fact that we face serious environmental pollution due to such harmful VOCs.
In recent years, shale gas extraction technology has made rapid progress, inducing a shale gas revolution mainly in the USA. Thus, the need for analysis of hydrocarbon gases, including natural gas, is expected to grow rapidly. Traditionally gas chromatography has been used for the analysis of hydrocarbon gases; it can accurately measure the concentration of each hydrocarbon component in a sample of natural gas.
Control Engineering Asia, May 2012
An exception level of engineering expertise tailored for the local market is one of the primary reasons why Yokogawa has managed to capture and keep the process automation top spot in the Land of Smiles, says Somkid Teraboonchaikul, managing director, Yokogawa Thailand.
Loek van Eijck, Yokogawa, The Netherlands, questions whether rapid analysis of gases and liquids can be better achieved through use of a gas chromatograph or near infrared analyser. Conventionally, the liquid and gas components such as those broken down by naphtha crackers have been measured by a process gas chromatograph (PGC), with the subsequent measurement values then being used for control purposes.
The EPA rule, 40 CFR 63 Subparts CC and UUU, is forcing refineries to monitor flares. Fortunately, modern analyzer technology makes it possible to meet the requirements, generate the necessary reports, and stay in compliance.
Here’s how to select the right analyzer to meet these demands.
Downloads
Brochures
- Process Gas Chromatograph GC8000 (5.4 MB)
General Specifications
- GC8000 Analyzer Bus System (695 KB)
- GC8000 Modbus Communication (256 KB)
- GC8000 Process Gas Chromatograph (8.4 MB)
Technical Information
News
-
Press Release May 29, 2017 Yokogawa Wins Analyzer Package Order for Petrochemical Complex in Oman
- Commission to deliver 75 GC8000 process gas chromatographs -
-
News Brief Nov 11, 2016 Yokogawa's GC8000 Process Gas Chromatograph Receives CIS Science and Technology Award
Looking for more information on our people, technology and solutions?
Contact Us